Conexpo-Con/Agg 2020 Preview
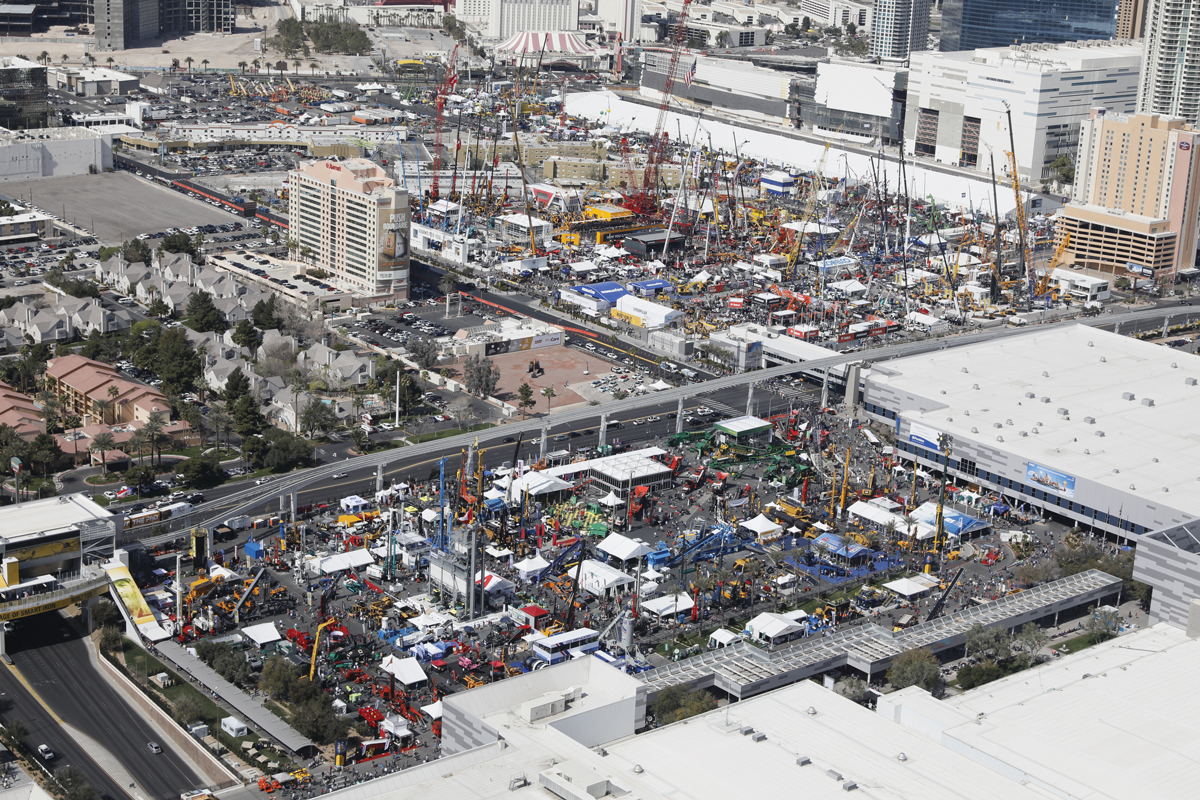
First published in the February 2020 issue of Quarry Management
With North America’s largest construction equipment exhibition set to open its gates in Las Vegas next month, QM takes a look at just some of the new plant, machinery and equipment that will be on show at this triennial showcase event
Conexpo-Con/Agg is North America’s largest construction trade show and the triennial gathering place for the world’s construction equipment and materials industries, with a particular focus on aggregates, asphalt, ready-mixed concrete, earthmoving, mining, quarrying and utilities, among others. Held every three years, the 2020 edition will take place from 10–14 March at the Las Vegas Convention Center in the heart of America’s gambling capital, Las Vegas. The event features exhibits of the latest technologies and innovations in equipment, products and services and attracts persons involved in all segments of the construction, aggregates, asphalt and ready-mixed concrete industries, including contractors, materials producers, and government and institutional sector officials.
