Next Chapter for Rokbak
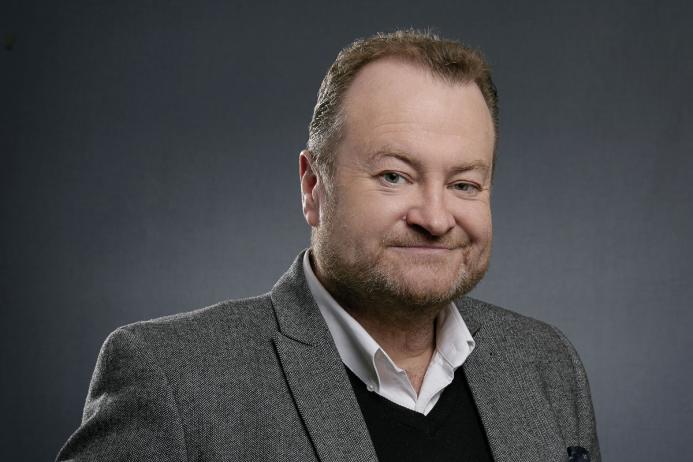
First published in the November 2022 issue of Quarry Management as Solid as a Rok
It has been a little over a year since Terex Trucks rebranded as Rokbak, replacing a well-known, recognizable industry brand with a fresh new name, image, and identity. Paul Douglas, managing director of Rokbak, talks to Quarry Management about the exciting new chapter for the Motherwell-based OEM and its ongoing drive for growth, improvement, and innovation to meet the evolving needs of its customers
When managing director Paul Douglas announced the rebranding of Terex Trucks at a virtual launch event last September, it caught everyone in the heavy construction equipment world by surprise.
Rebrands, after all, are risky business. Changing something is often much harder than starting from scratch and when rebranding takes place, companies must go to great lengths to connect and communicate with their customers, and not risk damaging the brand value that they have built up over the years. However, there are plenty of real-world examples of businesses that have taken the leap and reaped the rewards.
Ever since Mr Douglas unveiled the new Rokbak brand in the presence of hundreds of employees at the OEM’s Motherwell factory in Scotland – not to mention the highly successful online launch event – the company’s rebrand has generated an extremely positive reception from customers and dealers alike, and even garnered multiple national marketing awards, confirming that the decision to replace an established industry name with a new, unique corporate brand was indeed the right thing to do.
‘The rebranding project started around four years ago and it has been a massive learning curve for everyone at Rokbak,’ said Mr Douglas. ‘We’re not PR specialists or branding experts so it was very important, with the support of the Volvo Group, to launch the rebrand correctly and at the right time.
‘The work involved in the rebranding process from Terex Trucks to Rokbak was hugely challenging and complex. We had to think carefully about the brand strategy and development, the visual identity refresh, copyright ownership, the new website, delivery sequence et cetera, followed by a full roll-out of the rebrand across the markets we serve.
‘Whilst these developments and changes took place, it was also fundamental for our rebranding/marketing team to preserve the strong hauling heritage, expertise, and traditional core values that we’ve built in our 80-plus-year history – and translate all of this into the new Rokbak brand.’
Better than ever
The articulated hauler manufacturer recently held a milestone event in Motherwell to celebrate the brand’s first anniversary and Mr Douglas, who began his career with Rokbak more than 35 years ago, is clearly excited about what the future holds for the business and the challenges and growth opportunities going forward.
‘We are delighted to be celebrating a successful first year in business under the Rokbak brand,’ he commented. ‘The past two-and-a-half years have been challenging for most OEMs due to the Covid pandemic, Brexit, rising energy/material costs, and labour shortages. Ultimately, for us, it has also been an unprecedented time in which we have made remarkable progress as a business.’
With more than eight decades of experience developing and manufacturing reliable and robust articulated trucks, Rokbak say their haulers – the RA30 and RA40 – have become firm favourites among customers working on a variety of jobs, including quarries, mines, large-scale construction projects, and infrastructure developments.
