Real Rejuvenation of Bitumen
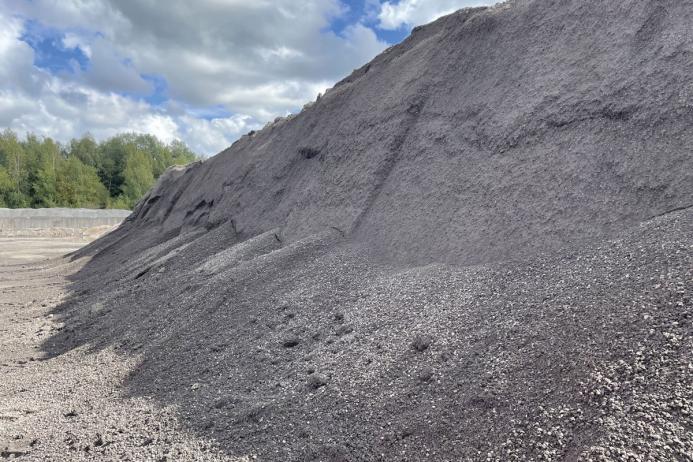
First published in the July 2024 issue of Quarry Management
Unlocking the Potential of RAP
By Rick Ashton, business development manager UK and Ireland, Rettenmaier UK Ltd
JRS (J. Rettenmaier & Söhne GmbH + Co. KG) have been manufacturers, problem solvers, and reliable system/technology partners for a wide range of industries since 1878, and as a corporate group are now globally active with around 4,000 employees at more than 90 locations worldwide.
The company’s VIATOP bitumen-coated fibre pellets and fibre-additive pellets have set the standard for years for functionally reliable and high-quality additives for modern asphalts.
Innovative products which provide other functional additives for a great variety of requirements besides fibres, have been developed in an intensive working relationship with asphalt experts around the globe in order to meet the constantly increasing requirements placed on demanding asphalt solutions.
It is innovative collaboration of this nature that led to the research, development, and launch of the VIATOP plus RC product described in this article.
The need to utilize road planings or reclaimed asphalt has never been more crucial. Asphalt manufacturers and their clients understand that they work with finite resources. Primary aggregates are often unavailable locally and sometimes onerous specifications around parameters such as PSV (polished stone value) require long supply chains due to limited geographic sources. All this increases carbon intensity and loads EPD (Environmental Product Declaration) certificates accordingly.
The most carbon-intensive element in the EPD and most costly constituent in the asphalt is undoubtedly the glue which binds it all together – bitumen. The good news is that the aged roads we replace contain both aggregate and bitumen, both of which can be reused or recycled depending how much innovation is applied. A road is, in fact, an undervalued linear quarry and refinery combined. Urban mining should be the approach to replacing worn-out roads.
Defining two often confused phrases ‘Reuse’ and ‘Recycle’ helps to explain what is required to improve the situation. The definition of each is important. Reuse describes using materials or products for the same purpose they were originally designed, eg asphalt to asphalt has been done on a limited scale for years, glass to glass is established, and plastic to plastic is commonplace.
There is little need now to use many of the reclaimed products that used intensive cradle manufacturing energy and carbon costs for uses other than for their original purpose. Some of the ‘waste’ products added to asphalts in recent years can now be reused for their original higher-value purpose by the manufacturers who produced them in the first place. ‘Greenwash’ and ‘trashfalt’ must be avoided at all costs. To be credible, any innovation considered should replicate or improve the performance and sustainability of the product for future generations’ environmental sustainability, safety, and economic security.
To differentiate, recycling is the preparation or treatment of materials into something new or different. In Germany, the Closed Substance Cycle Waste Management Law (Kreislaufwirtschaftsgesetz) requires that waste avoidance always takes precedence over waste utilization. Reclaimed product must be brought to the highest possible end use. RAP from surface courses must be used in new surface course mixes and not wasted in base or binder course mixes.
This is not common practice in the UK where all asphalt road planings tend to be homogenized into outdoor stockpiles and reintroduced as one product stream to the lower layers. This loses high-PSV aggregate into base and binder layers where its skid-resistance properties are not required. This, again, is recycling not reuse. Specification is opening up, however, with 20% RAP now allowed in surface courses.
