AR Demolition Dismantle Plant at Moorcroft Quarry
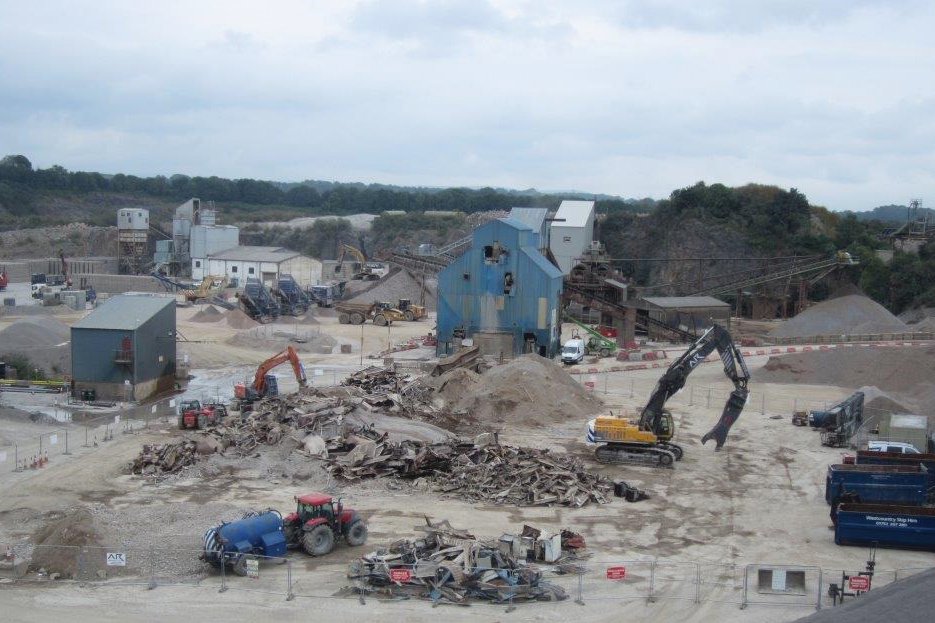
First published in the October 2016 issue of Quarry Management as All in Good Time
AR Demolition successfully complete project to dismantle a fixed crushing and screening plant at Aggregate Industries’ Moorcroft Quarry using suitable high-spec machines and specialist attachments for safe, efficient and high-reach demolition work
The recent upturn in the UK construction industry has seen pressure being put on quarry operators to increase production in a relatively short period of time. While many quarries have been able to step up to the mark and meet demands, there are some facilities which have been struggling to upscale due to older, slower plant.
Since the start of the recession, some forward-thinking quarry operators have realized that a fixed crushing, screening or batching plant cannot offer the production and cost flexibility of a mobile set-up.
One such operator is Aggregate Industries (AI) who have recently employed the services of Leicestershire-based demolition specialists AR Demolition to undertake the removal of a fixed crushing and screening plant at their Moorcroft Quarry, in Plymouth.
Capable of producing 500,000 tonnes of high-quality limestone per year, the AI management team looked into the annual costs of running and maintaining the static plant at the site and, after in-depth consultation with site staff, decided it was more financially beneficial to remove the fixed plant and invest in new mobile crushing and screening equipment.
The removal of the fixed plant also gives access to new reserves, once sterilized due to its location. The high-capacity primary crusher was retained in-situ with the AI team deciding to undertake all secondary crushing and screening operations through a newly purchased Kleemann plant.
The added versatility of the newly acquired plant means that the production equipment can be easily and cost-effectively relocated to another quarry to increase short-term capacity or should the Moorcroft site become unviable in the future.
Careful consideration
The tender process for the contract was extremely protracted taking almost two years. Various factors elongated the decision to undertake the work with the potential cost savings and increased reliability being the primary driving forces behind the company going ahead with the project.
With health and safety playing a very important part in the day to day running of a large-scale quarrying operation, AI were keen to see that AR Demolition were able to meet the stringent requirements of working in a live quarrying environment.
Such are the high standards of health and safety employed by AR Demolition and other members of the National Federation of Demolition Contractors, that AI were more than happy to employ the contractors to undertake the contract.
