A runway success for Tarmac
Tarmac describe successful Newcastle Airport resurfacing project as the ‘pinnacle’ of paving
VISITORS to Newcastle Airport generally have their eyes on the skies, but the infrastructure beneath their feet is key to maintaining this important transport hub. To ensure continued safe operations, Tarmac were appointed as principal contractor to undertake essential reconstruction and rehabilitation of the airport’s sole runway.
Tarmac’s established background in the aviation sector and ability to work in tight possession windows were integral to securing involvement in the £17 million project, with the company’s experience including previous reconstructions of the same runway in 1994 and 2008. This marks the third consecutive time that Tarmac have been entrusted to renew the critical infrastructure.
The longstanding partnership between the business and Newcastle Airport was instrumental in the project’s success, with senior Tarmac team members having been involved in all three runway resurfacing projects, thereby providing continuity of expertise.
The complex brief demanded that work did not disrupt airport operations, with strict demands and guidelines provided by the Civil Aviation Authority(CAA). When construction work started in November 2024, logistical planning and execution ensured that the project was confined to a strict 11.00pm to 6.00am possession window. During the project, the experienced team continually turned the runway into a busy construction site – and back again, in a feat of sleek logistics and exacting delivery that Tarmac are proudly labelling the ‘pinnacle’ of paving.
‘The timings, the people, and the plant and equipment were all organized like a military operation, not least of all because they simply had to be,’ said Chris Wright, regional contracting director North at Tarmac. ‘Diverting a plane due to an incomplete runway can cost hundreds of thousands of pounds, so non-delivery through even a small mistake just wasn’t an option. Working within this six-hour window, so that planes can take off early in the morning, calls for exacting preparation and delivery. It’s the ‘pinnacle’ of paving on critical infrastructure.’
The high-pressure environment demanded a meticulous approach. For six months leading up to the project breaking ground, Tarmac collaborated with Newcastle Airport in an intensive programme of planning meetings and trials. Rigorous planning was essential to manage and reduce risk while delivering the project.
Once work was under way, phased working was largely undertaken in 240m sections on the 2.4km runway. Tarmac carefully monitored the planing against asphalt production, ensuring there was always sufficient material on site to resurface the planed areas.
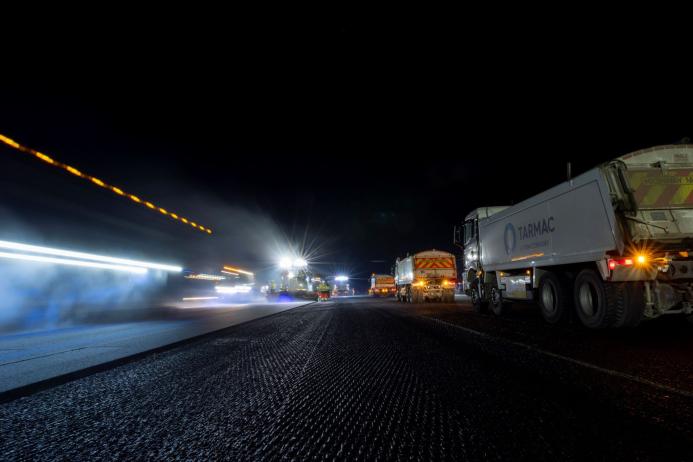
‘The works were carefully designed and managed to ensure they only progressed in close alignment with the amount of material arriving on site,’ explained Mr Wright. ‘Maximizing productivity was essential – deliveries were carefully planned prior to starting each and every shift, and then monitored in real time so we always knew where everything was at any given time.’
The rehabilitation of the runway extended beyond the surface, with the project covering multiple activities. The team reconstructed the central 20m section with a binder course to approximately 130mm depth, followed by resurfacing of the runway’s full 46m width. In total, 35,000 tonnes of new asphalt were used, with the choice of material a crucial consideration.