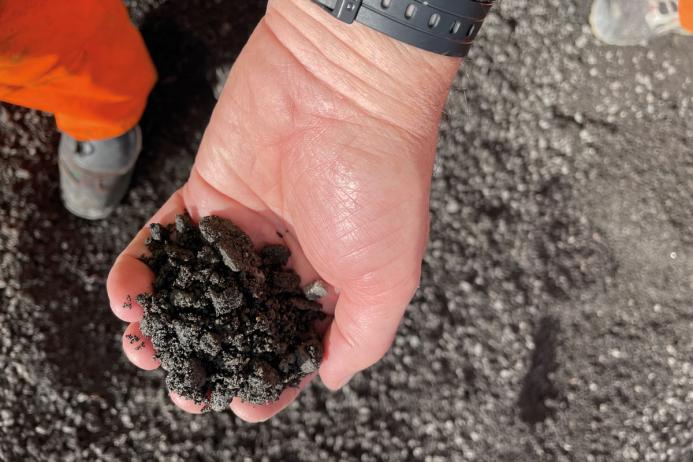
Following the German experience of best practice, to use RAP optimally it should be processed and stored in isolated stock bays. This storage should be covered for the smaller fractions as any moisture absorption will require extra heating fuel to dry the RAP, thus increasing carbon intensity. Once stored, a defined number of samples can be taken from the stockpiles and analysed.
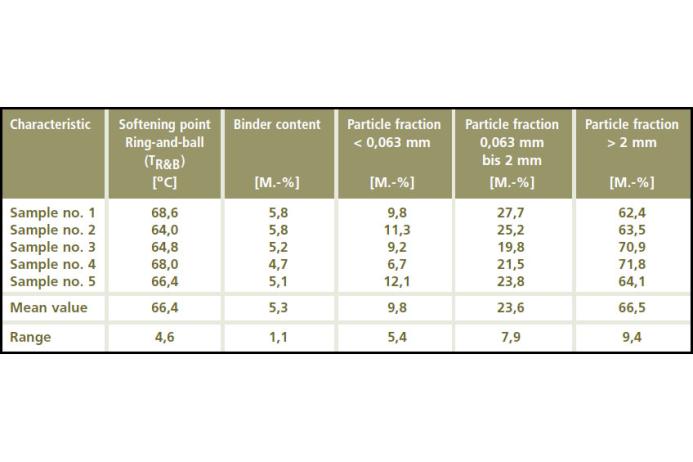
The basic constituents of the RAP are then determined by: binder content %m, softening point ring and ball (°C), and particle size distribution (grading), as shown in table 1.
The analysis of the above properties and the recovered bitumen characteristics will determine the optimum or maximum RAP addition rates based on the test results or the plant’s maximum capacity to add the volume permitted.
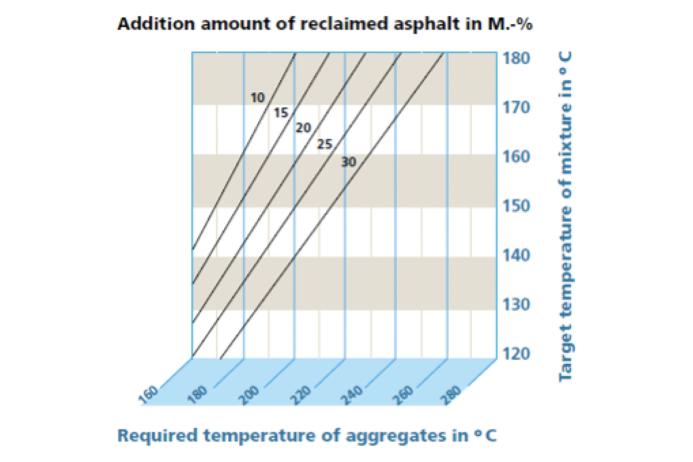
Once determined, addition rates will affect the end temperature of the mixture, therefore these factors can be considered with a matrix such as table 2, whilst table 3 demonstrates the need to minimize moisture content.
