The Use Of Secondary Sands
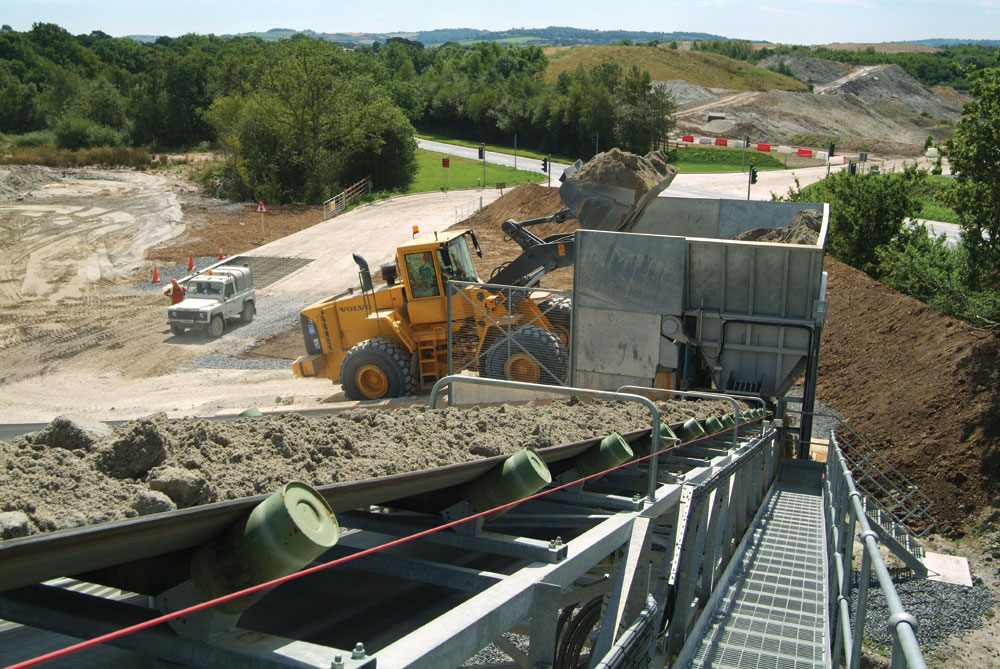
WBB Minerals optimize the utilization of their ball clay resources
By Ray Bovey, engineering manager, WBB Minerals UK
This paper explains how WBB Minerals – part of the S.C.R. – Sibelco NV Group of companies – are optimizing their ball clay operations in South Devon, focusing on a recent investment in plant designed to process secondary sands. The company’s UK clay operations consist of two china clay quarries on the south-western edge of Dartmoor at Lee Moor, near Ivybridge, and two ball clay production units, one in North Devon, near Petrockstow, and the other in South Devon, near Kingsteignton.
The term ‘ball clay’ stems from the way the material was once extracted and handled. Originally, cubes of clay were cut from the ground by hand, but by the time these had been transported to market by horse-drawn cart and sailing vessel, the cubes had become more rounded in shape, hence the term ‘ball clay’. In recent times the term ‘plastic clay’ has also become common.
The Bovey basin deposit in South Devon (figs. 1 & 2) has a surface area of 11km x 5km and boreholes have proven the existence of ball clay to a depth of 300m, although it is thought that the deposit extends much deeper than this, perhaps to over 1,000m. The economically workable sequence, however, is 125m in depth. Figure 3 is a much-simplified diagram but gives an indication of the complexity of the deposit. There are many seams of material which range from sand and lignite with clay contamination to clean clays with very little sand and lignite contamination. Seam thicknesses can range from a few centimetres to several meters.
The seams are individually extracted and classified as either waste, which is tipped, or saleable product, which is stored in ‘bulk’ storage sheds. The clay is won by Volvo 360B backhoe excavators and taken to the tipping area or storage sheds by 25- to 35-tonne articulated dumptrucks (fig. 4). A high-efficiency blending and shredding process produces saleable products (with a lump size of less than 40mm) as well as ‘upgrading’ blends, which are suitable for further refining and processing.
WBB Minerals’ ball clay refining facilities are at their East Golds Works between Kingsteignton and Newton Abbot. As well as dry powders, which are packaged or dispatched in bulk tankers, the plant also produces high-density slurry and noodled clays. Slurries are used in the UK sanitaryware industry, while the noodles are generally exported to similar markets overseas, their lower moisture content reducing transportation costs. Logistics is a very important aspect of the industry, as over 90% of sales are exports, the majority of which pass through the port of Teignmouth.
