Building more, with less
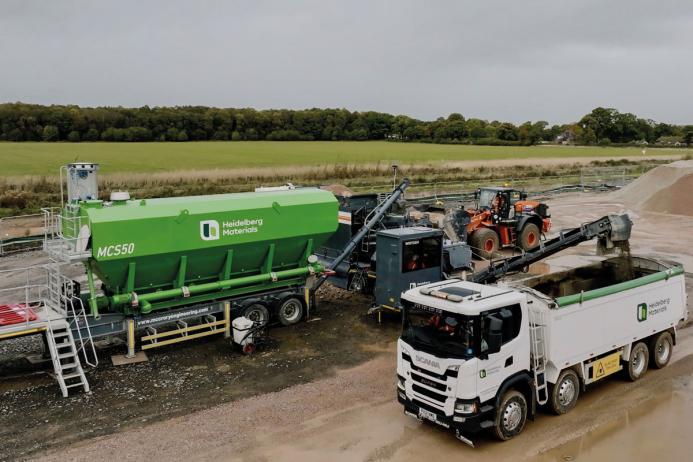
First published in the January 2025 issue of Quarry Management
Heidelberg Materials extend cold-mix capabilities to help create sustainable, resilient highways
Heidelberg Materials’ products and services are evolving to tackle challenges such as the impact of climate change and conserving natural resources by promoting the circular economy and decarbonizing the business.
One example of this is the company’s investment in mobile cold recycling plant, which can use both recycled and primary aggregate to produce cold-mix materials, providing a lower-carbon solution for road construction and maintenance projects.
The mobile batching plant has a large, 240-tonne mixing capacity and can process recycled construction materials, asphalt planings, and primary aggregate.
The Wirtgen KMA 240i plant allows the company to use technologies such as foamed bitumen, emulsion, cementitious and biogenic binders to produce a range of cold-mix materials.
Ian Price, Heidelberg Materials Contracting managing director, said: ‘Our investment in mobile plant allows us to complement our existing range of sustainable solutions with the option of cold-mix products, saving energy and associated CO2 emissions.
‘It also allows 100% of worn-out road surfaces to be recycled back into new materials, reducing the need for primary aggregate, which is crucial to reaching net zero.’
Heidelberg Materials offer their customers a range of cold recycled bound materials (CRBM), which are a like-for-like equivalent to replace traditional base and binder asphalt courses in road and footway construction.
Among them is foamed asphalt, which contains up to 95% recycled content and can reduce the carbon emissions associated with asphalt production and laying by a minimum of 40% compared with conventional hot-mix materials.
Foamed asphalt is manufactured by injecting water and air into hot bitumen under high pressure, which causes the bitumen to foam. This increases its volume and decreases its viscosity, allowing the effective coating of aggregate.
A wide range of recycled materials can be used within the mix including recycled asphalt planings, crushed concrete and tar-bound planings, allowing this hazardous waste to be safely reused in carriageway construction.
Foamed asphalt is suitable for a wide range of asphalt applications and can be placed and compacted immediately or stored for later use, extending working times and ensuring continuous supply.
The low production temperatures also greatly improve health and safety for the workforce – reducing fumes, odour and steam, improving air quality, and lowering the risk of burns – and enable faster completion of resurfacing work, increasing efficiency and resulting in less disruption for road users.
The material is designed and manufactured in accordance with the ISO 9001 quality management standard and meets Specification for Highway Works (SHW) Clause 948 and BS 9228 for Recycling of Roads.
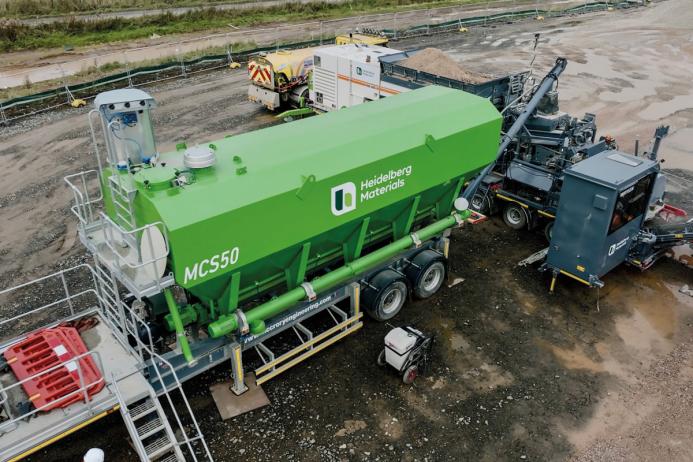
Heidelberg Materials’ cold-mix plant also produces cement-bound granular material (CBGM), which is a sustainable alternative to traditional flexible paving materials such as an AC 40/60 basecourse.
CBGM is an efficient and cost-effective option for constructing durable, long-lasting roads and footways quickly. It can be used in road foundations, as it is more robust than a MOT Type 1 aggregate, and also in flexible composite roads, replacing the asphalt base layer.
Heidelberg Materials are using their mobile recycling plant to produce around 10,000 tonnes of CBGM for use on the Carlisle Southern Link Road, which will connect Junction 42 of the M6 with the A595. The company is working with main contractor Galliford Try, manufacturing and laying the product to create the base layer of the new 8km road, which is due for completion in late 2025.
Liam Potts, the project manager at Heidelberg Materials Contracting who managed the Carlisle Southern Link Road project, said: ‘Using CBGM resulted in significant time and cost savings for the client.
‘Our mobile plant, located on site, provided surety of supply and high productivity levels due to its large capacity. CBGM is also a more cost-effective alternative than traditional asphalt base materials.’
Heidelberg Materials’ investment in cold recycling plant is part of their overall strategy to conserve natural materials and promote the circular economy.
Last year the company created a new recycling business line which recovers construction and demolition waste and processes and reuses it to deliver sustainable products to its customers through circularity and innovation to enable building more, with less.
Subscribe to Quarry Management, the monthly journal for the mineral products industry, to read articles before they appear on Agg-Net.com