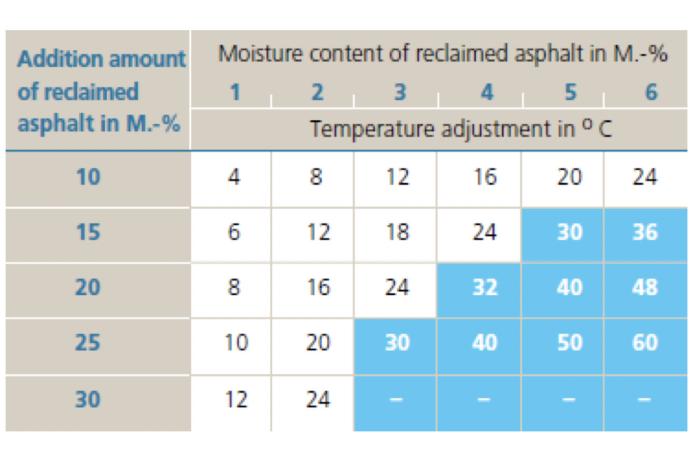
To utilize RAP to its optimum extent it is necessary to understand how asphalt and its bitumen binding agent age throughout the service life of the material. Aging is primarily caused by heat, UV light, and oxidation reactions within the bitumen. This leads to a brittle binder (increased stiffness) and reduced ductility, resulting in a loss of adhesion with subsequent ravelling or fretting plus thermally induced winter cracking.
When water then enters the cracks a ‘freeze-thaw’ cycle begins to pull the asphalt apart, resulting in potholes and surface defects. The aging process reduces the ratio of the oily phase (maltenes) in the binder, leaving a greater ratio of stiffer asphaltenes, which leads to a less ductile binder. These viscosity and elasticity changes result in hardened, brittle binder and the end of primary service life. Asphalt aging occurs in two stages: short term and long term.
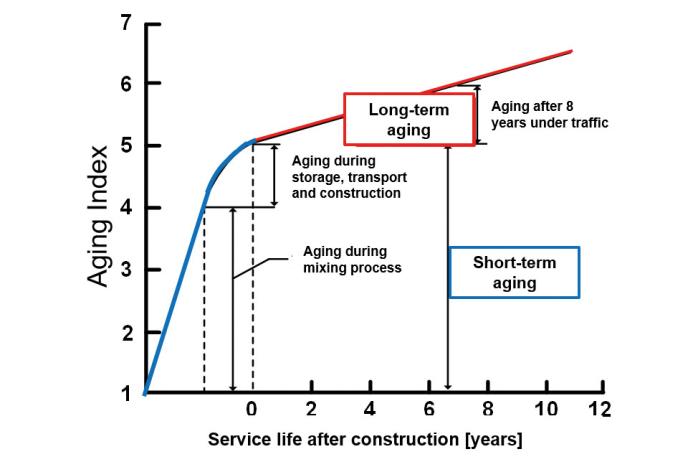
Short-term aging is mainly due to oxidation and the loss of volatiles and oily components, and happens during mixing, transport, and paving. The most accelerated aging occurs during the mixing process when bitumen is exposed to heat and oxygen due to it being in a thin film covering a large surface area in the mixer box.
Long-term aging happens during service life and is mainly dependent on factors such as void content in the composition of the asphalt and external influences such as atmospheric oxygen and dynamic forces.
Technologists cannot wait more than 12 years to benchmark or homologate a bitumen’s performance and resistance to aging. These aging characteristics can be laboratory simulated through short-term and long-term accelerated aging tests.
The short-term simulation is via the RTFOT (rolling thin-film oven test) EN12607-1. This test simulates mixer box and installation aging of the binder by exposing a thin film of bitumen to heat and oxidation in rolling tube cabinet under test conditions of 163°C for 275mins.
The long-term simulation is via the PAV (pressure aging vessel test) EN14769. This test simulates the in-situ (road life) service aging by exposure to test conditions of 100°C for 20h hours at 21 bar pressure.
These two tests allow recovery of the laboratory aged bitumen for benchmarking of aging characteristics. Reclaimed bitumen from asphalt samples displays corresponding characteristics to these laboratory aged samples in the standardized tests of penetration and softening point, and rheological tests such as DSR (dynamic shear rheometer). It is possible, therefore, to investigate what methods can be used to restore or rejuvenate aged bitumen using a protocol including these methods.
Rettenmaier’s technologists decided to investigate products that claim to restore the original properties of the binder to improve mix flexibility and reduce consumption of virgin or primary materials, the objective being to find a functional asphalt additive to offer ‘real rejuvenation’ rather than softening and plasticizing alone.
Rejuvenation of bitumen not only implies the reduction of age-gained viscosity, but also the restoration of the viscoelastic properties of the aged binder. This could open the possibility of higher RAP addition rates, thus lowering carbon footprint and saving finite resources of virgin bitumen and aggregates.
