Choosing the Correct Demolition Attachment to Boost Productivity
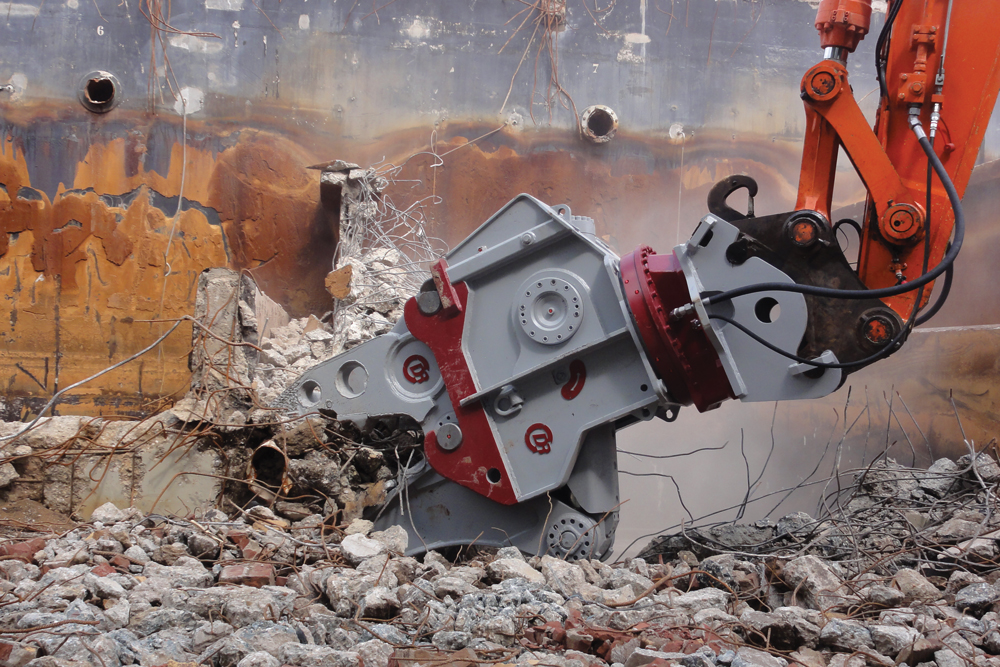
First published in the October 2018 issue of Quarry Management as Perfect Pairing
Francois Martin, North America general manager of Kinshofer, offers some tips on choosing an excavator demolition attachment to help boost productivity
With hundreds of different sizes and styles of demolition attachments available on the market — from small grapples to massive pulverizers — it is not as easy as picking one, attaching it to an excavator and expecting top production. There are many factors to consider ranging from the application and carrier type through to the return on investment.
First, consider the type of work the attachment will perform in. From primary to secondary demolition and from rebar-enforced concrete to wood and brick, the application should be the first factor to guide an attachment choice.
When starting to demolish a structure – multi-quick processors, shears, crushers, pulverizers and demolition grapples tend to be the top picks for primary demolition. The choice between them depends on the type of material and how it needs to be broken up.
Crusher and pulverizer attachments, for example, are best at tackling structures made up of mostly concrete. Choose a crusher or ‘cracker’ if the structure is composed of concrete with little or no rebar and if it is necessary to break the concrete into chunks large enough for easy sorting and recycling.
A pulverizer attachment is suited to handling concrete which is heavily reinforced with rebar. Unlike the crusher attachment, the pulverizer will break the concrete into small pieces and cut through the embedded rebar, allowing the concrete to fall to the ground rather than hang on to the rebar. Pulverizers can also break concrete into manageable sizes during secondary demolition.
If a demolition job involves both crushing concrete and cutting steel, contractors should consider combi-crushers that incorporate both cutting edges and teeth. For steel applications, a demolition processor with shear jaws or a mobile shear attachment is recommended as they both have the capability to cut through steel better than a tool meant for multiple types of material.
When working with light materials — such as wood and brick (commonly found in residential demolition jobs) — use a demolition grapple. In addition to breaking materials apart, rotating grapples work well for sorting during secondary demolition, and they help increase versatility and productivity by allowing flexible movement.