The main market for Devon ball clay is the ceramics industry, with sanitaryware, in particular, being the most important market.
With the ceramics markets gradually moving from western and central Europe to eastern Europe where labour costs are lower, the ball clay industry has faced a challenge, particularly as transport costs are high compared with the value of the clay. However, high quality in terms of consistency and performance has been the key to the industry’s success. The Bovey basin deposit contains clays which perform well in terms of the demands of the ceramics industry, but what is really significant about the deposit is the unique range of clays available. This allows consistency to be achieved but also means a diverse range of markets can be supplied, including fillers for rubber, fertilizers, ceiling tiles and cosmetics.
This high-quality reputation, which has served the business well, is based on a careful selection process. However, this process means a lot of material that is extracted has to be rejected to tip, which is a major issue as the depth of the deposit means a large area has to be kept open to maximize the resource. This precludes the (rapid) progressive backfilling that is often seen in shallower deposits elsewhere in the world.
Optimization programme
WBB Minerals would like to sell all the material that is extracted, but the reality is very different. In practice, utilization is limited by the day-to-day balance of customer requirements and material availability. Over the years many markets have been developed but, even so, the inherent yield of the deposit before WBB Minerals began their optimization programme was only around 25%, which meant that 75% of the total amount of material extracted went to tip (15% overburden, although this can vary greatly from year to year, and 60% inter-seam waste).
Tipping space is limited and, while future waste material will be accommodated within the quarry voids, the company is working hard to minimize waste and optimize yields through a number of new initiatives.
Until the late 1950s customers of the South Devon ball clay industry purchased specific seams of clay from various producers which they then blended, refined and mixed with other components in their factories. These blend recipes were closely guarded secrets and were considered to be significant assets. However, as WBB’s technical staff travelled around Europe, it became apparent that the ball clay blends were very similar. This knowledge, combined with rationalization of the large number of small producers into one of two large companies, WBB and Imerys (formally ECCI), led to the clay producers supplying ball clay blends. This allowed the producers some measure of flexibility, which in turn helped to improve yields.
By the late 1950s WBB had introduced combined drying and grinding plants to produce a range of products in powder form; classifiers and screens were also introduced to reduce sand residue content. As early as 1960 the company were investigating ways of removing the two main contaminants (sand and lignite). By 1971 WBB had a problem, Sanblend 55 (now Sanmix 55), a shredded clay blend, was selling so well that there were difficulties in meeting demand. Production costs were also high because of the amount of waste that was being produced.
By this time sand residue removal via the drying, grinding and classification route was already established. The major problem to be overcome, therefore, was the removal of lignite. Blunging and screening provided the basis of a solution (fig. 5) but the key to success was the use of chemical deflocculants that allow the slurry density to be kept high, so that when the powder and slip are mixed a manageable moisture content allows a noodle to be formed. There were many problems to overcome, one of the major ones being that the original plan to blend noodles and shred did not work (due to segregation). The plant was modified to include the shredded component within the noodle and in 1975 the world’s first refined ball clay noodle was launched (Sanblend 75). During the 1980s and 90s further refining plants were built, which also removed contaminants from otherwise unsaleable clays, and a range of refined clays are now marketed in powder, noodle and slurry forms.
For many years WBB Minerals had considered the construction of a sand-processing plant to reduce the amount of waste going to tip but the justification had always been marginal. The company’s merger with Sibelco Minerals & Chemicals (SMC) in 2000 made available technical and marketing expertise, and this, together with a successful grant application to the Waste Resources Action Programme (WRAP), made the project possible. The sand plant was commissioned in March 2005 and will eventually process 100,000 tonnes of waste sand annually.
Around 28,000 tonnes of lignite are extracted each year as inter-seam waste, but the main lignite seams are still in the ground (3 million tonnes to current quarry floor level) and will eventually have to be removed to continue to access the clays. Over the years many initiatives have looked at commercial uses for large volumes of lignite. The two main opportunities considered were energy and horticulture. WBB Minerals market a range of sand/soil mixes for root-zone and top-dressing applications and have recently looked at the introduction of lignite into these products. This project is seen as complementary to the company’s existing crushed-lignite product, which is sold in modest volumes to the compost market.
