Details Matter: Optimizing blasting efficiency through precision engineering
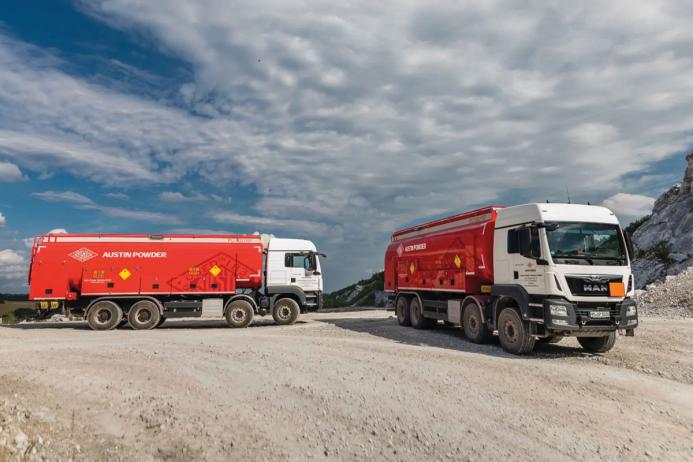
First published in the April 2025 issue of Quarry Management
By Ondrej Cermak, senior blasting manager, Austin Europe GmbH
Blasting is more than just breaking rock – it is about shaping the world responsibly and ensuring the safety and efficiency of every operation. Austin Powder are committed to using explosives in a way that enhances both performance and sustainability. The company’s approach integrates electronic blasting systems (EBS), high-quality explosives, and cutting-edge software, such as Paradigm, to optimize every step of the blasting process. By focusing on the finer details, Austin Powder are not only improving operational efficiency, but also upholding their commitment to safety, customer focus, and respect for the communities they serve.
The role of electronic detonators in fragmentation optimization
Non-electric detonators have long been a reliable choice for effective blasting, delivering consistent results across various applications. However, electronic detonators have taken precision to a new level, particularly in challenging geological conditions where timing adjustments are crucial. While all electronic detonators allow for variable delay configurations, E*STAR electronic detonators stand out by providing an unmatched level of control, ensuring that each charge is initiated at the optimal moment for the specific rock formation.
This level of precision translates directly into better fragmentation, with a more uniform particle-size distribution that enhances downstream processes such as crushing and milling. Well-structured muckpiles improve material flow, reducing the need for secondary breakage and increasing efficiency in loading and hauling operations. Additionally, controlled initiation helps to minimize back-break, preserving the integrity of highwalls and ensuring safer and more stable excavation conditions.
Field studies across quarries in the Czech Republic, Slovakia, Poland, and Austria confirm the advantages of switching to electronic initiation. The implementation of E*STAR electronic detonators resulted in a 15% reduction in oversized material, leading to a 22% increase in crusher throughput, demonstrating their capability to deliver both economic and operational benefits.
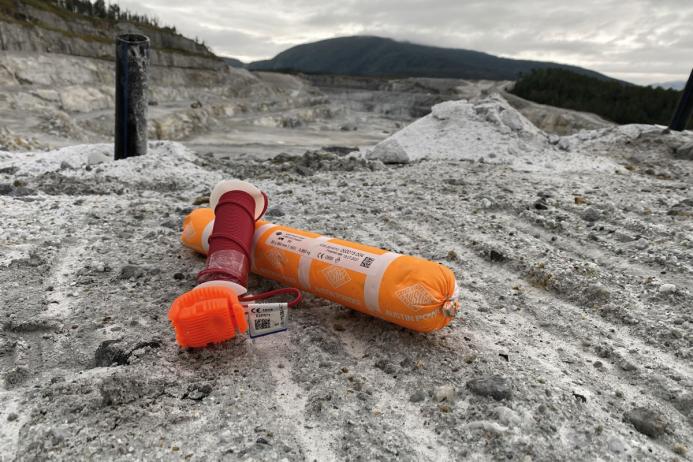
High-performance explosives: A key to success
Beyond timing precision, the choice of explosives plays a crucial role in achieving optimal blasting outcomes. Austin Powder’s Hydromite 70 bulk emulsion, in combination with APB boosters, has been extensively tested in field trials, demonstrating superior energy distribution throughout the rock mass. This ensures efficient breakage while maintaining control over blast dynamics. Additionally, Hydromite 70’s advanced formulation enhances safety by reducing the production of NOx emissions, making it a more environmentally responsible choice. The combination of high-energy performance and improved environmental compliance allows for safer and more effective blasting operations in a wide range of geological conditions.
Data-driven optimization with Paradigm software
While experience and careful planning are fundamental to successful blasting, Paradigm enhances optimization by providing precise control over every aspect of the process. This internally developed software allows tailored delay sequencing based on geological conditions, predictive simulations of blast outcomes, and detailed assessments of different charging scenarios.

Paradigm’s strength lies in its ability to integrate multiple interconnected modelling tools within a single platform, enabling comprehensive analysis of blasting parameters such as fragmentation, fly-rock, blast safety, energy distribution, muckpile formation, and overpressure. For example, Paradigm seamlessly combines 3D fragmentation analysis with geological data, using drone-based photogrammetry to capture detailed muckpile characteristics at multiple depths. This real-world calibration refines fragmentation models, ensuring predictive simulations align with actual results. By reducing variability and improving accuracy, Paradigm enables the selection of the optimal timing and charging scenario to achieve the best-possible blasting outcome.
