Conexpo-Con/Agg 2020 Review
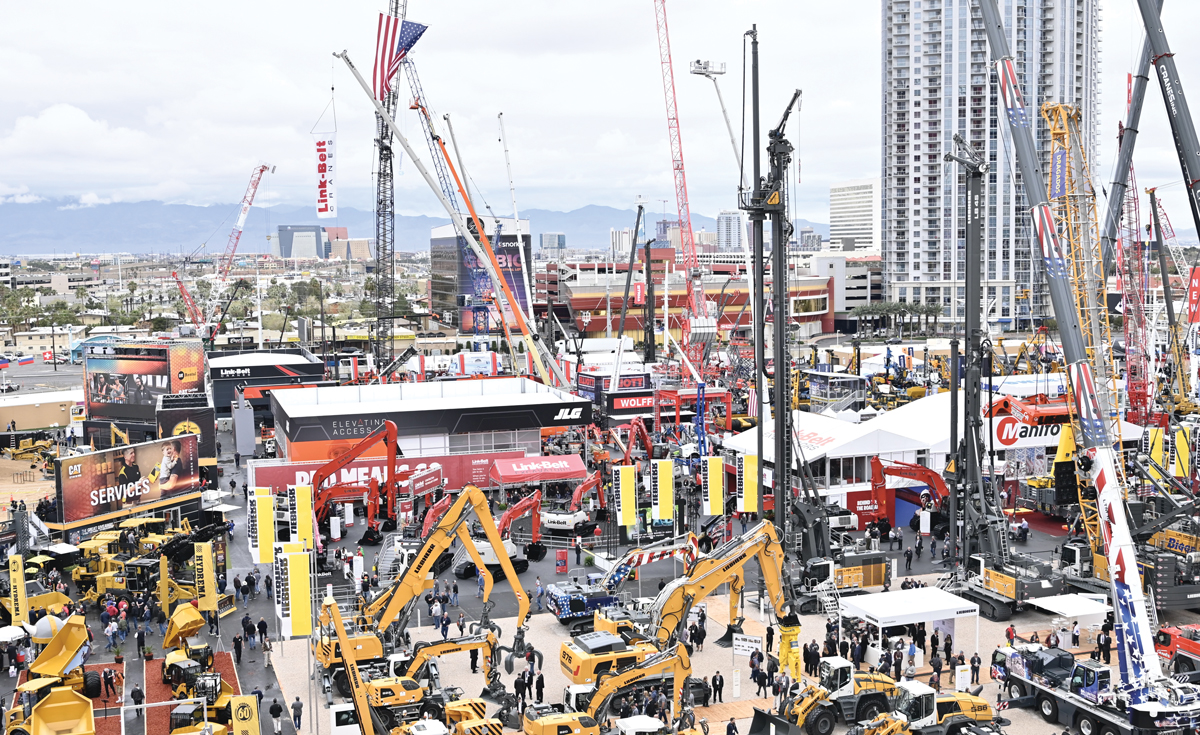
First published in the May 2020 issue of Quarry Management
QM takes a brief look back just some of the new plant, machinery and equipment that was on display at North America’s triennial showcase construction industry event
Members of the international construction and construction materials community, including aggregates and quarrying, converged on the Las Vegas Convention Center and Festival Grounds in March as they came together for Conexpo-Con/Agg 2020, to see all the latest new products and technologies, share knowledge, network with industry peers – and buy equipment.
According to the organizers, visitor registrations for the show totalled more than 130,000, and despite the event taking place just as the coronavirus outbreak was beginning to gain a foothold in some US states, at the conclusion of the show, cancellations from international attendees were said to amount to less than 1%.
‘We refer to Conexpo-Con/Agg as the ‘heavy metal’ show, but it’s more than that; it’s also small equipment, education and technology,’ said Mary Erholtz, vice-president of marketing at Superior Industries and Conexpo-Con/Agg 2020 show chairperson. ‘Giant machines, incredible exhibits, fantastic education and huge expectations – the organizers have a legacy of building and innovating on previous shows, and the 2020 gathering extended that record of success.’