This year some 2,800 exhibitors will showcase the latest technologies and innovations in equipment, products and services for the construction industries on around 2.5 million square feet of exhibition space. Product concentration areas as well as specialized exhibit pavilions will make it easy for visitors to locate specific products, services and exhibitors of interest, whilst a comprehensive education programme will also take place during the five-day exposition, with 150 seminars and sessions emphasizing industry issues and trends, management and applied technology. On the following pages, we provide a brief glimpse of just some of the new plant and equipment highlights that visitors will be able to see in Las Vegas.
Innovation, maximizing investment and being environmentally responsible are themes that will feature predominantly on the ALLU stand at this year’s Conexpo-Con/Agg. Exhibiting under the banner ‘Transforming the way you work’, ALLU will be using the show to highlight their materials-processing expertise, the strength and depth of their machinery attachments range and how they can help businesses maximize return on investment through improved productivity, efficiency and profitability.
The company will be showing a selection of machinery attachments from their existing Transformer, Processor and other equipment ranges. The ALLU Transformer Series – which comprises excavator/wheel loader/tractor-mounted processing buckets that screen, pulverize, aerate, blend, mix, separate, feed and load materials – will be the main focus of the company’s offering at the show.
Transformer Series bucket attachments on display will include: the DL2-09 with 8mm TS blades (thinnest blade model); DH3-17 with 16/32 TS blades; DH4-17 with 25/50 TS blades; and M 3-20 with 50mm TS blades. The development of the TS blade structure is one of ALLU’s most recent innovations for the crushing and screening market; catering for applications of all sizes and processing materials that can be screened, crushed, loaded and fed in one cycle.
The company’s Processor range is a powerful mixer attachment (fitted to excavators) which has been specially designed for the mixing and processing of the most difficult feed materials, such as clay, silt, peat, sludge, dredged material and contaminated soil. Visitors to the ALLU stand will be able to see the Processor 300HD attachment, with further exhibits to be announced ahead of the show.
Astec companies Kolberg Pioneer Inc. (KPI), Johnson Crushers International Inc. (JCI) and Astec Mobile Screens Inc., will be making a host of new product announcements as well as showcasing current aggregate processing equipment at Conexpo-Con/Agg.
KPI will be introducing their first hybrid FT4250CC horizontal-shaft impactor, which comes with a new two-deck pre-screen that minimizes the amount of undersized material passing through the chamber. The company says this reduces wear costs and increases the amount of final product by up to 30%. For economical fuel consumption, the hybrid option on the FT4250CC allows customers to operate the plant using either line power or diesel fuel.
KPI will also be showcasing their Pioneer 2742 jaw crusher, which features unique shaft and bearing assemblies for easy troubleshooting, reduced maintenance and ‘20% more capacity than competitive models’. Other products on show will include a demonstration of KPI’s new water-clarification technology.
Meanwhile, JCI will be exhibiting the latest addition to their Kodiak Plus cone crusher line – the K350+. The new model has been specially engineered to offer increases in drivetrain, stroke, horsepower, weight, head diameter and hold-down force, resulting in greater capacity compared with other similar-sized cones.
Astec Mobile Screens will be presenting their latest Ranger line of compact, track-mounted equipment. The mobile line will include a variety of jaw crushers, impact crushers, cone crushers, incline screens and trommels. These compact units will serve a variety of markets including construction, quarry operations and plant and tool hire. The ease-of-use, ease-of-transport, versatility and flexibility of the Ranger units makes them particularly suitable for smaller operations that require powerful machines with a limited footprint. Taking centre stage in the Astec Mobile Screens section of the stand will be the J20 jaw crusher.
The Caterpillar Conexpo-Con/Agg 2020 experience will include more than 30 Cat machines, including nine new product introductions. As successor to the Cat D5K2, Caterpillar say the new Cat D3 dozer continue to set the standard for small-dozer grading accuracy and efficiency. The operator cab delivers greater visibility, while enhanced controls deliver easier, intuitive finish grading and powertrain advancements improve fuel efficiency by up to 10% over previous models.
The new Cat 150 AWD motor-grader features all-wheel drive that assists with traction and manoeuvring, allowing the machine to work in any environment. Eco mode delivers up to 10% greater fuel efficiency without productivity loss, while the new mastless 3D Cat Grade control system unleashes the potential of the moldboard to give it a full range of motion.
