New Wash Plant for Brice Aggregates
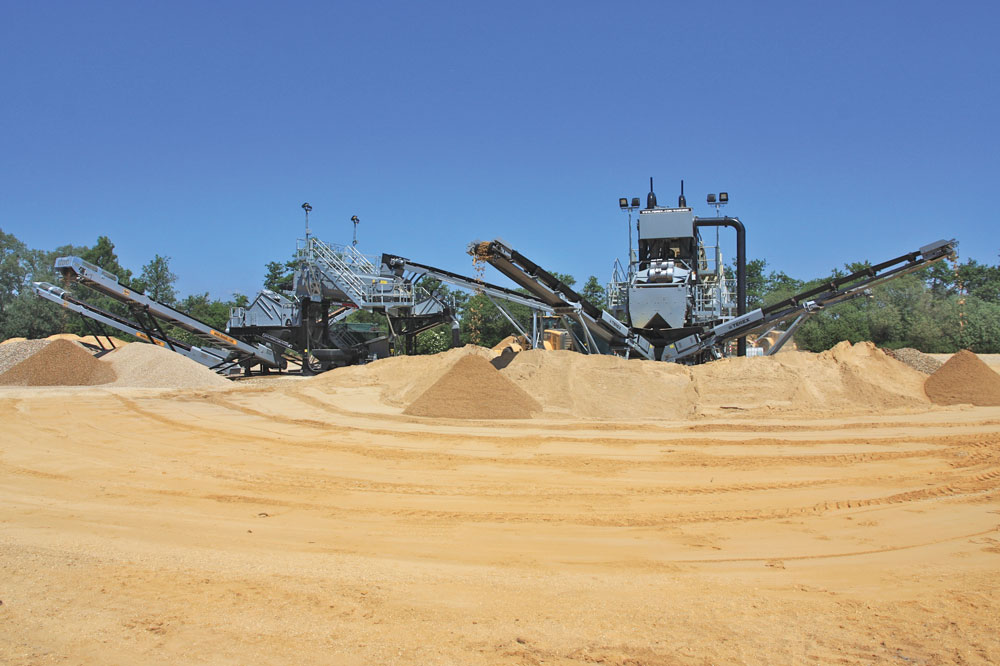
First published in the July 2017 issue of Quarry Management
DUO supply Essex-based sand and gravel operator with Terex Washing Systems AggreSand and AggreScrub combination
Based in Witham, Essex, Brice Aggregates are the latest quarry operators to take delivery of a new Terex Washing Systems (TWS) wash plant supplied by DUO (Europe) – TWS dealers for England and Wales. Owned and operated by Simon Brice, the new plant will process sand and gravel for a single supply contract within the area.
Development started one year ago on a 34.6ha greenfield site with approximately 2.5 million tonnes of sand and gravel reserves within the Colemans Farm Estate. Once the basic site infrastructure had been completed DUO Equipment were selected to supply a new wash plant based around the TWS AggreSand system.
Quarry manager Danny Shelley commented: ‘Based on our experience with Powerscreen equipment and the solid reputation that DUO have in the industry, we decided to invest in a 200 tonnes/h TWS modular wash plant based on an AggresSand and AggreScrub combination.’
The investment in the TWS wash plant is expected to provide cohesive solutions for all of Brice Aggregates material and mineral washing needs within today’s stringent specifications for clean material.
Sand & gravel plant
Installed and commissioned in January 2017, the main elements of the plant at Colemans Farm consist of: a Terex AggreSand 165, triple-deck modular wash plant and an AggreScrub 150 scrubber unit. The AggreSand is a pre-wired and pre-plumbed modular concept that facilitates quick and easy installation – a combination that is proving very appealing to operators in terms of access, serviceability and modularity.
AggreSand 165
The AggreSand 165 uses TWS’s H12 (12m3) feed system, which is fed by wheel loader via a heavy-duty 4m static grid and powered by an integral 37kW electric hydraulic powerpack. Material is delivered on to a main inclined feed conveyor driven by an 11kW WEG electric motor and Bonfiglioli gearbox mounted on the drive drum. The 19m long x 1,000mm wide conveyor features an integral heavy-duty rubber-lined washbox that soaks the material before it is delivered on to the rinsing screen.
