Technology in Screening
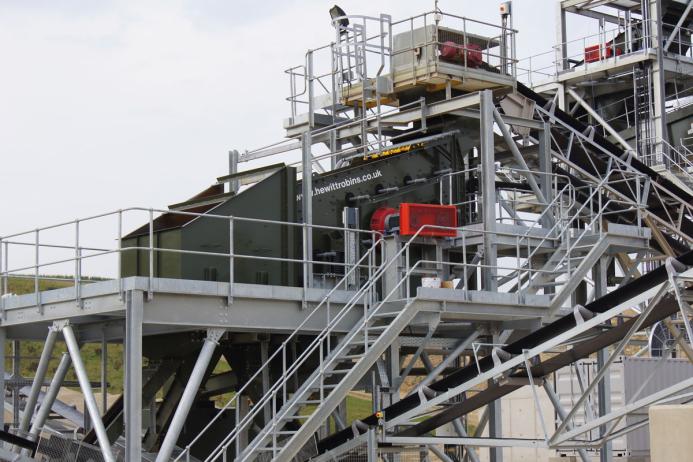
First published in the February 2025 issue of Quarry Management
Hewitt Robins offer some insights into how they apply new technological developments to different projects and applications
The development of technology has increased the tool kit which Hewitt Robins have at their disposal when it comes to the supply of vibrating equipment – from 3D scanning for CAD modelling through to developments in simulations that the company’s application engineers apply to new projects. The following short case studies provide individual insight as to how Hewitt Robins apply these techniques to different projects, solutions, and applications.
Capacity improvements in France
Hewitt Robins have had recent success improving a French customer’s screening capacity from 200 tonnes/h to 400 tonnes/h. Through careful screen selection and analysis of feed gradings, new machines using relief decks were able to double the performance of the existing units. This was guaranteed before supply using Hewitt Robins’ screening simulation software, which provides a screen capacity based on a raft of parameters (relieving decks being one of them). After inputting the customer’s application information, Hewitt Robins’ engineers were able to determine that these changes would offer a large performance gain on the same footprint.
In certain applications, relief decks aid screening performance by reducing the tonnage and bed depth of material reaching the critical deck. For this solution to be effective, however, there must be a significant amount of oversize material. If the material is mostly undersize it will fall through the larger aperture of the relief deck, rendering it ineffective. Application engineers can incorporate these factors into formulas to determine whether a relief deck is right for a particular application before supply.
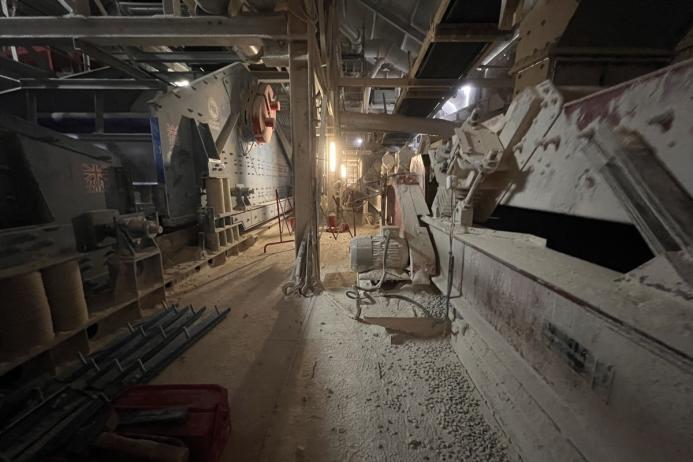
These machines can be tailored to fit into the existing structure and chutework, ensuring installation costs are kept to a minimum. This process allows Hewitt Robins’ designers to incorporate any additional changes the customer may want, in this case the modern self-synchronized pod design (fig. 1). This vibrating unit has the benefits of linear motion without the need for gears, thereby reducing the cost of maintenance in the long run.
