Day Tripper
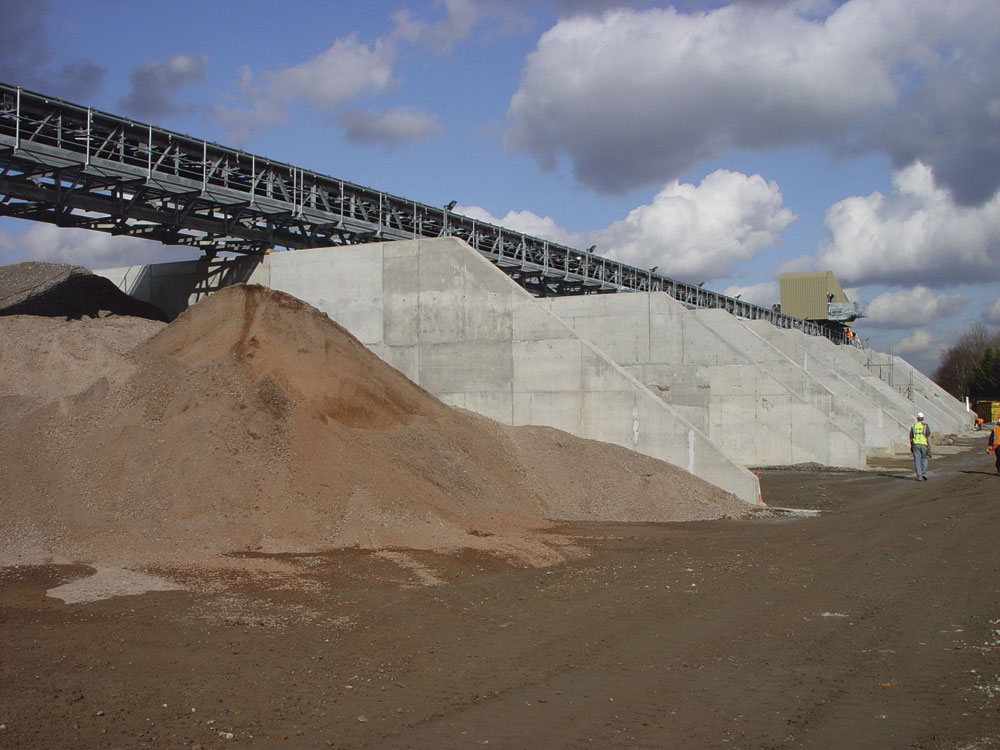
Day Aggregates invest £3.6 million in new unloading and storage system at key south London rail depot
Day Aggregates, a division of Day Group Ltd, handle nearly 3 million tonnes of construction materials each year. The original company was established by the late John Day, who made his name delivering coal to London’s power stations during the second world war. By 1955 the company had outgrown their original site in Hanworth and moved to a British Rail goods yard at Brentford where Day Group’s headquarters are still based today.
In 1971 the Brentford railhead allowed limestone aggregates to be railed into London, for the first time on a regular basis, directly from Foster Yeoman’s Torr Works quarry in Somerset. This, together with the demise of London’s coal-burning power stations, shaped the future of Day Aggregates, and during subsequent years further railheads and wharfs were acquired by the company throughout south London, Surrey, Sussex and Kent.
One of these railheads, located next to Purley railway station on the busy London to Brighton commuter line, represents one of only two strategic rail-fed aggregate depots in Surrey. First established as a rail yard in the late 1800s, in more recent times the Purley site had been operated by Charringtons as a coal distribution yard, and as such was equipped with rudimentary rail unloading facilities.
Since its acquisition by Day Aggregates in the early 1990s, the Purley depot has undergone a series of staged developments, including the installation of a modern, fully enclosed, static construction and demolition waste recycling facility in 2002. The latest phase of development has seen the replacement of the existing rail unloading facilities with a completely new bottom discharge wagon unloading system and associated tripper conveyor together with aggregate toast-rack storage facilities in a move to improve both operational and environmental efficiencies at the site.
Old system
Purley depot receives the vast majority of its aggregates by rail, with some 200,000 tonnes of limestone arriving each year from Foster Yeoman’s Mendip operations, and a further 130–140,000 tonnes per annum of marine-dredged sand and gravel being delivered from Brett Aggregates in Kent.
