KVM Selected At Mountsorrel
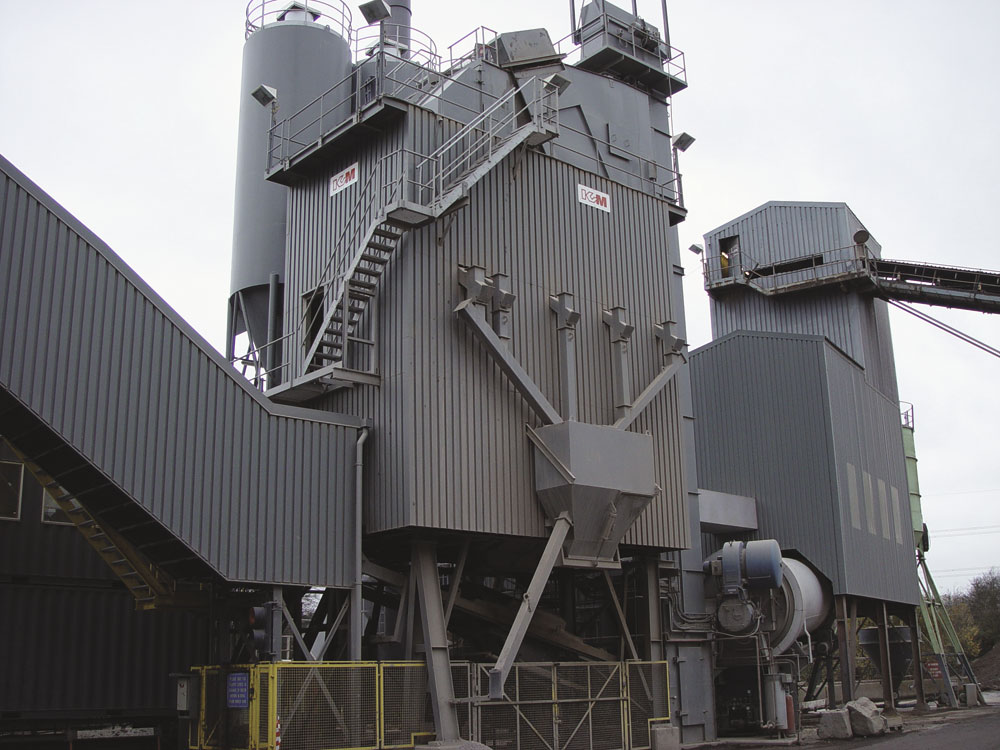
New asphalt plant redresses the balance at Lafarge Aggregates’ flagship Midlands quarry
Last year Lafarge Aggregates made a significant adjustment to the balance of coated stone production at their flagship Mountsorrel granite quarry in Leicestershire by replacing a 60 tonnes/h Quadrare batch-heater plant with a new 210 tonnes/h Freja 3500/250 asphalt plant from Danish manufacturers KVM International A/S. The change was made to meet today’s growing demand for high-specification thin wearing courses, a task that the batch-heater unit and the quarry’s other existing coating plant — a Standard Havens drum-mix unit — were struggling to fulfil.
Before selecting a supplier Lafarge set up a project team to identify and define the required plant specifications. The team soon highlighted a number of time constraints and space limitations that meant the new plant would have to be constructed to very tight tolerances and within a restricted time frame. Foremost among these considerations was the need to have the plant fully up and running in time to meet last year’s surfacing requirements on the M6 Toll. This was compounded by a 21m height restriction and the need to ‘integrate’ the plant with the existing cold-feed system, an overhead RAP conveyor to the Standard Havens plant, the original bunded bitumen storage area, and a new hot-storage/load-out facility.
Ultimately, KVM’s ability to overcome most of these constraints, combined with their reputation for producing coating plants that offer ease of maintenance, low energy consumption and flexibility in production, weighed heavily in the decision to award the bulk of the contract to the Danish manufacturer, as did Lafarge’s long-standing relationship with Stratford upon Avon-based Pedershaab Ltd, the sole agents for KVM in the UK and Ireland.
PLANT SPECIFICATIONS
Taking lead responsibility for installation of the new plant, KVM’s role involved the supply of the dryer, dust-collection system, mixing tower, filler storage and plant control equipment. However, in addition to this, four new bitumen storage tanks were supplied by Cormac Ltd and a new hot-storage/load-out facility was supplied by FMA Ullrich of Germany.
Work on the changeover commenced at the end of 2002 with the removal of the Quadrare batch-heater plant taking place from late December to early January 2003. This was followed by the laying of the concrete foundations for the new plant; a challenging task that was carried out with pinpoint accuracy by Newline Civil Engineering. Installation of the new plant took place in late January and February, wiring was completed in March and full commissioning took place on schedule in April.
Cold-feed system
The quarry’s existing feed system to the now defunct batch-heater plant was retained for use as the cold feed to the new KVM plant. In addition, the batch-heater building was stripped of plant items in order to accommodate a four-compartment feed hopper to provide up to 100 tonnes of surge capacity for the new plant. Aggregate is delivered into this vessel by means of a rotary chute arrangement, while discharge is via four individual discharge gates. Control of the feed into the hopper is effected by Lafarge’s existing cold-feed control system, but discharge is regulated by the new KVM control system. A variable-speed collecting conveyor equipped with a belt weigher delivers the aggregate from the hopper on to the dryer slinger conveyor.
