Blasting Practices to Control Quarry Floors and Correct Toes
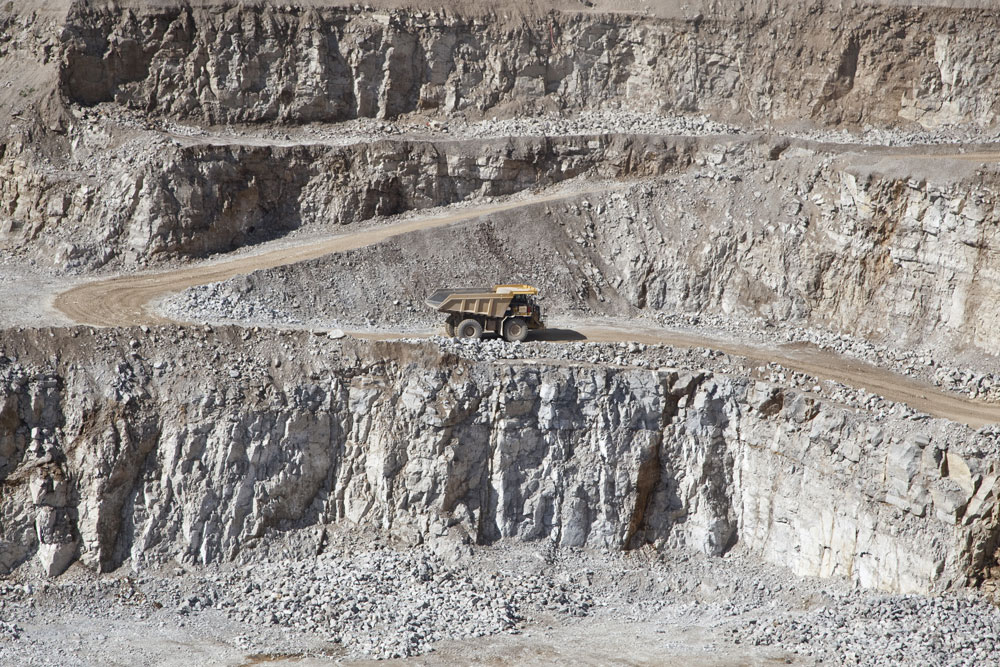
First published in the March 2018 issue of Quarry Management as Tackling Troublesome Toes
By Anthony Konya, senior project engineer, and Dr Calvin J. Konya, founder and president, Precision Blasting Services
The problem of toes and elevated floors after a blast can be traced back centuries to when explosives were first used in mining and quarrying. Why do they occur? Geology is commonly blamed as the cause of toes, but how does geology change so rapidly that one shot results in a decent floor whilst the next is elevated?
A better approach than attempting to blame factors that are beyond the shotfirer’s control is to try to solve these problems and reduce excess blasting, uneven floors, and possibly mechanical removal, by following a systematic approach to identify what is causing the toe. In most cases the toe is not caused by geological conditions, but instead is a direct result of the explosive product, pattern design or drilling inconsistencies. Moreover, if a geological condition is causing this issue it should not simply be written off as a given that the toe must occur; a good shotfirer or blast engineer will quickly modify the blast pattern to account for the geological change and eliminate the problem.
Geology
Geology seems to be the scapegoat of shotfirers and explosives companies worldwide, as the ever-changing nature of the rock makes blasting a highly dynamic and slightly unpredictable environment. However, what sets a good shotfirer apart from the rest is the ability to understand and cope with geological difficulties. Can geology cause problems with toes and elevated floor? Of course it can. Should a good shotfirer know how to change the blast pattern to eliminate these problems? Certainly.
The first problem that could cause a toe or elevated floor is a hard seam. This can be due to a harder material such as a granite intrusion into a limestone quarry, a reduction in the amount of bedding planes or jointing in a certain region, or even the grain size of certain sandstones. No matter what the cause of the seam they can all be treated equally from a blasting point of view.
Two types of hard seams can exist in a quarry, the first being a vertical seam such as an igneous intrusion or vertically dipping bed. Floor issues associated with this type of seam will often be isolated to this specific bed and will show up along the strike. The method to correct the floor problems with this type of geological condition will depend upon the direction in which the blasting is progressing. If the blasting is progressing along the strike (parallel to the bed) the spacing between boreholes around this seam can be tightened up slightly. If the blasting is progressing up dip (perpendicular to the bed) the burden should be reduced when blasting in and behind this bed.
