Radar Reliability Increases Productivity for E&JW Glendinning
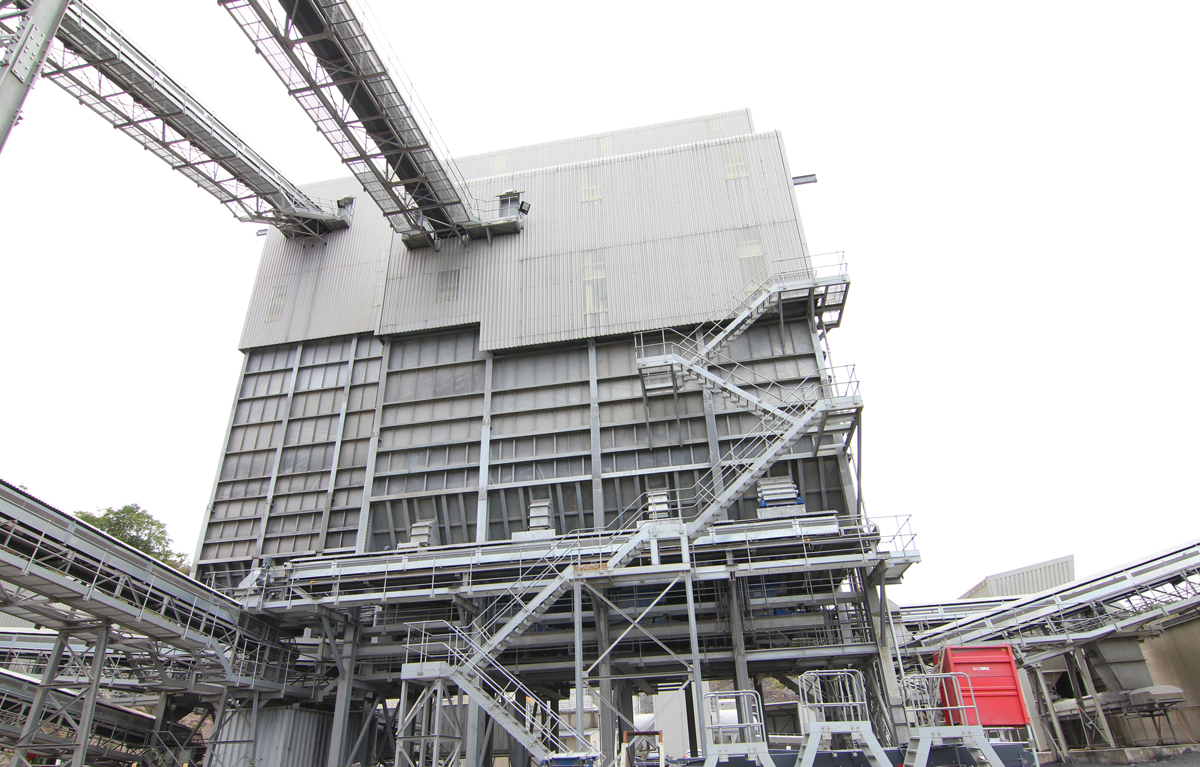
First published in the August 2019 issue of Quarry Management as Radar Reliability
Innovative 80GHz radar reliability increases productivity in the screen house for E&JW Glendinning
Following extraction and crushing, the screen house is very often the ‘engine room’ of a quarry where aggregates are processed and graded. Its principle function is to sort aggregates into various sizes and ensure the right product is available, ready for coating, stockpiling or direct load-out to transport. The main process challenges encountered in the screen house are the high levels of dust, noise and vibration, from both the screens themselves and other associated machinery, making it a very inhospitable environment for quarry personnel.
At Linhay Hill Quarry, in Devon, E&JW Glendinning have replaced the ultrasonic level sensors in the screen house with the latest generation of VEGAPULS 69 contactless bulk solids radars. This followed on from the previous successful application of the same radar technology on the secondary crusher feed hopper level a couple of years ago, which transformed the reliability and control in that key area of the plant.
Why the change?