Although the organizers eventually had to make the difficult decision to close the show a day earlier than planned due growing concerns over COVID-19, Ms Erholtz described this year’s slightly truncated event as ‘one of the best editions of Conexpo-Con/Agg – ever.’
Exhibitors across the show, from the Festival Grounds to North Hall to Bronze Lot to South Hall, echoed her sentiments, expressing enthusiasm for the ‘tremendous engagement’ they received from contractors and producers looking to purchase equipment, and saying the crowd was ‘much better than expected’ under the circumstances.
Mike Ballweber, president of Doosan Bobcat, remarked: ‘Tuesday for us was record breaking in terms of leads and attendance at our booth, which is how we measure how successful the show is for us. We had more people to our booth on the first day than all of the 2017 show. This is a one-every-three-years show, and our dealers and customers were really excited to be here.’
With growing concerns about COVID-19, the show organizers worked closely with the Las Vegas Convention and Visitors Authority and the Southern Nevada Health District to make sure exhibitors, vendors and attendees were provided with heightened cleaning services and hand sanitizers to help reduce the spread of germs and allow all show participants to remain safe and healthy while on site.
Notwithstanding the fact that a small number of companies withdrew their presence and/or staff from the event, the show’s record 2.7 million square feet of exhibition space featuring 2,300-plus exhibitors was still packed with plant and equipment from the leading US and global manufacturers, from the multinational giants to small firms with specialized products. On the following pages we present a brief look back at just some of the novelties on display.
CASE Construction Equipment used the show to stage the European launch of their next generation of compact track loaders (CTLs) and skid-steers with the introduction of the B-Series. The five CTL and nine skid-steer models span radial and vertical lift patterns, as well as numerous horsepower and size classes.
‘Through the B-Series, CASE CTLs and skid-steers have been enhanced to deliver a new and intuitive operating experience while also standing up to the rigours of heavy earthmoving and attachment use,’ said Egidio Galano, Europe compact product manager with CASE Construction Equipment Europe. ‘The B-Series retains the frame and styling of previous CASE loaders, but with critical operational systems re-engineered for greater performance. These have been fully integrated with new control and operator interfaces to give contractors a powerful match of productivity, efficiency and convenience.’
New CASE B-Series skid-steer and compact track loaders feature a completely redesigned operator interface combined with simple ignition, push-button start, easy throttle control and intuitive switches for all core machine functions. Operators can also choose between mechanical and electro-hydraulic controls when specifying a machine.
All B-Series models, except the SR160B, feature either a cooled exhaust gas recirculation (CEGR) design with a diesel oxidation catalyst (DOC) that requires no fluids or filter maintenance, or a CEGR design with selective catalytic reduction (SCR) after-treatment (on 90hp/67kW units) that requires no filter maintenance and just filling with diesel exhaust fluid (DEF) as needed. Daily checks on all models are simple, with regular service points and checks easily grouped at the rear of the machine.
Visitors to the Doosan Infracore stand were able to explore new models such as the DA45 articulated dumptruck (ADT), the DL580-5 wheel loader, a prototype hybrid iteration of the Doosan DL200-5 wheel loader, and the DX800LC-7 crawler excavator.
The new DA45 ADT carries a payload of 41 tonnes and is powered by the new Stage V compliant, 13-litre Scania DC13 diesel engine with an output of 368kW (500hp). The machine features a new cab and a semi-levelling front suspension that adjusts itself independently depending on the operating conditions to ensure a comfortable working environment for the operator.
With a bucket capacity of 5.4m3, the top-of-the-range 36-tonne DL580-5 wheel loader has a similar look to the DL550-5 but features robust structural components and an advance double-circuit axle oil-cooler system, making it well suited to applications such as block lifting and other heavier material-handling needs in quarrying, mining and recycling applications. The loader is powered by the Scania DC13 engine, which provides a maximum torque of 1,765Nm at 1,300 rev/min and up to a 10% reduction in fuel consumption.
Simply designated as DL Hybrid, the diesel-electric hybrid iteration of the DL200-5 wheel loader and other hybrid model configurations could be available in North America as early as 2023. Doosan have designed the hybrid iteration with a smaller diesel engine than that used in the standard model today, but with no noticeable difference in the loader’s power output and performance. The smaller diesel engine helps reduce the wheel loader’s fuel consumption and emissions.