Visitors will also experience the new Cat 725 articulated truck offerings. New cab features include assisted hoist, automatic retarder control and advanced automatic traction control, which improve operator experience and reduce operator actions. Performance improvements include up to 9% increased speed on grades, 8% improved acceleration and a 7% productivity increase.
Visitors to the show will also be the first to see Caterpillar’s latest remote-control offering, an enhanced operating station with expanded capability to operate multiple pieces of equipment, equipped with the Command Vision System, from a single remote station. The Cat Command remote-control system also offers a portable console, designed for line-of-sight use, which will also be showcased in the exhibit.
Also, making its North American trade show debut from Cat paving products, Command for Compaction automates the compaction process to increase quality. Featuring an intuitive interface for simple operation, Command for Compaction eliminates skill gaps to deliver up to 60% better coverage with consistent and precise overlap, constant speed and correct pass count.
CDE say they are set to revolutionize the wet processing industry once more with the launch of the latest in their range of Combo all-in-one wet processing solutions at Conexpo-Con/Agg 2020. The patented Combo – the world’s first all-in-one wet processing plant – was unveiled in Europe at bauma in April 2019. It was the first fully integrated, modular, patented turnkey materials wet-processing and water-management solution for the production of premium manufactured sands.
The latest model in the Combo range will have a number of soon-to-be-revealed enhanced features that have been specifically designed to allow operators in the Americas to capitalize on new opportunities.
David Kinloch, regional manager for CDE UK & Ireland, said: ‘At CDE, we are proud to deliver optimized operations for maximum yields and fast returns for our clients. Our high-performance solutions maximize resources and add huge commercial value to our customers’ enterprises, with the innovative Combo having led the way in a new era of wet processing.
‘We are looking forward to launching the latest Combo model at Conexpo-Con/Agg, directly to the very market that inspired it. This next-generation plant will deliver significant commercial benefits while minimizing operational costs.’
Importantly, the Combo is portable and incorporates all five essential processes – feeding, sizing, sand washing, stockpiling and complete integrated water management – on one compact and modular chassis. With a 30% reduced footprint compared with traditional set-ups it requires less civils expenditure and involves fewer planning requirements.
Kevin Vallelly, director of engineering at CDE, said: ‘The Combo is the first all-in-one materials processing system that accepts both natural sand and crushed rock feeds, giving our customers complete flexibility in the choice of the material they want to process depending on available reserves.
‘Having launched the Combo in 2019, we have further enhanced our game-changing technology to customize it to the American market. Delivering profitable material straight from the belt and minimizing operational costs, the Combo on display at CONEXPO-CON/AGG is the next phase in showcasing how CDE sand washing works.’
Haver & Boecker Niagara will be presenting their portable F-Class screening plant, which is said to reduce set-up time and extend machinery longevity for quarry and mining operators. The aggregate processing plant features a custom-built chassis and six hydraulic run-on jacks that quickly level the screen, eliminating the need for cribbing. The jacks also ensure the chassis stays level during operation, minimizing equipment wear.
‘Portable plants should not only give producers the flexibility to move from one site to another or within a quarry, but they should also be fast and easy to set up,’ said Karen Thompson, president of Haver & Boecker Niagara’s North American and Australian operations. ‘We are committed to producing mobile screening plants that possess these qualities, with the same durability, longevity and minimal maintenance as stationary vibrating screens.’
According to Haver & Boecker Niagara, users can move and set up the machine in under 30min at most locations. The custom-built chassis includes a hydraulic system that positions the vibrating screen at an optimal 20o angle. The plant has three screen decks and features an advanced double-shaft design supported by four high-performance, double-spherical roller bearings.
The F-Class unit is suitable for demanding screening applications (eg scalping and classifying ores, mineral, stone, sand and gravel etc.) that require consistent, load-independent performance at constant g-force. Operators can also customize the portable set-up to include a crusher or conveyor for enhanced productivity. Additionally, Haver & Boecker Niagara can offer the Pulse vibration-analysis programme to monitor the ongoing health of the F-Class and other vibrating screens through real-time views, logged reports and data analysis.
