BigChange for SVS engineers
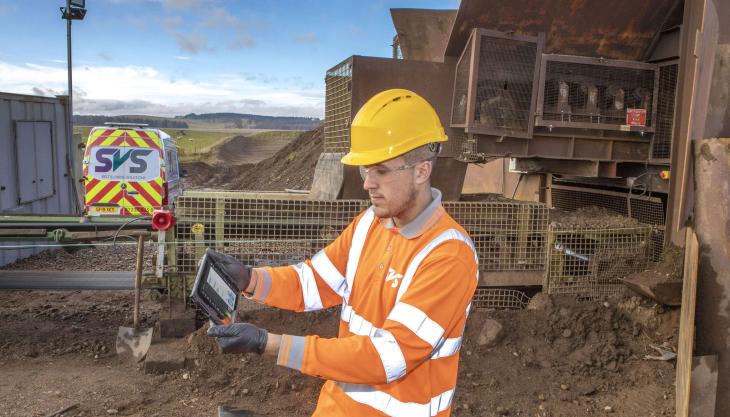
Conveyor system field service engineers go mobile with cloud-based paperless technology
QUARRY conveyor systems specialists Strathclyde Vulcanising Services (SVS) have rolled out a cloud-based mobile workforce management solution from BigChange. SVS field service engineers have been equipped with rugged tablets as part of a complete management system for paperless working that is improving efficiency, productivity and customer service.
Headquartered in Glasgow and operating throughout Scotland and the far north of England, SVS serve industries involved in bulk material handling, such as quarrying, mining, waste and recycling, and are specialists in the installation and maintenance of equipment where rubber is a key component, such as conveyor systems, chutes and hoppers.
Maintaining equipment that is usually critical to plant operation, SVS engineers provide a rapid, same-day response service 24 hours a day, seven days a week. However, owing to the nature of their critical work and health and safety requirements, the company was burdened with large amounts of paperwork.
‘With an ever-growing amount of paperwork, we were desperate to switch to digital working and invested heavily only to find that the solutions on offer were too cumbersome or too complex to use and didn’t fulfil our business needs,’ explained Iain Barral, managing director of SVS.
‘When we first discovered BigChange in 2018 we realized they had a system that could do everything we needed and more. It was also simple to use and we knew that would overcome the objections we had with previous systems.’
SVS have now implemented BigChange as a complete five-in-one business solution with back-office software synchronized in real time with field engineers equipped with tablets. For SVS engineers, the JobWatch app replaces all their paper reports from worksheets to health and safety forms, daily vehicle inspections and sign-offs.
The system gives SVS complete visibility of all jobs with reports being received from engineers in real time, including job card-linked photographs from site. By eliminating paperwork there have been significant gains in the office, with one person now able to do the work of two, doubling productivity.
In addition, fleet vehicles fitted with BigChange GPS trackers keep the office informed on progress and allow customers to receive texts and emails on the ETA of their engineer. Moreover, as SVS visit quarries and other industrial sites that expose vehicles to extra hazards, engineers also use the JobWatch app for vehicle inspections to improve fleet management. This ensures any defects are reported electronically, with photographs, to speed up and improve vehicle repairs and maintenance.
‘BigChange continues to transform our business. It has made monumental improvements to how we operate and enabled easy remote management of the business throughout COVID-19, and we are still exploring its capabilities for future advancements, adding value to our overall service and customer experience,’ said Mr Barral.
‘Working hard over the years we have doubled our turnover, and with our growth strategy we know BigChange will allow us to easily expand our services.’