Once manufactured, these machines are factory tested using state-of-the-art sensors to collect information on machine set up as well as natural frequency peaks, which helps ensure straightforward commissioning. These sensors can be installed permanently to provide remote monitoring, giving the customer up-to-date information on their screens’ performance and health.
3D scanning for screen installations
A great example of how modern techniques and practices are helping to improve screening is the use of 3D scanning, which allows designers to create a CAD model of any existing building/space. Alongside physical measurements, scanning allows Hewitt Robins to examine the real detail of where the machine will sit and gives the customer a visual representation of how everything will look after installation. This is not only great from a technical standpoint but also provides a strong illustration for the screen manufacturer to communicate with the installer to show what changes will be involved for a particular project, prior to the machine being manufactured. Any comments and changes from the customer/installer can be incorporated at a convenient stage. With tricky installations, where the new screen(s) are being modified to improve on the original machine(s), 3D scanning can prove essential.
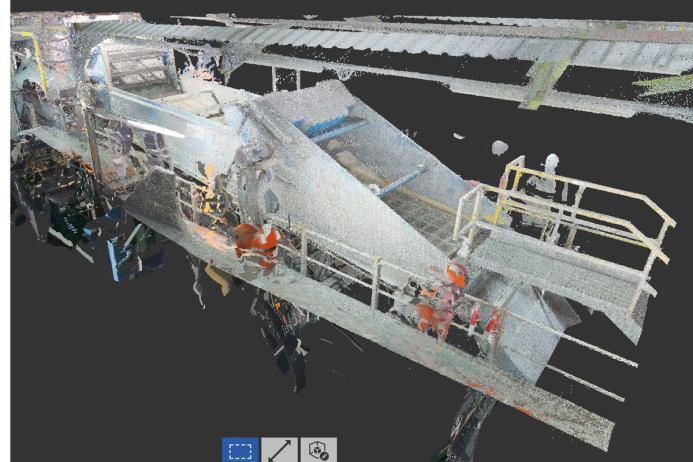
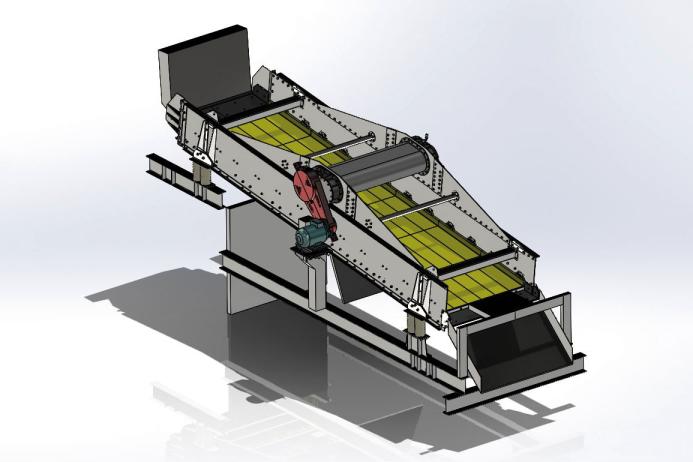
When a customer in South Yorkshire needed to update and replace their screens, Hewitt Robins’ designers used this new tool to aid in the swap, resulting in the images shown (figs. 2a and 2b).
Irish mine increases stroke
Hewitt Robins have enjoyed a long history of suppling heavy-duty machines to handle primary applications in mines and quarries, such as this underground zinc ore mine in Ireland.
The customer had an old resonance grizzly feeder which, due to its vibrator unit, had a low amplitude and was not able to choke feed the crusher. When the time came to replace this machine Hewitt Robins installed a twin-shaft unit with increased amplitude. As a result, the operator was able to choke feed the crusher, having to dial the new machine back with an inverter to suit the optimum feed rate.
