The Black Art Of Belt Weighing
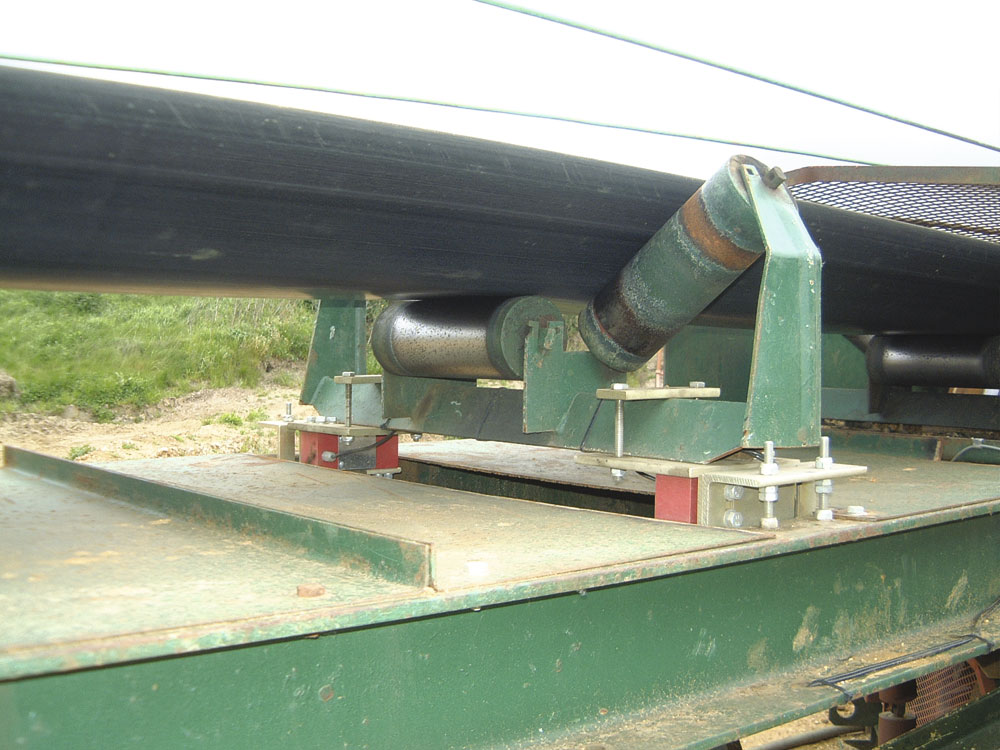
Dispelling some of the myths about belt weigher installations
There is a common fallacy that you need to have studied the ‘dark arts’ to be able to install and calibrate a belt weigher. This article aims to dispel some of those myths.
A belt weigher follows the same physics as a road weighbridge or shop scale with a few extra complications. The difference is that there are more forces acting on the weighbridge of a belt weigher than on a platform weigher. These forces need to be understood and reduced to a minimum. Good application engineering is critical as there is a requirement to understand what forces are occurring on a conveyor system and how this will affect the accuracy and long-term repeatability of a belt weigher installation.
The function of the electronics
A belt weigher is an integrating device, similar to a speedometer in a car, which integrates (multiplies) distance with time. The speed of the belt (technically the belt displacement) is multiplied by the weight of material on the belt thus giving weight per unit time. In Europe this is commonly termed tonnes per hour and totalized tonnes.
The problem with this type of measuring technique is that only a small proportion of the total load is passing over the weighing area at any point in time. This means that any error in the commissioning of the weighing equipment is accumulated and can appear as a large error in the final total.
Cost of ownership
The author has been involved in belt weighing with four different companies since the 1970s and has gleaned that part of the myth of belt weighing has been perpetuated by belt weigher suppliers who run a service department and wish to keep their technicians employed. The majority of belt weigher problems can be solved over the phone, thus saving the end-user a considerable amount of money in service visits.
Idler alignment
Attention to detail in the area of the weighbridge mechanics is fundamental to good belt weighing. Ideally, there should be two lead-in and two lead-out idler sets that become part of the weigh platform. These should be raised above the normal belt line by a minimum of 10mm along with the weigh idler(s). String lines, preferably two per idler set, should be used to align all of the idlers within 0.5mm of each other. The idler sets should also be square to the belt. In critical applications the idlers should be machined and balanced so that the TIR is within 0.5mm.
Conveyor design
The conveyor in the area of the belt weigher should be rigid, as any flexing of the conveyor structure in the area of the belt weigher will cause errors. Ideally the weigher should be placed on a horizontal section of the conveyor with multiple support points. This, of course, is usually not practical, so the conveyor has to be carefully surveyed and the best compromise found for the weigher position.
