Automating the Future of Quarry Management
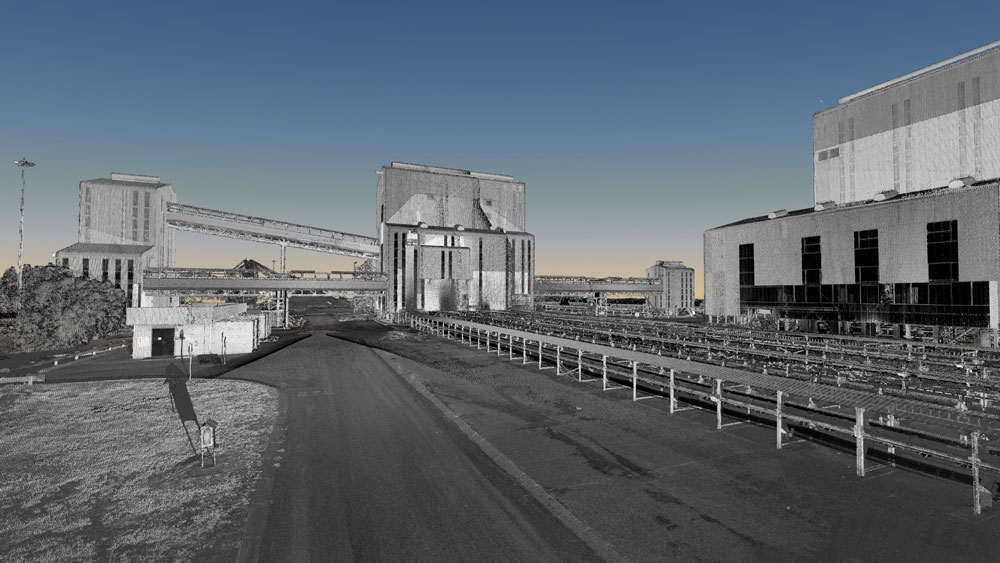
First published in the March 2017 issue of Quarry Management
The extractive industry is as safe as it has ever been, yet with the global construction market set to grow by around 70% in the next decade, and a distinct skills shortage in the sector, quarry operators will be under increasing pressure to deliver greater levels of efficiency whilst continuing to improve safety records even further. Here, Chris Firth, director of monitoring solutions at 3D Laser Mapping, discusses how technology can be applied to help achieve the zero harm target, whilst improving the productivity of operations.
The advent of rapid urbanization is starting to place a strain on the industries that support growth in the quarry sector. The engineering, construction and utility sectors are seeing a boom in many countries across the globe, which in turn has seen an increase in demand for raw materials and natural resources. With many countries reporting the highest growth rate in the mining and quarrying sectors in over a decade, and with a shortage of skilled workers, operational efficiency has never been more important.
The Internet of Things (IoT) is changing the way we live and work. From intelligent household appliances that save you time and money, to the introduction of self-drive vehicles, the digital revolution has started to gain momentum at a great pace. With many other sectors, including governments and authorities, committing to ‘digital by default’ standards, how can the extractive industry embrace similar advancements in technology to enhance safety and productivity?
Safety first
The safety implications in a quarry closely resemble those of a mine, both opencast and underground. With workers continually exposed to potentially hazardous conditions in an ever-changing environment, there is a great level of responsibility placed on operators to ensure that everything is being done to protect people from harm. Over the last 15 years both mining and quarrying operations have improved their safety records dramatically. Programmes such as the Quarries National Joint Advisory Committee’s (QNJAC) ‘Target Zero’ have helped decrease reportable accidents that resulted in fatal or serious injury by more than 80%.
Mining is facing a new, safer era, thanks in part to the adoption of automation technology. From Komatsu’s Autonomous Haulage System, currently being used in Rio Tinto’s ‘Mine of the Future’, to connected sensors that monitor slope stability remotely; mining operations are embracing the IoT and steadily incorporating more ‘connected’ systems in to day-to-day operations. The automated collection and analysis of data is helping to provide critical business information that would previously have taken years to collect and months to process. Companies are reaping the benefits in terms of increased efficiency and improved safety for workers.
One of the greatest risks in a quarry or mining environment is the potential for rockfall or slope failure. This can result in operations grinding to a halt, or worse, human injury and death. Slope and bench stability assessments were originally carried out manually, applying methods that attempt to calculate the behaviour of the material being extracted based on geological information and site characteristics. The introduction of laser scanners in the last half of the century helped to provide more accurate assessments on a more regular basis, with less time being spent taking measurements manually, and thus less risk to workers. More recent advancements in laser technology have helped to improve surveying techniques even further.
Surveyors have used electronic measurement systems for around 50 years, until recently in the form of total stations. These use infrared and prisms to calculate distance based on the parameter of how long it takes for the beam to return to the source. LiDAR (Light Detection and Ranging) systems work in a similar way, using lasers to create more in-depth three-dimensional models of the surrounding environment. As light moves at a constant and known speed, it is possible to calculate distance quickly and accurately. Information from an integrated GPS system and an Inertial Measurement Unit (IMU) then allows for the recording of the precise location of the sensor at the time the measurement is taken, resulting in a collection of millions of data points which create a 3D ‘point cloud’.