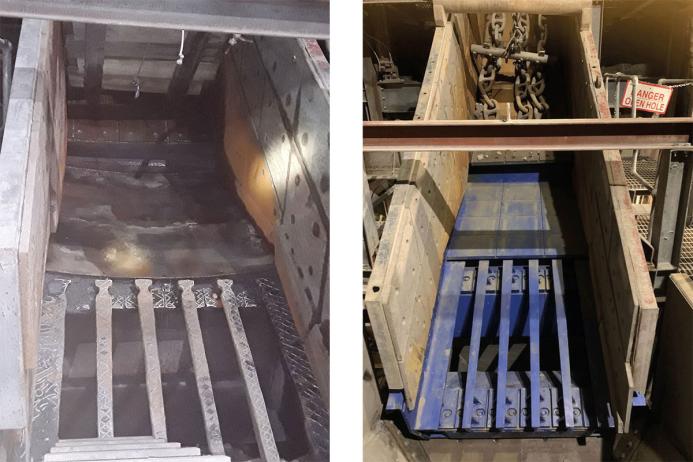
To increase the tonnage of a feeder, a wider machine is usually installed, as this helps throughput. However, as the feeder had to be replaced within the existing footprint, a wider unit was not possible. This meant travel speed was the remaining factor that could be optimized. Because the resonance unit on the existing grizzly had a low stroke, Hewitt Robins’ engineers opted for a new unit with an aggressive stroke. This improved the material’s rate of travel, thereby increasing the tonnes/h and allowing choke feeding of the crusher below (figs. 3a and 3b).
Hewitt Robins have supplied grizzly feeders as small as 50–100 tonnes/h through to units capable of 3,000 tonnes/h with deck loads in excess of 100 tonnes.
Health check pays off in Wales
Health checks are where an engineer is called out to troubleshoot a problematic screen. This can be anything from an application problem to general maintenance. Hewitt Robins support their old machines in situations where customer may not have knowledge of the ideal set up to optimize the productivity and lifespan of their screen.
A recent visit to South Wales was arranged to view a 10-year-old screen which, after other plant changes had been made, had become a bottle neck and had material tracking down one side. As the customer did not have a maintenance history, a visual inspection was performed and sensors placed on the machine to compare it with new. A report was then issued to site with Hewitt Robins’ findings and recommendations. It was discovered that the machine was running in natural frequency, which was likely the cause of the unusual material flow creating inefficient screening. In conjunction with the application information, simulations were conducted to see what performance could be expected from a screen of that size compared with its actual performance.
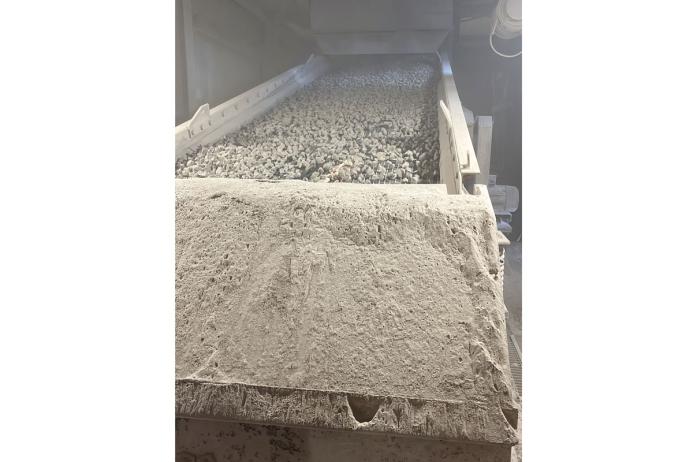
After all this information had been gathered and analysed, a speedy change was recommended to avoid a natural frequency peak, as was a reduction in aperture for the first few top deck mats to hold back material from the bottom deck. As a result, the customer reported increased efficiency, and that the material now tracks evenly down the machine (fig. 4).
For operators who think their plant could benefit from a health check or who have any other queries about vibrating equipment, Hewitt Robins’ engineers will be happy to advise on the best solution.
Subscribe to Quarry Management, the monthly journal for the mineral products industry, to read articles before they appear on Agg-Net.com