TWS to launch Aggrescrub 150 at Hillhead
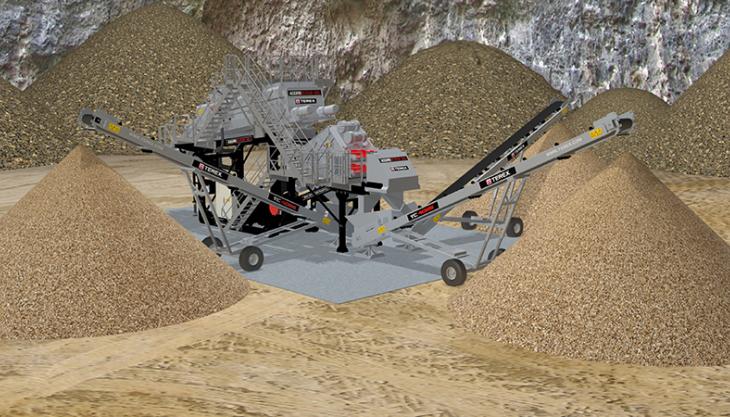
Terex Washing Systems will be showcasing the latest addition to their washing product portfolio
HILLHEAD will provide the stage to showcase the latest addition to Terex Washing Systems product portfolio, the Aggrescrub 150, which is designed to operate both as a stand-alone unit as well as having the ability to seamlessly integrate with the Aggresand range. The Aggrescrub 150 is designed to deal with stubborn clay-bound material which cannot be removed by rinsing or screening alone, making this plant a much more efficient and effective solution.
Terex Washing Systems (TWS) are showcasing the Aggrescrub 150 alongside the Terex Aggresand range, including the 165 (up to 250 tonnes/h) and the latest addition, the new and larger Terex Aggresand 206 (up to 400 tonnes/h), in what promises to be a great double bill.
A gap in the market for such a washing evolution was identified following extensive research, part of which was conducted at the TWS product development forums. This involved TWS engineers and sales technicians working with the global distributor network to formulate the concept.
Central to the development of the new plant was modular design, serviceability and functionality, making it quick and easy to set up and maintain. The plant also includes a range of other innovative features and designs including a web-frame chassis which is easily assembled and complementary to the Aggresand range. The chassis supports the scrubbing hull, the 6ft x 2ft trash dewatering screen, the 12ft x5ft two-deck rinsing and sizing screen, and has an integrated sump and pump. Fully galvanized walkways provide access to all areas of the plant.
In operation, clay-bound aggregate is delivered to a reception chute where the material is flushed with water. The reception chute employs a dead-box design which offers superior wear characteristics. The material is then aggressively scrubbed in the hull by two AR shafts with a spiral of blades and paddles attached.
The design of the shafts causes aggregate to collide with aggregate, ‘rock on rock’, which liberates the clay conglomerates. The liberated clay material discharges through the troughs at the rear of the plant (along with wood, plastic, roots, grass etc) for subsequent dewatering on the 6ft x 2ft dewatering screen, with the light and organic material delivered directly to a skip or stockpiled by conveyor.
Dirty water recovered by the dewatering screen is captured in a rubber-lined pan and piped to the integrated sump below the hull. The hull angle is variable between 9° and 11°, to control the retention time and throughput levels.
TWS offer three choices of blades/paddles including 15mm AR 500, 30mm AR 500 and specifically designed and forged manganese blades. The twin electric motor and gearbox design provides another benefit for customers, comprising two 22kW electric motor and gearbox arrangements for efficient direct drive.
The 12ft x 5ft aggregate screen receives the scrubbed aggregate from the hull. The two-deck screen not only sizes the aggregate, but also rinses off any grit which may still be stuck to the aggregate after scrubbing. The rinsed grit is captured and delivered to the integral sump tank. The two-deck screen, which uses high-quality polyurethane decks to size the aggregate into three stockpiles, employs a compact rolling chute assembly (patent pending) for good access and serviceability.
TWS have developed a cutting-edge but user-friendly control system for the Aggresand plants, which has proved a huge success. The same system has been adapted for the Aggrescrub to give operators levels of automation and control that have not previously been available on wash plants. Using advanced PLC technology, the control system will provide measurement and display of water pressure, pump pressures, motor currents etc. Radio control of all main functions is available as an option, as is remote telemetry, which will allow all data (alarm conditions, run times etc) to be sent to the plant owner remotely, through email or SMS alerts.