Technology unlocks fuel efficiency
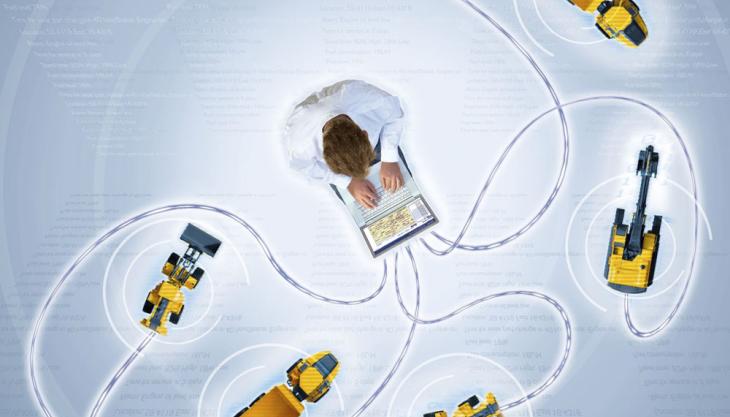
Volvo CE working on intelligent transport systems that could reduce fuel consumption by up to 30%
WITH fuel efficiency being a top priority for construction equipment owners, engineers in Volvo Construction Equipment’s Technology function are currently working on sophisticated innovations to make their mobile plant as fuel efficient as possible.
A key area of technological development in this field is machine-to-machine (M2M) and machine-to-infrastructure (M2I) communication.
‘One of the advanced engineering projects we’re working on is wireless machine communication technology,’ explained Peter Wallin, research co-ordinator with Volvo CE.
‘By increasing machine intelligence and making it possible for machines to ‘talk’ to each other, we can reduce operational costs through improved fuel efficiency, while also increasing safety and maintaining productivity.
‘So far we’ve looked at the quarry and aggregates segment and road construction – but this technology can be used in all the applications Volvo machines work in.’
Volvo CE have conducted tests to calculate the potential fuel savings M2M communication could bring to articulated haulers working in the quarry and aggregates segment. The project monitored a hauler, loaded with rocks from an excavator, travelling to the crushing site.
The machine was fitted with an internal measurement system to verify the fuel consumption, and the hauler was operated by different drivers, at both constant and varied speeds, with different amounts of idle time and both with and without stops along the way.
Tests showed that when the hauler travelled faster than necessary to the crusher, and as a result had to wait before unloading, fuel consumption was up to 30% greater compared to when the hauler travelled at a constant speed and arrived at the optimum moment.
‘In conjunction with the tests carried out in Braås, Sweden, we’ve visited customer sites and monitored how the machines are used,’ said Mr Wallin. ‘Today, sites aren’t optimized and usually there isn’t a structure stating when the haulers should arrive at the crusher.
‘Often the machines are driven at maximum speed but when you look at the amount of idle time it’s clear that this isn’t always necessary. When the machines are stationary, waiting to unload, they’re wasting time and money.
‘By using M2M communication the operator would know exactly when to arrive at the crusher and what speed to travel at to get there. Through reducing machine speed and idle time we are reducing fuel consumption and wear and tear on the machine, as well as facilitating an efficient flow of equipment.'
Mr Wallin continued: ‘The next stage of the project will be to provide the operator with information – such as target speed and arrival time – inside the cab. This live information will support and guide operators to the most fuel-efficient operation and could be presented in future concepts like heads-up displays and other innovative approaches.
‘If all the equipment on a job site was fitted with this technology, the machines could be linked to a central control point – such as a tablet device used by the site manager – to optimize the efficiency of the fleet.’
Volvo CE say the results from this project will determine if, when and how this technology will reach the market.
Mr Wallin added: ‘An undoubted advantage of increased machine intelligence is the ability to introduce active safety. Volvo have set themselves the target of reducing accidents relating to their equipment to zero – and future technology like M2M communication will play a major part in achieving this ambition.
‘For example, if we combined M2M communication technology with an automatic braking system, it would prevent the possibility of a collision between two Volvo machines – and by equipping site workers with a wireless beamer or a transmitter, machines could also detect and avoid humans in the vicinity.’