Understanding the Different Types of Crushers
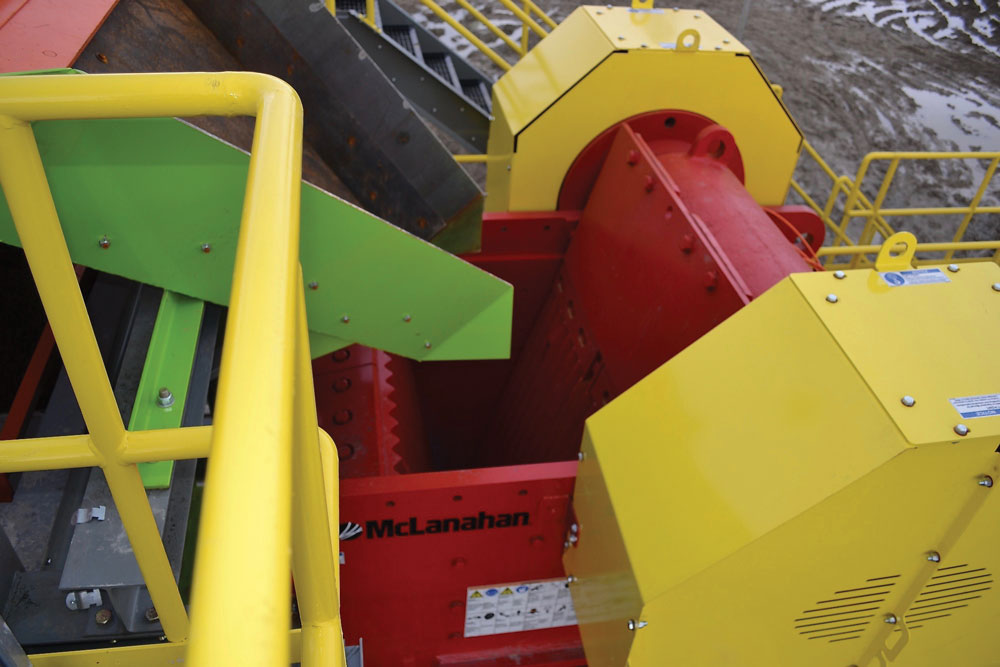
First published in the September 2018 issue of Quarry Management as Competent Crushing
Understanding the different types of crushers and how to look after and feed them for maximum efficiency
Selecting an appropriate crusher, or indeed any piece of processing equipment, is important in every quarry operation. Understanding what each crusher type is used for and knowing some general efficiency tips and the proper way to feed these machines will lead to the best results for any given site. Each type of crusher is different and each is used to achieve a particular result. Likewise, to obtain a specific output, each type of crusher requires different maintenance tasks to keep it running efficiently. Operators who can achieve this, along with a consistent feed to the crusher, will be the most efficient and, more importantly, the most profitable.
Jaw crushers
A jaw crusher is a compression type of crusher. Feed material is reduced by squeezing it between a moving piece of steel and a stationary piece of steel, with the discharge size controlled by the gap setting, ie the space between those two pieces of steel. The tighter the setting, the smaller the output size and the lower the throughput capacity.
Jaw crushers are mainly used in primary crushing stages and are rarely used for secondary crushing. As a compression crusher, this type of machine generally produces the coarsest material because it breaks the rock along its natural lines of weakness. Jaw crushers are an excellent primary stage solution to prepare rock for subsequent processing stages, such as washing, classifying or secondary crushing.
General efficiency tips:
- Grease lubrication systems are preferred over oil-lubricated systems.
- Inspect the radial clearance of the main frame bearing annually and record the results to track bearing wear.
- The minimum discharge setting should not exceed full-load amps.
- Do not crush oversize material against the barrel of the jaw. This area is not considered to be part of the crushing chamber.
- Periodically sample the oil in the bearings when using oil lubrication.
- The discharge conveyor and hopper under the crusher should be wider than the discharge width of the crusher.
- Sufficient tension must be placed on the toggle plate to ensure proper alignment.
Feeding for efficiency
Jaw crushers are routinely choke fed to maximize production capacity and ensure that particles are uniformly broken. This promotes stone-on-stone crushing, which breaks up flaky or slabbier particles. Those seeking fewer fines should try trickle feeding material into the jaw crusher. Keep in mind, however, that this will have an adverse effect on particle shape and will also reduce throughput capacity, hindering the crusher’s efficiency. Ideally, the feed rate should not be switched from choke to non-choke, as this can cause problems downstream at the secondary processing plant. In practice, many jaw crushers are fed in this intermittent fashion due to gaps in the delivery of feed material from the quarry. Jaw crusher feed should be pre-screened using a grizzly prior to crushing to remove any material finer than the closed-side setting.
