New Cats Unveiled
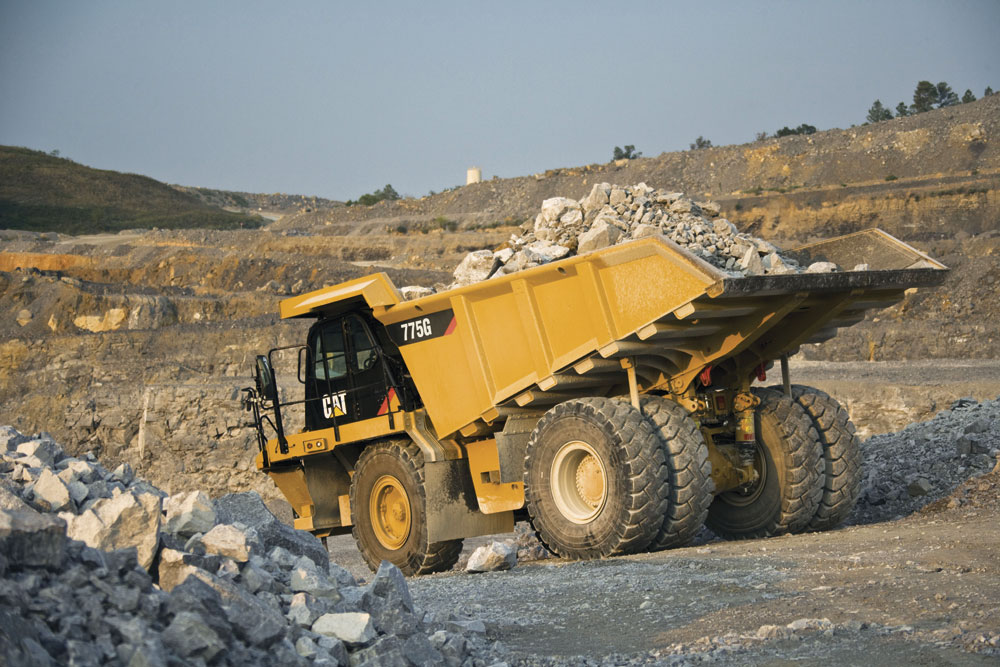
Caterpillar introduce G-Series dumptrucks, E-Series excavators, K-Series wheel loaders and the D8T dozer
Caterpillar have unveiled an array of new and upcoming earthmoving machines, including two G-Series off-highway rigid dumptrucks, four E-Series hydraulic excavators, three K-Series wheel loaders and the D8T track-type tractor dozer. The design of all the new machines has been driven by feedback from customers, with a focus on five key areas: quality; operator comfort; fuel consumption; productivity; and safety. The result is a line up of new models that offer enhanced operator safety, reduced noise levels, improved performance, lower fuel consumption and greater efficiency.
G-Series rigid dumptrucks
The new Cat 773G and 775G off-highway trucks went into production earlier this year following 24,000h of field validation trials in both hot and cold climates. The machines have been designed to meet US EPA Tier 4 Final emissions standards while delivering improved levels of performance. Thanks to a combination of new drivetrain strategies and a 5% power increase over the previous F-series models, the 54- and 64-tonne payload class trucks can hold a higher gear when climbing 10% grades in most applications. A new and simplified range of body options and liners is also available for the G-Series trucks, including a Quarry body for the 775G.
A number of new components and control changes help boost efficiency. Key among these is the next generation of Caterpillar transmission control, called the Advanced Productivity Electronic Control System (APECS), which is designed to enhance productivity, fuel efficiency, drivetrain durability and machine control. For example, to balance fuel savings and production, two different economy shift mode selections allow the customer to adapt performance to the needs of the task in hand.
Advanced control systems also integrate the optional engine compression brake with automatic retarder control to allow faster downhill travel and reduced cycle times – without increased fuel consumption.
To meet Tier 4 Final emissions regulations in the US, the 773G and 775G’s Cat C27 ACERT engine includes the Caterpillar’s NOx-reduction system and diesel oxidation catalyst. In the EU and other areas, the engines will be configured to meet EU Stage II emissions standards.
To help the operator work safely and efficiently, the trucks feature a new cab with a centrally positioned seat, which provides more space for the operator and allows access and egress from either side. The access system is equipped with stairs illuminated by LED lights.
In addition, the new cab provides a 4dB(A) reduction in noise (equivalent to a 50% reduction at the operator’s station) and features fully automatic temperature control. An enhanced cab pre-cleaner is available as an option to further increase air quality and extend the life of the HVAC components.
For easy access by maintenance technicians, both the 773G and 775G have a ground-level electrical service centre and diagnostics port on the front bumper. Likewise, fluid level indication, fluid fill ports and fluid filters are grouped for fast and efficient servicing. Filter service intervals for the steering, hoist/brake and transmission/torque converter have been increased from 500h to 1,000h.
