Wear Solutions for Critical Quarry Assets
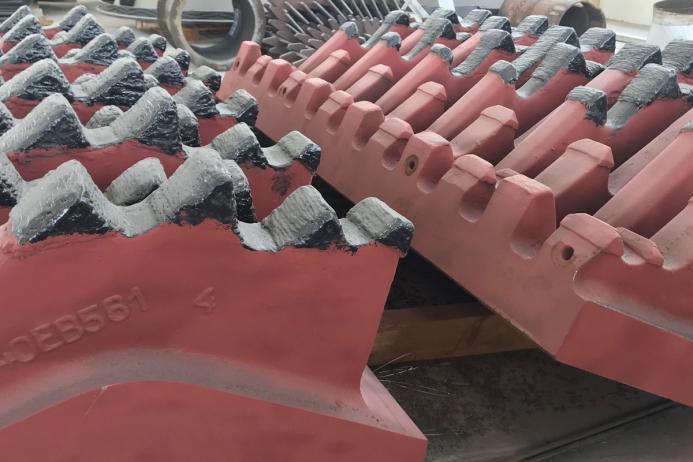
First published in the September 2023 issue of Quarry Management
Advances in wearfacing technology can make quarry operations more sustainable whilst increasing their profitability, as Mateusz Gierek, technical application specialist at Castolin Eutectic, explains
Equipment used for the extraction, processing, and transport of quarried materials is subject to powerful abrasive and erosive forces, as well as heavy impact shocks and vibrations. The need for frequent replacement of worn and damaged parts with new ones may seem inevitable, but Castolin Eutectic have taken a different view.
The company’s long-held philosophy is that repairing and strengthening parts makes more sense – both economically and in terms of sustainability.
Fundamentally, discarding worn parts and using more metal to make their replacements is a waste of the Earth’s resources. Manufacturing new parts also consumes extra energy and adds to carbon emissions.
By extending the lifespan of wear parts, wearfacing technology – or hardfacing as it is sometimes known – not only addresses environmental concerns but saves money. It can be applied to new equipment or added later as part of a repair and restoration process, which gives components a second life and a better-protected future.
A longer lifetime means less downtime for replacement work – saving on maintenance labour costs and lost productivity. Meanwhile, less investment is tied up in buying and accommodating large stocks of spare parts.
In cases where maintaining a component’s original shape optimizes the equipment’s effectiveness and energy-efficiency – wearfacing may bring additional benefits in relation to output, fuel economy, and carbon footprint.
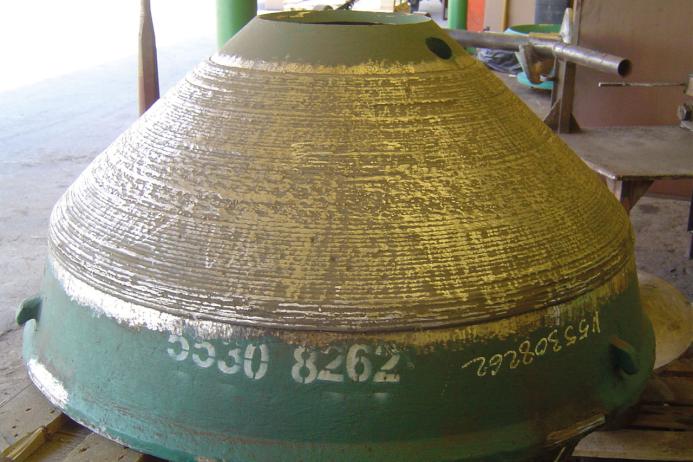
Wearfacing treatments
Essentially, most of Castolin Eutectic’s wearfacing treatments involve the application of advanced alloys to surfaces. The compounds and structures used are carefully selected to meet the demands of each specific situation. Choices and combinations are almost unlimited.
They are applied as coatings, as welding wires or as weldable steel wear plates hardened with alloys. These CDPs (CastoDur Diamond Plates) are easily cut, shaped, and fitted to protect any surface.
If required, they can be pre-cut and formed into sections of a given size and shape, ready for application to the equipment. They are then simply attached using screws, rivets or spot welding. A further advantage is that individual plates can be repaired or replaced in the event of localized wear.
Like any other wearfacing solutions, wear plates are available with a variety of alloy compositions to meet different needs. An important factor in the choice of these alloys is the inclusion of carbides, which add considerably to their hardness. In laboratory tests for abrasion resistance, according to the US standard ASTM G65, CDP wear plates last five times longer than standard wear plates.