The second type of hard seam that could influence toe creation would be a tough, horizontal seam located at the foot of the blast. While, typically, the burden would be reduced to account for this hard material, the rest of the material may be easily blasted at the current burden. The goal is not to sacrifice the economics of the operation by reducing the burden just to deal with a toe, or to accept the presence of the toe; the ideal solution would be to put a heavier charge into this hard seam, such as emulsion if the borehole is normally loaded with ANFO. If packaged emulsion is used, this area could have a larger-diameter emulsion. If the borehole is normally loaded with bulk emulsion, a cast booster could be placed into this area. In this manner the hard seam will be dealt with by adding additional energy without adding significant cost to the operation.
It is not only a hard seam that can create a toe; a soft seam can have the same effect but for a completely different reason. If a soft seam located within the blast is not properly dealt with, the seam will blow out, significantly reducing the energy in the borehole. This is similar to an over-confined charge with too large a burden, which is one of the major causes of toe and elevated floor problems. In this case, soft seams should always be decked across to ensure proper breakage to the full depth of the blast.
Another geological situation to consider is where vertically oriented bedding or jointing exists between boreholes. In this situation there may be one or more bedding planes between boreholes. If a toe is forming in between boreholes, this is likely to be due to the bedding planes limiting the interaction of boreholes in the same row. To combat this situation a slightly closer spacing should be used throughout the pattern.
In situations where vertically oriented bedding or jointing exists between a borehole and the free face, the bedding planes limit the explosive energy near the free face and at the toe, creating areas in the rock that receive little to no explosive energy and are simply pushed on as the remainder of the material breaks. This is especially prevalent if the rock is harder and stuck to the floor but the planes are lightly cemented together. To account for this situation the burden of the blast should be reduced (with an accompanying decrease in spacing).
Explosives
After geological problems have been considered, the next items to be investigated with regard to random toe or elevated floor problems are the explosive products. Often, operators believe that the explosives used in blasting are carefully made to ensure proper consistency and mixture. Unfortunately, this is not always the case, as commercial explosives are made in large quantities and are not major profit producers. Because of this, explosives need to be carefully tested – or at the very least stored for future testing should a problem occur.
How do poor explosives generate toe and elevated floor problems? If an explosive is improperly manufactured the energy released during detonation can be much lower than expected, causing a state of over-confinement. This leads to poor breakage at the bottom of the shot because it is the hardest area to pull. In addition, a shotfirer may notice significantly higher ground vibration, poor fragmentation and throw, and cratering of boreholes on shorter benches.
The first explosive to consider is ANFO, which comprises a mixture of ammonium nitrate and fuel oil, with the goal being 5.7% fuel oil. If the product is over-oiled it will produce carbon monoxides and suffer from slightly lower energy. If the product is under-oiled it will produce nitrous oxides and have significantly less energy. Through worldwide studies carried out by the authors, the average oil percentage in ANFO is between 3% and 3.5%, causing a loss in energy of around 40–60%.
The other explosive product that needs to be considered is emulsion. While the testing of emulsion is difficult, two important features that should be tested are the sensitivity and the crystallization of the emulsion. It is crucial to test sensitivity when chemically gassing emulsion. This is typically done on the bench with a cup-density test; site specifications should clearly state that this is to be done at the bottom of the first hole and, at minimum, at the bottom of every hole starting a new row. The 20-minute density should be recorded on the blast report.
Crystallization of the emulsion is a major concern, as crystalized emulsion yields much less energy and can completely desensitize. How bad can this be? The authors have worked with emulsion manufacturers to revamp their processes after it was found that inserting a cap into a packaged emulsion could cause shock crystallization to the entire package. With complete crystallization the emulsion will not fire, whilst with partial crystallization the emulsion will fire but with much less energy. It is possible to test for crystallization by rubbing emulsion between the hands and feeling for any grit, which is a sign of crystal formation.
Bench height
Another cause of elevated floors and toes that frequently occurs during blasts is the firing of a short bench. A short bench is not defined by a certain height, but instead by a figure commonly referred to as the stiffness ratio. The stiffness ratio is simply the bench height divided by the burden, which means that a 10m bench that is being shot with a 2.2m burden (75mm packaged emulsion) would have a stiffness ratio of 4.5. As anything above a stiffness ratio of 4 is considered a high bench, floor problems would not be expected with this bench. However, if bulk emulsion were used in a 150mm diameter borehole, this would yield a burden of 4.4m and a stiffness ratio of 2.3, indicating that toe problems are likely, as the shot will now function under more of an uplift mechanism.