Offering high capacity and performance, the 38-tonne payload RA40 machine delivers cost-effective productivity in the most challenging off-road conditions, whilst the 28-tonne RA30 articulated hauler, with its new EP320 transmission and true independent front suspension as standard, offers refined performance, superior comfort, and longer oil maintenance intervals for operators.
Since becoming part of the Volvo Group in 2014, Rokbak have embarked on a journey of continuous evolution and transformation in all facets of the business, from sustainability and safety to professional development and product design.
‘A big part of Rokbak’s DNA is continuous innovation and improvement in collaboration with our customers, partners, and, of course, the Volvo Group,’ said Mr Douglas. ‘Over the last eight years, our articulated haulers have been progressively updated with major advancements in emissions technology, transmission/traction control systems, and serviceability, making them even smarter, more efficient, and easier to operate.’
In Europe, both the RA30 and RA40 feature the latest EU Stage V emissions-compliant engine, boasting up to a 7% improvement in fuel efficiency compared with older Stage IV engines. And to provide added value to Rokbak’s customer base, the haulers are equipped with the company’s Haul Track telematics system, which gives fleet managers and business owners a digital platform to monitor operational data (eg fuel consumption, engine speed, idle time, system fault code alerts etc) for maximum plant uptime and greater productivity.
With quarry operators and aggregate suppliers under constant pressure to optimize the efficiency of their haul cycles, nothing is more important than maximizing equipment uptime and delivering optimum performance at the lowest cost per tonne. Keen to show off their latest articulated hauler improvements and technologies in the quarrying, construction, and heavy equipment sectors, Rokbak took the opportunity to exhibit at this year’s Hillhead exhibition.
‘We’re finding most of our customers are looking at the bigger picture when it comes to site efficiency and safety, machine performance, and reducing fuel usage and emissions, which leads to environmental benefits and lower running costs,’ commented Mr Douglas.
‘Hillhead 2022 was the perfect showcase event for bringing dealers and customers up to speed with our latest product improvements and technological features, as well as showing visitors how the RA30 and RA40 machines can reduce downtime, boost productivity, and deliver lower total cost of ownership.
‘We’re currently seeing huge demand for our articulated haulers and one of the key messages we wanted to convey at the show was that we are continuously evolving our range of products to give our customers significant improvements in functionality, design, operator comfort, and maintenance.’
Competent workforce
Over the past few years, the company has invested not only in facilities at its Motherwell manufacturing plant, but also in the continuing professional development (CPD) of its people. With an ageing and predominantly male workforce, and the prospect of large numbers of workers leaving the construction and quarrying sectors in the UK through retirement, there is now growing pressure to attract younger employees from more diverse backgrounds.
Rokbak are one of several OEMs in the heavy equipment industry to have developed a wide-ranging skills strategy that allows their current workforce to benefit and develop professionally. Confronting recruitment challenges head-on, the company is also using apprenticeship schemes to bring in new blood.
‘One of my proudest achievements as managing director of Rokbak is our strong track record of bringing apprentices through our business, nurturing fresh talent and, ultimately, helping them to achieve their career goals,’ said Mr Douglas. ‘Each year we take on a significant number of new apprentices, who typically go on to enjoy fruitful careers in manufacturing, engineering, and sales roles within the company.
‘Since the launch of our apprenticeship programme in 2011, we have taken on a total of nearly 90 apprentices, which demonstrates our strong commitment to get young people to pursue careers in the construction, engineering, and manufacturing professions. For me, there is no greater satisfaction than training the next generation of manufacturers, engineers, and business specialists – and creating a lasting skills legacy that will hopefully shape future industry leaders.’
As well as delivering Rokbak’s apprenticeship ambitions, Mr Douglas is also a strong advocate of continuing personal and professional development. He believes everyone at Rokbak should be given an opportunity to develop new skills and build on existing experience and knowledge.
