Terex Washing Systems launch AggreSand system
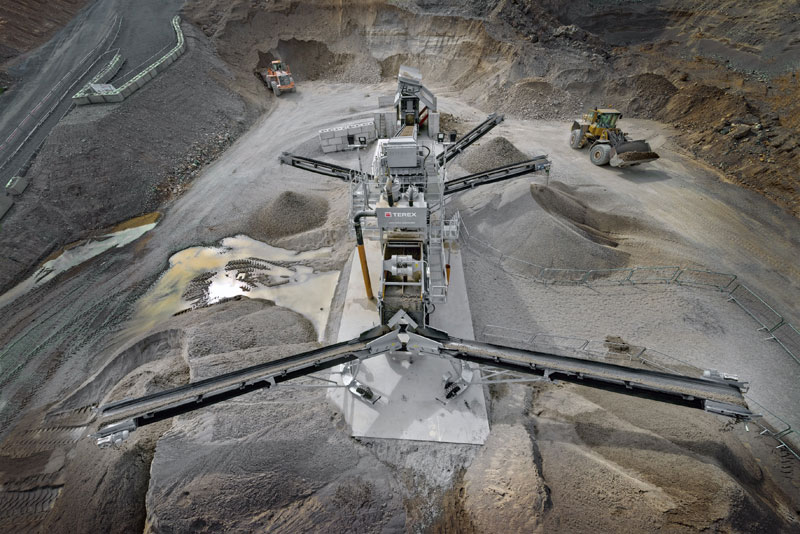
First published in the November 2013 issue of Quarry Management as Game Changer
Terex Washing Systems officially unveil the AggreSand system with a demonstration at an Irish quarry
On 5 September Terex Washing Systems (TWS) officially launched their newest aggregate and sand washing plant – the AggreSand. The innovative system – which combines aggregate washing and screening with sand processing – was unveiled and demonstrated at Dowling Quarries’ Lisduff Quarry, near Abbeyleix, in County Laois, Ireland.
More than 40 TWS distributors from around the world attended the product launch and reaction to the new washing plant was good, with a large number of enquiries resulting from the dealer event.
‘We are delighted to officially launch the AggreSand washing plant after what has been an eagerly awaited event for TWS distributors and customers,’ said Elaine Donaghy, marketing manager for TWS. ‘Following the programme, we are already witnessing a huge surge of enquiries. The AggreSand plant will set us part from other providers in the market and revolutionize the wash plant market by continuing to serve our customers’ needs around the world.’
A gap in the market for such a system was identified following extensive research, part of which was conducted at TWS’s first-ever product development forum. This involved the company’s engineers and sales technicians working with the global distributor network to formulate the concept.
The AggreSand system is able to produce three aggregates and two sand products in one machine by bringing together aggregate and sand washing on a single modular chassis.
The new plant is also efficient and quick to set up thanks to essential ‘plug and play’ plumbing/pipework and electrical wiring, allowing it to be erected within a day. Other key design features and benefits of the AggreSand plant include:
- A new TWS-designed 12m3-capacity modular hopper feeder available with an automatic tipping grid and a 12ft two-deck vibrating grid, complete with variable-speed belt feeder, all controlled from the main operator interface and radio-control unit.
- A wide inclined feed conveyor with direct-drive electric motor and gearbox arrangement that works at a 19° angle when feeding the AggreSand system. The conveyor features an innovative sealed wash box at the discharge point to give material a pre-rinse before screening. Its innovative design eliminates splashing and produces an even distribution of material across the full width of the rinsing screen.
- Highly efficient 165R-3 (three-deck, two-bearing) rinsing screen of riveted construction. The screen is designed to isolate the spray bars from vibration by utilizing high-quality rubber gators on the mid and bottom decks, while rubber extensions prevent overspill or splashing from the top-deck screen. The 165R-3 unit offers a full 80ft2 (7.54 m2) of screening area on all three decks, each of which has eight individually controlled spray bars fitted with polyurethane fan-type spray nozzles.
