Achieving Greater Efficiency in the Extractives Industry
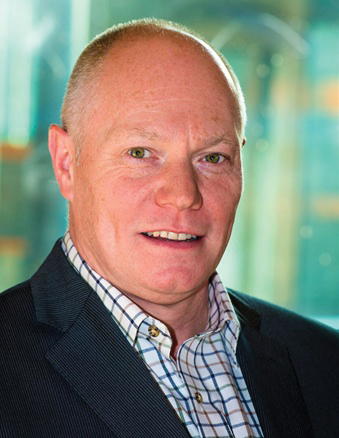
First published in the April 2016 issue of Quarry Management as Why Reinvent the Wheel?
Stuart Moran, head of Minerals and Aggregates Markets with Siemens Process Industries & Drives, explains how the extractives industry can achieve greater efficiency by learning from other sectors
There is no doubt that the extractives industry continually needs to innovate and modernize in order to help it become more effective on a worldwide scale. Several years of mothballing through a world recession have meant that equipment requires reviewing, updating, refurbishing or replacing altogether.
Learning from other sectors is one way the extractives industry can get up to speed on the latest innovations and examples of best practice to raise its own game. After all, why reinvent the wheel?
Integration and automation are buzzwords across many industries at the moment. Being able to fully integrate control and operating systems on conveyors and associated extraction equipment means they will function more smoothly, perform better and have a higher percentage of availability – throughout their longer life cycle. There is one industry that stands out in this area: the automotive industry. The UK’s automotive industry really does lead the world, just as UK technology is behind most of today’s Formula 1 race cars. So, what can we learn from it?
Automotive is a sector that has invested more than £6 billion in the last two years (figures from EEF 2014), and it turned over £555 billion last year. A total of 1.58 million cars and 2.5 million engines were made in the UK in 2013. It is a UK success story and its drive for efficiency, flexibility and control have made it what it is today. The car industry embraced the concept of integrated drive systems and total integrated automation long before other sectors and now is the time to benefit from its experience.
In conveying, sorting, storing, picking and placing, the concepts remain much the same: seamless and integrated productivity is imperative for business success. Integration offers a future-orientated solution that can be individually tailored to suit almost any application, with cost-effective material flow, precise positioning, the efficient spanning of long distances and smart technology packed into the smallest space.
Integrated drive systems
The Siemens concept of integrated drive systems (IDS) covers three dimensions: horizontal, vertical and life-cycle integration. Horizontal integration covers all components within the ‘drivetrain’, such as variable-speed drives, motors, gearboxes and couplings. Correct specification leads to a drivetrain perfectly matched to the load requirements, which maximizes efficiency and reliability throughout the lifecycle, and plant availability can be boosted by up to 99%.
Vertical integration: by incorporating controllers that also acquire data, the ability to predict and avoid a problem becomes a welcome reality, with planned maintenance scheduled and performance and energy usage being monitored. Engineering time can be cut by up to 30% using this method. With the new European energy-related product standard now in force (EN 50598), being able to monitor and control motor-driven systems will become increasingly important in all industries. Knowledge truly is power in this situation.
The life-cycle integration dimension complements the other two, ensuring a drive system is always working to its maximum potential and supporting the process 24h a day, 365 days a year, throughout its operating life. It can help reduce maintenance costs by up to 15%.
Improving efficiencies need not be limited simply to systems such as conveyor machinery. At a cement works in the south of England, using a more efficient motor and drive in a grinding mill upgrade saved more than £175,000 per annum and paid for itself in under two years. It also reduced CO2 emissions by 1,487 tonnes in eight months. Power consumption was reduced by 37% using integrated automation and drive systems.
Best technology
Taking the best of integrated technology from the automotive industry, one of the most popular solutions is distributed, close-to-the-motor control, which provides a flexible and efficient solution for conveyor operators. Here, the topology is based upon geared motors, distributed inverters and motor starters as the linked elements. Using PLC controllers and HMI operator panels for control, detailed monitoring and diagnostics of the plant or conveyor system puts all information at the operator’s fingertips. These units are combined with an overload-protected power supply, distributed control through additional PLCs and variable-speed drives, providing a high degree of flexibility, IP65 protection, compact modular design, simple installation and fast commissioning. This type of system uses Profinet/Profibus for communication, parameterization and diagnostics, and the digital inputs and outputs of the units can be used as distributed I/O for the control.
Using variable-speed drives which are capable of energy recovery means braking resistors are not required and integrated ‘safe torque off’ safety function means encoders are not required. Replacement is simple owing to the modular design and optional memory card. Additional functions of a unit like the Simatic G120D include integrated positioning capability via HTL or SSI encoder and basic PLC functionality. These systems are maintenance-friendly, easy to replace and can also incorporate high levels of safety technology into the process.
Geared motors such as Simogear provide a great deal of flexibility for conveyor systems, with a wide range of gearbox types, mounting options and optional pluggable connection systems to ISO 23570, mounted encoders and brakes. RFID systems and code-reading systems can also be installed.
Building safety into the system
Built-in safety measures on all equipment used for conveying applications are increasingly becoming critical priorities for operators, in an industry where temperature extremes, dust and hazardous environments are common. A high degree of protection is inherent in standardized, modular products that are designed to function together and this protects people, the machinery and the environment. Distributed and comprehensive control, drive and switching technology on longer-distance conveyors can provide many built-in safety features, such as:
- safety integrated systems and modules
- system consistency
- greater availability and more reliable use (fewer breakdowns)
- optimized outputs for global competitiveness
- built-in overload protection
- simplified retrofits and modernizations
- quicker restarts after system modifications
- easy expandability and integration within the Totally Integrated Automation portal
- helpful diagnostic tools
- continuous, live monitoring
- efficient and planned maintenance strategies.
Totally integrated automation
In a world where efficiency and productivity are decisive success factors for manufacturing industries, being able to totally integrate the automation elements can give a company a crucial edge. Being able to control increasingly complex machinery and plants and to make all automation components interoperable not only reduces costs, but also reduces engineering time and produces greater flexibility for a genuinely future-proof system.
A major UK-based Japanese car manufacturer implemented this style of fully integrated drive and PLC solution including Simogear, Et200 pro frequency converters and direct online starters for the drivetrain and PLC, safety, RFID and Profinet. This fully integrated solution allows line-wide visibility of all components on the HMIs so that diagnostics are far superior, minimizing downtime and improving line OEE. The Profienegy profile was integrated to allow devices to be switched off during stoppages, such as break times, giving additional energy saving results.
Conclusion
Using the experience of the world-leading automotive industry can give the extractives industry some very useful short cuts, such as the use of distributed control for flexible, efficient solutions. As quarries gear up for increased production, now is the time to be investing in new equipment and processes, optimum solutions and safety improvements, to ensure a successful and efficient future.
For more information visit: www.siemens.co.uk.