A Concrete Issue: Why process efficiency matters for net zero
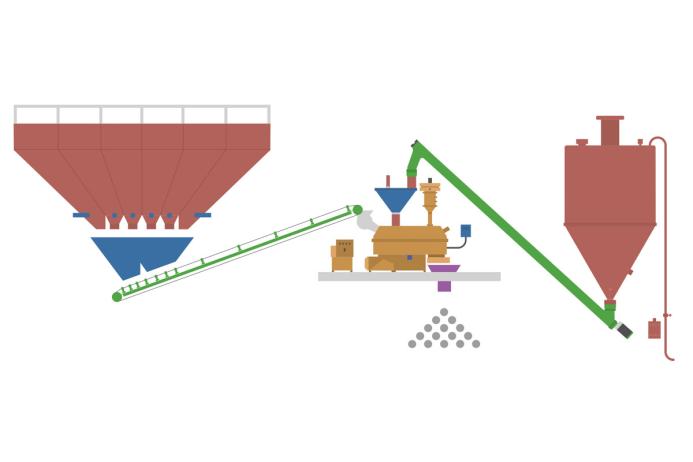
First published in the December 2023 issue of Quarry Management
By James Bullock, chief executive officer, ConSpare
The Mineral Products Association’s (MPA) UK Concrete and Cement Industry Roadmap to Beyond Net Zero illustrates real strides made by the cement industry in terms of reducing carbon dioxide (CO2) emissions from cement production. The way most of that cement enters the built environment is through the production of concrete, therefore concrete producers play a crucial role by minimizing the amount of cement used.
Whilst great progress has been made in many aspects of concrete production, James Bullock, chief executive officer of ConSpare, says that focusing efforts to optimize batching plant operation can reduce cement wastage and, therefore, provide further savings in terms of both carbon and cost.
In nearly 40 years working in the industry, Mr Bullock says he has rarely seen the whole industry rise to a challenge in the same way as has been seen in the recent past. The focus on sustainability and achieving carbon net zero by 2050 is having an enormous impact on UK concrete producers.
However, there is still more work to be done to take every opportunity to make concrete production more sustainable and to reduce emissions associated with the process. As part of the UK Concrete and Cement Industry Roadmap to Beyond Net Zero report, the Mineral Products Association (MPA) first identified all of the points at which emissions are created in the cement and concrete industry, and then developed ‘levers for change’ – a selection of seven key areas where carbon emissions can be reduced.
Progress across those seven areas – including indirect emissions, transportation, and carbon capture – has been admirable, and things are definitely moving in the right direction.
However, one area in which further progress could be made relatively quickly is by optimizing how concrete is made through process development. For example, by improving process control and batching accuracy.
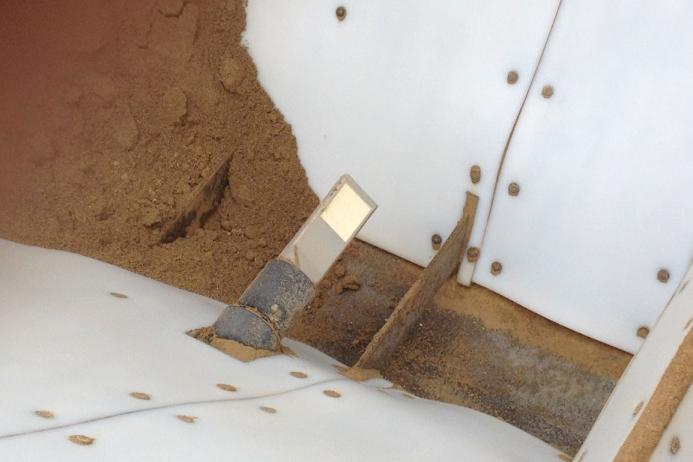
The over-cementing problem
Cement is responsible for a highly significant part of both the cost of the raw materials in concrete and overall carbon emissions. To put it into perspective – the production and transport of a tonne of sand and gravel emits around 5kg of CO2 to the atmosphere*, but the production and transport of a tonne of UK average-blend cement emits 832kg of CO2*. Efficient use of cement is, therefore, vital for any business that produces concrete and also to the environmental impact on the planet overall.
The problem begins with the moisture content of the sand and the smaller aggregates in the concrete. The moisture present in these materials can vary widely, causing changes in the amount of water entering a mix. It is difficult to accurately sample and test these materials in large quantities via manual methods. It sounds simple but getting the right amount of water and dry weight of material into each batch is not easy when a plant is consuming hundreds of tonnes of material per day. As a result, there will always be some level of error present at this stage of the process.
Extra cement is often added to the concrete to account for this error. Essentially, the greater the error from moisture content variation, the more the concrete varies in strength, and ultimately the more cement is required to keep the majority of it within tolerance.
By using inline moisture-measurement equipment, it is possible to improve the accuracy of this part of the process and reduce the amount of additional cement being added, which lowers the carbon footprint of the concrete.
In one example, Hydronix moisture measurement equipment was installed in a ready-mixed concrete plant, resulting in an average reduction of 26kg of cement per cubic metre of concrete produced – equivalent to an annualized saving of 1,413 tonnes of cement and 1,030 tonnes of CO2 emitted per year. Rolling this out to plants across the industry would have a significant impact, complementing other initiatives and playing its part in helping the industry on its journey to net zero.
There are other areas where efficiency improvements can be made across a batch plant, such as installing more energy-efficient mixers and reducing maintenance interventions through extending the service life of abrasion-resistant wear parts.
If these changes are looked at through the lens of carbon emissions, targeted investment decisions can be made to ensure that concrete plant operators achieve maximum benefit, with process improvement and smart maintenance techniques used to reduce the emissions associated with production.
The concrete batch plant – an accelerator for change
At this point, it is really about opening the conversation about how much impact concrete batching plant efficiency improvements can make in terms of carbon reduction. It seems that there is a huge amount of untapped potential in the area of resource and process efficiency, especially with seemingly marginal gains that compound over time when changes are made at scale.
ConSpare’s database shows that there are approximately 2,000 concrete batch plants in the UK, and a collective tightening of processes and investment in efficiency can make a significant difference if everyone is pulling in the same direction.
Working together, across multiple fronts, the industry needs to drive as much carbon as possible out of the concrete production process as quickly as it can, however it can.
For further information, visit: www.conspare.com
*ICE Database 2019: Embodied CO2e of Cement, General, UK Average Blended
Subscribe to Quarry Management, the monthly journal for the mineral products industry, to read articles before they appear on Agg-Net.com