Some products are marketed as rejuvenators but upon analysis are actually just basic softening agents or fluxing oils. Basic vegetable oils can lower viscosity but these cannot reactivate aged binder, alter resistance to deformation, or restore cold temperature crack resistance. Another method to increase RAP addition is to use very soft-grade, often premium-priced 250/330 pen bitumen to soften the recovered penetration of the end mixture. This can lower virgin binder content and achieve penetration recovery compliance but has little influence on the aged binder in service – merely recoating the RAP with fresh bitumen as black aggregate.
The function of a credible rejuvenator is more holistic. The goal should be to restore the physical and rheological characteristics of an aged binder to the requirements of current binder specifications by activating the aged binder and not just softening or plasticizing it. The aim is to eliminate or reduce cracking whilst maintaining rut-resistance and improving the relaxation, ductility, cohesive, and adhesive properties of the aged binder.
This report describes one such product – VIATOP plus RC. This additive pellet is the result of comprehensive research and development and brings a true rejuvenator to the Rettenmaier VIATOP portfolio of functional asphalt additives – the active ingredient being a high-purity fatty alcohol wax mixture made from sustainable raw materials. For ease of handling in asphalt plants the product is pelletized for addition in the same way as the pellets used in SMA production. Alternatively, for bitumen producers the ‘prill’ raw additive is available from Rettenmaier UK in bulk or large bags to produce rejuvenating bulk bitumen for tank storage and delivery.
The assessment of the product followed testing of the physical and rheological properties of a 50/70 penetration grade binder with the status ‘virgin’ and ‘RTFOT + PAV’ to age the binder. The following analyses were then carried out on the laboratory aged specimens – ring and ball softening point test (TR&B), needle penetration (NP), bending beam rheometer (BBR) and dynamic shear rheometer (DSR).
The properties of the virgin, short-term, and long-term aged binder were measured. Post long-term aging in the PAV the rejuvenation of the aged bitumen was attempted by adding 3% of the active additive used in VIATOP plus RC to the aged bitumen (at 3% of the binder content).
Testing of the physical and rheological properties of the bitumen was undertaken using the same aging test protocol. Repeated aging of the rejuvenated bitumen and analysis of the physical and rheological properties of the binder was undertaken to benchmark aging characteristics against the virgin 50/70 pen.
Penetration and softening point – aging profiles
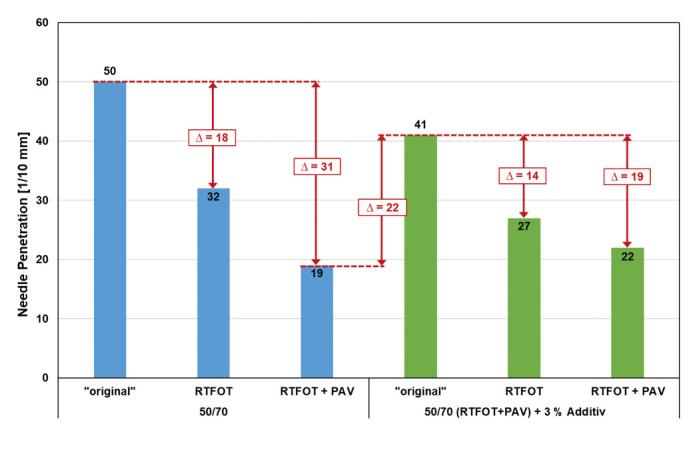
Table 5 shows the results of the NP tests then rejuvenation with 3% VIATOP plus RC additive. The repeated aging rate of the rejuvenated binder is comparable to the original binder demonstrating that asphalt using RAP treated with VIATOP plus RC should age in a similar manner to primary or virgin asphalts.
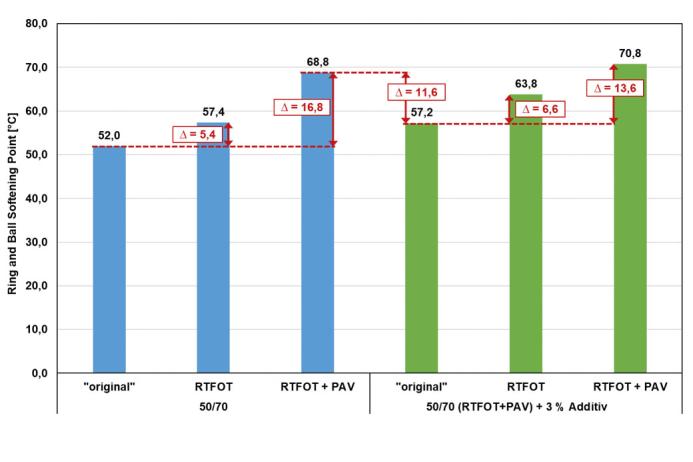
Table 6 shows the results of the softening point tests then rejuvenation with 3% additive. The repeated aging rate of the rejuvenated binder is positively comparable to the original binder.
