Edge introduce the RS1500 roll-sizer
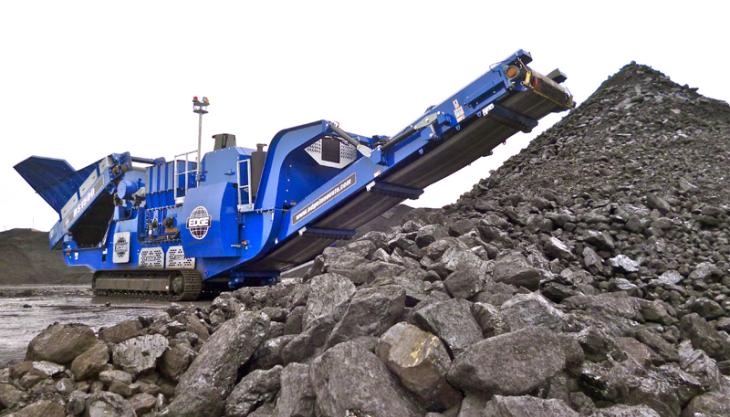
Robust and versatile mobile roll-sizer machine designed for use in the quarrying and recycling sectors
BUILDING on the success of new products launched in 2013, such as the Slayer XL, the MS100 and the 360° Unlimited range, Edge Innovate (NI) Ltd have recently unveiled the newest member of their materials-handling range, the RS1500 mobile roll-sizer for the quarrying and recycling sectors.
Designed to process a wide range of materials, from coal, lignite, bituminous, and sub-bituminous materials to sticky materials, friable materials, soft ores, limestone, salts, glass, recycled concrete and tarmac, the RS1500’s robust and innovative design is coupled with high manoeuvrability and a small footprint.
Key features include: a highly efficient hydraulic drive system; tramp metal release; easy select sizing controls; intelligent hydraulic load-sensing system; and a five-function remote control.
The full HMI control panel provides easy fine-tuning for accurate application performance and allows for automatic start/stop operation as well as providing visual data output, such as engine load, individual shaft pressure, hydraulic oil temp and fuel consumption, while the machine is still operating.
Powered by a Tier 4 Caterpillar C9 260kW (350hp), which offers full torque while consuming just 25–30 litres/h, the RS1500 has the capacity to process 250 tonnes/h with a maximum feed size of 400mm.
Material is fed into the RS1500 via seven cubic metre capacity hopper and carried to the machine’s pre-screen on a 1,400mm wide, heavy-duty, variable-speed belt with full-length impact bars. The feed hopper boasts a hydraulic sliding function to allow quick transition from transport to operating position.
The single-deck, two-bearing pre-screen allows fines to bypass the chamber, thereby increasing processing efficiency and throughput. An easily retrofitable optional side conveyor is available to stockpile diverted fines separately.
The roll-sizer chamber has the ability to handle wet and sticky materials and employs an intelligent load-sensing system to prevent overloads. The tooth rotor design allows undersize material to pass through the precision-designed shafts to increase product throughput. The shafts are designed to ‘grab’ the feed material and reduce it to the desired product size while creating minimal fines.
The RS1500’s automatic sensing system protects the roller shafts against tramp metal or trapped material, thereby reducing maintenance costs and downtime. The chamber houses two variable-speed, reversible roller shafts, both of which are independently driven and controlled via the HMI control panel.
Material is stockpiled via a 1,150mm wide heavy-duty product conveyor which provides a discharge height of 3,560mm, creating a stockpile volume of 77.5 cubic metres or 125 tonnes. Impact bars underneath the roll-sizer chamber take the impact from the processed material prolonging the life of the conveyor belt. The hydraulic folding head section allows for quick transition from transport to operating position.