According to Glendinning, the ultrasonic level sensors were regularly giving false indications throughout their measurement range, which meant lost time and productivity, both on the lorry-loading process and infeed control. To keep them working, the sensors required regular maintenance, cleaning and adjustment, with false signal mapping of the silos. Although problems with individual sensors were infrequent, maybe a few times per year, when multiplied by tens of sensors, along with the associated outages and delays, it became a significant problem.
In a typical example of these outages, the plant operator would start to load out to a lorry based on the initial level reading of a particular grade, but then be unable to complete the loading process due to the bin running empty and the lorry having to be topped up by a loading shovel from the quarry stockpiles, thereby losing time, causing additional traffic movements around the site and taking resources from other areas of the quarry. Once a loss of trust in level readings takes hold in this way, it can be difficult to regain.
Materials involved
The materials measured at Linhay Hill Quarry are from 0–4mm with very high dust levels inside the bins, up to 60mm in size where high levels of filling noise can also be encountered. The sensors are deployed across nine bins (see SCADA image). The plant has a 600 tonnes/h load-out capacity for road-going lorries and internal dumpers that feed the ready-mixed concrete and block production plants. An accurate ‘picture’ for the operators is, therefore, a key element in the efficient running of the plant.
Costs and installation
As the fastest-growing level technology for bulk solids, radar-based level sensors are often not as expensive as people think. The price is equivalent to high-power ultrasonic sensors, which are often used in applications with high dust levels. The difference, when coupled with the performance increase, becomes very marginal, but the payback from the use of a more reliable solution can be very quick indeed.
The installation in the screen house at Linhay Hill Quarry was easy; the sensors were supplied with flanges to match the existing sensor locations and were also able to utilize the existing cabling. This new 80GHz radar technology also has an extremely capable measuring range, from just a few hundred centimetres up to 120m, offering great versatility for solutions in silos, hoppers, crushers etc, and even fast-change response for conveyor positioning. A sister device, an 80GHz radar for liquids, is suitable for bitumen tank levels.
Why radar technology?
The reason why radar technology is better for level measurement in this application is because it uses microwave signals and is unaffected by any in-flight dust, air movement, pressure, temperature or filling noise that can affect ultrasonic sensors. In addition, the new 80GHz radar has superior focusing. A 3.5o beam angle is typical, so it can easily avoid any build-up on the sides of the bins and focus entirely on the product level, from top to bottom. The higher frequency is also unaffected by even very large amounts of aggregate dust build-up on the transducer face, which again can quickly attenuate ultrasonic sensor signals. A question that is often asked is: Is microwave-based radar safe to use? The latest-generation radar devices are safe; they conform to EN LPR (Level Probing Radar) standards, so they can be used inside or outside the plant with absolutely no risk to personnel.
The outcome
Since the installation of the new sensors, Glendinning have seen an increase in plant throughput. The operators are able to control and trim bin levels efficiently. The level increase and decrease is followed in a smoother, more accurate manner, offering a truly ‘analogue or dynamic’ representation, rather than the series of jumps and steps they had before. Also, because there are no false high level alarms, the plant does not place the infeed on hold unnecessarily either, as the levels seen on the SCADA screens can be trusted. Moreover, there has been a decrease in traffic movements around the site, with the reduced pressure on the stock-loading shovels, freeing them up to load the products they are designated for. Likewise, reduced demands on the electrical, control and instrument engineers frees their time for other projects and proactive maintenance, as well as reducing their exposure to risk. Glendinning subsequently purchased another set of radar sensors for their coarse screens, to complete the efficiency improvements across the entire screen house.
The future
The site is now also utilizing another VEGA innovation: a Bluetooth sensor set-up and maintenance tool. Using a smartphone, tablet or PC with Bluetooth, all VEGA devices can be easily and safely commissioned and monitored with ease. The VEGA Tools iOS or Android app can be downloaded for free and allows any ‘plics’ transmitter (even all those manufactured since 2002) to have Bluetooth capability to securely communicate via encrypted, protected communications. This increases speed of set-up and removes the need for personnel to climb silos or work in hostile locations.
For further information visit: www.vega.com/uk
- Subscribe to Quarry Management, the monthly journal for the mineral products industry, to read articles before they appear on Agg-Net.com