‘As clichéd as it may sound, employees are our greatest asset. They bring to life everything that Rokbak is all about,’ explained Mr Douglas. ‘As a business invested in staff retention and the next generation, we are always encouraging our people to be more than they are and to actively participate in continuing professional development. Whether it’s gaining formal qualifications or accessing more specialist training and development programmes – undertaking CPD is a step in the right direction towards developing a highly skilled and competent workforce for the next phase of Rokbak’s growth.’
The company’s investment in building a workforce with future-proof skills, knowledge, and competencies – not to mention a people-centred culture that it has successfully embedded over the years – is a clear indication of the business’s commitment to further improve its safety standards.
Earlier this year, Rokbak received a RoSPA Gold Health and Safety Award in recognition of their continual commitment to employee health, safety, and well-being. It was the company’s second successive Gold Award – the previous one being received last year, when it was still known as Terex Trucks, following on from four successive years of Silver Awards.
‘Health and safety has always been a top priority for us,’ said Mr Douglas. ‘We’ve adopted a rigorous ‘zero-harm’ approach to workplace safety in every area of our Motherwell manufacturing site, from the shop floor and warehousing to the office facilities and transport/logistics operation.
‘Achieving Zero Harm is a challenge for all of us in the industry and delivering health and safety best practice should be second nature for any organization or business. Rokbak have never stopped learning and we will continue to work with our stakeholders, who have been an integral part of our success, assisting us in implementing innovative change and sharing our vision for all-round safer working practices.’
Seeking sustainability
In recent years, Rokbak have made considerable progress to embed sustainability across their operations – making significant reductions in carbon emissions, as well as energy and material use, at their Motherwell plant, with the full support of parent company Volvo Group.
A first major step towards reducing carbon emissions came in 2019 when the company’s manufacturing site shifted to 100% renewable electricity, and it is now operating as part of the Science Based Targets initiative (SBTi) to achieve net-zero value chain emissions by 2050 (at the latest), with a 50% reduction in emissions from site operations by 2030 and 30% from products in the same period.
The target of net-zero value chain greenhouse gas emissions by 2050 is a united commitment for the Volvo Group across all their business areas. Achieving carbon neutrality solely through operational changes is a tall order, but Mr Douglas believes there has never been a better time for the Scottish manufacturer to make the energy transition than now and reach closer to its net-zero sustainability targets.
‘Under the ownership of the Volvo Group, millions of pounds have been invested in improving our products, developing our people, expanding our global distribution network, and modernizing our factory processes and facilities in Motherwell,’ said Mr Douglas. ‘This is an important evolution of Rokbak’s long-term strategy, and with the UK Government’s commitment to reach net-zero by 2050, it’s crucial we support the adoption of alternative fuels and the development of new, climate-friendly technologies, so that we can move to a cleaner, greener future.
‘Volvo’s investment in reducing our carbon footprint and energy consumption in Motherwell is also a big statement to the global heavy mobile equipment sector about our commitment to building a better tomorrow. It makes good business sense for us and our customers because energy-efficient products and solutions mean significant savings for plant operators and, at the same time, a maximum return on investment, improved sustainability credentials, and better readiness for future legislation.’
Continued growth
With global articulated hauler sales increasing and the company enjoying its biggest ever order book, Mr Douglas has every reason to be optimistic about Rokbak’s growth, development, and vision for the future. While the UK and Ireland remain Rokbak’s home markets, the company has made great inroads into the booming North American market – a region that currently accounts for 50% of the total worldwide sales of articulated haulers.
‘Driven by a huge infrastructure spend and surge in housing demand in the US, the highest potential for achieving growth at present is North America,’ said Mr Douglas. ‘Europe and the UK – which is the second biggest market for articulated haulers, thanks to major projects such as HS2 – also form a significant part of our global expansion strategy over the next few years.
‘Although the global demand for articulated haulers has plateaued in recent months, market activity continues to be buoyant with total worldwide sales of haulers expected to be as high as 8,800 units for 2022. As we continue to see strong demand for our rugged and reliable RA30 and RA40, we’ve tapped into new markets such as Hong Kong, and strengthened our market share in traditional, high-potential regions, including Southern Africa and Indonesia.’