- Large-capacity split sump tank that receives rinsed fines from the bottom-deck screen into either a coarse or fine compartment. The coarse side has a built-in float system to help equalize the levels in both tanks and prevent overflowing.
- Two centrifugal slurry pumps (coarse and fine) pump material from both sides of the sump tank into two hydrocyclones. These remove silts and clays (–63 microns) which are sent to the water-treatment plant. Heavier material (+63micron) exits the bottom of the hydrocyclones into a rubber-lined box where blending takes place if required.
- Underflow from the hydrocyclones transfers on to a 125 dewatering screen via a discharge box which evenly distributes the material across the screen. Both materials are dewatered over a 500-micron polyurethane screen to produce two instantly saleable grades of sand. The high-energy dewatering screen is fitted with two high-efficiency, counter-rotating vibratory motors that remove capillary water to produce two dewatered sands.
- Ease of transport as all components are designed to be easily dismantled and placed into standard 40ft containers, resulting in fewer crane lifts and reducing the re-assembly time on site.
The first AggreSand machine was delivered to Dowling’s Lisduff Quarry in August this year and has been successfully processing sand and gravel material ever since.
‘The plant arrived on site and was installed in approximately 10 hours,’ explained quarry owner Humphrey Dowling. ‘The throughput capacity of 250 tonnes/h being achieved on the plant is excellent and the quality of the aggregates and sands being produced is very impressive.
‘The high-performance two-deck vibrating grid allows us to feed material directly from the face of the quarry; at 200mm, large material is scalped off while the –50mm material goes straight into the wash plant. This eliminates the need for expensive pre-screening of the feed material.’
Dowling Quarries’ AggreSand system is fitted with a 12ft double-deck vibrating grid with 100mm bofor bars and 50mm woven wire mesh. The plant separates 0-40mm and produces three aggregate materials and two sand products.
On the bottom deck of the plant, –50mm product is delivered by the feeder belt on to a 1,000mm wide electrically driven inclined feed belt. This wide conveyor is fitted with an integral wash box to pre-soak and deliver the material to the full width of the screen, thereby utilizing the full screening area.
The 16ft x 5ft (4.9m x 1.5m) three-deck screen is electrically driven, producing an aggressive 6mm throw and is fitted with eight individually controlled spray bars on each deck. The sized and rinsed aggregates produced by the screen are stockpiled on three integral 9m stockpilers.
Elsewhere, the dual sand plant includes two rubber-lined centrifugal pumps and two heavy-duty rubber lined cyclones which remove silt –75 micron). The silt-free sand is delivered to a split 12ft x 5ft screen to produce two grades of dewatered (12% moisture) silt-free sand.
The sand stockpilers are radial-powered through electrical wheel drives and have an impressive stockpiling capacity of 350m3. The end products include: 6-14mm (503 drainage material); 14-22mm (503 concrete material); and 22-40mm (505 drainage material).
The 0-3mm sand produced is used for plastering and block making, while the 0-5mm sand is used in the production of concrete. According to TWS, there is zero waste from the plant and minimum sand is lost to ponds.
Commenting on the AggreSand plant at the dealer event, Fintan McKeever of DUO plc, said: ‘I am extremely impressed by the build quality and features of the machine and believe that this is a world-class product with nothing comparable on the market. I am confident it will serve our market well.’
Another dealer impressed by the AggreSand washing system was Giuro Kralex of Powerscreen Bulgaria. ‘The AggreSand is an extremely good concept for washing with the ability to produce five products, including two sands,’ he explained. ‘I am amazed by the quality and build of this unique machine, which demonstrates what washing should be.’
Sean Loughran, director of TWS, concluded: ‘The Aggresand plant definitely serves our customers’ various demands and needs worldwide and will continue to meet and exceed customer expectations. This machine is the first in a line of planned modular plants to be released over the coming 24 months that will quite simply change the very nature of how aggregates and minerals are washed and managed throughout the world.’
- Subscribe to Quarry Management, the monthly journal for the mineral products industry, to read articles before they appear on Agg-Net