New wash plant maximizes yield for Glendinning
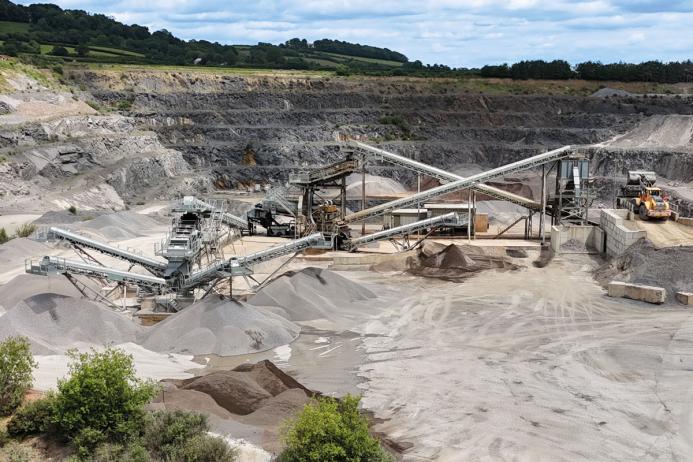
First published in the February 2025 issue of Quarry Management
PowerX Equipment installed plant at Linhay Hill Quarry reduces reliance on imported sands, lowers carbon footprint, and reduces truck transport on local roads. Dan Gilkes reports
Maximizing the productive output of a quarry requires a combination of the right equipment, an experienced team and, in many cases, a healthy dose of innovative thinking. For EJ&W Glendinning’s Linhay Hill Quarry, near Newton Abbott, in Devon, the company was granted permission to extend in March 2021. This created a need for an upgrade to the site’s main washing plant. However, rather than simply replace like for like, the company has installed a system that allows it to use more of the material from the quarry, reducing cost and boosting profitability.
Glendinning are major suppliers of quarried aggregates, ready-mixed concrete, asphalt, and block products to contractors throughout the South West. Founded in 1958, the family-owned business is now investing to sustain its operations and construction materials supply as it is prepares to quarry the first stage of the extension. Creating various limestone aggregates from 6mm to 20mm, the site also produces 0-4mm washed, crushed aggregate fines (black concrete sand). This black sand is mixed with traditional china clay sand, before being used in ready-mixed concrete at the firm’s plants within the quarry and in nearby Plymouth and in Exeter.
Two tracked excavators work Linhay Hill Quarry’s main production benches, loading into mobile primary crushers at the face. A mixed fleet of 70-tonne rigid and 40-tonne articulated haulers transfer the crushed rock from the primary output to a secondary plant at the top of the site, from where it is distributed between the asphalt plant, an agricultural lime facility, a ready-mix concrete plant, and into stockpiles of loose aggregates.
To maximize yield from the uppermost benches of the extension, Glendinning installed the new wash plant in September 2023. In part, the plant will allow the company to handle a partial mix of overburden from the anticipated rockhead pinnacle formations of the top bench, reducing the potential for waste material. Designed and installed by Power X Equipment, the new plant incorporates two adaptable hydrocyclones, to recover fines passing 63µm.
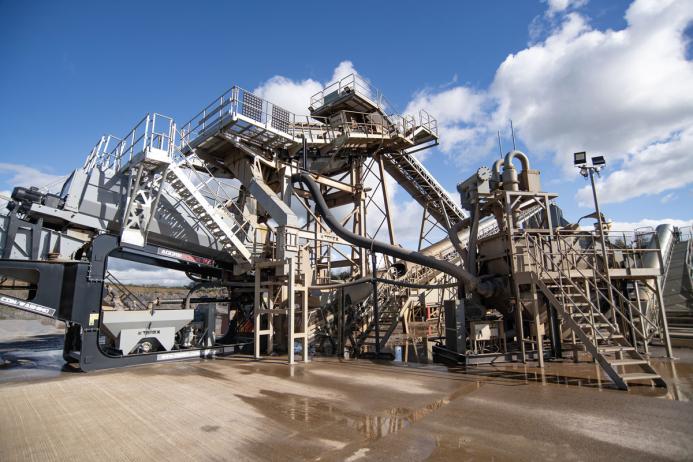
The washing plant includes twin, rubber-lined hydrocyclones, that are fed by a single 200/150 pump. The site did try a single-cyclone design, but it failed to remove enough fines, so was swapped for the dual system. With minimal overflow, the plant consumes less than 300m3 of water per hour, considerably less than some competitive quotes. The cyclones offer a choice of three feed tubes, three vortex finders, and seven apexes, allowing the company to fine-tune the end product, to suit the current market requirements.