Under the old system, the limestone materials were unloaded from box wagons by grab bucket, while the sand and gravel was unloaded via a primitive bottom discharge system. With up to two train deliveries per day, these unloading methods were considered to be unsustainable in the long term – the equipment itself being over 30 years old, often unreliable and generally unfit for purpose. Moreover, unloading operations involved considerable double-handling of materials which, together with the regular translocation of stockpiles, made it difficult to achieve effective dust suppression at the site.
Situated in close proximity to several large suburban residential properties, the site is not surprisingly very environmentally sensitive, with the potential for dust emissions and the noise arising from shunting and grab unloading operations being of particular concern to near neighbours. The attenuation or elimination of such impacts on the local neighbourhood was a key factor in the consideration of the re-development of the unloading facilities in order to ensure continuity of business into the future.
New system
Planning permission for the new bottom discharge unit and storage facilities was granted in early 2003 and construction began in June 2005. The main mechanical and electrical engineering contract was awarded to DUO Manufacturing (LJH), with Martin O’Brien and Associates acting as consulting engineers. DUO Manufacturing subcontracted the electrical design and installation work to Bridges Electrical. The civils contract was awarded to Bankside Construction.
Representing an investment of £3.6 million, with modest financial assistance in the form of a small grant from the Aggregates Levy Sustainability Fund, the development formed the large part of an overall £4 million scheme at Purley which included the provision of new offices, mess facilities, underground fuel storage, lorry washing and car parking facilities. Particular care and attention was paid to the visual impact of the site, with some £75,000 spent on landscaping work alone.
In a testament to the organizational skills of local site manager Tim James, day-to-day operations at Purley were maintained at full capacity throughout the entire nine-month build period, with only four scheduled train deliveries having to be called off during this time.
The new bottom discharge unit is housed within a secure, purpose-built building which is fully sheeted with composite cladding and equipped with motorized roller shutter doors. A specially constructed bridge structure allows the inspection of 102-tonne gross weight wagons as the 129-tonne Class 60 locomotives to pass over two underground receiving hoppers which provide a combined capacity in excess of the 76-tonne payload capacity of each rail wagon. Two electrically operated, rail-mounted, wagon door opening trolleys are provided along the discharge section, together with an air-compressor unit for occasional air-operated wagons.
The discharge openings into the stainless steel-lined receiving hoppers are covered by protective grids with steel bars spaced at 150mm x 150mm. In common with all feed boots and discharge chutes around the plant, the receiving hoppers have been designed to minimize spillage and have a minimum slope angle of 65º to aid material flow. The two hoppers feed directly on to a pair of parallel 2m wide x 21m long variable-speed discharge conveyors inclined at 18º, each rated at 800 tonnes/h and fitted with a single-idler Siemens belt weigher. Designed to feed –100mm aggregates on to the plant’s main tripper conveyor, both belts are powered by 37kW shaft-mounted Flender geared motors and equipped with heavy-duty impact bars at their feed points. The tail ends of both belts are suspended from overhead structural work to minimize the need for support plinths, struts etc. This, together with hinged guarding, aids the clean-up of any spillages beneath the belts. Sufficient access has also been provided to allow a Bobcat skid-steer to carry out clean-up work around the tail ends of both conveyors.
Adjacent to the two main primary aggregate discharge conveyors is a wheel loader-fed reclaim/blending system, rated at 960 tonnes/h and comprising a 4m2 hopper lined with Hardox 400 panels, a 1.2m wide x 5.35m long variable-speed belt feeder, and a 1.2m wide x 12.4m long inclined discharge conveyor, which also feeds on to the tripper conveyor. The Siemens single-idler belt weigher fitted to this system is designed to ‘communicate’ with the belt weighers on the other discharge belts to permit the addition of up to 60% recycled material for the production of primary/ recycled blends. An electrically powered variable-opening feed gate on the feed hopper ensures accurate trimming of the recycled materials to produce precisely blended products, such as Day Aggregates’ increasingly popular Ecoblend range.
Powered by a 132kW Flender drive system and rated at 1,600 tonnes/h, the 1.2m wide tripper conveyor extends 166.5m in length and provides 110m of actual discharge capacity. Apart from its initial 18º inclined section from the rail discharge building, the tripper structure is supported on top of the new concrete stocking bay walls at a height of 6m. The tripper carriage, which is fully clad to match the rail discharge building, is mounted on four 600mm diameter flanged wheels that run on 40ft lengths of flat-bottomed steel rail bolted to the conveyor support structure. Inverter drives on both axles permit constant speed control over the acceleration, running and deceleration of the tripper carriage, thereby helping to prevent over-speeding due to the forces imparted by the loaded belt and also providing the ability to ‘inch’ the tripper either side of a normal fixed point over each bay for highly accurate stockpile control. Ultrasonic level probes are mounted on the tripper carriage to prevent overfilling and damage to the tripper.