Beyond fragmentation, the software’s vibration modelling, validated through extensive studies, such as the AGH research from Poland on predictive accuracy, has demonstrated its ability to match real-world vibration measurements with over 90% precision. This high correlation between predicted and actual results ensures that blasts remain compliant with seismic limits; indeed, over time the measured vibration levels actually decreased by 95%.
By leveraging Paradigm’s advanced capabilities to make data-driven decisions, Austin Powder ensure that every blast achieves maximum performance while maintaining the highest safety and environmental standards.
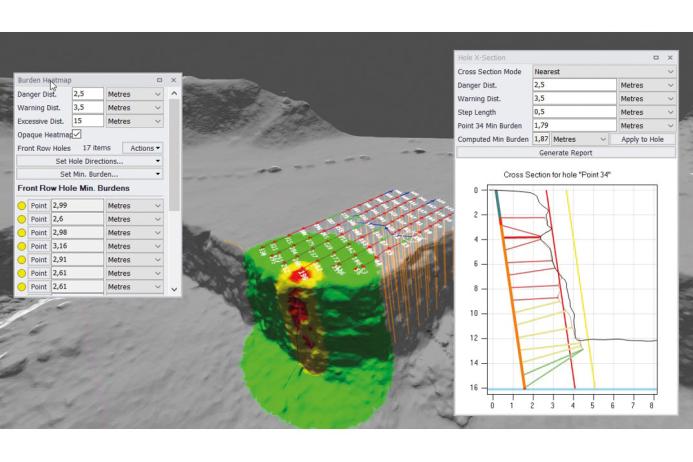
Case study: Balancing fragmentation and vibration in Slovakia
In most blasting scenarios, achieving optimal fragmentation often comes at the cost of increased ground vibrations. This was the case at a quarry in Slovakia, where the customer faced significant challenges in balancing effective rock breakage with compliance to strict vibration regulations. The initial blasting setup led to excessive peak particle velocity (PPV) values, impacting nearby infrastructure and raising concerns about operational feasibility. Seeking a solution to optimize both fragmentation and vibration control, the customer collaborated with Austin Powder to implement a data-driven approach.
Using E*STAR electronic detonators, an optimized charge distribution, and real-time data analysis through Paradigm software, Austin Powder developed a tailored blast design to address both concerns. The precise delay timing provided by E*STAR enabled better energy distribution, reducing excessive peak vibrations while ensuring efficient fragmentation. Paradigm’s vibration modelling, validated through extensive studies, demonstrated a strong correlation between predicted and real-world measurements, allowing for precise adjustments to blast parameters before execution.
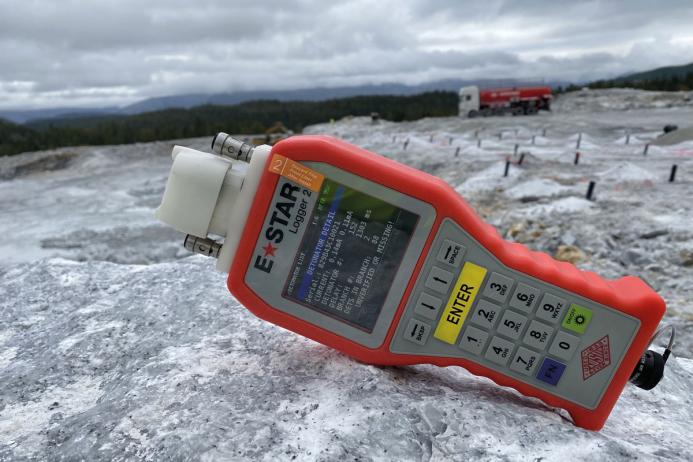
Through multiple blast cycles, Austin Powder refined the interaction between charge weight, timing, and vibration response, continuously improving the accuracy of the vibration model. To further refine the process, they incorporated 3D fragmentation analysis with detailed muckpile assessments to ensure timing adjustments did not compromise fragmentation quality. Pre- and post-blast analyses confirmed that optimal timing configurations resulted in a 20% improvement in fragmentation uniformity, thereby enhancing material flow and reducing secondary breakage requirements. Adjustments to charge weight and stemming parameters optimized energy distribution, minimizing excessive rock movement and improving overall blast efficiency.
The results of this approach were clear: PPV was reduced to compliant levels, while fragmentation quality improved, thereby improving material consistency and overall operational efficiency. By integrating Paradigm’s predictive capabilities with on-site analysis, the customer successfully implemented a long-term blasting strategy that balanced fragmentation performance with strict vibration constraints. This case study highlights that, with the right technology and expertise, it is possible to achieve both optimal fragmentation and controlled vibration levels, ensuring operational success without compromise.
Conclusion: Small details, big impact
Safety and responsibility are at the heart of everything that Austin Powder do. Their solutions are designed to protect both people and the environment while enhancing productivity and precision. By focusing on the smallest details – electronic detonation precision, tailored explosives, advanced software optimization, and full-depth fragmentation analysis – the company ensures that blasting operations are more efficient, cost-effective, and environmentally responsible.
Austin Powder treat safety as their highest priority, fostering strong customer relationships, and building on the strength of their team. The company does not just blast rock; it engineers solutions that make a difference, because in blasting, as in business, details matter.
Subscribe to Quarry Management, the monthly journal for the mineral products industry, to read articles before they appear on Agg-Net.com