Participating at Conexpo-Con/Agg for the sixth time, Keestrack will once again present their latest full-line programme of mobile processing equipment for the recycling and aggregates industry.
Highlighting the heavy range will be the Keestrack H6e full hybrid cone crusher for secondary and tertiary crushing. With a maximum feed size of 215mm and variable crushing chamber configurations and stroke settings, the specially adapted cone crusher, based on proven Sandvik technology, can processes up to 440 tonnes/h. The powerful e-motors for the crusher drive and plant hydraulics (220kW and 2 x 30kW respectively) and all other directly electric-driven components are powered by a detachable power unit including onboard diesel and generator (345kW/500kVa) or plug-in via mains or external genset. An optional three-deck post-screen module
(24.5 m2) with oversize recirculation ensures high-quality end products. With all options fitted, the machine weighs 68 tonnes (56 tonnes without three-deck screen).
Designed for hard stone and recycling applications, the diesel-hydraulic Keestrack B4 primary jaw crusher – also available as full hybrid electric plug-in version B4e – accepts a maximum feed size of 600mm and has a feed capacity of up to 400 tonnes/h. Integrated pre-screening, a feed opening of 1,100mm x 700mm, closed-side settings from 45–160mm and automatic hydraulic gap adjustment ensure efficient production of defined end products. An ultra-sonic sensor provides optimal feed control, while the patented NSS auto-release system and reversible jaw movement ensure continuous production.
The company’s impactor range will be represented by the 30-tonne Keestrack R3 in its new award-winning design. Available as a diesel-hydraulic or fully hybrid e-version, the plant combines compact transport dimensions and low weight with production rates of up to 250 tonnes/h, making it well suited to short-term construction site operations or flexible semi-stationary production at medium-sized recycling companies or aggregates suppliers. An optional single-deck post-screen unit
(9ft x 4ft) with recirculation conveyor optimizes machine performance for the production of high-grade final product.
Keestrack will also be presenting their new S1e semi-mobile, plug-in electric feeder/stacker. Installed on a height-adjustable pedestal with lifting and 180o swivel hydraulics, the 6-tonne machine features a 39ft 4in conveyor capable of handling up to 200 tonnes/h of material with a feed size of up to 200mm. Monitored by an ultrasonic sensor, the stacker swivels automatically to create radial stockpiles of up to 2,900 tonnes, thereby minimizing loader traffic, labour and fuel costs as well as optimizing on-site safety.
Having commenced manufacturing in the US in 1970, Liebherr will be celebrating 50 years as a leading North American provider of construction equipment, products and services with an extensive selection of earthmoving and construction equipment at Conexpo-Con/Agg 2020. Among the company’s featured products will the US premier of the new generation of Liebherr crawler excavators. The Generation 8 series consists of seven models ranging from 22 to 45 tonnes. Two machines from the product range, the R 926 and R 938, will be on show for the first time in the US. Highlights of the new machines include higher engine power, a heavier counterweight for greater bucket capacities, and minimal fuel consumption.
Liebherr will also present four wheel loaders at the show, including an L 566 XPower with power-split travel drive, which combines optimal hydrostatic drive for short loading cycles with the benefits of mechanical drive over long distances and up hills. The L 566 XPower is also equipped with numerous new assistance systems, plus the new joystick steering for wheel loaders.
The L 538 model will represent Liebherr’s medium-sized wheel loader range. It is equipped with parallel kinematics for high holding forces in the upper lift arms area, making it particularly suitable for working in heavy-duty industrial applications such as recycling with high-dump buckets.
Liebherr’s latest Generation 8 dozers will also be introduced to North America with the new PR 736. Their dozer, powered by a newly developed Liebherr EVO-series diesel engine that meets emission level Tier 4 Final, has an operating weight of up to 25.5 tonnes and various blade versions (straight, semi-U and six-way blade) with capacities from 4.10m3 to 5.56m3.
MAJOR, a global manufacturer of high-performance screen media, will be using this year’s show to present their Flex-Mat high-vibration wire screens. The company’s technologically advanced wire screen media has been designed to deliver increased throughput by providing more open area than traditional panels.