For the transport of abrasive and erosive materials through pipework, another ready-made solution is available in the form of tubes that are lined with wearfacing alloys. They can be supplied in a variety of diameters and section lengths, with elbows or Y-joints as necessary, and are easy to join.
Wear challenges and solutions
The equipment and processes used in quarrying are many and varied, but a few examples will help illustrate some of the situations in which wearfacing can help.
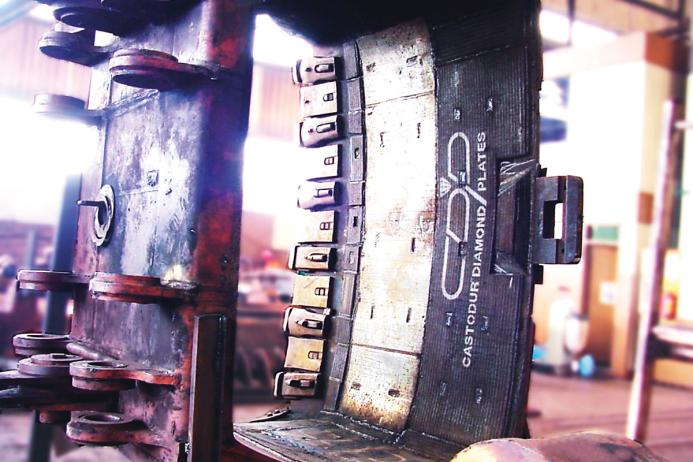
Excavation
The buckets/shovels of diggers, loaders and similar machines may wear very quicky on both their internal and external surfaces. The same is true of dredging equipment whose buckets are used to dredge sand or gravel from underwater deposits.
To slow down such wear, they are often fitted with protective liners. A more effective way of protecting those surfaces is with a section of wear plate that is cut to fit the vulnerable area. This can be quickly replaced when it becomes worn.
The very largest mining or quarrying shovels may require a variation on this approach. Sometimes the edges, which come into most aggressive contact with quarried materials, are protected by large blocks of hardened steel that wear away to nothing within about two weeks. Regular replacement is the only option. However, other surfaces of the shovel can be protected by wear plates.
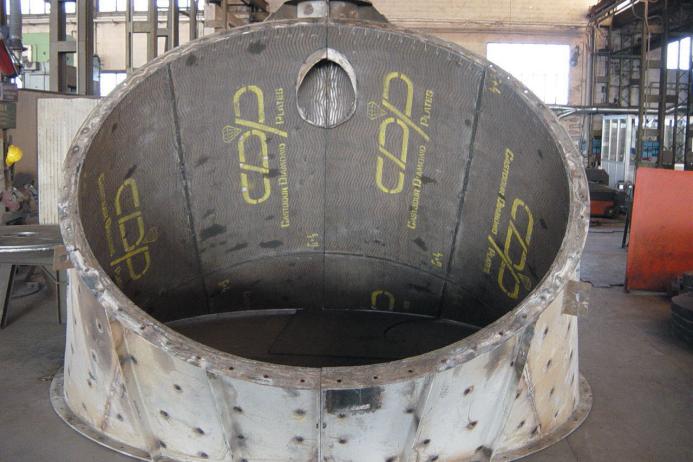
Processing
Large rocks are fed into primary crushers, and the resulting smaller pieces may be reduced subsequently to smaller sizes in other crushing equipment. The surfaces of the crushing teeth and hammers can be hardened with alloys to increase their service life.
Other wearing surfaces in these machines are often overlaid with wear plates. In cone crushers, for example, ready-cut pieces of plate can be supplied for simple application, on site, to the most exposed surfaces.
In a primary crusher, pounding by heavy rocks, with massive forces and high vibration levels, can damage the machine’s overall cast steel construction. This is difficult to weld but with specialized welding knowledge and technology, it is possible to repair cracks in cast structures.
After crushing, rocks may be screened for grading. The screen or sieve may be made from polymer, wire or – for longer life – hardened steel. As the sieve wears, its holes enlarge and it allows material of a larger size to pass through. Even with hardened steel, this may only take a week or two.
The problem is that in making the holes, using plasma cutting, for example, the steel is heated and loses hardness at the hole edges. The answer is to make screens from wear plates whose hardness is unaffected by the hole-cutting process.