Drying plant
The drying plant comprises a 9.3m long by 2.5m diameter KVM 250F contraflow dryer drum which runs on individually driven polyurethane rollers and features an 18.6MW dual-fuel burner suitable for use with gas-oil or heated reclaimed fuel oil. Drive is transmitted to the drum through KVM’s ‘floating’ rolling ring system, which minimizes the structural stresses caused by expansion and contraction of the drum. For ease of maintenance, the dryer drum can be accessed from both ends and the discharge chute is fitted with replaceable wear plates.
Dust-collection system
The plant is equipped with an 80,000m3 capacity, low-energy consumption S16-40M bag-filter system with an adjustable pre-skimmer. Coarse particles captured by the pre-skimmer are returned to production via the plant’s hot-stone elevator, while fine dust can be fed to an existing waste silo and pugmill system for dumping or to one of three new filler/fibre storage silos.
Delivery of the fine filler dust to storage is by means of dust-proof screw conveyors and a high-temperature rubber belt and bucket elevator, allowing Lafarge to benefit from considerably reduced power consumption and lower noise emissions compared to pneumatic conveyance systems. Furthermore, this method of filler transportation eliminates the risk of dust pollution from blow-outs.
Cleaning of the bag-filter system is achieved by a high-efficiency jet pulse which gives a very low pressure drop over the bags even during high dust loadings. As a result, the power requirement of the inverter-driven exhaust fan is said to be around half that of competitive dust-collection systems of similar capacity. Moreover, the temperature drop across the bag house is also very low, resulting in a relatively low (less than 120°C) dryer exhaust gas temperature without risk of condensation, thereby reducing fuel consumption.
Mixing tower
Heated aggregate discharged from the dryer drum is delivered to the top of the 21m high mixing tower by a bucket elevator equipped with a long-life, single-strand REX-type chain. For ease of maintenance, the base of the elevator housing features a large, hinged door for walk-in access, while at the top of the structure the discharge chute is insulated against noise and has anti-wear strips and replaceable wear plates.
The elevator discharges the hot stone into a totally enclosed 2.0m x 5.5m six-deck screen which provides a generous 53.4m2 of mesh surface for maximum screening efficiency. The drive mechanism is external to the screen housing with transmission via two independently driven shafts featuring oil-lubricated bearings. Screen amplitude can be adjusted by varying external swing elements. For maintenance purposes the noise-insulated screen cover features a walk-in access door as well as a roll-back section.
Screened aggregates are discharged into a 60-tonne capacity, heat-insulated hot-bin section comprising six single-size bins and a by-pass bin, all fitted with two-speed discharge doors. For simplicity, each discharge door is operated by a single air cylinder with two position settings (coarse and fine). This allows accurate adjustment of the fine feed position and thus a very low inflight for precise control of material flow to the aggregate weigh scale.
The mixing tower is equipped with four load-cell-mounted weigh scales for aggregate, bitumen, filler or colour pigments, and fibre pellets. Each vessel is equipped with a system for automatically checking scale accuracy via the control system without the need for manual positioning of test weights on the scales. In addition, the bitumen and aggregate scales are positioned within a separate enclosure to ensure that weighing accuracy is not affected by changes in exhaust pressure.
Fibre and filler storage is catered for by three 55-tonne silos mounted at high level adjacent to the mixing tower with horizontal screw conveyors feeding the respective weigh scales. Each silo is fitted with an ‘air canon’ aeration system to assist with material movement.
Bitumen storage comprises four new 80-tonne capacity insulated tanks positioned in two banks of two, each with its own pump system for blending. To save power, each inverter-driven bitumen pump features a ring main which allows heated bitumen to be recirculated locally at 10% of normal speed.
Weighed ingredients are dispensed from the various weigh scales into the plant’s 3,500kg capacity twin-shaft paddle mixer, which has the ability to produce batches ranging from 3.5 tonnes down to 700kg. Once mixed, the material is discharged into a travelling skip for delivery to the new 200-tonne capacity hot-storage/load-out section. This comprises a cluster of four load-cell-mounted bins and one foul-batch outlet mounted above a traffic light-controlled lorry-loading bay.
In addition to its primary function of larger-volume, high-specification thin wearing course production, the new plant’s ability to produce smaller batches and the availability of the hot-storage facility has provided Lafarge with the additional flexibility needed to cope with expansion of the collect trade — an area of the business that had previously been limited by the batch-heater plant’s lack of hot storage.
Control system
Designed for one-man operation, the plant is controlled and monitored from a cabin situated above a transportable electrical sub-station. Full plant control is achieved using standard off-the-shelf PC and PLC hardware (Compaq & Allan-Bradley respectively), with the operator interface comprising a full-colour flat-screen monitor, mouse and keyboard.
The plant’s WIN ACS control system is the latest generation of KVM’s WIN-3000 control concept, a Windows-based system which provides a user-friendly graphic display of the plant layout and production process status on screen and allows the printing of production reports when required. All production parameters are continuously monitored and stored in a database for maximum traceability, and modem link to KVM is available should service assistance be required.
ACKNOWLEDGEMENT
The editor wishes to thank Lafarge Aggregates for permission to visit Mountsorrel Quarry and, in particular, Trevor Warren, operations manager, Preben Sørensen, sales manager with KVM International A/S, and Preben Nielsen, general manager asphalt with Pedershaab Ltd, for their help in preparing this article.