ARJA’s Impact Crusher That Can Match Cone Crusher Performance
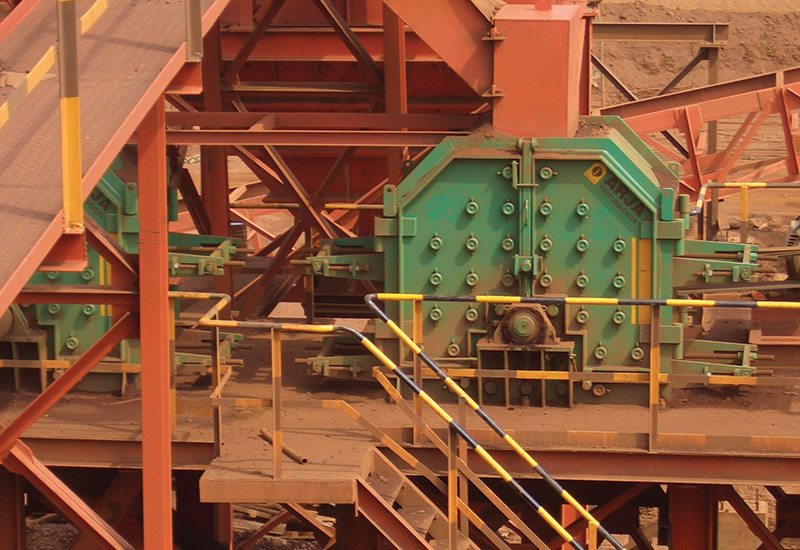
First published in the September 2014 issue of Quarry Management as A New Era is Here
Continuous research and development by a few manufacturers has allowed some impact crushers to match or even exceed the wear cost performance of cone crushers in hard and abrasive stone applications, offering operators cheaper and better results. Spanish impact crushing specialists ARJA explain how
The post-primary crushing sector is largely divided into impact crushers for the processing of softer stone and cone crushers for the processing of harder, more abrasive stone, and the advantages of both machines are well known. The impact crusher, for example, has a higher coefficient of reduction, produces crushed material with an optimal cubic shape for asphalts and concretes, allows faster and simpler maintenance, has a lower acquisition cost, gives continuous production curves with no irregularities or breaks between sizes, permits bigger feed sizes, delivers higher production of small sizes etc. The cone crusher, on the other hand, has the advantage of fewer wear parts.
The vast majority of impact crushers have been conceived and designed to process releatively soft stone. Accordingly, their construction materials and components are strong enough to cope with this kind of material, but are generally insufficiently robust to crush harder, more abrasive materials such as granite, flint, basalt and iron ore.
However, what would happen if impact crushers could match cone crushers in terms of performance and wear costs? In emerging markets such as Russia, Africa, East Asia and South America, among others, cone crushers are increasingly being replaced by impact crushers in granite and basalt quarries, providing an improvement in the quality of the crushed material and a reduction in the cost per tonne, thereby increasing the competitiveness of some companies against their local rivals.
But how have these impact crushers reached the wear parameters of cone crushers? In the past, the philosophy of using impact crushing for hard and abrasive stone was mostly limited to very small niche markets, especially in countries such as Spain and Germany. It was in markets such as these that the impact crusher evolved and matured for 50 years to become the trusted product that it is today.
Based on innovation and experience, and an awareness of the advantages and disadvantages of impact crushers compared with cone crushers, and the opportunities that this implies in overcoming the problem of wear, a few manufacturers have worked on two key areas: improving impact crusher efficiency and wear parts management; and developing the technology of the materials from which the parts are made. The development of ceramic chrome alloys to increase the durability and abrasion resistance of wear parts, together with evolution in the management of these parts during use, has resulted in a significant reduction in the cost per tonne of material produced.