The second potential use for waste lignite, which has been researched in some detail, is as a fuel. In the early days the main barrier to be overcome was a technical one but, with the development of fluidized bed and other combustion and gasification equipment, the main barrier later became a financial one. As the calorific value of lignite is about one-third that of coal, the combustion and environmental systems have to have three times the capacity of an equivalent coal-fuelled system. However, recent energy price increases and potential uses for the ash produced have re-awakened interest in the use of lignite in a combined heat and power (CHP) plant.
The final element in WBB Minerals’ current strategy for optimizing their ball clay operation is to revisit the refining plants. As sales of refined clays have grown, pressure on the production units has increased and the need for high throughput has meant that a limit on the contamination level allowable in the feedstock has been introduced. A refurbishment programme is being investigated that will permit material containing higher amounts of grit and lignite to be processed.
When completed, the measures described above should reduce the amount of inter-seam waste going to tip from 60% to 32% of the total dig. In tonnage terms, some 270,000 tonnes per annum of material is currently being recovered that would otherwise have to be tipped, and the target during the next five years is to increase this to 440,000 tonnes per annum.
The sand plant project
In 2002 WBB Minerals applied to WRAP for a grant to construct a plant to process the sand being extracted as a by-product of their ball clay operations in South Devon. The company had estimated that more than 100,000 tonnes of sand would be extracted each year for at least the next 15 years, meaning that 750,000m3 of tipping space would be required. Research and development and marketing activity had uncovered a demand for the sand in the construction and sports and leisure markets.
During 2003 a mobile trial plant was used to help specify the equipment required to process the sands and to provide samples for customer trials. The WRAP grant and WBB Minerals’ internal project approvals were agreed in July 2004 and plant procurement and construction at the Preston Manor works, near Kingsteignton, got under way. Production began in March 2005.
There are three main elements to the plant: a primary process, a secondary process and a settlement/wash water pond. The primary and secondary plants are positioned at opposite ends of this pond because no single location was large enough for the raw feed and finished sand stockpiles plus the process plant. Nevertheless, this arrangement has a number of advantages: the primary plant and feed stockpiles are near the main source of sands; the secondary plant is near the dispatch weighbridge; and the sand/slurry pipeline linking the two plants eliminates the need for an ‘attrition’ processing stage.
The raw sand feedstock (fig. 6) is classified as ‘dark’ or ‘light’ and can contain up to 20% clay. ‘Dark’ sands are used in WBB Minerals’ range of sand/soil mixes, while the ‘light’ sands are used for bunker sand and in concrete products. The raw sand can come from any one of four quarries but generally around 50% comes from Denistone Quarry, which is adjacent to the primary plant.
The primary plant is fed via a tipping boot fitted with bars spaced at 100mm to prevent large lumps entering the system (fig. 7). Around 2–6% of the clay is removed at this point, after which a Binder screen with a single 6mm deck removes a further 8% of the clay.
The –6mm material passing through the screen is pumped via a 500m pipeline to the secondary plant. Had space been available to locate the primary and secondary plants adjacent to one another, attrition cells would have been needed at this point in the process to achieve further breakdown of the clay. However, the pump and pipeline achieve a similar result.
At the secondary plant (fig. 8) a twin-deck Binder screen is used to create two coarse sands: –6mm +2mm off the top (2mm) deck; and –2mm +1.2mm of the bottom (1.2mm) deck. The clay contents of the coarse sands are 0.2% for the –6mm +2mm material and 0.06% for the –2mm +1.2mm fraction. Material passing through the 1.2mm screen is pumped to one of two cyclone towers (fig. 9); the silt content at this point is 0.26%.
The cyclones cut at 50 microns and remove a further 6 tonnes/h of clay and slimes from the feedstock. The effluent is discharged into one end of the settlement pond, while clean wash water is drawn from the opposite end of the pond in a ‘closed-loop’ arrangement.
In the plant’s first year of operation 60,000 tonnes of feedstock was processed against a target of 40,000 tonnes agreed with WRAP. Some 2% of the washed product is –2mm +1.2mm sand, 8% is –6mm +2mm sand, 15% is –1.2mm ‘dark’ sand and 75% is –1.2mm ‘light’ sand.
Sand from the new plant is supplied into traditional construction markets as well as for use in WBB Minerals’ range of sustainable sand/soil products, marketed under the ‘Eco’ label, whereby soil and peat are replaced with compost and lignite. ‘Eco Zone’ and ‘Eco Topdressing’ are used in the construction of golf greens, bowling greens and football pitches.
This article is based on a paper presented by Ray Bovey at the Institute of Quarrying’s annual conference symposium in October 2006.