New QMS washing screen for Croxden Quarry
Tarmac sand and gravel quarry reaches its full potential with help from Quarry Manufacturing & Supplies
TARMAC’s Croxden sand and gravel quarry has reached new levels of efficiency and performance thanks to the installation of a cutting-edge washing and screening plant from Quarry Manufacturing & Supplies (QMS). This advancement marks a transformative step for the Staffordshire site, ensuring it can reliably meet growing demand for its products while delivering enhanced production capabilities.
Croxden sand and gravel quarry supplies a range of high-quality aggregate products to builders, contractors, and landscapers working on small-, medium-, and large-sized projects in Stoke-on-Trent and the surrounding areas. However, the quarry faced challenges with its existing plant, which was no longer capable of supporting the operation’s full potential. This led the quarry’s management team to seek a solution that would not only restore production, but also enhance productivity, accuracy, and quality, cementing the quarry’s reputation for excellence.
The quarry management team were already familiar with Coalville-headquartered QMS, knowing of the support the company has provided to similar operations throughout the UK and Europe, delivering equipment, spare parts, aftermarket support, and process advice. This gave the Tarmac team the confidence to contact QMS when seeking a solution.
‘We were pleased to be contacted and after assessing the situation we realized that we could not only rectify the situation, but also improve production and the quality of the end product,’ explained QMS managing director Jonathan Beck. ‘We have expertise in the quarrying industry, and providing a washing screen for sand and gravel production is right up our street.’
After site visits to find out what exactly was required, the QMS team devised a solution for the quarry. ‘What we came up with incorporated what the quarry’s customers required from the sand and gravel produced there. We assessed the quarry and the logistics of the production process as well as what the end product would be used for,’ explained Mr Beck.
‘This resulted in us using one of our triple-deck washing screens which is actually bigger in size than the one it replaced. Despite this, due to our engineers’ expertise and experience, it fitted in precisely with the existing plant and equipment. In fact, the new screen provides a 50% larger screening area.’
Screening accuracy and washing efficiency are now provided by the QMS 1.83m x 6.0m inclined triple-deck screen, which produces 20mm and 10mm concrete sand and building sand. Any oversize is recirculated for further crushing and then redirected into the screening/washing process. The screen is equipped with wet modular vibrating units, huck bolt fastened decks, along with full length stiffeners. Aiding production is a large feed box to help distribute material across the screen.
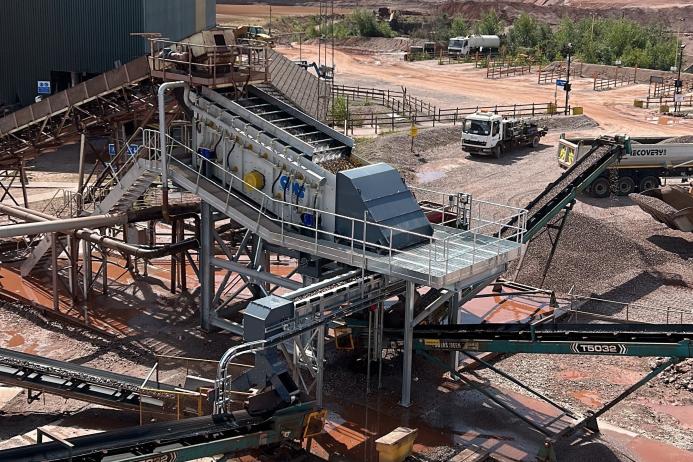
The improved and renewed performance of the sand and gravel quarry should not come as a surprise to those familiar with the QMS offering and support. Since their foundation in the 1980s, QMS have developed a range of pre-designed modular plants designed to work with the most common crushing and screening applications in the quarrying, mining, demolition, and recycling industries.
Moreover, the company has used its industry expertise to offer a bespoke design facility to meet customers’ exact requirements. All offerings are manufactured in the UK by QMS and have been designed to be mixed and matched interchangeably, allowing hundreds of possible combinations. This concept provides a platform to not only meet current requirements, but also allows for upgrades in the future.
All QMS plants, such as the one at the Tarmac Croxden, include all the required walkways, stairs, handrails and guarding, and are pre-wired and tested prior to leaving the factory, thereby saving valuable installation time on site. The equipment can be erected on site in minimal time using basic tools and features an integrated plug-and-play PLC control system, operated by touch screen, allowing the plant to be up and running in a matter of hours. All equipment is supported by QMS’ after-sales service.
‘QMS personal liaised with us many a time during design period and fabrication. This process gave them a good insight and understanding as to site requirements,’ said Jason Cotton, unit manager at Tarmac’s Croxden Quarry.
He continued: ‘This benefitted the site and Tarmac as a whole. The new screen QMS designed and installed has delivered in all aspects as build quality is good. The washing and production of accurately sized material, efficiently and reliably, enables us keep supplying quality products to our customers. Aftermarket support is very good, with QMS always being proactive and extremely helpful and professional in all aspects of their work. We look forward to continuing to work with them at Croxden on other areas of plant as well dealing with our requirements.’
QMS managing director Jonathan Beck concluded: ‘The sand and gravel quarry was a tricky problem, but the QMS team rose to the challenge. We proactively sought to understand the quarry’s real requirements, what the problems were, and what the customers required. This enabled our engineers to use their industry expertise to come up with the solution that is meeting production and quality targets. The plant’s efficiency is further enhanced as we also provide full aftermarket care including quality inspections, spare parts, and servicing.’