Belt tension vs material download
The greatest conflict with any belt weigher is the download pressure versus the belt tension. The more the belt is tensioned, the less the apparent material download on the weigh section. Changes in tension can be caused by a number of factors, the commonest being changing amounts of material on the belt and multiple feed points. On a screw-tensioned belt the tensioners are used to track and tension the belt. As the resultant change in tension can cause weighing errors, once the screw tensioners have been adjusted, the weigher should be re-calibrated.
Weigh length determination
In order to determine the required weigh length for accurate weighing, t1 and t2 need to be determined. This may sometimes be supplied by the conveyor manufacture or can be calculated. For very high-accuracy and critical weighing applications, the following data needs to be determined in order to engineer the application correctly:
- maximum tonnes per hour
- maximum belt speed
- belt width
- idler roll diameter
- conveyor centres
- height of conveyor
- angle of drive wrap
- gravity or screw tension
- bare or lagged drum
- height between feed and discharge points (work done)
- material bulk density
- idler troughing angle
- material surcharge angle
- GTU (gravity tension unit) mass
- motor size
- conveyor angle.
The tension in the conveyor belt caused by the material weight and the motor torque can now be calculated. Whichever value of tension is greater is then used to calculate the required weigh length to give an accuracy of 1.0%, 0.5% and 0.25% over a period of six or 12 months.
GTU
A conveyor belt should be tensioned with a GTU. This has many advantages both in conveyor belt life and for a belt-weighing system as the belt tension is kept relatively constant.
Belt troughing
The most suitable belt for weighing is flat. The deeper the troughing angle of a belt, the greater its mechanical stiffness. A simple example of this is if you try to hold a sheet of paper horizontally, it will flop. If you fold up the edges it will tend to stay horizontal and, in the extreme, if you put a crease along the length of the paper in the centre, it will become rigid.
The same theory applies to a conveyor belt — the deeper the trough, the greater the rigidity. To determine how much this will affect the weighing, the volumetric utilization of the conveyor needs to be calculated, ie how much material will be passing over the weigher at any point in time. From this information the range of material flow can be assessed that is required for accurate weighing. This figure is expressed in a percentage of the maximum flow of material. If a user requires an accuracy of ±0.5%, the supplier may need to state that this is achievable between 50% and 100% of the maximum flow rate. Below this figure the system will probably become non-linear and unpredictable. If a constant flow rate can be maintained at a lower flow rate, however, the belt weigher can be calibrated at this point and will usually maintain its accuracy. If the flow rate changes, then errors could result.
Belt tracking
It is hard to assess the change in accuracy that a poorly tracked belt causes. This is probably because the material tends to run in the same place relative to the idlers but on a different place on the belt. The main problem appears to be that there are additional pressures on the wing idlers that can cause errors. If the mechanical alignment has been carried out correctly, however, the problem can be minimized. It has been observed in some applications that tracking idlers can cause a bigger problem than poor belt tracking. It is recommended that the root cause of poor tracking should be found and resolved.
Seasonal changes
Probably one of the commonest sources of error in a belt-weighing system is the changing size of a conveyor due to temperature changes. In more moderate climates, such as in the UK, this is not always so noticeable but in extreme temperatures, such as the Arctic Circle, the change can be seen in a few minutes. In this case it is due to the stiffening of the belt rather than the metalwork changing shape, but temperature does have a very significant affect on weighing accuracy.
To reduce these effects the belt zero needs to be performed when the belt is up to its working temperature. This simply involves allowing the conveyor to run for a period before performing a belt zero; the zero should be performed as often as is necessary. If the conveyor is run empty, the rate value (tonnes/h) can be observed. It should be changing and moving negatively and positively depending on which part of the belt is currently moving over the weigh area. If the value remains high in either direction then a belt zero is required; this should be checked at least once a day.
Why have multi-idler weighers
In order to get high accuracy and repeatable weighing from a belt weigher, a multi-idler weighing system may be required. A multi-idler weigh carriage increases the resident time of material in the weigh area, and the longer you get to measure the material the more likely you are to get it right. This can be particularly critical with high belt speeds and low throughputs, and in the case of applications such as waste disposal, low throughputs, very low bulk densities and wide belts, sometimes with deep troughs. Low throughput systems are always more difficult to engineer than, for instance, a 4,000 tonnes/h application.
Conclusion
Despite everything that has been stated in this article the fact is that many belt weighers are installed without any real knowledge of the required application and a great number work. Things begin to go wrong when a supplier has not understood that the application is difficult and may require greater scrutiny. It is generally these cases that give the belt weighing industry a bad name. There have been cases where belt weighers have been installed in a catenary where the belt does not touch the weigh idler until it is loaded, this is particularly prevalent on mobile plant. Any good weighing company can advise an end-user on what is needed to achieve the required weighing standards and, if necessary, send an engineer to survey the application.
The author, Jon Scarrott, is managing director of Lodestone Electronics Ltd