In addition, the Cat VIMS 3G data-collection system, which allows the customer to access prognostic and diagnostic information, is now fitted as standard.
E-Series excavators
Operating in the 25–30-tonne, 29–32-tonne, 36–39-tonne and 48–53-tonne weight classes, respectively, the new Cat 324E, 329E, 336E and 349E hydraulic excavators all use Cat ACERT engine technology to meet EU Stage IIIB emissions standards while offering greater horsepower, improved productivity and up to a 5% reduction in fuel consumption over their predecessors, the 324D, 329D, 336D and 345D.
Both the 324E and 329E are powered by the Cat C7.1 engine, offering 145kW and 173kW of power, respectively, while the 336E is powered by a 236kW C9.3 engine, and the 349E by a 317kW C13 unit.
Performance enhancements for the 329E model include 13% more net horsepower, reduced fuel consumption and 5% more lifting power. These improvements, coupled with hydraulic refinements, new amenities in the operator’s station and new safety and serviceability features, help ensure high productivity and lower operating costs.
The 329E’s diesel particulate filter, part of its emissions-control system, can be regenerated to remove accumulated particulate matter in either automatic or manual mode. The automatic mode initiates the regeneration process when conditions for cleaning are optimal. This process requires no operator intervention and does not interrupt work cycles. In manual mode, regeneration is initiated by the operator at the touch of a button, allowing the cleaning process to proceed with regard to application-specific circumstances.
The 329E reduces fuel consumption through a combination of features, including: electronic adjustment of engine operation to precisely meet load demand; constant engine speed (electronically controlled); a variable-speed cooling fan that runs only when required; ‘one-touch’ idle control for reducing engine speed to low idle; and an engine-shutdown system that stops the engine after it has idled for a pre-set time.
As well as a powerful two-pump, pilot-operated implement hydraulic system that delivers both fast response and fuel savings, a new main-control valve enhances oil-flow efficiency, while a new electric regeneration valve in the boom circuit and a hydraulic type in the digging-arm circuit minimize hydraulic flow for further fuel savings.
The machine’s robust, grease-lubricated undercarriage features a press-fit master link (as opposed to a slip-fit type) to improve durability, while a new three-piece guiding guard (optional) assists in maintaining track alignment.
A selection of booms and digging arms allows the 329E to be tailored to specific applications. Choices include three booms (reach, super-long reach and mass-excavation) and four appropriately sized digging sticks, all of which use castings and forgings in high-stress areas.
Cat New Generation buckets for the E-Series range feature new geometry, with the leading-edge pushed forward for more efficient filling, higher production and greater control. The buckets also feature improved wear resistance for corners and side cutters.
In-cab sound levels for the 329E have been reduced by 4dB(A), and the new LCD monitor is 40% larger, has higher resolution, and presents a simpler, easy-to-use menu, as well as serving as a display for the rear-view camera system.
Seat choices include new heated and air-cooled options, and the climate-control system incorporates new outlets with positive filtration. Full adjustment of the operating consoles and dual 12-volt power outlets further enhance the operator’s environment.
The optional Cat Grade Control system for depth and slope uses internal front linkage sensors to provide real-time bucket-tip position, resulting in less grade checking, fewer cycles to attain grade, and reduced fuel consumption. The system can be expanded to full three-dimensional capability by adding Cat AccuGrade technology.
Visibility from the 329E’s cab is enhanced by powerful working lights (standard halogen or high-intensity-discharge). For operator safety, a falling-object-guard structure (FOGS) can be bolted directly to the ROPS cab, while anti-skid surfaces together with new ISO-compliant hand rails help prevent slips.
Wide service doors and a new hood design provide easy access to the engine and cooling compartments for maintenance and service. The cooling package is easy to clean, featuring a charge-air cooler and air-conditioning condenser that tilt out from the side-by-side hydraulic-oil cooler and radiator. Fuel and engine-oil filters are accessible from ground level, and Quick-Evac ports allow efficient changing of engine and hydraulic oils.
K-Series wheel loaders
Like the E-Series excavators, the new Cat 966K, 972K and 980K wheel loaders feature new designs and engines certified to meet Stage IIIB regulations in the EU. Designed to offer high productivity and excellent fuel efficiency, the loaders have a new operator station, new electro-hydraulic steering with either joystick or steering-wheel control, Performance Series buckets and a more efficient drive train.
The 966K and the 972K are designed to accommodate buckets ranging in capacity from 2.50 to 9.90m3 and both are powered by the new Cat C9.3 ACERT engine, which delivers peak net power of 201kW and 217kW, respectively, at 1,800 rev/min. The 980K accommodates buckets from 4.00 to 12.20m3 and is equipped with the new Cat C13 ACERT engine, which offers peak net power of 274kW at 1,600 rev/min.