Paired with a 6.1m3 bucket at Conexpo, the new Tier 4 compliant DX800LC-7 crawler excavator is the largest Doosan model ever introduced in the US and Canada and is scheduled to be available across North America in late 2020. It is primarily intended to serve customers in mining and quarrying applications who need to remove overburden and load large amounts of material into ADTs or rigid-frame dumptrucks.
Making its debut at Conexpo, the new Dressta TD-16N dozer is said to set a new benchmark with unrivalled visibility encompassing 309o. To test this claim, the LiuGong Dressta team invited a select group of operators to try the machine prior to the show. Irish operator Neil John Mckeown said: ‘It’s like sitting without a cab – you have the visibility right round you.’ His sentiments were echoed by American equipment owner and dealer Rob Winmill, who commented: ‘The visibility is second to none. Floor-to-ceiling glass, no obstructions, you can’t do better than that.’
With an operating weight of 19,090kg and 127kW (170hp) of power, the dozer features a mid-cab design over a mid-mounted automatic, dual path hydrostatic drivetrain. It comes with a standard six-way angle blade and it is compatible with 2D and 3D grade-control systems. The controls are easily accessible, intuitive and easy to use thanks to electro-hydraulic joysticks.
The next-generation dozer is also said to be a game-changer in terms of versatility, thanks to its special undercarriage design which utilizes a single-track gauge for all track shoe widths. This allows the dozer to be reconfigured at any point in its life – from standard to low ground pressure (LGP) undercarriage – by simply changing the track shoes and the blade.
Whilst visibility and performance were high on the design team’s agenda, operator safety was another priority. Non-slip steps complete with safety handrails at the rear of the machine totally negate the need to step on to the tracks, allowing easy access to and from the cab with three points of contact maintained at all times. Also, all access points for daily checks, maintenance and fuelling are accessible from ground level, with no need to stand on the tracks.
Continuing their commitment to providing innovative solutions for conveyor belt splicing, cleaning, tracking and slippage, Flexco showcased a number of products designed to increase efficiency and reduce downtime. For example, the Flexco Wash Box has been specially engineered to deliver superior cleaning efficiency in applications where head-end cleaning is not enough. Mounted on the return side of the belt, hinged doors are available on each side of the unit for simple inspection. Also on show was Flexco’s Y-Type secondary cleaner which is suitable for use in aggregate applications. Providing improved belt-cleaning efficiency and easier and economical maintenance, the cleaner offers multiple blade options.
For dust containment in the belt loading zone, the company displayed its enclosed skirt system and dual-seal polyurethane skirting solutions. Another key focus was in helping to make belt installation and maintenance safer and simpler with several maintenance tools, including the company’s new TUG HD belt clamps, which have been specially developed to meet the most stringent safety test standards. Available in 6- and 8-tonne versions, the clamps are said to provide even tensioning across the entire belt width for ultimate strength, whilst their modular components offer increased versatility and portability.
Flexco’s exhibits for safer belt conveyors maintenance were rounded off by the company’s Flex-Lifter belt lifter, 900 series belt cutter and cordless electric belt cutter, whilst live demonstrations of conveyor belt rip repairs and 45° fastener installation using Flexco’s bolt solid-plate fastening system also took place on the stand.
General Tire, a brand of Continental, are launching a new line of foo-the-road (OTR) bias tyres in 2020. On show at Conexpo was the TE188 multi-purpose earthmover tyre for use on articulated dumptrucks, rigid dumptrucks, wheel loaders and scrapers. The tyre’s bi-directional pattern with massive bars provides gripping edges on soft and wet ground, whilst the wide ground patch leads to even wear, good surface interaction and a long service life. The TE188 comes in one E3 size (16.00-25) and seven E3/L3 sizes (ranging from 20.5-25 to 37.25-35).
Today’s assistance systems for construction machinery transmit a variety of optical and acoustic signals to the driver. They are, however, sometimes unheard or overlooked during daily work, which can lead to hazardous driving situations. Firmly integrated into the seat, the Haptic Warning System developed by Grammer creates a direct connection between the seat and the assistance systems. Reliable and perceptible, haptic signals alert the driver via the seat cushion and thus improve safety significantly.
