Measure While Drilling
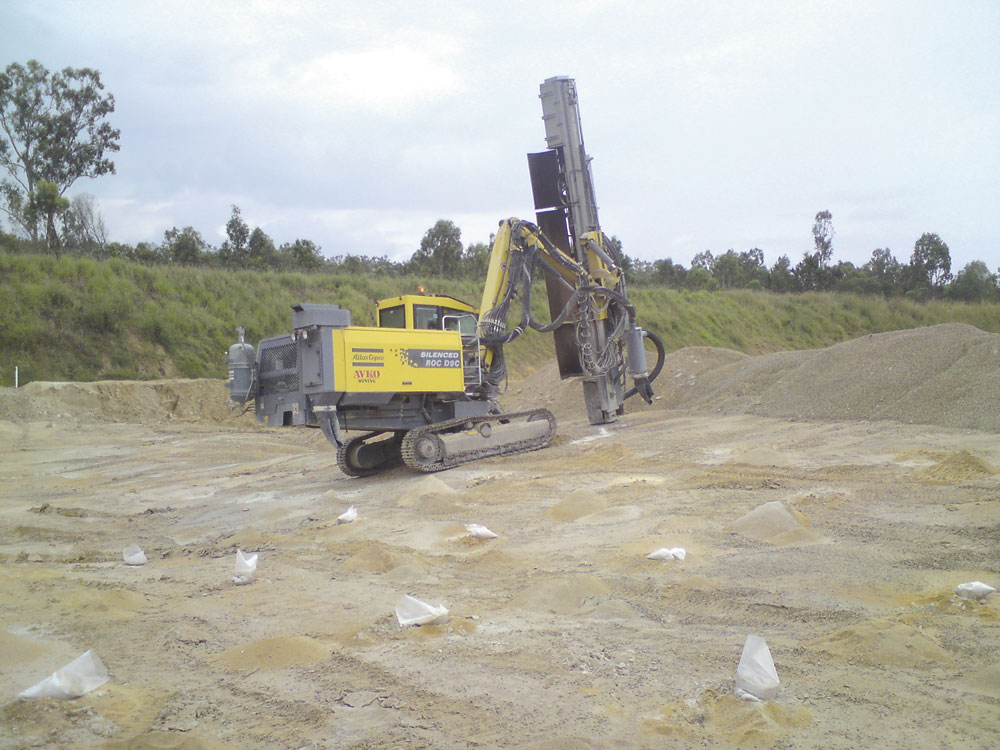
The optimization of drilling and blasting techniques can have far-reaching benefits for the quarrying industry. Alan Robertson of AVKO Quarry Consulting Group explained to Damian Christie how the Measure While Drilling (MWD) system can refine the drill and blast process in terms of time, money and productivity
AVKO Quarry Consulting Group, based in Brisbane, are a subsidiary of AVKO Mining, who are renowned for their underground and civil construction work, particularly in Western Australia but more recently on the east coast of Australia. The Quarry Consulting Group was formed in September 2008 and is headed by principal engineer Alan Robertson.
In their first 18 months, AVKO Consulting Group have been involved in several quarrying and civil construction projects, mainly in Queensland, assisting greenfield resource programmes to plan for drilling and blasting, primarily using Measure While Drilling (MWD) techniques.
MWD helps to determine accurate rock properties while measuring a number of drilling parameters, including penetration rates, rotation speed, fracture density and torque. The MWD data can then be used to calibrate a drill rig for a particular rock type and can also assist the blasting engineers with input into the blast design for achieving ideal fragmentation.
Measure While Drilling
In 2009, AVKO Quarry Consulting Group worked with several Queensland quarries, including Bungil Quarry, owned by the Roma Regional Council, and Boral’s Narangba and Coolum quarry operations in resource assessment and drilling for drill and blast operations. AVKO trialled the MWD approach in these quarries, drawing upon Atlas Copco’s ROC Manager software to interpret the MWD data to calculate the relative hardness of the rock and fracturing parameters, and providing Orica Quarry Services with full ‘in the hole’ geological data for its blast-design package.
‘MWD measures penetration rates, rotation speed, fracture density, torque and other drilling parameters,’ explained Mr Robertson. ‘We calibrate the machine for a particular rock type. When we are doing the resource assessment, we collect the 1m samples of the drill cuttings and have them checked by a geologist. We then refer to three logs – the driller’s log, the geologist’s log and the MWD log – to calibrate the rig for the site.
