Advanced Sustainable Concretes Boost the Use of Cement Replacements
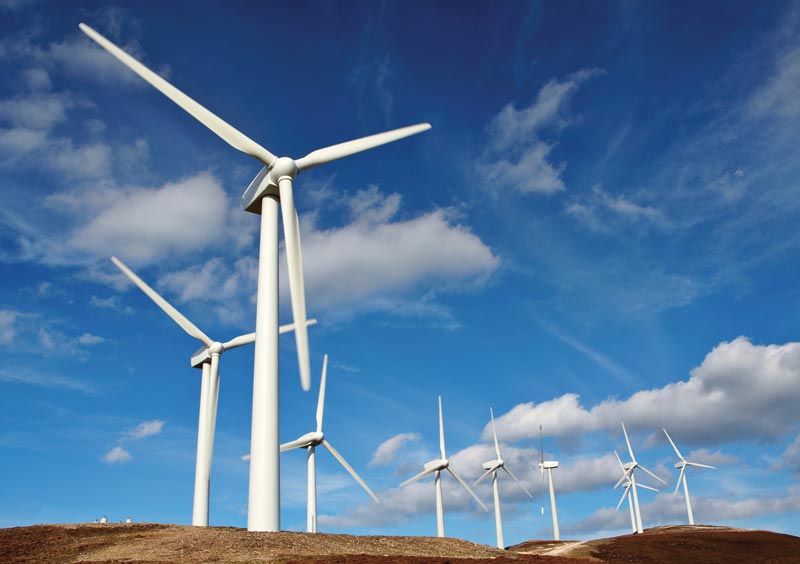
First published in the December 2013 issue of Quarry Management as Sustainable Mixes
Hanson Concrete technical services manager Terry Balmer looks at how innovation in the development of advanced sustainable concretes is boosting the use of cement replacements
After five years of decline, demand for construction materials has, at last, started to pick up and the signs are that it is more than just the false dawn the industry experienced in 2010. With this improving outlook, the spotlight will be on how the industry can become more sustainable and help contribute towards the Government’s sustainability targets by reducing the carbon emissions associated with construction projects.
A lot of work has been done in the last few years to develop concrete products with lower embodied carbon, and the sector has also been using its technical expertise to design concretes which incorporate a greater proportion of recycled or waste materials, but can still perform to high industry standards.
Cement is a vital component of concrete but its production is a major source of CO2 emissions. Manufacturers have been working to reduce this by improving the energy efficiency of their plants and increasing the use of alternative fuels ranging from tyres and bone meal to waste paper and plastic.
Embodied CO2 in concrete can be further reduced by replacing some of the cement with Regen (ground granulated blast-furnace slag or ggbs), a by-product of iron-making, as shown in table 1. Manufacturing Regen requires much less energy and produces around one tenth of the CO2 emissions of Portland cement. It also requires no mineral extraction and prevents thousands of tonnes of waste being disposed to landfill. Replacing one tonne of Portland cement with one tonne of Regen in concrete reduces the embodied CO2 by around 850kg.
As an example, producing 100m³ of conventional concrete typically uses 32 tonnes of cement. Producing 100m³ of concrete with 50% of the cement replaced with Regen saves 13.53 tonnes of embodied CO2, which is equivalent to taking 42 cars off the road for a year or 41 years of electricity usage in the average home.
The use of Regen also means the material is more durable than conventional concretes, improving its longevity, even in aggressive environments, due to its different chemical make-up and inherent ability to reduce the permeability of the concrete through secondary hydration.
In addition, using concretes incorporating Regen can be beneficial when placing large sections as it reduces the effects of restraint. This is because Regen concretes will generally remain workable for longer periods, which is particularly useful in warm weather as there will be a reduced risk of cold joint formation between the different sections.
For the first time, a range of off-the-shelf concretes is available that incorporates Regen. Hanson have introduced EcoPlus, which provides a range of mixes suitable for most applications and significantly reduces the CO2 emissions associated with concrete.
There are eight standard EcoPlus mixes for use in foundations, pavements and structural applications, all of which are easy to use and place, and conform with the latest regulations and standards. They also allow specifiers to see at the design stage exactly how much CO2 could be saved if a specific EcoPlus mix was used.
EcoPlus Foundations offers three mix options for increased resistance to attack from naturally occurring sulphates in the ground. EcoPlus Pavements has two mix options that are air-entrained for superior freeze-thaw resistance, while EcoPlus Structural is intended for the majority of above-ground needs and comes in three mix options. Additional bespoke mixes can also be designed and supplied for requirements that do not fit within the standard EcoPlus categories.
EcoPlus mixes are available from all Hanson plants and specifiers and customers can track the potential CO2 savings using the online carbon calculator at www.hanson.com/uk/ecoplus
- Two high-profile developments in London are benefiting from enhanced sustainability credentials through the use of Hanson EcoPlus concrete in their construction. The 20-storey building at 25 Churchill Place in Canary Wharf and 20 Fenchurch Street in the heart of the city have been designed to achieve a BREEAM Excellent environmental performance rating. Hanson are supplying both buildings with a high strength bespoke EcoPlus mix containing up to 50% Regen, which will play an important part in achieving this.
- In the North, Hanson’s on-site operation at Sellafield supplies bespoke EcoPlus mixes with up to 70% Regen for a wide variety of structures, while at One St Peter’s Square in Manchester, a 15-storey BREEAM Excellent Grade A office building, Hanson have supplied 4,000m³ of a bespoke EcoPlus mix containing 60% Regen for the central slip-formed core.
- Subscribe to Quarry Management, the monthly journal for the mineral products industry, to read articles before they appear on Agg-Net