According to MAJOR, Flex-Mat offers customers greater operational benefits with up to 40% more screen capacity than traditional woven wire and up to 50% more than traditional polyurethane/rubber panels, setting a new standard in performance for aggregates and mining producers. The product’s high-frequency movement helps make the media an active part of the screening process, improving efficiency compared with static media such as woven cloth and synthetic panels.
‘Quality is key to any operation, which is why we place a strong emphasis on it at MAJOR,’ said Bernard Betts, president of MAJOR. ‘We understand that no two operations are identical, which is why we configure each screening panel to precisely fit individualized requirements. That attention to detail is how we achieve what alternative media cannot — unrivalled throughput and superior end-product quality.’
The efficiency-enhancing characteristics of all Flex-Mat screening media products, including the modular panels, are created by bonding long-lasting OptimumWire with distinctive lime-green polyurethane strips rather than weaving them. This allows wires to vibrate independently from end to end under material contact. The high frequency of the wires, at 8,000 to 10,000 cycles per minute, adds to the vibration of the screen box (800–900 cycles per minute) which speeds up material separation and passing.
MAJOR say these features improve material throughput while virtually eliminating near-size pegging on the top decks and fine material blinding and clogging on the bottom decks, reducing the overall cost of production as well as providing up to five times longer wear life than traditional woven wire.
The Flex-Mat modular panels are available in three pattern options – D, S, and T series. The D series feature a standard square pattern for precise sizing, while the S series maximize open area to eliminate blinding and reduce fine contamination. The T series enhance screening for particles below 1.5mm and feature small openings to minimize blinding. The wire screen is secured through either grooved, step, or pin and leg panels.
MAJOR’s flagship Flex-Mat screen media panels are offered in either the patented OptimumWire or 304 stainless steel wire. They are also available in tensioned sections for use on crown decks.
At Conexpo-Con/Agg 2020, Metso will be showcasing their latest innovations and field-proven technologies for the aggregates industry, with a particular emphasis on the needs of small-to-mid-sized quarry operators and general contractors.
Previously launched at the 2017 show, the MX Multi-Action cone crushing technology has been well received by quarry operators around the world with close to 100 units sold in total globally. This year, Metso will feature the new MX3 crusher and a special Lokotrack mobile crushing plant equipped with an MX4 crusher.
Also on display will be the new Lokotrack ST4.10 mobile screen, a high-capacity screening plant for quarrying that further adds to Metso’s range of hybrid equipment. Other key offerings at the show will include Metso’s new lightweight truck body solution, which is available for all major off-highway truck models used in quarrying and mining operations.
In addition, with recycled aggregates becoming more acceptable in many regions, Metso will be showcasing their latest solutions in recycling and demolition, including their new, purpose-designed Nordtrack range, which includes track-mounted crushers and screens as well as track- and wheel-mounted stacker conveyors for recycling, demolition and small quarries.
At this year’s show, Philippi-Hagenbuch Inc. (PHIL), specialists in off-highway truck customization, will be showcasing a new version of their Autogate Tailgate specifically for off-highway trucks that require a 100% positive seal. The latest design can be paired with PHIL’s proprietary fluidic seal material to provide a water-tight seal that contains liquid materials within an off-highway truck body or roll-off container when environmental regulations make even slight spillage undesirable.
The Positive Seal Autogate Tailgate has been designed for any size off-highway truck and, when paired with PHIL’s simple and robust outrigger, its traditional scissors-style mechanism is said to provide an industry-leading maximum opening clearance at full dump. In the closed position, the new design locks into place and will not open under normal conditions without the body or container entering the ‘dump’ mode.
The Autogate Tailgate builds up the rearmost portion of the truck body to create a cohesive flange from which the tailgate compresses. Two hooks on either side of the base of the flange intercept a corresponding tag on the tailgate, allowing the tailgate to pivot inward as the sidearm and over-centre locking mechanism compressively locks the rear tailgate into place.