Grammer presented numerous new products and further developments of their proven driver seats, including the MSG95EL/742 and MSG97EL/741, which offer maximum seating comfort in construction machinery and have not only been given a new design but also now come with additional functions. For example, the new S700 seat-top upgrade features pneumatic side contour control in the backrest cushion, allowing the seat to be adjusted even more individually to the driver’s requirements and offering significantly improved side support.
Also, the active seat climate control system is now more effective with up to a 40% increase in performance compared with the previous climate control system, whilst the two-stage seat heating provides pleasant warmth. Together with the new multi-function armrest, the seat forms an effective operator system from which the driver can control relevant vehicle functions comfortably and safely.
Komatsu showcased the breadth and depth of their entire portfolio at Conexpo, including an integrated solution for the quarry and aggregate markets designed to maximize productivity and uptime through a single-source supply system. The new Komatsu ZT44 drill rig, which made its debut at the show, forms part of this solution. Designed to enhance productivity in challenging geology, the versatile tracked drill has the flexibility needed to drill in a variety of settings, including small patterns and uneven ground conditions, as well as multiple angles and even dewatering (see April 2020 edition of QM for more details). However, taking centre stage on the Komatsu stand were the new WA475-10 and WA800-8 wheel loaders.
The WA475-10 wheel loader, which is well suited to quarry and waste applications, was developed to support customers’ needs for improved productivity and lower fuel costs. Its engine boasts 22hp more than the
WA470-8 model, but thanks to its Komatsu Hydraulic Mechanical Transmission (KHMT), achieves up to 30% better fuel efficiency. Moreover, the wheel loader’s Independent Work Equipment Control simplifies operation and further reduces fuel consumption by separating the accelerator pedal from the speed of the work equipment.
The improved operating environment includes floor-to-ceiling glass, ergonomically designed switch layouts, and a fully adjustable five-axis console for enhanced operator comfort. To boost productivity, the boom lift force of the WA475-10 has been increased by 20%, breakout force has been boosted by 8% and the new bucket design improves pile penetration, making it easier to fill and improving material retention in load-and-carry applications. Also, the machine’s auto-hill-holding function allows the WA475-10 to remain stationary on a slope without using the brakes, thereby reducing service brake wear and enhancing operation.
With its newly designed front and rear frame and loader linkages, the new fuel-efficient Tier 4 Komatsu WA800-8 wheel loader has the most durable chassis in this model’s history. Designed to load 60–100-tonne dumptrucks in quarry, aggregate and mining applications, the 115-tonne machine’s variable traction control and modulation clutch systems provide optimal tractive effort in various ground conditions, whilst the reinforced z-bar loader linkage is said to provide high breakout force even in the most challenging digging applications.
Leveraging the power of connected technology, the WA800-8’s automatic dig, semi-automatic approach, and semi-automatic dump systems can be used together or separately to automate the work phases when V-cycle loading dumptrucks, helping newer loader operators to become productive more quickly as well as reducing fatigue for all operators. To keep operators comfortable throughout long shifts, the cab has been re-engineered with a 7in high-resolution monitor, a heated and ventilated air-suspension operator seat, improved access, and enhanced visibility. KomVision with radar obstacle detection provides the operator with a bird’s-eye view of the working area on a dedicated monitor, whilst radar obstacle detection provides visual and audible alerts when an object is detected.
In addition to the latest model in their UltraWASH modular washing plant range, a major attraction on the McLanahan stand was their newly developed UltraDRY modular dewatering screen. This compact, skid-mounted unit is designed to improve the final product dryness of the discharge from a McLanahan fine material screw washer, as exhibited at Conexpo, but will work equally well with any other brand of screw washer.
Spray bars spanning the width of the dewatering screen provide a double wash for removing excess fine material from the product. The fines exit with the water through the screen media and into the sump underneath the screen, where they can either be sent to waste or returned to the screw via an optional pump feature.
Removable spacer blocks are a standard feature of the UltraDRY unit, allowing the operator to change the screen from a horizontal position to an inclined position. When preceded by a screw washer, the UltraDRY will normally run in the horizontal configuration. Screw washers typically deliver product with 15–30% moisture content, whereupon the UltraDRY further reduces this to as little as 7%, suitable for next-day sale. Should more retention time be necessary, the easy-to-install spacer blocks alter the dewatering screen from horizontal to inclined in the field.