‘It’s a very neat and compact plant incorporating an in-line system with ‘as-raised’ ballast being fed by loading shovel into the feed hopper. With pumps installed, we are responsible for the wash water going in and the dirty slurry coming out of the plant to the lagoons, so it’s a very simple and effective set-up,’ said Mr Shelley.
The AggreSand 165 at Colemans Farm features a three-deck 16ft x 5ft rinsing screen that operates at an 18° angle and utilizes individually controlled spray bars on each deck. The two-bearing screen is fitted with polyurethane modular media on all three decks, with the top deck removing any +40mm material, which is fed, via an on-board conveyor, to stockpile. The middle and bottom deck overflows feed 5–40mm material on to an extended inclined conveyor that feeds the AggreScrub 150, while the split bottom deck (2mm and 5mm appertures) provides the feed to produce two sand products. All chutework on the AggreSand 165 employs the well-tested dead-box system, resulting in stone-on-stone contact that helps ensure excellent wear properties.
The Brice AggreSand 165 was supplied with a high-capacity 200 tonnes/h sand plant, which consists of one 30kW 200/150 pump and G4 660mm cyclone for coarse sand and a 22kW 200/150 pump and G4 500mm cyclone for soft sand. A specially designed rubber-lined underflow box allows blending to take place so that an acceptable coarse and fine sand ratio can be achieved. The clean in-specification sands are delivered on to separate radial stockpile conveyors.
AggreScrub 150
The AggreScrub 150 consists of a 6.5m hull fitted with twin rotating shafts equipped with 30mm abrasion-resistant blades. The blades convey the aggregate materials from the feed end of the scrub to a 12ft x 5ft twin-deck part-rinsing/sizing screen. As the material travels through the hull the abrasive stone-on-stone action scrubs it clean and breaks up any clay agglomerates. Any plastics or organics are floated off for dewatering by the AggreScrub’s 6ft x 2ft trash screen. Underflow from the trash screen is captured in a catch box and gravity fed to the sump tank under the main hull.
Meanwhile, the scrubbed aggregate exits the AggreScrub 150 on to the 12ft x 5ft two-deck part-rinsing screen fitted with polyurethane modular media to produce 5–10mm, 10–20mm, and 20–40mm clean aggregates, which are stockpiled using three TC6532 conveyors. The initial section of this screen is equipped with spray bars to rinse off any remaining sand or grit residues produced during scrubbing. These are captured beneath the screen and piped to the sump tank below the hull to join the trash screen underflows. The sump tank is fitted with a 100/100 centrifugal pump that pumps the dirty water back to the AggreSand 165 sand plant to recover any remaining sand and maximize the recirculation of process water.
John Bracken, DUO Group operations director, commented: ‘The TWS AggreSand plant is ideal for the Brice Aggregates operation at Colemans Farm, offering a fully modular, pre-wired and pre-plumbed, electrically powered wash plant. With its robust, heavy-duty design, it is well suited to rugged operating environments, and offers an environmentally friendly operation with zero exhaust emissions.’
Since the plant was commissioned it has operated successfully and consistently, providing Brice Aggregates with complete control over their production and the flexibility satisfy the requirements of their contract.
Danny Shelley commented: ‘There are a number of other sand and gravel operations in the area and demand for 20mm stone is high. Although this material is in short supply, we have been able to offer greater availability, as we have a more favourable 60% stone, 40% sand split. Since the plant was commissioned it has consistently produced very clean, high-specification, saleable materials. We are very pleased with it and have confidence in the support from DUO.’
Garry Stewart, regional sales manager with TWS, said: ‘It’s great to have another successful installation in the UK. TWS and DUO have had major success in this market where the TWS modular concept has been well received. Customers are demanding rapid deployment and higher production rates combined with minimal downtime, and the AggreSand and AggreScrub modular concept delivers on all these fronts.’
- Subscribe to Quarry Management, the monthly journal for the mineral products industry, to read articles before they appear on Agg-Net.com