Waste Not, Want Not
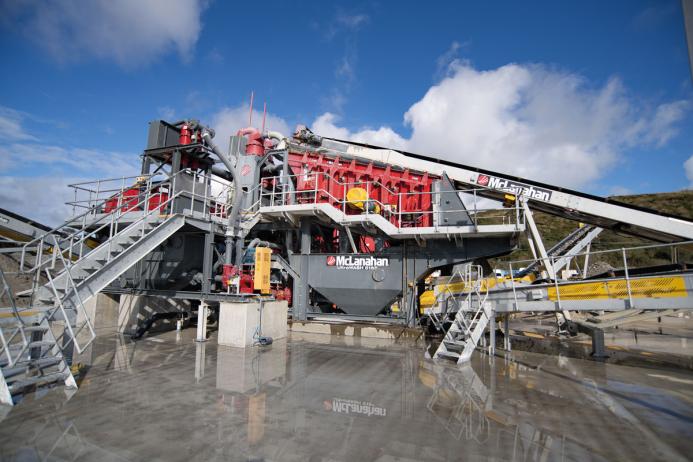
First published in the December 2024 issue of Quarry Management
McLanahan washing plant ensures zero waste to tip at Goonvean Aggregates’ Melbur Quarry. Dan Gilkes reports
Goonvean Aggregates, a family-run aggregate supplier based in Cornwall, serve a wide range of markets, providing a range of aggregates, from sub-bases and fills, to graded construction aggregates, mortar and plastering sands. Unlike many quarry operations, however, the firm’s Melbur Quarry processes secondary granite-based aggregates, which are the by-product of other industrial processes.
The secondary aggregate market is expected to expand rapidly over the coming years, as it takes an increasing share of the market. This is partly due to the difficulty in gaining approval for new quarries and extensions to existing sites, but is also a result of ever-increasing landfill tax rates, which is making construction and demolition waste a valuable source of recyclable aggregate.
The Melbur Quarry site, near Fraddon in Cornwall, receives its feed material from a separate supplier, with a small portion returned to that business for disposal after processing. Goonvean were looking for a way to be able to utilize all of the supplied material, without having to send any back to landfill, improving environmental sustainability for both businesses.
The company worked with McLanahan to design a wash plant that includes water recycling capabilities. The plant can be integrated with the site’s existing crushing facility, or be fed independently from external sources. To meet this need, McLanahan combined an UltraWash Modular Wash Plant, an UltraSand plant, and a 10m diameter EcoCycle high-rate thickener.
The feed material comes into the UltraWash directly from the crushing process, or through a feed hopper. The UltraWash washes the material and separates it into three aggregate sizes and a double-washed sand product. The UltraSand plant then processes the secondary residue material into a further saleable product.
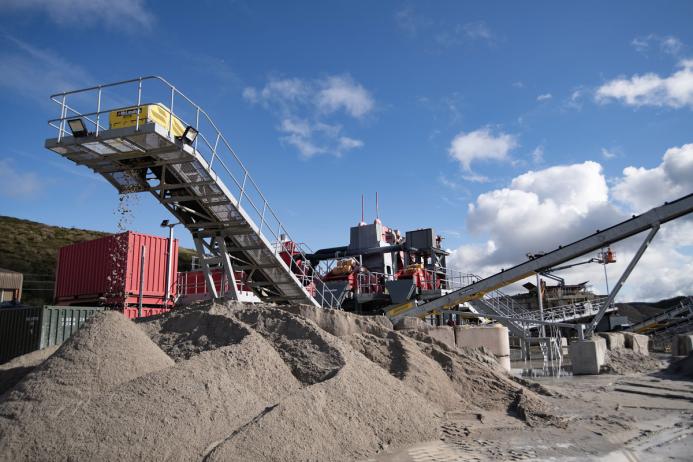
The waste streams from the two plants is fed into the EcoCycle thickener, which separates the solids from the liquid in the slurry, to recover reusable process water. This water is reused in the wash plants to clean the aggregate materials, further aiding sustainability.
‘Since we chose McLanahan as a partner, we’ve been quite productive in the way we’ve been able to reutilize and adapt the plant to our bespoke nature for the product we’re looking to produce,’ said Matthew Penny, general manager of Goonvean Aggregates. ‘The dialogue and feedback have been very strong and allowed us to end up with a plant that meets our requirements.’
By using the new washing and processing plants, Goonvean Aggregates are now able to make use of all of their feed material, greatly reducing the amount of waste that was being returned to the supplier, eliminating the need to take material to tip.
‘Our goals as a business are to be more sustainable in every facet of how we operate,’ said Mr Penny. ‘It’s an ongoing process and we’re looking to reduce our carbon footprint. Since we’ve had the McLanahan plant on site, our productivity and efficiencies have increased. We’re able to provide additional products to the local and national markets. As part of this it means that as a company we are ‘zero to tip’.’
