DISAB BagVac cleans up at Linhay Hill Quarry
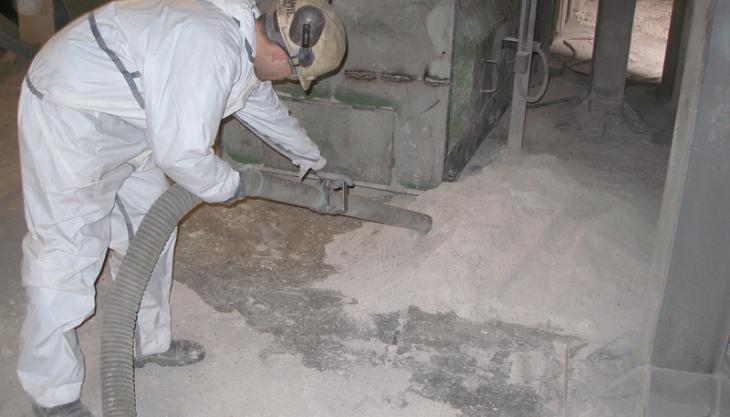
System ‘more than lives up to expectations’ of waste-management strategy
IN 2010, E&JW Glendinning purchased a DISAB BagVac and fixed pipework system as part of a larger investment programme in new asphalt, crushing and screening plant at their Linhay Hill Quarry. The company’s waste-management strategy is aimed at saving time and money coupled with recycling waste, a strategy that is proving highly popular with its employees.
The investment programme was to replace plant that had reached the end of its engineering life, and the first major item was a new £2.5 million asphalt plant in March 2010. It was designed and built with fixed pipework and inlet valves on all four floors (screen, hot-stone bins, mixer and skip levels) so that, for the first time, all floor areas and surfaces could be reached with a DISAB BagVac’s 60ft flexible suction hose.
Neil Gibbs, manager of Linhay Hill Quarry, commented on the efficiencies gained: ‘Previously, our quarry operatives would have done all this manually using brushes and brooms, shovels and barrows. On the upper floors of any plant, sweeping all the dust and waste into a pile is one thing, moving that down to ground level for collection and removal is quite another.
‘In addition, because of the very fine dust these processes create, brushing makes more dust and there’s a significantly higher risk of dust exposure to our employees, something that we were determined to eliminate through design. As a result, in each of the new plants, fixed pipework systems were built in and inlet valves were provided on each floor so that the flexible suction hoses could be attached.
‘With completion of the investment in 2012 the full potential of DISAB BagVac was realized, as our plant operatives were then able to use it to power the pipework system in all the plants and suck up everything in the way of dust and waste up to 50mm in size. This has made a dramatic difference to the dust and waste-removal efficiency, and, as importantly, has minimized the risk of dust exposure.’
Mr Gibbs continued: ‘In terms of how much dust and debris is removed, it’s around one IBC bag a week or approximately one tonne from all three plants. All we have to do is to move the BagVac with a forklift or telehandler to wherever it’s needed alongside the plant, connect it to the pipework inlet, turn the BagVac on and it’s ready to clean each floor and every surface.
‘On the crushing and screening plant, we set aside about three-quarters of a day a week for plant maintenance, which includes cleaning and housekeeping tasks, but on the hot asphalt plant we usually do the cleaning on a Saturday morning. All the material is collected in the IBC bag and then put back into the process, so there’s zero waste.
‘The DISAB BagVac has more than lived up to all our expectations. As the key cleaning system on each plant, the BagVac ensures all the possible dust, debris and waste it can handle is removed safely and efficiently. The use of a plant vacuum system is clearly far more efficient than brooms and brushes. Everything goes into the collection bag, and from nozzle to bag it’s a fully enclosed process.’
Mr Gibbs continued: ‘It’s also far more popular with our employees, who no longer have to face the back-breaking and very laborious chore of doing this manually, and of course, they know they’re working in an environment that’s relatively dust-free and in which the risk of dust exposure is minimized.
‘All this makes a difference to the external inspections as well,’ added Mr Gibbs. ‘When BSI come to inspect our product quality, a clean and dust-free plant is a major factor in their audit. Processing plant that’s kept clean means quality end product for our customers. In what we all know is a very competitive marketplace, that kind of endorsement is priceless when it comes to winning and retaining business.’