As with PHIL’s entire line of Autogate Tailgates, a three-year warranty is standard when installed with the company’s ‘installation supervision assistance’ scheme or at its Peoria facility, in Illinois. Optional body seals, fluidic seals and cushion pads are available to further customize PHIL’s Autogate Tailgates for unique applications.
When capacity is a concern, PHIL’s Positive Seal Autogate Tailgate can be built up for sideboards. These are available in 1in increments from 6in to 40in in height and provide a unified body height whilst increasing the volumetric capacity of the truck body, helping operators achieve optimal loads.
Making their ninth appearance at the Conexpo-Con/Agg show, Northern Ireland-based Rapid International will be exhibiting their Trakmix mobile continuous mixing plant, which offers an entirely self-contained design mounted on tracks, including an on-board genset, for fast, mobile flexibility.
According to Rapid, Trakmix is the first track-mounted mixing plant of its kind to market. Patent pending features include a superior control system that weighs all materials and a double-hopper cement weighing system. Popular with both civil engineering and road contractors alike, Trakmix is well suited to semi-dry mixing applications such as roller-compacted concrete (RCC), cement-treated base (CTB), soil stabilization, soil cement, bentonite, marine dredging, mine backfill and many more.
As a long-standing exhibitor, Rapid’s first Conexpo appearance was 27 years ago in 1993. The first ever Rapidmix continuous mixing plant was later sold to the US market in 1996 and is still operational today in Florida, 24 years later.
Sandvik Mining and Rock Technology will be showcasing several innovative solutions in application areas including rock drilling, crushing and screening, loading and hauling, quarrying and breaking and demolition.
For example, Sandvik’s Leopard DI650i down-the-hole (DTH) drill rig is designed for demanding high-capacity production drilling applications in surface mining and large-scale quarry applications. In addition to a powerful engine and compressor, the rig incorporates a highly ergonomic iCAB cabin and offers a high level of serviceability, mobility and fuel economy, along with scalable automation packages for superior overall productivity.
Also, being presented at the show for the first time will be SanRemo Mobile – a mobile device-based connectivity solution for Sandvik surface drill rigs which quickly and easily transfers drill plans, reports and other drilling data to increase operational efficiency.
The Sandvik UJ440i is an intelligent, fuel-efficient and user-friendly mobile jaw crusher. Featuring a fully tracked chassis and operated via radio remote control, the UJ440i is fitted with Sandvik’s 1,200mm x 830mm CJ412 jaw crusher, which offers effective size reduction, consistent production and more efficient operation.
Also on display from Sandvik’s mobile crushing and screening offering is the company’s modular 3.5m x 1.4m double-deck hanging screen, which connects to Sandvik QH332, QS332 and QI442 tracked crushers for operation in open or closed-circuit configurations. The complete module can be installed or removed from the plant in less than 30min, without any need for on-site lifting equipment.
The new CH840i cone crusher, which features mechanical upgrades, connectivity, advanced automation and rebuild possibilities, comes with Sandvik’s Automation and Connectivity System (ACS) as standard, to continuously monitor and optimize crusher performance and control the complete lubrication system, for increased uptime and reliability.
Sandvik’s new SJ circular-motion screen range is specially designed for extra heavy-duty, medium and fine screening applications. This inclined screen range is well suited to screening after primary and secondary crushing, as a splitter screen to divide flows within a plant and for final screening of a finished fraction.
For demolition and recycling, the latest hammer offerings from the Rammer Excellence and Rammer Performance lines will be on display, as well as Rammer’s purpose-developed RD3 remote-monitoring device, which uses the MyFleet Telematics service to track and monitor fleet equipment usage without any need to go to site to collect the data.
Superior Industries Inc. plan to debut their brand-new Sentry horizontal-shaft impactor (HSI) at Conexpo-Con/Agg, one of a dozen new products the company will be introducing during the Las Vegas trade show.
Superior’s Sentry HSI is designed with a fully fabricated open-style rotor which produces low inertia energy for a lower cost of ownership. In addition, proper spacing inside the crusher’s chamber creates more area for processing larger feed sizes. Also, owners and operators will be able to safely and easily complete maintenance of the HSI’s mainframe components via a hydraulically controlled opening and closing feature.
