First Volvo paver for Saxby Surfacing Contractors
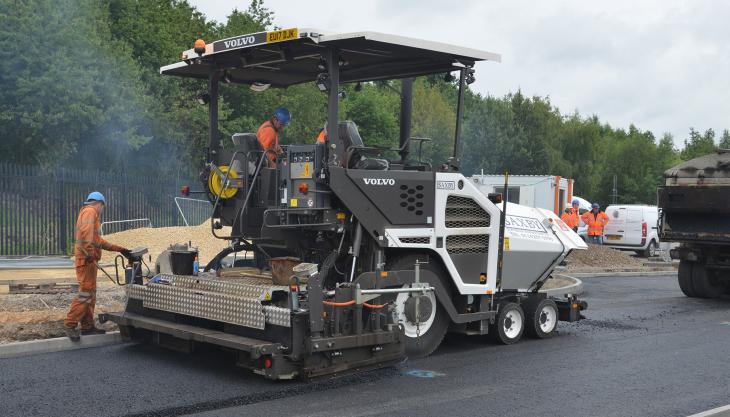
Yorkshire-based family firm celebrate 30 years with new fuel-efficient P6870C ABG paver
SHEFFIELD-based Saxby Surfacing Contractors are entering their thirtieth year of trading and, to commemorate the event, have taken delivery of their first Volvo paver – a P6870C ABG model.
Run by the Saxby family, the company operates throughout the Yorkshire region for a wide-ranging client base, including local authorities, house builders and developers.
Over the last three decades the company has used a variety of pavers, initially favouring the British-made Blaw Knox machines before moving to other manufacturers. ‘We run three machines full time, including a mini-paver, which seems to be the busiest,’ said Ian Saxby.
Looking to replace one of the company’s larger machines with a new model, Mr Saxby contacted a number of suppliers and contractors for feedback on what was available in the market. ‘We were obviously aware of the Volvo machines, but had not tried them in the past,’ he commented.
‘When I called Volvo, the response was immediate. They couldn’t do enough to help me. We soon had a machine on demo, which was accompanied by a qualified Volvo engineer, whose help and expertise was invaluable.’
Having worked through the specification process with Volvo’s road equipment sales manager, Matthew Sheridan, Mr Saxby claims he now has the best paving machine he has ever had. ‘Everything about the paver is first class,’ he remarked. ‘It is built to do the job and do it well.’
Constructed around a tried and tested chassis, the P6870C employs a 6x6 drivetrain that allows it to work in even the most difficult conditions. The majority of drive for the vehicle is from the large rear wheels with additional drive coming from both sets of steering, load-dependent front wheels. A tight inner turning circle of just 2.5m allows the large paver to operate in the tightest of locations.
According to Mr Saxby, the view from the operator’s seats is ‘simply the best’. ‘You can see what you have in the hopper, what’s happening over the screed and exactly where you are in relation to the kerb,’ he said.
Both Mr Saxby and his team are also very happy with the straightforward, easy-to-use, intuitive control layout on the Volvo, which is very quick to respond when needed. The large and easy-to-read screed control units (SCUs) are mounted either side of the hydraulically adjustable, electrically heated screed unit, whilst the main control unit (MCU) is movable across the full width of the machine, allowing the operator to be in the ideal working position at all times.
The extending operator station allows for good visibility on either side of the machine, with protection from the worst of the elements provided by an all-weather roof. The detailed yet easy-to-use MCU allows for instant adjustment of each part of the paver thanks to the installation of EPMII, Volvo’s electronic paver management system.
The paver is powered by a fuel-efficient, Tier 4i, Volvo 6-litre engine capable of delivering 175hp at 2,000 rev/min. When paving conditions do not require the use of full power, the operator can select Smart Power Mode through the MCU, reducing the engine to 1,600 rev/min and resulting in substantially lower noise and up to a 30% reduction in fuel consumption.
A range of screed options is available on Volvo pavers, with Saxby taking the smaller 2–5m version. ‘This is an ideal size for our operations,’ commented Mr Saxby. ‘It gives us the flexibility we need on some of our jobs and keeps the weight of the machine down too.’
The machine’s large, 12-tonne capacity hopper allows for continuous paving with the folding front flap ensuring good material retention at all times. Independent reversible drives for both conveyors and height-adjustable augers supply a constant flow of material to the screed, and a newly designed and through-hardened tamper bar improves durability and reliability.
Whilst Mr Saxby says he does not have a dedicated fleet-replacement schedule, the Volvo will be kept in the company for at least five years. ‘The build quality is far superior to what we have had in the past and, if it is performing well, we may keep it longer,’ he said.