Cone and gyratory crushers
Cone crushers and gyratory crushers are also compression-type machines that crush material between a moving piece of steel and a stationary piece. The output is controlled by the setting between the two pieces of steel. Though the chamber is round in shape, the moving piece of steel is not meant to rotate. Instead, a wedge is driven around to create compression on one side of the chamber and a discharge opening on the opposite side. Cone crushers are used in secondary and tertiary roles as an alternative to impact crushers when product shape is an important requirement but the proportion of fines produced needs to be minimized. Even though the reduction in fines produced may only be a few percentage points, this could represent a significant amount of material in a large operation and, ultimately, increase a company’s bottom line and profitability.
General efficiency tips:
- Be especially careful that a cone crusher does not suffer from ring bounce or chatter.
- Variable flow controlled by level sensors will ensure consistent feeding and maintain a full crushing chamber.
- Low oil temperature should prevent operation of the unit.
- High oil temperature should stop the crusher feed and allow the unit to cool down. After the machine has cooled, further investigation of the high-temperature condition is needed before the machine is operated again.
- No oil flow should prevent operation of the unit. If the condition occurs during operation the feed should be stopped immediately, with the crusher stopped 30s later.
- Gradations of cone feed and crusher discharge must be monitored as both a crushing/reduction performance indicator and a liner wear indicator. This should be done at least once a month, and more often if required.
- Daily inspections below the crusher should be made to ensure no bridging, plugging or foreign material is under the crusher.
Feeding for efficiency
Uniform distribution of feed material around the cone crusher inlet is good practice. This allows production of a consistent product as well as efficient, reliable operation of the crusher. Choke feeding is important for ™b to maintain approximately 10–15% of material finer than the closed-side setting in the feed to assist the crushing action. More than 10–15% will likely cause ring bounce due to the pressures in the chamber.
Impact crushers
An impact crusher uses mass and velocity to break down feed material. First, the feed material is reduced as it enters the crusher and makes contact with the rotating blow bars or hammers in the rotor. Secondary breakage then occurs as the material is accelerated into the stationary aprons or breaker plates. Impact crushers tend to be used where shape is a critical requirement and the feed material is not very abrasive. The crushing action of an impact crusher breaks a rock along its natural cleavage planes, giving rise to better product quality in terms of shape. The quality of these products makes them ideal for use in highly specified roadstone and concrete aggregate applications.
General efficiency tips:
- Primary impactors should be of a solid rotor type to reduce maintenance costs.
- Impactors should have a connected horsepower sufficient to ensure 110% utilization. The crusher application, speed and setting are the factors affecting this.
- Impactors should be consistently fed based on the amperage drawn.
- Impactors should be fed evenly over the full width of the rotor.
- Precise calculations are needed to achieve the correct material penetration into the rotor.
- The efficiency of a secondary or tertiary horizontal-shaft impactor decreases with the mass and size of the material. The smaller the size, the less effective the crushing.
Feeding for efficiency
Size reduction in an impact crusher relies on energy being conveyed into the rock from the rotor, and it begins with the feed. The initial impact is responsible for more than 60% of the crushing action, with the remainder being made up of impact against an adjustable breaker bar and a small amount of inter-particle collision. This is why it is vitally important that the feed arrangement to an impact crusher ensures an even distribution of feed material across the full width of the rotor. This will allow for even distribution of energy into the feed material and uniform wear patterns, ensuring consistent product gradation and power consumption.
Remember, when selecting the correct crusher to best suit a particular operation, it is important to understand the requirements for each stage of crushing and how to properly feed each crusher. During the primary crushing stage, the aim is to get the material to a size that conveyors and other aggregate processing machines can handle. Generally, jaw crushers are installed at this crushing stage. Some operations will need further crushing in secondary and tertiary crushing stages. These stages are used to better control and size the output. Impact crushers and cone crushers tend to be used during these stages to better control particle size and shape. Understanding how to best match the type of crusher to the right crushing stage, as well as working with a manufacturer to properly size the crusher, will ensure crushing and feeding efficiency throughout an operation and, ultimately, overall profitability.
For further information visit: www.mclanahan.com
- Subscribe to Quarry Management, the monthly journal for the mineral products industry, to read articles before they appear on Agg-Net.com