A further process in sand and gravel quarrying is washing. Washers are typically fitted with rotating shafts, armed with rows of blades. Making these blades from wear plates will enable a longer life.
Transport
Between stages of processing, rocks may be transported on conveyors – often at high speed. There is much abrasive contact with the sides of the conveyor, so pre-cut sections of wear plate can be ordered to apply on site.
Similarly, the surfaces of chutes used to direct materials to different processing lines can be covered with wear plate. In one example of a plate that acts as a switch to direct the flow of material to different places, it is now possible to apply wear plate on both sides of the structure.
The load-contacting inner surfaces of any vehicle or container used for quarried products can also be lined with ultra-hard plate. This includes dumptrucks and freight trucks, as well as hoppers and skips.
Pipework may be used for transportation of dust extracted from quarry operations, and for movement of sand, gravel or sludge. Effective dust-extraction systems are important for two reasons. First, they remove a serious airborne hazard to people’s health, in and around quarries. Secondly, they minimize the potential for rain-soaked dust to create a sticky mud which ‘glues’ aggregates together and makes them more difficult to handle.
Dust and submerged sand are especially abrasive due to the combination of their fast flow speeds and their hard, sharp-edged particles. Elbows in pipework face the harshest wear forces. In operations where elbow replacement is currently a monthly task, using CastoTubes from Castolin Eutectic can make it more like an annual one.
Cost-saving co-operation
Depending on their circumstances and preferences, quarry businesses may need a full, end-to-end wearfacing service, from inspection, analysis and monitoring of wear problems to implementing solutions. This appeals particularly to quarry operators with minimal in-house staffing for equipment maintenance. Alternatively, a company’s own engineers may simply need advice, training, and supply of products.
It should be stressed that repair of materials like cast iron and cast steel is difficult and requires highly specialized knowledge. Castolin Eutectic have a global network of 400 technical advisers with the necessary expertise to solve these wear and repair problems. Their specialisms include welding, brazing, coating, and more. Wherever you are in the world, a reliability engineer can be on site quickly to provide help.
As one illustration of the cost-saving benefit of repair over replacement, it was recently noted that a digger arm repaired by Castolin Eutectic seven years ago is still working today. Repairing the large crack in this machine had required about a week of specialized welding, at a cost of €3,000. A replacement arm would have cost €25,000.
Aside from saving on the cost of replacement parts, this approach makes businesses much less vulnerable to supply chain problems. During the recent pandemic, for instance, some parts were difficult or impossible to obtain, especially from Far East suppliers. By refurbishing, rebuilding, and strengthening existing components, a closed loop is created. Space, time, and investment dedicated to stocking spare parts can be redirected.
Better still, the hardening processes used on new parts improve the quality of OEM parts. Not surprisingly, some customers are now asking OEMs to use Castolin Eutectic’s ultra-hard materials when building machines.
Importantly, specifications for the shape and size of wearfacing linings and other pre-cut pieces can be calculated accurately, even if the equipment’s technical drawing no longer exists. Using a 3D scanner and portable measuring arm, reference points are plotted, and documentation is quickly recreated through reverse engineering.
For a quarry business with its own maintenance team, many wear parts that would previously need to be stocked can be replaced by versatile repair kits, with advice and training to support the process. In fact, when it comes to a relatively simple task such as attaching a wearplate, no great amount of specialized expertise is needed.
Measurable environmental benefits
Reducing material consumption, energy use and carbon emissions has rapidly become a top priority for quarrying businesses. The EU’s increasingly stringent sustainability-related legislation has been a major driving factor, along with public pressure to protect the environment. More and more companies have ESG (Environmental, Social and Governance) strategies and aims.
Wearfacing can help considerably in meeting environmental targets. To calculate its impact, Castolin Eutectic have developed an EcoTest calculator. For any suggested refurbishment solution, this shows the tonnages of metal and CO2 that can be saved by preventing wear. Other ways of reducing emissions include using hydrogen instead of acetylene for brazing.
The solutions summarized here are just a small sample of what has been developed through many years of research and experience. It is not a one-size fits all approach. In practice, quarries will get the best results by assessing each wear concern and its circumstances individually before identifying the ideal wear-management solution.
For further information visit: www.castolin.com
Subscribe to Quarry Management, the monthly journal for the mineral products industry, to read articles before they appear on Agg-Net.com