KVM Asphalt Plant Installation in Greenland
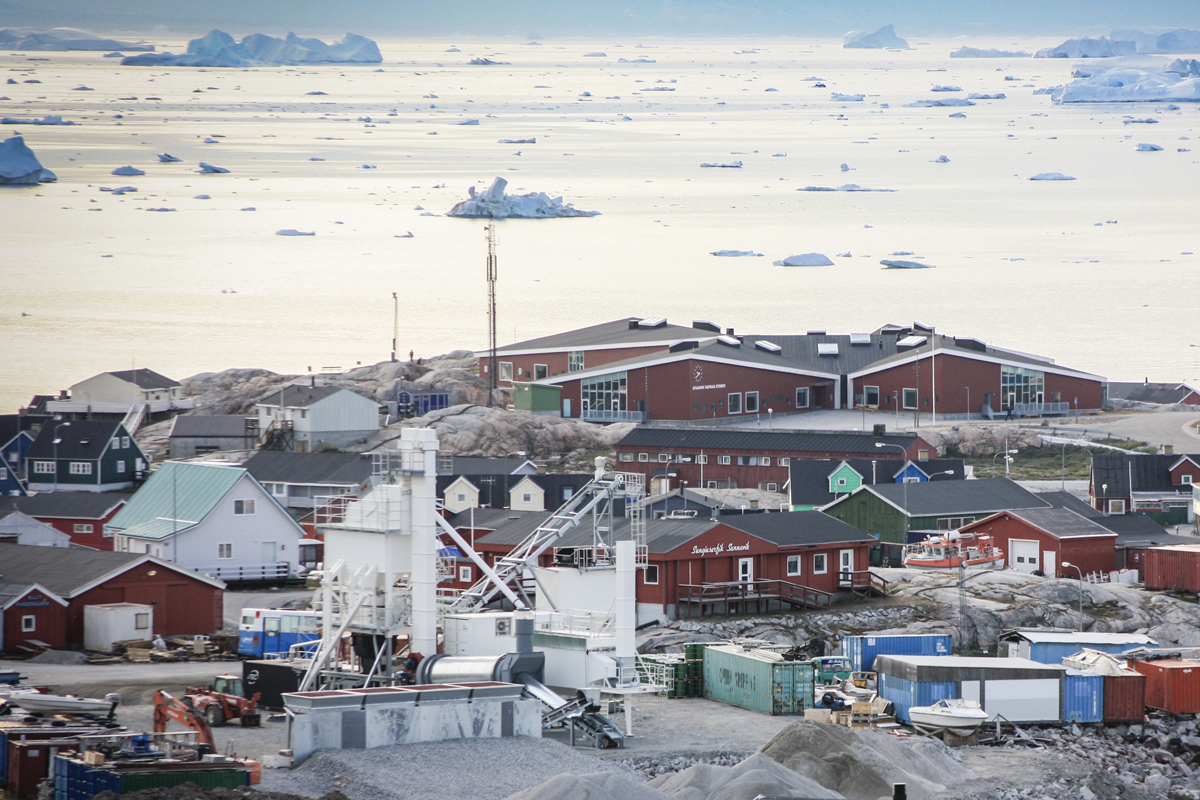
First published in the January 2020 issue of Quarry Management as Arctic Asphalt
KVM install a new Viking 2000 semi-mobile asphalt plant in the Avannaata Municipality of Greenland – where nature sets the agenda
Greenland is one of the most beautiful islands in the world and attracts many visitors with its nature, seals, whales, polar bears and the birth of icebergs in Disko Bay. Tourism and interest in Greenland has increased significantly in recent years, which is why its infrastructure is being improved. Development projects currently taking place include, among others: improvements to harbours, airports, hotels, the Isfjord Centre, and the Northern Light Centre, as well as the infrastructure in general to cope with the increased influx of visitors. To improve access to the municipal centre of Ilulissat, located in the new Avannaata Municipality region, the municipality is embarking on major projects to improve the roads and infrastructure in the area.
To this end, Avannaata Municipality was looking for a partner capable of manufacturing an asphalt plant that would be able to withstand the harsh arctic climatic conditions and aggressive environment that Greenland experiences. Of equal importance was the need for a robust, modular plant design that would allow for quick build/setup, due to the short building season, and be able meet the logistics and transport challenges, both by sea and during haulage over Greenland’s unyielding terrain. Transport from town to town in Greenland is typically by ship or boat, and then by truck from port to installation location.