Subdrill
The most common cause of sporadic toes and elevated floors after a blast is insufficient subdrill for one or more boreholes. It is important to understand that a subdrill increases the tension zone of the bench to the grade of the floor and an ideal subdrill for this is around 30% of the burden. The first step in ensuring toe problems do not occur is having a properly designed depth for the subdrill. Furthermore, the subdrill needs to be regularly checked to ensure accuracy in terms of both the depth and placement of the bottom of the borehole.
The first step after a driller has completed drilling a hole, before moving the drill, should be to check with a tape measure the total depth of the borehole. Often the driller will not have reached the proper depth for the shot and can now immediately and easily put the steels back into the hole to finish drilling. This final depth should also be recorded on the drilling logs. The driller should then place an upside-down cone or other device into the borehole to stop material from falling back in – before the drill is moved on.
However, material will often find its way into a borehole both from the surface and from slumping on the sides of the hole. To combat this, a system must be put in place to ensure the shotfirer always has at least 30% of the burden available in the subdrill. To begin with, before any explosives are placed, the shotfirer should measure each hole on the morning of the blast. If a borehole is found to be short where the driller has documented that it was to the proper depth, the shotfirer can try to blow this out using compressed air. If this material is not cleaned out to full depth and the fallback is sufficient, a high spot will develop on the floor of the excavation. Another option for short boreholes is to bring driller back to make the hole deeper.
All boreholes should be measured again immediately before loading, with these depths documented on the blast report. All attempts should be made, including the use of compressed air, to clean holes of all fallback and ensure they are loaded to the proper depth. The site should then determine the average depth of backfill by comparing the drill-log depth to the blast report depth for each borehole. The subdrill should then be increased by this amount of depth to ensure the proper depth of borehole is always available.
However, what happens if the subdrill has been increased and the entire borehole is open when the shotfirer measures it before loading – will explosives be wasted? The answer is no, as the shotfirer can simply add drill cuttings to raise the bottom of the borehole to its proper depth.
The next consideration is whether the bottom of the borehole is in the correct location, or whether it has wandered significantly during the drilling process. Drill deviation is a large concern and can dramatically increase toe and floor problems. The longer the borehole, the greater the possibility of large drill deviation, especially where a borehole has been drilled at an angle. Methods such as the flashlight test can indicate if wander has occurred, which is almost always the case, but the only true method to find the bottom of the borehole is through a borehole-tracking device. This gives a 3D profile of the borehole and can be combined with face-profiling systems to determine exactly how large a toe burden is present.
Stemming
The final aspect to be examined with regard to toe or elevated floor problems is one that is traditionally not considered – stemming. When a stemming failure occurs, the energy of the explosive is released and causes a situation similar to that of an over-confined charge. Stemming failure can be easily seen, as on a production blast the stemming should not blow out of the holes but should be completely retained.
Stemming blowouts occur for two reasons, the first of which is the use of improper stemming material. Proper stemming material will lock into the borehole walls, form a bridge, and then shear along the walls until compacting and forming a new bridge. This mechanism occurs until the pressure has been released through breaking of the burden. Inadequate stemming materials such as sand, water, or cement/plaster do not allow for this bridging–shearing–bridging mechanism. For this reason, along with many others, angular gravel stemming material should always be used to stem the borehole.
The other reason why stemming blowouts occur is improper stemming height. For a reasonably designed blast, the stemming should be at least 70% of the burden. However, if improper material is used, short benches are encountered, the timing of the pattern is too fast, or numerous other improper blasting principles are encountered, the stemming will need to be increased beyond this figure – up to 110% of the burden. In many instances of poor blasting even this increase in stemming will not ensure complete retention, but will give the material additional time to hold.
Conclusion
Toe and elevated floor problems have plagued mines and quarries for decades, but are not always a result of geology or variables that are beyond control. In many situations, simple practices can be applied to deal with geology to prevent toe problems and increase the overall performance of the shot. Numerous other problems can also cause toes, such as poor or improper explosive products, inadequate subdrill, improper drill diameter, and stemming issues. In addition, problems with timing, burden and spacing can also severely impact toes on shots.
It is important to remember that the blasting process is ever changing and highly dynamic. A properly trained shotfirer or blast engineer should be able to quickly identify the areas of concern for any type of shot and adjust that shot to give the proper results. In today’s industry, blasting is not simply about breaking the rock into manageable pieces, but properly fragmenting and placing that rock to minimize overall quarry costs and environmental effects.
- Subscribe to Quarry Management, the monthly journal for the mineral products industry, to read articles before they appear on Agg-Net.com