Caterpillar’s new Performance Series buckets come standard on the K-Series machines. Developed especially for production loading, these buckets are designed to deliver faster fill times, greater fill factors and better material retention, reducing cycle time and improving productivity and fuel efficiency.
For operator comfort and safety, all three K-Series machines feature new steps that are less steeply inclined than on their H-Series predecessors, to provide easier access to the cab. A wider door opening, well-placed grab bars and a new front-hinged door that can be opened and closed while seated also allow for easy entry and exit.
A streamlined four-post ROPS design and a new operator position that has been moved slightly forward provide enhanced visibility to the front and sides, while a standard rear-view camera with large colour monitor enhances visibility to the back of the machine. Two rear work lights are located in the rear grille and can be activated to illuminate the area behind the machine in low-light conditions, while four halogen work lights illuminate the work area.
The three models come as standard with a new seat-mounted, low-effort, electro-hydraulic joystick steering system, allowing the operator to work in the most ergonomically neutral position. The joystick steering system has an exclusive force-feedback feature that automatically increases joystick effort as ground speed increases. This improves steering control and comfort, especially at higher speeds.
An optional electro-hydraulic steering wheel system will also be available, and this too will sense ground speed and automatically adjust steering effort to improve controllability and comfort at higher speeds. Full machine articulation will be achieved by rotating the wheel through approximately 330 degrees. Outside the cab, a window washing platform with full-coverage grab bar around the roof cap is now fitted as standard.
Improved hydraulics include a new load-sensing system that automatically directs the right amount of flow to the implements based on operating conditions. As a result, fuel consumption is reduced because the hydraulic pumps only produce the required flow. Heat generation is also reduced, which decreases cooling requirements and average fan speed, thereby resulting in additional fuel savings.
The new hydraulic system also allows parallel flow to the lift, tilt and auxiliary hydraulics, so the functions can be performed simultaneously. In bucket loading, for example, the operator can lift and tilt at the same time for faster, smoother, more fuel-efficient loading. On the 980K, the lift and tilt forces have been increased by 25% and 16%, respectively, reducing bucket loading times and increasing fill factors.
Drivetrain components on all three machines have been designed to optimize productivity and fuel efficiency. A new torque converter that increases rimpull in all gears boosts performance, especially on grades, and all three loaders have new transmission-shift logic for downshifting into first gear, based on the machine’s torque requirements instead of ground speed, thus allowing operators to use the automatic transmission mode from first through to fourth gears. The result is faster acceleration, better ramp-climbing performance and improved shift quality. To further enhance productivity, ride control is standard on the new loaders.
For ease of maintenance the K-Series machines retain the one-piece tilting hood first introduced on G-Series models. However, the rear portion of the hood now incorporates a clamshell design that allows quick access to the engine-oil dipstick, oil fill, fuel fill and cooler cores for cleaning. Two ground-level service centres are provided for hydraulic and electrical components.
D8T dozer
The new Cat D8T dozer builds upon the reputation of its predecessors, retaining key features such as differential steering for infinitely variable turning control with full power to both tracks and a suspended undercarriage for optimum traction in uneven terrain, but with additional new performance-enhancing and cost-reducing features, including an enhanced auto-shift system that can reduce fuel consumption by as much as 6% in certain applications.
The machine is powered by a 2321kW Cat C15 ACERT engine, which meets EU Stage IIIB emissions standards, and features an all-new cooling system that incorporates a single-unit coolant radiator, hydraulic-oil cooler and air-to-air after-cooler positioned in an easily serviced single-plane design. Complementing the new cooling system is a ROPS-mounted air-conditioning condenser that is fully protected for use in high-debris applications.
Ground-level service centres provide access to the battery disconnect and engine shutdown switches as well as optional lighting switches, while new lighting packages, steps and grab bars provide safer machine access and egress.
The D8T comes equipped with integrated harnesses that allow for easy dealer installation of an AccuGrade machine control and guidance system, either when the machine is purchased or at a later date as business requirements change.
The machine also is available with a new Caterpillar grade-control option – a factory-integrated machine control and guidance system designed to guide the blade to the desired design contours and enhance overall machine productivity with features such as AutoCarry, Automatic Ripper Control, Auto Blade Assist and Grade Protection. The chassis-mounted system moves the traditional blade-edge positioning technology to the top of the cab, thereby helping to reduce receiver damage, enhancing visibility for the operator and eliminating receiver/antennae, masts and cables.
The D8T also offers optional key-off regeneration, as well as a delayed engine shutdown timer and an engine idle shutdown timer.