Additionally, Avannaata Municipality required an asphalt plant with optional ‘limited production’ capacity capabilities, as roads in Greenland are relatively short. A further design consideration was the need for mobility, to allow the plant to be relocated to alternative production sites, to satisfy future development work. Finally, the municipality was looking for a manufacturing partner with high levels of service, including online service support 24h a day, seven days a week, as well as customized solutions and a partnership based on a long-term relationship.
With a preference for a single supplier to manage the entire project from start to finish, and in order to secure a simple-to-install, high-end plant with a top-quality asphalt mixer and user-friendly control system, KVM were contacted. After several proposed layouts and discussion sessions, the final plant design was agreed and a contract between Avannaata Municipality and KVM was signed.
KVM Viking 2000 semi-mobile batch plant
The optimum solution was the KVM Viking 2000 semi-mobile asphalt plant, which is designed and built to perform in harsh weather and environmental conditions, and can be mounted on a steel foundation to facilitate future relocation. Moreover, the plant is built in container-sized modules to allow easy transportation by ship and truck, whilst the cable and control cabinets are installed within a container to provide additional protection and to facilitate easy plug-and-play power connection, especially where the power is delivered by diesel generators. According to KVM, the Viking plant has everything needed to fulfil the demand for simple setup and optimized production capacity.
Four hot-galvanized cold-feed units feed four types of aggregate. Each unit has a rubber dosing belt that feeds on to a collecting conveyor which transports the aggregates into the 120 tonnes/h capacity dryer drum. The drum itself is fitted with replaceable bolted lifters and the shell is made of heavy steel plate to ensure long life. Dust passes through a bag-house filter, rated at 45,000 Nm3/h, with compressed-air filter bags cleaning from where the separated filtered dust follows the dried aggregate up into the asphalt mixing tower, transported by a KVM REX 450 hot elevator. The KVM Viking 2000 has a three-and-a-half-deck sorting screen, which splits the dried aggregates into three fractions and distributes them to storage in three separate compartments within the tower, giving a total hot aggregate storage capacity of 30 tonnes.
At the heart of the asphalt plant is the mixer; the KVM Viking 2000 features a 2,000kg batch mixer with a toothed belt synchronized and driven mixing process with a cycle time of 1min, giving an asphalt production capability of 120 tonnes/h. The mixed asphalt is stored in a square, 30-tonne capacity silo complete with discharge chute that allows the material to be dispensed into waiting trucks positioned below. The mixer box includes two ™ large access doors to allow easy inspection and maintenance.
In Greenland, bitumen is supplied to the plant in 200-litre drums, which are heated and emptied into a KVM Bitumen Melting Unit which has the capacity to handle
33,000 litres/day. From here, the heated bitumen is pumped to a 30m3 insulated storage tank ready for dosing to the mixer via a pump and bitumen kettle arrangement.
KVM Asphalt Manufacturing Control system
The asphalt plant was delivered with a KVM Asphalt Manufacturing Control (AMC) system that allows the entire plant to be controlled from a centrally located operator control station. According to KVM, the AMC system sets new standards for user-connectivity, efficiency and responsiveness.
Whether creating or handling recipes, or managing daily production, the operator has quick, easy and flexible access to system controls and production data. Production-specific controls are available to facilitate production parameter diagnosis and recipe verification, allowing the operator to initiate, in real time, amendments or production corrections. Post-production data and reports are generated following each production run, providing auditable accountability, critical KPI data, and the opportunity for root-cause analysis.
For the Greenland project, KVM supplied a customized container for the plant’s control room, positioned to provide the operator a full view of the entire plant and supplied complete with an operator’s workstation, windows, doors, and a heating system, to provide the best working environment and welfare facilities for the operator.
The Motor Control Centres (MCCs) containing all the electrical equipment were designed and built by KVM and are configured for 24h operation. The MCC cabinets, manufactured from stainless steel, are weather resistant and were positioned within containerized cabins to provide additional protection from the elements and to facilitate easy inspection and maintenance.
Thanks to the installation of the KVM AMC control system, KVM can provide remote online support for their customer’s entire system, via their online support service, 24h a day, seven days a week, 365 days a year.
Commenting on the new asphalt plant, the Mayor of Ilulissat, Palle Jerimiassen, said: ‘I was very satisfied with the service we received during the project discussions, installation and commissioning of the plant. KVM’s customized solution satisfied all our concerns about our location, the environment, build quality, and production requirements. Now, whenever we have a question, we simply contact them and they help or advise us on how to proceed, which is a great benefit for us and is why we were right to choose KVM.’
For more information, visit: www.kvm.com
- Subscribe to Quarry Management, the monthly journal for the mineral products industry, to read articles before they appear on Agg-Net.com