Rheology and bitumen aging
The dynamic shear rheometer (DSR) measures stiffness and elastic properties of bitumen, as explained below.
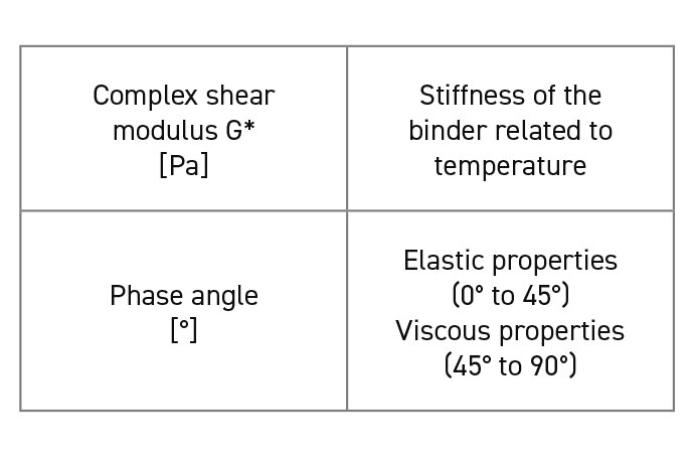
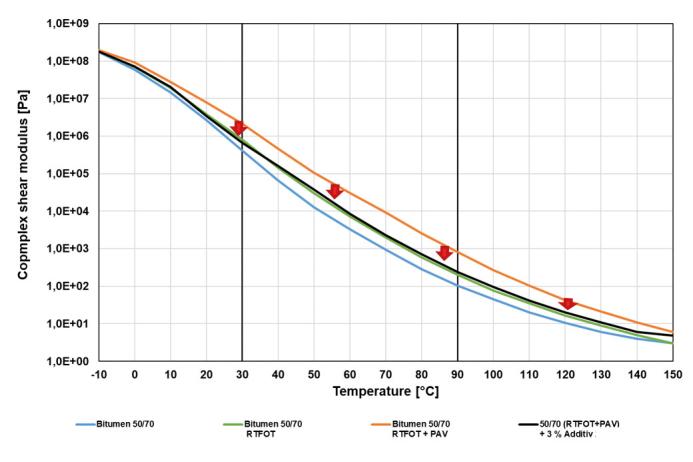
Table 7 displays complex shear modulus progression through the aging protocols. Complex modulus increases as oxidation and viscosity increases. It is clear the viscosity of the aged then rejuvenated binder is reduced over the entire temperature range.
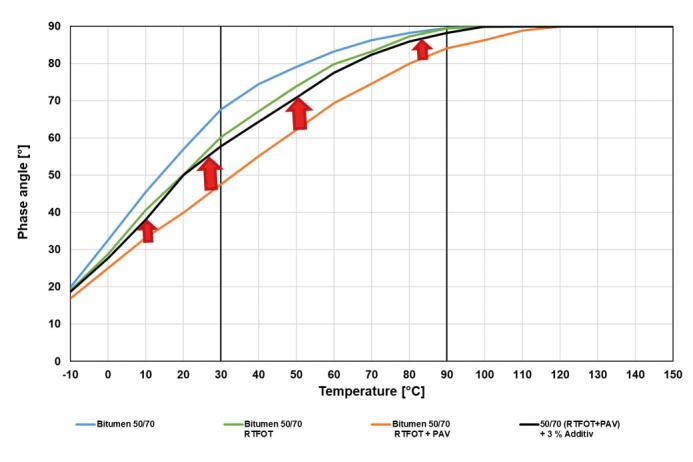
Aged oxidized bitumen demonstrates a reduction in phase angle as asphaltene levels increase or change in dimensions. Table 8 demonstrates the black (rejuvenated) curve has reactivated the aged binder and not just softened or plasticized it. The phase angle moves from a long-term aged profile back toward that of a newly produced (short-term aged) material across the entire temperature range.
