You’re Hired!
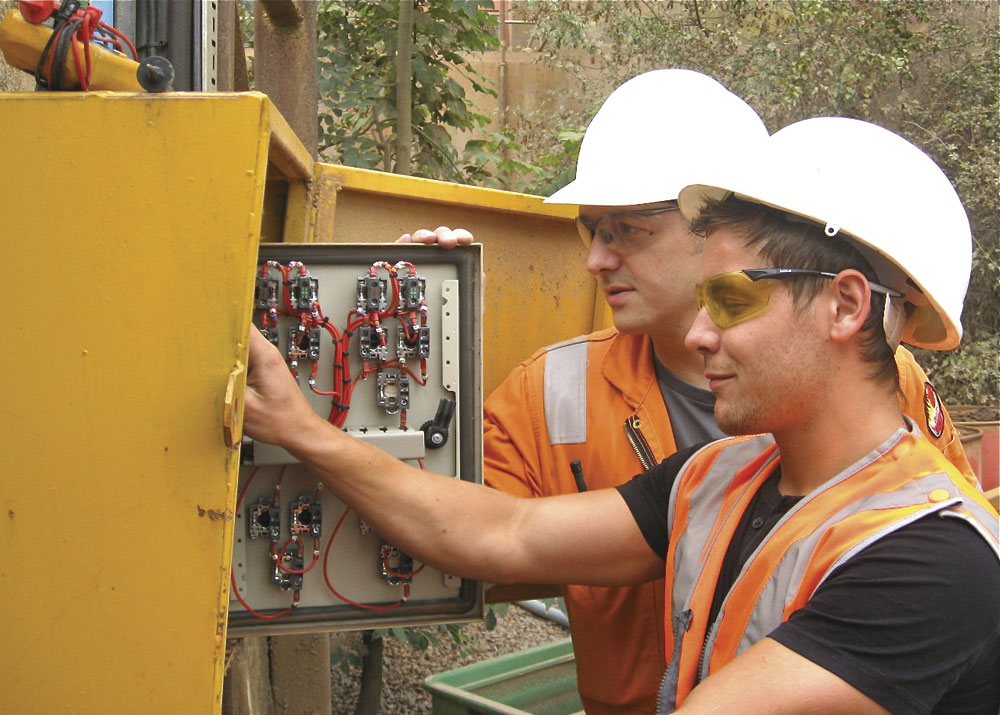
How Lafarge are using apprenticeship schemes to bring in new blood
Lafarge are one of a growing number of forward-thinking firms focusing on a traditional system to foster new talent. The aggregates and concrete arm of the business in the UK, based in Syston, Leicester, is using apprenticeship schemes to bring in new blood.
Last year, after a 24-month lull due to the recession, Lafarge Aggregates & Concrete UK (LACUK) took on 13 new apprentices, bringing the number of apprentices enrolled since the inception of the current scheme to 100. The new recruits, mostly straight out of school, filled roles in areas including business administration, production and mechanical and electrical engineering.
Chris Thompson, LACUK’s human resources advisor for aggregates, said: ‘Employee development is a priority for Lafarge. We believe that to have a truly sustainable business we need strong succession planning and employees with the right capabilities to take on greater responsibilities when opportunities arise.
‘Apprenticeships are one of the best ways for us to develop fresh talent, with candidates learning the ropes from experienced mentors but also improving their academic qualifications. These are truly modern industrial apprenticeships offering newcomers the chance to gain a broad range of both practical and theoretical skills.’
Britain has a long history of apprenticeships stretching back to the guilds of the Middle Ages.
In 1583 the system became more prescribed and regulated with the Elizabethan Statue of Artificers setting out terms and conditions for training. It took more than 200 years before further significant legislation came into effect with the Health and Morals of Apprentices Act 1802, which provided for a 12h day and a requirement that factory apprentices were taught reading, writing and arithmetic.
More recently, towards the end of the last century, the popularity of apprenticeships declined with the scheme labelled as archaic, male-dominated and ineffective. Government intervention ranged from a levy-funded programme to no support at all until 1993 when, due to concerns about skills shortages, plans for Modern Apprenticeships were unveiled.
Today, under the auspices of the National Apprenticeship Service (NAS), established in 2008, apprenticeship programmes are seen by candidates as a valuable way to earn and learn while they work, and by employers as a way to provide the skilled workers they need for the future. Anyone aged 16 or over can apply to become an apprentice but those over the age of 19 do not get 100% funding from NAS, which means the majority of apprentices tend to be older teenagers.
LACUK had run apprenticeship schemes over the years but it was not until 2001 that bosses started looking into launching a more structured apprenticeship programme covering the whole aggregates sector. They recognized that the demographic of the workforce, particularly at operational sites, was mainly above 40 and there was a dearth of young, fresh talent coming through the ranks.