The tripper carriage itself houses a 5.8m long x 1.2m wide reversible transverse conveyor which discharges products into the appropriate stock bays either side of the centre line from a nominal discharge height of 8m. Some 2,000m3 of ready-mixed concrete were used at Purley to construct 15 toastrack-style storage bays offering a total storage capacity of around 22,000 tonnes.
The tripper conveyor, in common with all other conveyors at the plant, is fitted with Horizon primary and return plough scrapers and Hosch secondary scrapers. Likewise, Cooper split bearings and Interroll idlers and return rollers have also been used throughout, and where appropriate the bearings have been fitted with remote greasers so that guarding does not have to be opened for greasing.
The entire discharge and stocking system is controlled by an Allen-Bradley PLC system via a touch-screen HMI (human-machine interface), which is mounted alongside CCTV monitors in a small GRP control room situated adjacent to the rail discharge section. Plant control is by automatic sequence start-up together with timed reverse-sequence shutdown to allow the conveyors to be emptied of materials. All conveyor drives above 22kW incorporate star delta or soft starts to minimize electrical consumption and reduce shock loads during the start-up process. In addition, Rotech rotational speed control units are fitted to all conveyors to maintain sequence running and to stop the entire plant in the event of individual belt failure.
The PLC also controls the newly installed dust-suppression and water-addition systems, which utilize recycled process water with top up from a new 63mm mains supply. In common with the electrical cabling, the ‘moving’ water supply to the tripper carriage is achieved via a novel track system with ‘tangle-free’ roller suspension hangers.
Commenting on the newly completed installation, Day Aggregates’ operations director, Nick Sadler, singled out DUO Manufacturing (LJH) for particular praise, describing their contribution to the project as exceptional. ‘They knew we were nervous about the project to begin with, but their overall performance, flexibility, ability to meet deadlines and attention to detail was outstanding and very reassuring,’ he said. ‘We spent a lot of time drawing up detailed plant specifications for Purley with the help of specialist quarry plant consultants, but DUO had no problem meeting these specs and in places improved on the designs using their experience, common sense and logic. The project was seamless from start to finish.’
Benefits
The new facilities at Purley offer considerable functional and environmental benefits not only for the company, but also their nearest neighbours. The entire unloading process is now a one-man operation with materials automatically dispatched directly to designated storage bays via the tripper conveyor. Rail wagons are now ‘pulled’ through the new bottom discharge unit rather than the former method where they were ‘pushed’. This has the effect of increasing the distance between the locomotive and the nearest residential properties and thereby helps to mitigate the effects of noise pollution. In addition, the total elimination of grab unloading operations at the site has eradicated this particular source of nuisance noise. Moreover, the new BDU, tripper conveyor and toastrack storage facilities have facilitated the installation of permanent and effective and dust-suppression and control measures at the site.
By incorporating a new ‘run around’ track within the depot itself, as well as utilizing an existing section of track for stabling purposes, the Purley depot can now accommodate trains comprising up to 18 wagons instead of the previous 12. This 50% increase in capacity allows existing volumes to be maintained with fewer deliveries, while the new bottom discharge unit achieves quicker and more efficient discharge. With unloading now taking approximately 3min per wagon, 18 wagons can be fully unloaded in approximately 1.5–2h (including shunting), whereas unloading of the former 12-wagon trains was a 3h operation.
In addition, with the blending of primary and recycled aggregates becoming increasingly common, the new facility offers Day Aggregates a major commercial advantage by providing the company with the ability to create blends containing up to 60% recycled material from their on-site construction and demolition waste recycling facility.
Conclusion
The successful installation of the new BDU and associated facilities at Purley has fully achieved Day Aggregates’ key aim to maintain a significant presence in this part of south London and to ensure the continuity of their rail-fed business. Moreover, although primarily designed to deliver improved environmental and operational efficiencies at existing levels of demand, like most major investments of this kind the new facility provides capacity for future growth and development should new commercial opportunities arise.
Acknowledgement
The editor wishes to thank Day Aggregates for permission to visit the site and, in particular, Nick Sadler, operations director, Michael Woodward, project manager, and Steve Fry of DUO Manufacturing for their help in preparing this article.