LEAN Screening: How to increase value-added aggregate processing
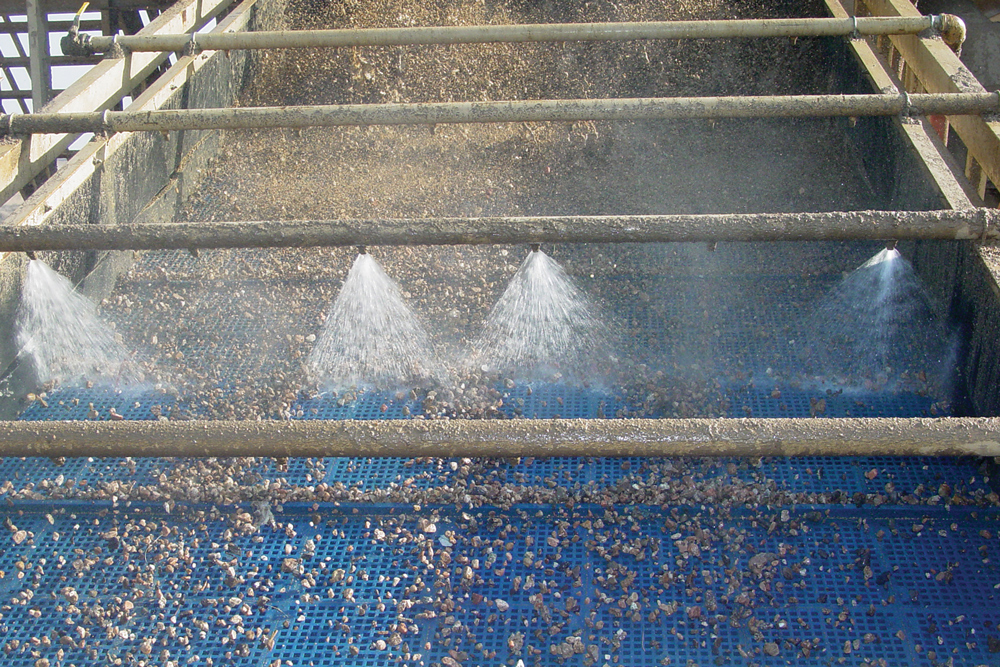
First published in the February 2018 issue of Quarry Management
LEAN methodology is traditionally associated with manufacturing rather than quarrying. However, as Carol Wasson reports, employing LEAN tools in a screening application can significantly reduce costs and optimize site performance.
LEAN manufacturing is fully focused on reducing waste and improving process flow, while strengthening value-added issues, exceeding customer needs and boosting profitability.
Within aggregate and quarrying operations, one example of ‘LEAN screening’ is the use of properly specified modular synthetic (polyurethane or rubber) media. In even the toughest wet or dry screening applications, operations may realize greater wear life, consistent gradations and a significant reduction in maintenance costs and downtime. These time- and labour-saving benefits provide maintenance personnel with valuable time for other core tasks.
‘Nowadays, it’s all about yield – specifically, the yield of critical products,’ said Tod Eberle, key account manager for Polydeck Screen Corp. ‘It’s about achieving efficient separating and sizing that delivers the most value.’
According to Mr Eberle, today’s producers are highly attuned to the inventory control of their key saleable products.
‘Years ago, producers could sell almost everything they made – and they didn’t mind dealing with waste products or working an extra 100 hours a year to make more of a particular product,’ he said. ‘But today, they’re smarter. They understand that product yield and ultimate control over gradations is imperative. Every tonne that an operation cannot maximize means more time in production and more by-products that are not as marketable.’
Mr Eberle is an aggregate industry veteran who spent more than 20 years as a producer before joining Polydeck.
‘I had specified their media for a number of plants, and I found that I could tweak a deck in fine increments, completely controlling the gradations and yield percentages, because I had so many variations to work with,’ he said. ‘They offered options in polyurethane and rubber, different durometers and hardness, different opening sizes and shapes, and media for higher wear life and open area.’
Optimal process flow
To ensure optimal process flow over the long term, the right screen media specification strategies must be employed up front. Detailed data must be gathered on the material type, tonnes per hour and desired gradations, says Mr Eberle.
Further analysis will examine issues such as blinding or plugging and pegging problems, as well as bed depth and carryover. Due to the modularity of the Polydeck screen panels, ‘there are many options in sizing openings at various points on the deck, such as placing a few larger openings at a critical point on the deck to allow just enough coarse material through to make a particular spec, for example’.