Despite the challenges presented by the Covid pandemic, Brexit, the energy crisis, and constraints to the wider construction supply chain, Rokbak have maintained their commitment to drive growth, innovation, and sustainability, and to develop and supply some of the most advanced, productive, safest, and environmentally friendly haulers to the global heavy equipment sector.
By heavily investing in research and development, and continuously developing their products and technologies, not to mention the £35 million-plus worth of improvements already spent at the Motherwell site to transition to more environmentally sustainable operations, Rokbak have never been better positioned to address their customers’ changing needs and to meet the complexity and challenges that lie ahead.
Mr Douglas concluded: ‘We are all proud to be part of one of the most forward-thinking and environmentally driven multinational companies in the world. Rokbak will continue to embrace new technologies and sustainable change, pushing the boundaries of innovation, safety, quality, and environmental performance.
‘The last year or so has been an incredible journey for everyone at Rokbak – from rebranding the business and meeting the evolving needs and priorities of our customers, to gaining an even stronger foothold in some of our well-established export markets. This could not have been achieved without the confidence our customers, dealers, and partners have instilled in us, the support of Volvo Group and Volvo Construction Equipment, and the amazing dedication of employees and my colleagues at Rokbak.
‘Two things have really stood out for me during this period – a fantastic team and supportive stakeholders. We are fortunate to have both. A lot of work remains to be done and much potential remains untapped, and my focus is to continue building on the company’s great legacy, strong hauling heritage, and technological advancements.
‘With the continued support of a great team and our shareholders, Rokbak will evolve again and grow – expanding its global footprint, further developing its product offering, and increasing its profitability. These are very exciting times for the business, and I look forward to being a part of it all.’
Change today for a better tomorrow
QM spoke to Jacqueline Reid, global director – marketing, communications, and product management at Rokbak, and Johncraig Savage, head of operations at Rokbak, about the articulated hauler manufacturer’s road to zero landfill and carbon neutrality
Highlighting their commitment to hauler reliability, power, and enhanced environmental performance, Rokbak opted to showcase four machines at Hillhead 2022, which gave visitors plenty of opportunities to get up close to the articulated haulers, see them in action, and speak to product experts.
On the company’s Solid as a Rokbak-themed stand was an RA40 machine, whilst an RA30 unit was displayed on the Molson Group stand, Rokbak’s sole UK dealer. In the Quarry Face Demonstration area of the showground, a Rokbak RA40 hauler was put through its paces to show visitors its real-world capabilities and the work it can do in a live quarry environment. Elsewhere, another Rokbak hauler was chosen to demonstrate third-party technology.
This year’s Hillhead exhibition was also used as a platform to share the company’s rebranded name, slogan, and fresh new brand identity with visitors, customers, and partners. ‘The feedback from our dealers, customers, and market has been extremely positive,’ said Ms Reid.
‘Many of the visitors at Hillhead had caught a first real glimpse of the well-received sand livery and colours on the RA40 and RA30 haulers. So, it was vitally important to be at a leading industry trade show such as Hillhead, especially as it is the first time Volvo Group has ever launched a new brand in the heavy equipment sector.
‘At Rokbak, we are evolving at a rapid pace to ensure we’re offering our customers the very best products and most cost-effective solutions. The rebrand [from last autumn] will support the continual evolution journey of the business, with an agenda to transform the earthmoving sector and provide innovative value-added products, services, and propositions for our customers. The Rokbak brand name encapsulates everything we stand for and our strong ambitions to drive the company forward and become one of the world’s leading construction equipment manufacturers.’
All the Rokbak articulated haulers are manufactured at Volvo Group’s Motherwell factory in Scotland, where the Swedish company has invested millions of pounds in improving products and modernizing facilities over the last few years.
Manufacturing is one of the largest single emitters of greenhouse gases in Europe.