The UltraDRY can also be used in conjunction with hydrocyclones, where the underflow is more dilute than the material discharge from a screw washer, and thus more retention time on the screen is necessary – another instance in which the dewatering screen would be operated in the inclined position.
Mobile crushing and screening equipment specialists McCloskey International demonstrated their continued growth with a total of nine products on display, encompassing both their newest machines and some of their latest features.
Tin particular, the first McCloskey C-Series cone crushers were officially unveiled at Conexpo. These third-generation mobile cone crushers have been designed to deliver superior performance, while also achieving higher capacity, better product quality, optimum versatility and improved fuel efficiency.
The new cones are said to marry the high performance and power of HP cones with McCloskey features such their open chassis design, with excellent access for service and maintenance. A new conveyor design, recirculating screen options, as well as continuous load and material level monitoring are standard features on this new product line.
The C3 cone crusher is equipped with a 3.78m x 2.2m integrated hopper with folding rear door, a 44in MC300 cone crusher with hydraulic close-side setting adjustment, and a 440hp power unit. The crusher offers both high material throughput and a high degree of control over the final product, whilst a large stockpile capacity is afforded by the main conveyor’s 3.88m stockpile height.
Among the other McCloskey exhibits on display at the show were the J45 jaw crusher, the I44RV3HD impact crusher, the heavy-duty S250 screener, the 516RE trommel screen, the long-hopper R155 scalping screen, and the SDX-150 telescoping stacker, which is now available with the company’s new lift axle option.
Rammer unveiled a host of new solutions at this year’s show, including the global launch of their giant 9033E hydraulic hammer – the latest addition to the company’s Excellence Line. Weighing 7,400kg, the 9033E is designed for carriers in the 65-tonne to 120-tonne range and has all the features found on existing hammers in the Excellence Line, but in a size and format that delivers the extra punch demanded on major quarrying and demolition projects. However, despite its extra power, Rammer say the design of the heavyweight 9033E means it is able to work quietly with a guaranteed sound level of 131dB LWA.
Topcon Positioning Group introduced their new Thermal Mapper for asphalt paving, which is designed to monitor temperature segregation, measure performance and provide accurate compliance reporting – all with real-time kinematic (RTK) positioning accuracy. The mapper records temperature readings behind an asphalt paver as the paving is in progress and provides a visualization to operators, in real time, of whether the mix falls within a pre-defined temperature range, and if any segregation is limited within specifications.
‘If too much segregation occurs, roads will soon develop major problems. The mapper quickly tells operators if the mix is stable or if moderate or severe temperature variation is occurring. If the readings are unacceptable, operators can adjust for more efficient and accurate project outcomes,’ said Murray Lodge, Topcon’s senior vice-president of construction. ‘The system’s sensors also bring to the market the first thermal mapping system with RTK GPS positioning for more accurate results than conventional methods.’
The system creates data reporting files to download through an interactive Pavelink module, the Topcon cloud-based logistics application for asphalt paving. ‘We are excited about where Topcon is taking the paving industry with the different solutions we are bringing to market. From SmoothRide, where we scan the existing road to determine the optimal design for variable depth milling and paving, to the newly released Pavelink system, we are focused on improving paving,’ said Mr Lodge.
‘Pavelink allows contractors to monitor the entire paving workflow from the batch plant, mixing plant, trucks, to the paver, to the rollers. By connecting the entire process, it allows the contractor to have full control over their projects in real time and make adjustments along the way, instead of after the fact as is so often the case with conventional methods. Now, bringing the heat sensor system into that workflow, we are giving contractors more resources to meet the specifications demanded today. It’s part of our commitment to revolutionize the planning and management of the asphalt paving process with real-time visibility throughout the project lifecycle.’
The next edition of the triennial Conexpo-Con/Agg show will take place from 14–18 March 2023 in Las Vegas, Nevada.
For more information visit: www.conexpoconagg.com
- Subscribe to Quarry Management, the monthly journal for the mineral products industry, to read articles before they appear on Agg-Net.com