Cold temperature performance and aging
Aged asphalt is particularly sensitive to cold temperatures. As viscosity increases and ductility decreases the bitumen’s ability to relax stress becomes inhibited leading to cracking or fretting. This aging is accelerated as asphalt void content increases beyond 5%, as reflected in the service life of different asphalts with various void contents. Porous asphalts age much faster than SMAs and dense mixtures for this reason. The bending beam rheometer (BBR) three point bending-beam test is designed to characterize the low-temperature behaviour of binders in the range –40°C to 0°C.
The BBR test predicts the critical temperature of bitumen with thermally induced cracking in winter. The BBR measures the temperature at a stiffness of 300MPa (°C). This gives a benchmark of how a bitumen will resist low temperatures. Another measure used in BBR testing is the m-value, to provide an indication of the ability of a binder to dissipate stresses or relax. BBR is not a destructive or failure mode test, however the properties measured correlate with asphalt failure tests, eg TSRST – thermal stress restraint specimen tests.
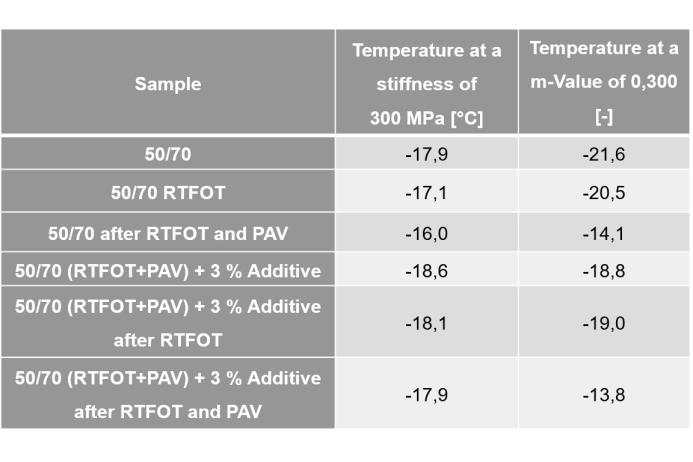
Table 9 presents the results with the virgin binder, then through the two-stage aging protocols, and then following the addition of 3% VIATOP plus RC rejuvenating agent. Remarkably, the results show that, even after two aging protocols, with the addition of the rejuvenator the bitumen has retained (or slightly improved) its original low-temperature resilience.
Out of the lab and on to the roads
Full-scale plant industrialized trials were conducted in Germany using 3% addition rates into SMA surface course. Two test sections were prepared in the city of Münster. Binder and surface course layers, both ‘modified’ with VIATOP plus RC rejuvenating pellets, were produced. The target RAP content was 60% for both layers. The use of such high levels of RAP in a surface course was only possible through the careful isolation of surface course planings and correct analysis and assessment of the recovered material. With these data, the Rettenmaier technical support team could then advise on additive levels to achieve the optimum dosing levels. The technical support offered to end users of the product is extensive, for example, the supply of blending worksheets for addition rates to be optimized based on the input of RAP analysis results.
The trials commenced in November 2017 and samples recovered confirmed the extensive lab data on the efficiency of the rejuvenator with the asphalt material meeting all regional and national specifications. Some seven years later the roads are still performing as predicted.
In terms of compaction and workability, the material was found to be consistent with primary or virgin-produced asphalt and complied with all void specifications with in-situ void content results less than 3%. This indicates an impervious material that will resist oxidative aging and water ingress to give a long service life.
Conclusions
VIATOP plus RC wax-coated pellets represent a real rejuvenating product for aged binders in reclaimed asphalt products.
The product is made of natural plant-based renewable raw materials. It is non-water-polluting and does not need hazard labelling.
VIATOP plus RC is a highly efficient way to gain additional reuse of reclaimed asphalt.
Higher addition rates of reclaimed asphalt mixes are made possible compared with traditional methods of RAP reprocessing.
The use of 60% RAP addition offers substantial carbon and cost reduction.
VIATOP plus RC conserves natural finite resources.
VIATOP plus RC uses the existing dosage systems for fibre pellets, requiring no additional capex investment for addition tanks or additive stations.
The product is pre-blended and ready to use, releasing asphalt producers from the quality control element of mixing liquid additives.
The product is now available for UK supply and samples are available, if required, for pre-production trials.
The plant-based VIATOP plus portfolio of technical cellulose fibre technology offers sustainability, durability, and environmental credibility.
Subscribe to Quarry Management, the monthly journal for the mineral products industry, to read articles before they appear on Agg-Net.com