For versatility across different demolition jobs, a multi-quick processor often fits best. The attachment’s interchangeable jaws handle numerous materials, thanks to various jaw types including: crushers, pulverizers; a combination of both; and steel-cutting jaws. Some manufacturers offer additional specialty options, such as jaws for cutting through timber in the forestry industry; jaws for cutting steel tanks, pipes and vessels; and highly powerful jaws for heavily reinforced concrete.
While multi-quick processors are more costly than other attachments, for example, as much as 20% more than crushers, they more than make up for that difference in their versatility achievable through the interchangeable jaw sets.
Powered Up
After deciding the best type of attachment for the job, consider the technology powering the tool. Cylinders power demolition attachments, and typically the larger the cylinder, the more powerful the tool. In the past, contractors seeking more demolition power have often bought or hired a larger excavator to handle the larger attachment, but this is no longer the case.
As OEMs incorporate more advance technology into attachments, some are providing up to 25% more power without increasing the cylinder size. To achieve this, manufacturers are building additional chambers into the cylinder to increase the surface area.
Often, this results in an attachment with the same power as a tool two sizes larger. For example, for a crusher it means that a section of concrete that may take a competitive attachment five or six ‘bites’ to break through only takes the tool with enhanced cylinder technology one or two.
Improved technology has given contractors access to higher crushing and cutting forces without the huge expenses of a larger tool as well as a bigger carrier to operate that attachment. Some attachments with innovative cylinder technology reduce carrier fuel consumption by up to 20%, compared with other models.
And in some cases, the efficient design of the attachment allows it to function as normal when the carrier is set in economy mode; achieving the same performance as competitive attachments on an excavator running at full throttle.
The advanced cylinder technology also helps manufacturers to design high-performing attachments. When combined with double-acting speed valves, the advanced attachment designs not only offer improved power and efficiency but also increased productivity.
Together, the enhanced cylinder design and double-acting speed valves are known to deliver faster cycle times — from 3.8s to 5s on bigger tools — and as much as 20 percent more power than conventional cylinders.
Of course, the best demolition attachment in the market still needs a suitable carrier to perform well, so it is essential the attachment matches to the correct machine size and weight. Heavier attachments require larger, heavier carriers, which cost more to operate. Too heavy an attachment can cause excessive wear to the excavator and will affect performance.
In addition, tools that are too heavy for a machine will pose a safety risk for other workers near the carrier, while an attachment that is too small will reduce productivity.
It is important to ensure the carrier has enough hydraulic capacity to feed the attachment. Inadequate flow or hydraulic pressure will slow the attachment’s cycle times, reducing overall productivity. Too little pressure also results in less closing force or torque, depending on the attachment.
Another item to check is the tool’s hydraulic circuit requirements. Is the excavator equipped with enough auxiliary hydraulic circuits for the attachment?
For example, rotation shears and multi-quick processors require two double-acting hydraulic circuits – one for opening/closing the jaw and another for 360° rotation. Attachments that do not rotate, such as static pulverizers or shears, only require one double-acting circuit.
Easy maintenance
When determining the attachment best suited for the application and power rating, search for a product that is durable and easy to service. Some attachments may seem cost-efficient up front, but end up being a nightmare of downtime and repair costs.
One method for choosing a low-maintenance attachment is to find a tool with no or very few protruding parts (eg hydraulic hoses). These can be easily damaged during operation, particularly in harsh demolition environments. Look for attachments with components enclosed within the tool yet are easy to access through service openings.
Also keep in mind wear parts. Shear and crushing attachments with cutting edges and teeth need to be replaced when worn, while exchangeable cutting edges are an industry standard in most countries.
When considering multi-quick processors, pay attention to how quickly jaws can be switched out. Some manufacturers build multi-quick processors with jaws that operators can change within minutes on site, compared to the hours needed to bring many other attachments back to the shop for exchange.
Choosing the most effective pairing of tool and carrier goes beyond application and power. Carefully consider every aspect of the attachment and carrier to form a pair that will boost productivity, ROI and, potentially, open up opportunities to work in new applications. The right choice will mean the perfect match.
- Subscribe to Quarry Management, the monthly journal for the mineral products industry, to read articles before they appear on Agg-Net.com