Industry 4.0 perspectives for the aggregates industry
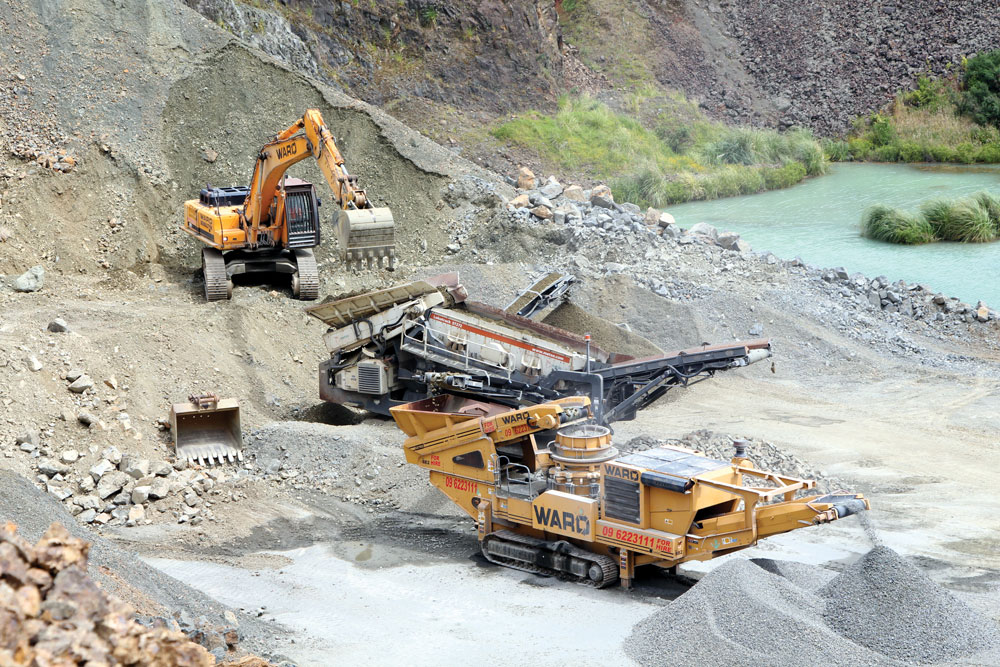
First published in the March 2017 issue of Quarry Management as The Fourth Industrial Revolution
By Sören Schramm, regional product application manager for aggregates, Trimble
While some argue about whether we are in a new industrial revolution, it is clear that the era of the digital enterprise or ‘Industry 4.0’ is upon us. Policy-makers and technology providers have embraced the philosophy as the ‘Fourth Industrial Revolution’ or the Industrial Internet of Things (IIoT) for its promise to converge information and communication technologies to transform the way producers run operations. With national leaders’ energetic support of Industry 4.0, and investments made by GE, Cisco and others, the digital enterprise will be a driving force for years to come. In fact, Accenture estimate that the IIoT could add US$14.2 trillion to the world economy over the next 15 years.
Big data meets IIoT
In an Industry 4.0 ecosystem, all devices or ‘things’ in a factory or manufacturing process have sensors that are connected to the Internet. These sensors stream massive amounts of data back to the manufacturer, who can then use software and analytics to interpret the data to support real-time decision-making.
Connecting digital technologies with industrial products and logistics is not an entirely new concept. The mining industry, for example, has applied this approach for years. Today, pressure on aggregate product margins due to competition and the rising costs of production is just one of the factors pushing aggregates producers to rethink the way they work too.
The rise of Industry 4.0 in the aggregates sector
Improvements in cloud technology and cloud-based applications are also helping to advance the concept of the IIoT and universal data exchange in the aggregates industry. Before the era of enterprise cloud computing, collecting and storing a vast amount of data was an almost impossible task for most small and mid-size manufacturers, including quarries. Most managers would have been overwhelmed at the prospect of managing data centers and IT systems, in addition to running day-to-day aggregate operations. But now technology is getting simpler, faster, easier to use and less costly than ever before. This makes technology adoption and deployment possible for small and mid-size aggregate operators.
Industry 4.0 concepts and the seamless transfer of data between quarry productivity applications − such as machine control, wheel loader scales, measurement tools, planning and load-out applications, and fleet-management systems − is changing the aggregates business now and for the future. By connecting data between production equipment and systems, managers get a more holistic view of site operations, with the ability to create valuable production and performance reports for extraction, processing and load-out operations.
The Industry 4.0 ecosystem allows for a streamlined quarry workflow in five main areas – extraction, processing, load out, inventory and transportation and distribution:
Extraction
Excavator scales, wheel loader scales and haul truck management systems let managers track pit loading and haulage targets and estimates automatically. Data can then be analyzed and reports created that allow for continuous improvement; this eliminates the guesswork or ‘gut feeling’ that used to govern much of the extraction process.