‘Our old Powerscreen plant was built by Powerscreen Washing Systems, who have since become PowerX Equipment,’ said Ian Hannaford, control systems and project engineer at Glendinning. ‘We did go out to tender, but the PowerX solution was the best for the site. PowerX worked to my electrical specification and they were just a better fit for us.’
Material is fed into the plant through a double-deck rinsing screen, allowing sand to drop through the bottom deck, while aggregate larger than 20mm is returned on a closed-circuit conveyor. This is fed into a surge bin before entering an impact crusher.
‘We scalp out dirty oversize to get washed and processed into single sizes,’ said Mr Hannaford.
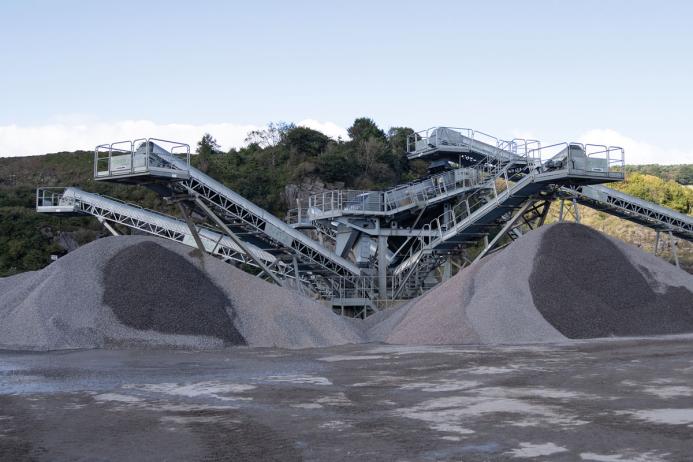
The aggregate passes on to a secondary feed conveyor and into a twin-shaft log-washer. Scrubbed aggregates exit the plant through a 2.4m x 1.2m dewatering screen, which liberates any fines through a transfer conveyor to a sizing screen. Materials are fed to the stockpiles by up to four conveyors.
While PowerX have recently carried out a 12-month inspection on the washing plant, all maintenance is completed by Glendinning’s in-house engineering team. The company has installed a fibre optic connection across the site and all equipment has a common control system, making it easier to operate. The controller can monitor everything, from individual motor speeds to tonnes per hour production and material flow rates.
‘Our plant operator is certainly happy with the new system,’ said Mr Hannaford.
By being able to use a larger percentage of the black sand within the ready-mixed concrete plant, Glendinning have been able to reduce their reliance on imported sands, lowering their carbon footprint and reducing truck transport on local roads.
Solar power
Quarries consume a huge amount of energy and, in future, an increasing amount of that energy will be electricity, as companies look to lower their carbon footprint and cut their reliance on diesel power. To cope with this increased demand for cleaner energy, many businesses are looking to renewables to provide much-needed electricity. However, while it may be possible to install wind power in some more remote locations, for Linhay Hill Quarry, erecting a turbine was not a possibility.
Instead, the company has been increasingly turning to solar power, to provide a growing percentage of the energy for its facilities. Mr Hanniford has already installed solar panels on all available south-facing roofs throughout the site, creating around 0.5MW of power in total, which accounts for up to 8% of the quarry’s needs.
With no additional buildings available, he has now turned to other locations for potential photovoltaic cell installation. In an inspired move, Glendinning are going to float pontoons on their settlement and water storage lagoons. These pontoons will carry a further 0.5MW of solar panels, taking the renewable energy supply to 15–16% of the site’s overall demand.
Assembled in a fixed position, the solar panels will cover an area measuring 70m x 54m. As the site will consume all of the available power as it is produced, there will be no requirement for electrical storage, so the company will not be installing any form of battery system. The installation should see a return on investment within five years, going on to reduce the company’s fuel bills and its carbon emissions beyond that point.
Subscribe to Quarry Management, the monthly journal for the mineral products industry, to read articles before they appear on Agg-Net.com