Other design elements include commonly shaped side liners, hydraulically adjusted curtains, mainframe inspection doors and a replacement upper feed opening. One- or two-piece blow bars manufactured with two or four rotors are equipped with fixed clamping for best performance in hard rock applications.
Superior define their new line of Sentry HSI’s by rotor size and have 15 models available with production capacities ranging from 80 to 900 tonnes/h and maximum feed sizes from 400 to 1,000mm.
Superior will launch 11 other new products for crushing, screening, washing and conveying applications. Among the equipment on display will be the Fusion modular platform; Liberty jaw crusher; Alliance low water washer; and portable Spirit wash plant.
Additional equipment with new features will include the Anthem inclined screen; Valor vertical-shaft Impact (VSI) crusher; P500 Patriot cone crusher; Aggredry dewatering washer; and TeleStacker conveyor.
Moreover, aftermarket solutions including new conveyor idlers, pulleys and accessories, plus crushing rotors, cone bushings, cone heads and jaw dies will be displayed alongside a multimedia experience showcasing several turnkey projects completed by the company’s construction management division.
Displaying solutions for ‘today and tomorrow’, Volvo CE will present more than 30 machines and related uptime and productivity services, including a number of global and regional launches, across 5,574m2 of show space in Las Vegas.
Volvo CE will be joined by sister companies Volvo Penta, Volvo Trucks and Volvo Financial Services, who will be presenting the latest engine, truck and financial offers. Likewise, Volvo CE’s other equipment brands Terex Trucks and SDLG will be present at the show.
Melker Jernberg, president of Volvo CE, said: ‘Our presence at Conexpo is set to be our best yet – with a fully immersive technology experience to highlight the changing face of construction. Innovation has long been a part of our DNA, and we are especially proud to be bringing it to the mainstream with the unveiling of some game-changing launches at this year’s show.’
Anchoring the booth will be show-stoppers from both the largest and smallest models in the Volvo range. The company’s biggest exhibits will be on prominent display – namely the heavy-duty EC950F crawler excavator, which is now available globally, and the R100E rigid hauler, both of which are designed for quarrying, mining and mass excavation.
Also prominent will be the new EC300E hybrid excavator, which is now available in North America, while in road machinery Volvo will debut their 8ft-class P5110B tracked and P5170B wheeled pavers. Conexpo-Con/Agg 2020 is also where Volvo will reveal two new concept models that herald where the company is taking connected, electric, and autonomous machines.
In addition, attendees will be able to familiarize themselves with the Volvo Assist technologies that are now standard on many products, with hands-on demonstrations to show how the machine-control software gives operators greater accuracy and time savings. Also, an extensive array of more than 30 attachments, from buckets to couplers and breakers, will be fitted on equipment across the Volvo stand.
Wirtgen Group will be exhibiting the newest technologies, equipment and services on their ‘Innovation. Performance. Partners.’ themed stand. More than 30 machines will be on display, including 10 worldwide and North American premieres, as well as Wirtgen’s latest large milling machines.
Conexpo-Con/Agg 2020 will mark the international launch of the new W 250 Fi and W 220 Fi cold-milling models, while the large W 210 Fi and W 207 Fi milling machines, along with the W 380 Cri cold recycler, will make their North American debut.
Vögele will be unveiling their software-based application WITOS Paving Docu for the first time in North America. The latest innovation has been specially developed for contractors who want to record and evaluate other data in addition to the paving temperature, but who do not need the full range of WITOS Paving Plus functions, including process optimization.
Hamm will be travelling to Las Vegas with no less than three trade show premieres. The specialists for asphalt and soil compaction will be introducing their new HP 180i pneumatic tyred roller; DV+ 90i VV-S tandem roller; and H 20i C P remote-control compactor with a padfoot drum, new thrust shield and impressive gradeability.
Wirtgen Group’s product premiere will be topped off by two aggregate processing machines on display from Kleemann – the Mobicat MC 120 Z Pro jaw crusher and Mobiscreen MS 952 Evo mobile screening plant.
- Subscribe to Quarry Management, the monthly journal for the mineral products industry, to read articles before they appear on Agg-Net.com