‘Also, to maximize wear life and gradation accuracy, there are simple ways that panel types can be moved around to take advantage of where material stratifies and passes through the deck,’ said Mr Eberle. ‘Additionally, we can employ various surface features such as dams and skid bars to control flow and provide cleaner material, while increasing throughput.’
The key to a successful LEAN screening strategy, says Mr Eberle, is focusing on the bigger picture – from crushing to stockpiling.
‘And, in between, we examine the screening circuit as a whole,’ he said, noting some manufacturers offer producers the opportunity to complete a ‘screen performance evaluation’ prior to specifying and installing new media.
‘We combine our engineering expertise with high-tech electronic instruments to measure and evaluate all aspects of a screen’s operation.’
He says the evaluation examines the screen’s G-force, stroke, deflections (aberrations in its movements), critical frequencies, support structure integrity and more. ‘Subsequently, we issue our findings with recommendations to bring the screen up to its peak screening performance in the particular application,’ he said.
From more than 1,000 screen panel design options, the screen media is correctly matched to the vibrating screen parameters, making sure the circuit will keep pace with the crushing side.
Mr Eberle stressed that all product mixes were reviewed so potential gradation inconsistencies and plant bottlenecks could be identified and adjustments made.
‘After we’ve identified critical processing statistics, we can run ‘what if?’ scenarios to optimize media specifications to the application, and to determine how any changing variables within the screening operations will affect overall efficiency,’ he said.
Reduce waste, downtime
Time management skills are essential to the LEAN processing mission.
‘There are producers out there who really don’t understand the value of repair and maintenance time,’ said Mr Eberle.
He says it’s common to replace wire cloth decks on a weekly basis. ‘Producers are all too familiar with the need to shut everything down, pull workers from other jobs, bring in a crane and switch out the wire cloth. It’s a lengthy job.’
Alternatively, the wear characteristics of synthetic media allow operations to avoid changeouts throughout a season or even over multiple seasons, depending upon the application.
As a result, the wear life of synthetic media delivers a gain of significant hours for maintenance personnel to focus on other value-added tasks, and for the operation to increase its yield of critical products. Again, the latter is integral to LEAN screening.
There are also the issues of blinding and pegging. Mr Eberle says a producer may choose wire cloth for its open area, yet the deck will blind up within days or weeks, resulting in a dramatic loss of throughput, and increased downtime.
Modular synthetic panels can be very competitive with wire cloth on open area, Mr Eberle says, adding that producers should consider that the open area in wire cloth is often overstated. He says many wire cloth catalogues list percentages of open area that figure in all the openings in a section of wire cloth.
However, upon installation, bucker bars, crown rubber, clamp rails and centre hold-downs block a portion of those openings. This means the open area is significantly different, causing calculations to be off by as much as 40%.
‘It’s also important to note that, in the case of conventional synthetic media brands, the open area is often calculated by ignoring the border,’ he said. ‘The conventional panel has a large border or dead area around the perimeter that is not taken into account, and in this case as well, the open area is overstated.’
On the issue of waste, Mr Eberle says producers that run wire cloth do one of two things: they run it until it catastrophically fails and contaminates the stockpile or, to avoid this, they pull the deck too early. Either choice wastes both time and money.
‘One of the biggest benefits of synthetic media is that you rarely have a catastrophic failure,’ he said. ‘Instead, synthetic media gives you a warning of any wear via gradation creep. As you take quality control samples, watch for subtle changes in gradations. Usually, when your samples become coarser, you’ll most likely detect some wear in the panels. In most cases, you simply change out a panel or two, and you’re up and running again.’
Inventory control
For efficient inventory control, it’s a good idea, says Mr Eberle, to keep records on what, where, and when panels are replaced. ‘By documenting the wear life of each panel, operations can better forecast any needs for replacement panels, allowing them to plan ahead and budget for yearly screen costs,’ he said.
Finally, LEAN screening is rarely seen in operations that choose to do nothing else but what they have always done. ‘Adhering to the same old wire cloth routine may seem a comfortable choice, until you look at the bigger picture,’ said Mr Eberle. ‘The goal is the highest yield of quality products, and the best use of your valuable time.’
Ultimately, LEAN screening gets the right products to the right stockpiles at the right time, to achieve optimum process flow, production flexibility and customer satisfaction.
Acknowledgement
Article reproduced courtesy of Aggregates Manager (www.AggMan.com)
- Subscribe to Quarry Management, the monthly journal for the mineral products industry, to read articles before they appear on Agg-Net.com