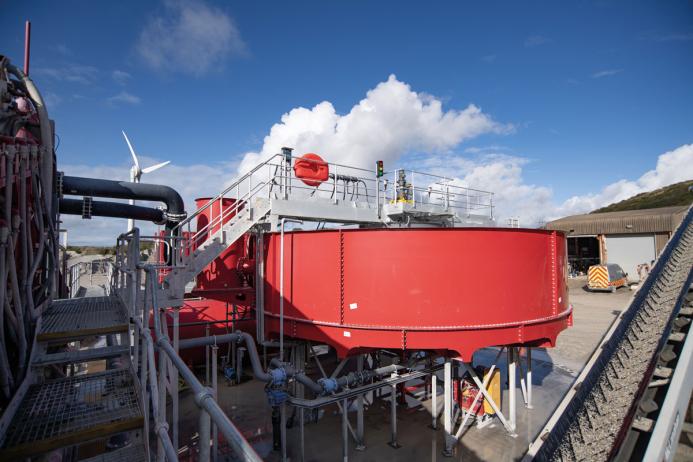
Goonvean’s Melbur Quarry looks set to become an increasingly important source of saleable construction materials, as the market in recycled and secondary aggregates continues to grow. Likewise, being able to clean material, whether from extraction or from construction and demolition, will become increasingly vital. If not washed, construction waste containing deleterious materials can be unsuitable for reuse, causing cracking in structural projects and preventing drainage in transportation projects.
By combining the washing process with particle sizing, it is easier for producers to separate material that is too small to be sized on traditional screening machinery. Some materials only require washing on a screen, while others require a more vigorous process, to remove clay and other debris, which is where manufacturers like McLanahan come in.
With a wide range of scrubbers, coarse material screw washers, fine material screw washers, hydrocyclones, hydrosizers, log-washers, and sand-washing plants, the company has an option to meet every need. By being able to pick and choose from that range, to combine various systems, like the plant at Goonvean Aggregates, it is possible to create a washing plant that can process all feed material, reducing waste and increasing sustainability.
‘Every part of the product which comes in to us, we’re able to process and resell as a finished product,’ said Mr Penny.
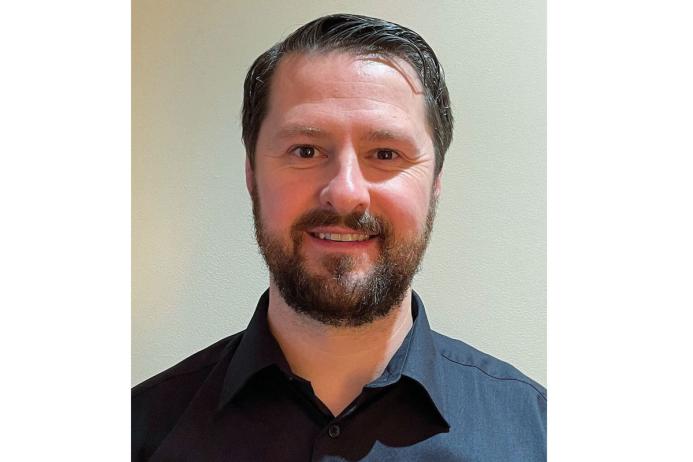
McLanahan building market share in Europe
Aggregate processing solutions providers McLanahan are pushing ahead with expansion into Europe, as their UK business continues to grow. The Northern Ireland-based manufacturer, which is owned by the US-based McLanahan Corporation, has experienced a period of steady expansion, both organically and from acquisition of crushing and screening businesses such as Anaconda Equipment.
The company also acquired Leicestershire firm CMB International in 2022, integrating it into the business and using CMB’s established expertise and field service team to provide back-up for the larger group’s businesses across the UK.
‘For us at the moment, things are looking really good,’ said David Hunter, McLanahan’s business line director for Aggregate Systems. ‘We are on an upward trajectory. We are building market share and the only way is up. We’ve really started to get our message out there. Now we are starting to branch out into Europe as well.’
McLanahan have been taking that message to the market, with a number of events that spotlight their wide-ranging capabilities. The most recent open day, at Goonvean Aggregates’ Melbur Quarry in Cornwall, created a huge amount of interest, with potential customers visiting from across the UK and further afield to see the installation in action.
‘We can provide customers with individual components, or with complete washing plants, like the one at Melbur Quarry,’ said Mr Hunter. ‘Customers come to us and say, design the plant and make sure it works. We are one of the few companies that owns all of the intellectual property (IP) across the range of equipment and we’ve been heavily backed by our parent company in the US. They give us all of the support that we need.’
Subscribe to Quarry Management, the monthly journal for the mineral products industry, to read articles before they appear on Agg-Net.com