In the last five years, LiDAR systems have become smaller, portable and more affordable, making the safety and efficiency benefits more accessible to smaller operations. As with total stations, traditional terrestrial laser scanners only have a limited range, and rely on repeated set-ups to collect sufficient data to produce a detailed digital terrain model. Mobile LiDAR systems are now changing the face of surveying by making remote capture possible in almost any environment, with the ability to capture large amounts of data whilst moving.
Mobile Laser Scanners (MLS), such as ROBIN, allow for complete digital surface models to be created in one set-up. They can be attached to land vehicles, mounted on to UAVs (unmanned aerial vehicles) or helicopters, or even worn on a backpack, meaning data is collected around 80% faster than previously possible using a terrestrial scanner or total station. Vehicle or airborne systems also have the clear advantage of remote capture, meaning that operators are out of harm’s way while the scan is carried out. The resulting data, or point cloud, provide millimetre-accurate visualizations which can then be used to calculate slopes and gradients, widths and depths, and clearances for machinery and vehicles.
Geotechnical assessments carried out by mobile mapping systems are extremely accurate and provide critical business intelligence to any operation. From the initial planning stages of a quarry, all the way through its lifecycle, this permits the historic documentation of the site, at regular intervals, assisting with compliance and legislative reporting requirements. Once the initial assessment has been carried out, a detailed quarry development plan can be created. This includes 3D renders of the site and surrounding areas, which can also be of help when communicating plans for new works to local communities in exact terms, rather than relying on CAD drawings or outline OS maps.
One of the greatest benefits of using LiDAR in a quarry or mining environment is the ability to scan through mesh and vegetation. This allows surveying teams to capture a complete picture of the site, including areas that have already been identified as unstable, or sites that are yet to be excavated. Once collected, the generated point cloud has many potential uses, from providing accurate calculations of stockpile volumes, to assisting with environmental impact assessments. Software such as SiteMonitor 4D can also use this collected data to analyse changes in the landscape over a period of time, highlighting rockfall patterns and areas of deformation. Repeated scans can be assessed to help identify at risk areas and provide enough time for potential failure mechanisms to be put in place. This can help to protect workers and prevent site closures in the event of an incident.
Time is money
Mogalakwena in South Africa is the largest open-pit platinum mine in the world. As part of their business improvement initiatives, operators Anglo American wanted to raise productivity and reduce costs whilst still making improvements in their safety record. Similar to SiteMonitor 4D, SiteMonitorSV uses time-series laser measurements to provide business-critical information in a mining or quarrying setting. Anglo American invested in five static scanners to monitor the site’s north pit, with the aim of using the resulting data to reconcile volumes. This helped them to maximize the value delivered from the asset. Fully automated, SiteMonitorSV acts as an inventory management system, which is capable of providing real-time reconciliations for stockpiles and volumes, giving operators such as Anglo American the ability to plan and report with more accuracy and efficiently than ever before.
Productivity at Mogalakwena has increased by 33% in the past two years since the introduction of autonomous systems such as SiteMonitorSV. Anglo American also achieved significant results with their intensified safety programme, which focused on decreasing workers exposure to hazardous conditions. Tasks such as stockpile management were automated, with the lost-time injury frequency rate dropping from 0.68 in 2013 to 0.12 per 200,000 hours worked in 2014.
The connected workforce
Forestry is one industry that is reaping the benefits of applying the IoT in an industrial setting. ‘Precision forestry’ is defined as being the application of intelligent, information-based systems that use technology to make data-driven decisions. Vehicle or aircraft mounted scanners are assisting with the collection of data to enable evaluations to be made remotely. Intelligence is gathered which helps to make planting, harvesting and stock management easier and more efficient.
Facing similar skills shortages to the quarrying sector, both precision agriculture and precision forestry are looking to advancements in technology as a way to attract more skilled workers into the field. Many school leavers may not immediately look towards a career in an industrial setting, however, applying technology to these critical, growing sectors can introduce a new range of future skills. This helps ensure that innovation can be applied to environments not typically predisposed to technological advancement.
Another industry making use of LiDAR technology is archaeology, with scans being performed of ancient sites to assist in the discovery and protection of our heritage. With ancient quarries having been discovered in Cambodia, Egypt and Rome, LiDAR is not only helping to track the history of quarrying but also supporting the safety and sustainability of its future.
There is no doubt that the application of automation technology can help quarry operators to deliver greater levels of efficiency. The challenge lies in using these intelligent, connected systems to extract data which ensure that the industry’s growth is sustainable and, more importantly, that the environment is safe for its workers.
- Subscribe to Quarry Management, the monthly journal for the mineral products industry, to read articles before they appear on Agg-Net.com