Competitiveness of impact crushers against cone crushers
The smaller the output size, the more competitive impact crushers become, because their percentage of finished product in the first pass is considerably higher than cone crushers. Combined with an upgrade to the wear parts materials, this can allow impact crushers to reach a lower wear cost ratio (€/tonne) than cone crushers (see table 1).
While it cannot be denied that the useful hours of impact crusher wear parts have not yet reached the useful hours of cone crusher wear parts in tertiary stage works, they have been upgraded enough to be a better option than cone crushers in some situations, allowing them to reach figures like those shown in table 1.
For secondary stage works, impact crushers have equalled cone crushers, successfully overcoming all their disadvantages and matching their main advantage, the wear cost ratio.
There is, however, an extra feature available when using a secondary-stage impact crusher instead of a cone crusher. Because of an impact crusher’s ability to deal with bigger feed sizes, the primary-stage equipment can be smaller (ie lower purchase cost) or production through existing primary stage machines can be increased because the jaw crusher will be able to work at a wider setting.
Impact crushing is also more eco-friendly and can help save energy. A cone crusher will require the installation of a downstream VSI to achieve a similar cubic shape as that of an impact crusher, ie two machines instead of one and double the energy consumption. Also, the friction-less movement and physical weight of the rotor and blow bars in an impact crusher help facilitate the rotation, thereby drawing less power from the motor. This does not apply with cones because of the continuous friction involved in achieving the cone crushing action.
The reason why impact crushing has not been developed in this way before is because most manufacturers produce both cone crushers and impact crushers, and each product is focused on its own market segment. Moreover, cone crushers are much more expensive to purchase than impact crushers and provide greater returns for manufacturers. Most crusher manufacturers, therefore, are not interested in developing their impact crushing lines out of the soft-stone segment and prefer to invest their R&D resources in the upgrading of their cone crusher lines. Only a small number of manufacturers, such as ARJA Group, have focused their activity solely on manufacturing and developing impact crushing technology.
ARJA Group impact crushers
ARJA Group’s philosophy is to make the difficult easy; simplifying machines to the maximum in the smartest way possible. In hostile environments such as quarries or mines, it is essential to reduce the chances of breakdown and, as far as possible, facilitate any repairs. ARJA not only work towards this goal in the design of their crushers, using the best materials and parts from top-quality brands, but have also implemented this philosophy in their manufacturing processes, improving efficiency and productivity in order to be able to deliver any shipment in two weeks.
Currently, the most successful ARJA impact crushers are Tauro-series secondary-stage crushers and Piscis-series tertiary-stage crushers, as well as the affordable Libra series for smaller-scale secondary and tertiary work. All three series are available in permanent, mobile and semi-mobile formats, and with more than 10 years’ experience in the UK, ARJA Group have delivered a considerable number of proven solutions to meet the challenges of the UK market.
The ARJA Tauro (40 to 300 tonnes/h) is the flagship series of the company. Designed as a secondary-stage impact crusher, the Tauro has the versatility to carry out primary works, by supporting a maximum input size of 300mm, as well as tertiary works because of the wide range of adaptable elements of the crusher, such as rotor speed or apron adjustment. According to ARJA, Tauro-series features that users appreciate the most are: the excellent cubic shape of the crushed product; the performance, robustness and the reliability of the machine; and fast and easy maintenance – a single operator can change the blow bars in just 30min.
The ARJA Piscis series (50 to 180 tonnes/h) is the company’s other star product line. These tertiary-stage impact crushers stand out in the market due to their high production of 0–10mm material in the first pass, reducing recirculation to around 15–25%, and their ability to crush hard and abrasive stone (granite, basalt, pebbles etc). The Piscis-series machines also allow one of the largest input sizes on the market (90mm). The most appreciated features of these machines are: their huge capacity for sand production; the quality of the sand produced; their low wear cost per tonne produced; and efficient management of their wear parts.
For further information visit: www.arja.com
- Subscribe to Quarry Management, the monthly journal for the mineral products industry, to read articles before they appear on Agg-Net