Processing
In a quarry environment that ties weighing systems, such as belt scales, with mobile production management applications, the need to manually track throughput and final tonnage is eliminated. For instance, measurement tools on the belt accurately capture data and show how machines are running, including tonnes per hour, total tonnage, reasons for downtime, empty run times, and more. In turn, this level of detail about throughput gives quarry operators the ability to monitor and improve the crushing and screening process. Better analysis allows more proactive decision-making when it comes to plant performance. This includes the ability to look deeper into any bottlenecks and the ability track every product. By measuring weight, downtime and performance of multiple belts automatically, quarry operators can decide on the optimal mode mix when planning production to meet sales forecasts.
Load out
Delivering the right product to the right customer at the right time is a critical component of any operation. In a quarry operation that has embraced Industry 4.0 principles, accurate loader scales seamlessly exchange data with load-out management applications. This optimizes the load-out process and helps ensure each truck is loaded safely and quickly, and to the optimal capacity. These connected scales also generate billable information and generate tickets straight from the loader scale. By exchanging information freely, these solutions can feed data into load-out management tools that provide real-time customer job lists. Load accuracy and better analysis capabilities help with machine utilization and customer satisfaction.
Inventory
Using conventional methods to conduct a ground survey of an active pit or quarry can be time-consuming, as well as potentially dangerous. Measuring inventory with UAVs (unmanned aerial vehicles) keeps quarry personnel out of danger and helps operators improve data collection accuracy and efficiency. This helps with forecasting and avoids costly write-offs at the end of the year if stockpile estimates are inaccurate.
Transportation and distribution
Data automatically collected about vehicle location, condition and driver behaviour minimizes the need for manual load sheets and reduces driver frustration. Asset and fleet-management tools that exchange data let operators know when and where machines are working compared with targets, so operators can make the right decision at the right time.
Adoption strategies
Although quarry productivity technology is becoming easier to use, operators should never underestimate the importance of selecting the right supplier and choosing a good local partner. Whether the quarry is a major producer with many sites or a single-site operation, having the right partners in place that can troubleshoot problems and have a grasp for the complete aggregate workflow is critical. Other best-practice adoption strategies include:
Keep it simple
To start with, focus on a specific area of the quarry that needs optimization and work outwards from there. For instance, if extraction estimates are always in question, consider a solution such as a haul truck management system. Sophisticated monitors provide in-cab displays and sensor systems that collect production figures and payload data, without the need for manual tally sheets. A next step would be connecting these sensors to the Internet and using a production-management application with cloud reporting tools to highlight material movement issues. From there, reports would show haul truck activity, loading time and waiting time. Better data in one area allows operators to make key adjustments to variables such as cycle time and product ratios, which together have a big impact on meeting plant demands.
Focus on ROI
Similarly, start on the area with the biggest opportunity for return on investment (ROI). For instance, running the pit loading operation at capacity can eliminate the cost of additional machines and trucks to support the excavator. Even small tweaks in the pit loading operation can eliminate load adjustments, the dumping of excess or turn-arounds during haulage, which can save significant money and time. When ROI is high, quarries can make additional investments incrementally, building the technology infrastructure methodically while mitigating risks.
Establish manageable benchmarks
Set benchmarks during the adoption period to monitor progress. When technology used across the quarry is linked, operators have a historical perspective and analysis of data from multiple sources. This insight allows teams to better benchmark operational performance and then compare time periods, operator performance, product inventories and sites to identify cost drivers and opportunities.
Have a long-term plan
While it is important to start small, having a long-term plan will ensure each technology component (ie machine control, scales and load-out applications), as well as the supporting infrastructure, is interoperable. The seamless, universal exchange of data is the foundation that will support the operation’s long-term goals for connectivity and optimized production.
Conclusion
While it may take several years to fully realize the benefits of Industry 4.0, many quarry operators are acting now to improve their operations. The vision for a more connected aggregates production process and real-time data sharing is no doubt driving quarry operators forward. By syncing data captured across the entire aggregates workflow, from pit to processing and then load-out, quarry managers will continue to benefit. Those aggregate operators that apply best practices and next-generation technology today will experience increased visibility across the production site as well as improvements to production efficiency, machine productivity and personal safety.
Note on the author
Sören Schramm, regional product application manager for aggregates at Trimble, leads the Trimble Aggregate Innovation Partner Program. Based in Germany, his 10 years’ experience working with clients in aggregate operations around the world has resulted in the development of a range of industry-led Trimble Loadrite products, including loader, excavator and belt scales. Trimble have also recently released a haul truck monitor for haul fleet productivity reporting. For more information visit: aggregates.trimble.com
- Subscribe to Quarry Management, the monthly journal for the mineral products industry, to read articles before they appear on Agg-Net.com