However, they also realized that there was a huge resource of experience and knowledge within the existing, long-serving workforce that could readily be utilized to develop new starters. There was also a recognition that as a company committed to supporting its neighbouring communities, offering local job opportunities to local people was the right action to take.
The first new-style apprentice programme ran in 2003 with a varied number of positions open each year since then depending on organizational need and suitability of the role. Of the 87 apprentices enrolled between 2003 and 2008, 63 completed the two-year programme and 52 have remained at Lafarge. Generally, apprentices are taken on at the age of 16 or 17, with a few already having some experience of work or having undertaken college courses.
‘Each year we ask our managers whether they have a vacancy for an apprentice and then we look at the suitability of the prospective position,’ explained Chris Thompson. ‘There has to be enough work for them to do relative to their age, the job and the site. We’re not interested in bringing people in just to sweep the floor or make the tea; this is a scheme where the apprentice is part of the team right from the start, with real tasks to do and real responsibility.’
The programme runs for two years with day-release studies leading to NVQ qualifications at a college local to the apprentice. Lafarge, who have around 1,400 employees across the UK, work closely with Loughborough College in creating the programmes and identifying relevant courses.
College advisor Mike Manns is instrumental in organizing the educational element of the programme and he undertakes regular apprentice study reviews alongside Chris Thompson, who carries out job-specific checks. Success rates are high and every apprentice who has completed the two-year programme has been taken on full-time.
If candidates show significant promise and a suitable vacancy crops up, they may even be taken on full-time before the two years is up. Further opportunities for study and personal and professional development are also available once the apprentice is employed.
Mr Thompson said: ‘We are proud of our record with the number of apprentices who qualify, are taken on as staff and who stay with the company, but obviously there is some level of drop-out. At operational sites you tend to find if they make it through the first winter they are here to stay. Unfortunately, some apprentices get put off by the outdoor element of working at a quarry in inclement weather. There’s not an awful lot we can do about that.’
Last year apprenticeships were offered in the areas of business administration, production and mechanical and electrical engineering. With 13 apprenticeships, the number for 2011 more than tripled from the previous year’s intake of just two – a mark of increased optimism in economic growth and the need to boost supporting roles across the company.
LACUK are among 90,000 employers offering apprenticeships at a time of mass youth unemployment. Figures show that around one in five young people aged between 16 and 24 are out of work – one of the highest figures since these data were first recorded in 1992.
Lewis Taylor (aged 20), from Loughborough, was among four apprentices who joined in 2008, securing an electrician’s position at Mountsorrel Quarry. He had already spent a year at college studying electrical installation but was eager to get into work so began sending his CV to companies seeking apprentices. With youth unemployment running at alarming levels and fierce competition for apprenticeships, he was hopeful but not convinced he would strike lucky. But the knowledge he had already gained and his enthusiasm stood him in good stead.
‘Lafarge got back to me pretty much straight away and invited me along for an interview,’ he said. ‘I had my interview on a Friday and about an hour after I’d left I got a phone call saying the apprenticeship was mine.’
The teenager was quickly welcomed into the team and started work under the supervision of electrical assistant manager Simon Munday, himself a former apprentice taken on under an older scheme 12 years ago.
It was an enormous change for Mr Taylor coming face to face with the industrial intricacy of Mountsorrel’s plant compared to learning about domestic electrical systems at college.
‘The college course was a good grounding but I didn’t realize how different the work would be to what I’d been used to,’ he said. ‘There we focused on domestic electrics but obviously at Mountsorrel it is more complex and industrial, with motors, conveyors and lots of high-voltage equipment.
‘It was obvious right away that the role carried quite a lot of responsibility. If something goes wrong with a motor or conveyor it needs to be corrected as quickly, but also as safely, as possible. Hold-ups can have a major impact on production and that can have a major impact on the business.
‘But the safety element was stressed at all times. I was told no task was worth putting my health in danger and it really impressed me that the commitment to health and safety was so ingrained and such a priority for the business.’
Mr Taylor was also encouraged by the scope for progression within the company – taking his boss, Simon Munday, as a prime example. Although the apprentice scheme he joined differed from the more modern version, it still allowed for further training and career development.
Also a Loughborough local, even attending the same schools as Lewis Taylor, 32-year-old Simon Munday has risen through the ranks, gaining both an HNC qualification and a degree in electrical engineering during his decade or so with the company.
Mr Munday said: ‘If you think you can do it and show ambition, Lafarge will support you. It was clear to me, the same as it has been for Lewis, that if you wanted to progress the backing would be there.
‘When I left school I actually wanted to be an accountant but I didn’t have any luck with my applications so I turned to electrical engineering with no experience or knowledge of the subject at all. I don’t regret making that choice though, and thanks to Lafarge I’ve improved my academic credentials while also achieving a position of responsibility within the organization.
‘It proves that apprenticeships are worth it, and that you don’t have to get hands on with rocks and sand to carve out a successful career with a quarrying company.’