The health and safety regime at AR Demolition is said to be among the best in the demolition industry – the training undertaken by all AR operatives far exceeds the minimum requirements within the industry.
As members of the National Demolition Training Group of which AR demolition’s managing director, Richard Dolman, has been past chairman, the company regularly undertakes demolition and general site safety training throughout the wider construction industry and for which AR Demolition have recently received awards from both the National Federation of Demolition Contractors (NFDC) and Construction News.
Effective equipment
AR Demolition’s contract at Moorcroft included the removal of 12 material-holding bins, a secondary crushing house, a control room and a variety of conveyors joining the primary/secondary crushers and screening plant. While a typical project for the demolition contractor may involve a total exclusion zone being formed around the area, the quarry itself was to remain in operation whilst all the demolition works were taking place.
‘Maintaining access for the haulage vehicles entering and leaving the site was a major concern for our clients and ourselves,’ said Mr Dolman. ‘The main access to the stockpile yard was underneath a set of conveyors which were due to be removed; to this end we discussed the possibility of removing them at the weekend to no detriment to the production figures of the quarry.’
Moorcroft’s management team was very pleased with the ‘can-do’ attitude of both the AR management team and site-based operatives. ‘We wanted to work alongside the quarry team at all times and have undertaken weekly meetings with the management team to ensure that our operations had no or very little impact on the day-to-day running of the quarry,’ continued Mr. Dolman.
AR Demolition had successfully undertaken work for AI at Croft Quarry, in Leicestershire, and it was the quality of service which put them in good stead to undertake the Moorcroft contract. As one of the UK’s leading demolition contractors, AR operate a modern, high-tech fleet of plant and equipment.
While the quarrying industry relies on just the base machines to undertake extraction work, the demolition sector relies on both the base machine along with a plethora of specialist attachments to successfully undertake its operations. On the Moorcroft project, AR utilized the services of a 25-tonne Hitachi ZX225USLR hydraulic excavator and the biggest machine in their fleet, a 70-tonne Volvo EC700.
While the standard zero-tail-swing Hitachi machine was used to undertake the less demanding part of the demolition operation, along with helping to process the larger materials, the Volvo excavator came equipped with a choice of front-end equipment, including a standard reach boom and dipper along with a 29m high-reach boom combination.
The tallest building to be taken down on the site was the 25m high screening house, which the Volvo unit accomplished with ease. The general perception of demolition; where a building is dropped in a cloud of dust leaving a pile of mangled remains could not be any further from the truth. At Moorcroft Quarry, the safe and systematic demolition of the structures was undertaken with such precision using a shear-equipped, high-reach machine.
Once the cladding had been peeled off and the steel framework exposed, the operator on the Volvo EC700 machine was easily able to work from the top of the building, removing various sections of steel columns and beams. Gradually working forward as the building was reduced in height, the operator methodically reduced the whole structure in a steady operation with the steel frame proving no match for the 3-tonne rotating hydraulic shear.
AR Demolition are one of very few demolition companies in the UK running a full fleet of excavators equipped with the Swedish-made OilQuick hydraulic quick-coupling system. Capable of changing hydraulic attachments in under 30 seconds, the system allows the operator to remain in the cab during changeover and this, according to AR Demolition, has benefitted users with an increase in overall performance and large cost savings on the repair and replacement of damaged hydraulic hoses from the dipper to the attachment.
Less hose damage also means there will be a reduction in lost hydraulic oil. A small substation next to the main screening building remained in use until the end of the demolition phase. To help keep the facility secure and protected from damage, AR created a temporary scaffold structure lined with protective plywood covering.
Along with the two excavators and associated demolition tools, the company also used the services of a tractor and water bowser to undertake dust-suppression duties. Purchased second hand, the bowser was equipped with a remote-controlled monitor allowing the operator to effectively and accurately control any dust emanating from the building during the demolition process.
All material generated from the demolition of the structures was disposed of by AR Demolition with the waste sorted, graded and removed from site for recycling. ‘As with every other project we undertake, we will endeavour to recycle as much material as possible,’ said Mr Dolman. ‘There are very few materials which we cannot effectively recycle these days.’
- Subscribe to Quarry Management, the monthly journal for the mineral products industry, to read articles before they appear on Agg-Net.com