Trio of Kleemann machines for Simcox Construction
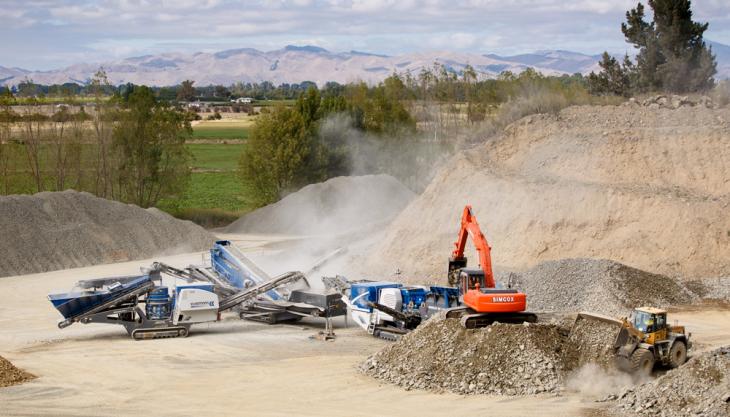
New Zealand quarrying and construction contractor switches to German crushing and screening technology
TWO Kleemann crushers and a Kleemann screening plant have commenced work in the quarries operated by New Zealand construction contractors Simcox Construction in the Marlborough region located at the top end of the country’s South Island.
Those responsible at Simcox were immediately impressed with the German technology: ‘Everything is so much faster and there is far less downtime compared with our old machines,’ said general manager Antony Clark.
The three Kleemann plants – a Mobicat MC 110 Z EVO jaw crusher, a Mobicone MCO 9 EVO cone crusher and a Mobiscreen MS 16 D screening plant – are the first of their kind in New Zealand and are being used to process greywacke for use, among other things, as a basecourse in road construction.
In the first crushing stage, material ranging from 0–400mm in size is fed into the MC 110 Z EVO. Pre-screening takes place using the machine’s independent double-deck pre-screen, with the pre-screened material transferring directly to the main discharge conveyor via the bypass.
Next, the material is conveyed from the MC 110 Z EVO jaw crusher to the MS 16 D screening plant, where the –20mm fraction is separated and discharged, while any +20mm is fed into the MCO 9 EVO cone crusher to produce a 0–20mm material which is returned to the screening plant for further screening in a closed circuit (pictured).
Once the decision to invest in Kleemann equipment had been made, Simcox wanted the plants to be commissioned as soon as possible.
‘Gary Payne from Wirtgen New Zealand put the wheels in motion,’ said Mr Clark, with the result that the crushing and screening plants were delivered within a few weeks. ‘Having the first machine on site right on time without disruptions to our schedules was crucial for us – and confirmed we had opted for the right partner.’
The plants’ performance was also impressive: ‘Our biggest benefits are greater efficiency and increased production,’ said Mr Clark.
Plant operator Richard Price agreed: ‘I’ve been involved in the quarry industry for more than 30 years and I’d never actually seen a Kleemann before our machines arrived; I was sold on them pretty quickly.
‘In the event of a material accumulation, the plants are all self-regulating. That sort of smart technology is great because it’s protecting the integrity of the machines, which means they should be able to provide us with consistent crushing for a long time.’
Simcox are now managing to process such large quantities that, for material feeding, they have had to change from a 12-tonne to a 23-tonne excavator in order to fully exploit the plants’ capacity.
Furthermore, an additional wheel loader is being used to haul away the end products. Based on this experience, Simcox said it soon became clear that investment in Kleemann equipment pays off. ‘The implementation of these technologies is a big step forward for us,’ said Mr Clark.