Recognizing the need for action and the economic and political pressure to tackle the problem, many industrial companies are implementing sustainability initiatives to decarbonize not only their products’ carbon footprint, but also their production and logistics operation.
Volvo Group, for example, have set an industry-leading target to reach net-zero value chain greenhouse gas emissions by 2050, including cutting emissions by half across their own operations, facilities, and manufacturing processes, and achieving a 30% reduction in the use of their products as early as 2030.
For Rokbak, the journey to creating a ‘green factory’ fit for the future is well under way in Motherwell. ‘As a world leading environmentally responsible manufacturer, it gives us an opportunity to lead the charge in demonstrating best practice in reducing carbon emissions, improving operational efficiency, and cutting down production costs,’ said Mr Savage.
‘We want our Motherwell plant to be a zero-emissions, carbon-neutral production site. We’ve already adopted simple measures to reduce its carbon footprint but, more importantly, we’ve taken a consistent and co-ordinated approach to cutting our overall carbon emissions and cost base right across the Motherwell factory.’
Some of the energy-efficient solutions have included the installation of 54 submeters across the site to give greater visibility over electricity use and empower teams to drive their own efficiencies. They give Rokbak employees an insight into where electricity is used and how targeted action can be taken towards reducing unnecessary consumption.
The next big step for Motherwell is to tackle natural gas consumption, which is primarily used for space heating. The administration building and some of the other annexes have already moved over from gas to electric heating/cooling, whilst other areas are being switched to electric-powered systems. That will leave the factory and the warehouse, which will also require new roofing and insulated cladding.
Whilst this long-term sustainability project is in development, the plant has implemented two key measures to reduce gas use in the factory and warehouse. First, it has been compartmentalized into smaller working areas that are easier to heat, partitioned off by fire-retardant curtains. This contrasts with the previous layout, which was a large, wide-open workspace.
Elsewhere, the factory’s use of large, corrugated metal roller doors has been replaced. The previous doors had to be manually winched up, so they were often left fully or partially open, allowing heat to escape. The new roller doors – which are equipped with motion sensors – can automatically move up and down, thereby reducing heat loss.
The Motherwell plant has also started to replace its fork-lift truck fleet with new electric models, with the aim of saving around 75 tonnes of CO2 per year. The phased roll-out of the zero-emissions fork-lifts is expected to be completed in the third quarter of 2023.
When it comes to reducing material waste, the site is now practically landfill free and will soon apply for Volvo Group certification for demonstrating that at least 95% of waste is diverted from landfill. All steel and wood, for example, are recycled, whilst food waste is composted.
Rokbak are also actively working with their suppliers to reduce the number of materials consumed in the first place, such as requesting to receive goods on reusable stillages instead of wooden pallets and asking oils/lubricants to be delivered in larger containers that can be refilled or repurposed.
Since joining Rokbak in 2017, Mr Savage has seen the Volvo Group invest heavily in the Motherwell facility, including a multi-million-pound investment in two state-of-the-art robotic welding systems within the shop floor of the factory.
‘Any improvements to operations and equipment made to the site are likely to have long-term cost-savings and efficiency benefits for the business,’ said Mr Savage. ‘The robot welders, in particular, have strengthened our automation and manufacturing capabilities, increasing throughput efficiency and improving employee safety from what was a very labour-intensive process.’
Since September 2021, Ms Reid has seen a huge demand for Rokbak articulated haulers and believes equipment sales will continue throughout 2023. ‘As we move through the last quarter of the year and into 2023, we will continue to recruit for a variety of disciplines, including manufacturing, design, sales, and after-sales support,’ she commented.
‘We are very optimistic about the huge potential the global construction equipment market has to offer, and I am confident that, with the substantial investment and much-needed improvements made at Motherwell, the company is well placed to capitalize on the strong demand for its class-leading haulers.’
Subscribe to Quarry Management, the monthly journal for the mineral products industry, to read articles before they appear on Agg-Net.com