Airport pavements require highly durable asphalt, able to deal with the extremely high loading characteristics of aircraft that can weigh as much as 300 tonnes and land at speeds of over 250km/h. The Marshall asphalt that was used is a high-specification material designed specifically for airfields. Not only does it need to withstand the significant daily impacts from landing aircraft and be resistant to cracks, but it also has to be resilient to the chemicals used to de-ice the surface during winter months.
To achieve the rigorous specification, Tarmac’s team engaged with their supply chain and selected a polymer-modified bitumen (PMB) from Shell, which provided a more durable alternative to traditional bitumen and created a more robust asphalt mix.
All aggregates used were locally sourced and 100% of the planed materials removed from the existing runway surface were recycled at nearby Barrasford Quarry, and were then able to be repurposed into new asphalt for other applications.
The latest technology was also employed to further optimize operations during the installation, including 3D models for planing control provided by National Road Planing (NRP).
‘The project was a great example of precision engineering at its best,’ said Jamie Town, general manager at NRP. ‘Our 3D planing technology enabled the project to achieve the highest levels of accuracy, meaning the new surface met the exacting standards needed for safe and long-lasting aviation infrastructure.’
The surfacing process was delivered with precise design levels, with echelon paving deployed to eliminate joints in the runway and boost the smoothness and longevity of the surface.
‘Marshall asphalt is a very high paving specification. Airfields are a rigid environment when it comes to the selection of materials and surfacing needs to meet CAA standards as well as international specifications that have been around for over 50 years,’ explained Chris Wright.
He continued: ‘The demands and robustness required mean that before you even lay a tonne of asphalt on site, rigorous planning has been carried out. A regime of testing and trials began months in advance of the works starting on site. We started by assessing the mix design and then carried out off-site trials at our nearby quarry. Lastly, on-site trials provided peace of mind that every single aspect of work would progress without a hitch.’
In addition to resurfacing, the project also included repainting the runway markings as well as upgrading all of the existing runway lighting with new LED technology. This required the installation of approximately 35km of new electrical cabling and replacing around 1,000 lights on the runway and connecting taxiways.
To allow water to drain and remove the risk of aquaplaning, great care had to be taken to precisely texture the newly applied surface. ‘Cutting tiny grooves into the asphalt helps disperse water quickly and increases friction for planes coming in and landing at 180 miles/h,’ Mr Wright explained. ‘The grooves were cut into the surface every 25mm, with this process taking place 72h after the new surface had been laid. Throughout the project, air traffic controllers and pilots knew exactly which sections had been grooved and were able to manage landings accordingly.’
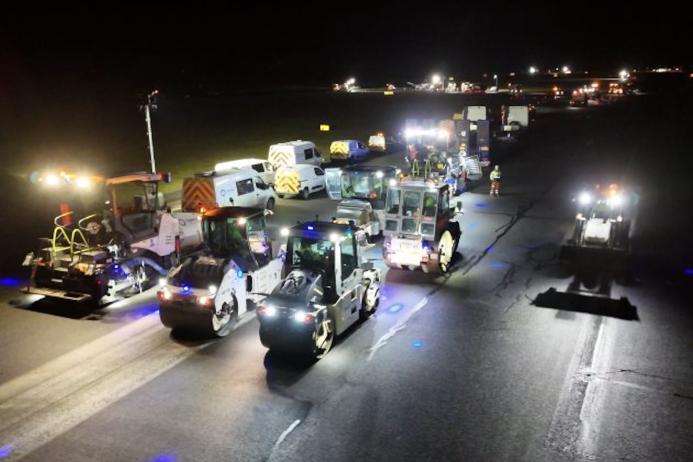
Resurfacing methods have a lot in common whether on motorways or runways, but tight airport security added a further challenge to the brief. With up to 80 pieces of plant and vehicles on site each night, the project team liaised continually with the airport authorities to ensure that each of the 100-strong team had the correct permits to enter the site, and to give feedback on the precise condition of each section of pavement.
Stephen Barnard, project manager at Newcastle Airport, commented: ‘Our longstanding relationship with Tarmac was key to the successful delivery of the resurfacing project. The team has an in-depth understanding of the highly controlled and constrained environment and there was mutual trust that the project would be successfully completed without issue.’