‘When we return to that site we have all the data on-board, based on those parameters, to read any rock type. For example, if we are going from a highly weathered granite to a moderately weathered granite to a freshly weathered granite and then into a dyke, we can actually pick up the changes in rock type. And if there were sediments above the granite, such as a sandstone, we could detect that. That is really important to blast design.’
According to Mr Robertson, the actual process of using data from drill logs is often ignored by the blast designer. ‘The lack of knowledge or wrong interpretation of the rock type and structures is a major issue in blast design. MWD gives the blast designer the full ‘in the hole’ geological data and, ideally, could be downloaded to the blast-design package,’ he said. ‘By having different persons carrying out the data-collection activity, such as the hole marking, drilling (drill logs) and bore tracking to measure hole angle and deviation, there is increased room for error in the blast design. MWD allows this to be done by the machine and the driller. By boretracking after each hole is drilled, the driller immediately gets an indication of his drilling accuracy rather than waiting until the whole shot is drilled out.’
Mr Robertson cited some recent work by the Quarry Consulting Group that he felt would have benefited from access to more accurate data. ‘In one recent job, it would have been nice to have given the blast designer the whole MWD data in a graphical form that could have made the actual blast work better than it did. The data may have been able to improve the blast, as we had some oversize at the top of the blast.
‘One of the issues, of course, is that if you don’t know the exact rock type you are drilling through, once you set your burden and spacing for the blast, the only parameter of change you have is your bulk density or explosive weight. A knowledge of the rock conditions in each hole will determine how you distribute the explosives in the hole, whether you air deck or whether you charge and stem and then double time.
‘MWD can help in making these decisions, especially if there is a weathered zone which varies significantly in depth over the shot – an assumption using an ‘average depth’ may result in not enough ‘oomph’ where the fresher rock is close to the surface. With MWD we have a full plot of which rock types are where so that we can change input into the blast designs.’
According to Mr Robertson, the upshot of MWD is that, when combined with other software, such as ROC Manager and Gemcom’s Surpac, the system could lead to an optimized drilling and blasting process. In turn, for the quarry operator, that could mean reduced crushing and screening costs, thanks to accurate drilling (including hole length and orientation) and recorded data on rock types and fractures for input into the quarry design model.
AVKO utilize a fleet of drill rigs spearheaded by Atlas Copco’s D9C ROC Silenced Smart Rig. The D9C Silenced Smart Rig’s silenced mast reduces noise by up to 10dB(A), compared with conventional drills, which allows it to work up to 1km closer to urban population centres than other unsilenced rigs. It also comes equipped with the capacity for MWD and features a Hole Navigation System (HNS) that allows automated hole drilling after initial set up. In addition, the D9C has an automatic feed alignment and automatic rod-adding system, which sets the feed to pre-defined angles and drills automatically to a given depth.
According to Mr Roberston, MWD has been very successful in Scandinavia, where there are 40 or 50 of these GPS-controlled rigs operating. ‘There are simple savings such as not having to mark out the shot. Basically, you bring the rig over the hole location you want to drill and move the feed beam until the co-ordinates and mast orientation match those for the hole design and off you go.’
Scope for future analysis
While AVKO do not have MWD data from Scandinavia to refer to as a benchmark, in 2009 the Quarry Consulting Group supported a research project by Rubik Ghosh, a University of Queensland undergraduate, to analyse MWD exploration data and the potential impact of MWD systems as a cost-saving component of the quarry drill and blast optimization process.
The study concluded that MWD data analysis could be used as an aid to the driller’s and the geologist’s logs for correlation (when identifying a change of hardness in the rock), and that incorporating MWD and bore tracking into current drilling and blasting practices would lead to fewer steps in the quarry to processing cycle.
The study also proposed further research avenues, including the development of a MWD interface link between available software, implementation of topographical surveying in current practices, optimum stemming material determination, fragmentation monitoring studies and blast-design modification studies.
REFERENCES
- GHOSH, R.: ‘Optimization of quarry drill and blast – The Measure While Drilling (MWD) approach’, University of Queensland, Brisbane, 2009 (unpublished).
This article first appeared in Australia’s Quarry magazine in February 2010 and is reprinted here, in edited form, by kind permission.