Six new Volvo machines for Raymond Brown
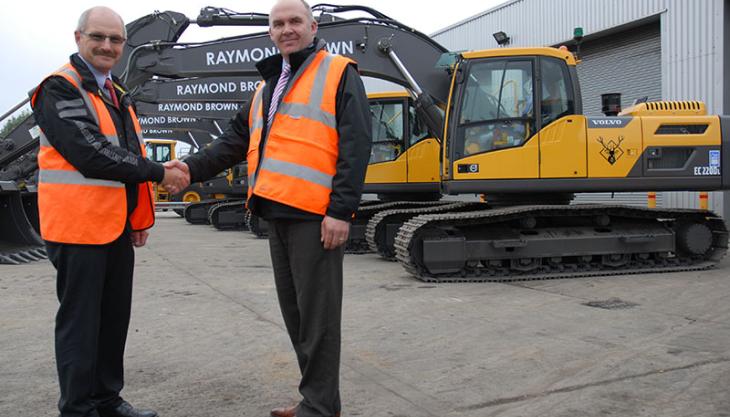
Company takes delivery of excavator and wheel loader package for its aggregates operations
RAYMOND Brown have taken delivery of a substantial package of Volvo CE products for their aggregates operations and other long-term contracts. The package comprises three 22-tonne Volvo EC220D excavators, two of the latest 25-tonne E-series EC250E excavators, and a Volvo L150H loading shovel complete with a 4.2 cubic metre general-purpose bucket.
The six machines represent part of a replacement plan but also an increment to the Group’s overall mobile fleet, as it has recently secured additional long-term contracts.
‘We’ve been associated with Volvo equipment for more than 25 years,’ said group plant manager Nick Moth. ‘In our opinion, build quality and overall performance, coupled with excellent operating costs, are the reasons why we choose Volvo.’
Whilst the three EC220D excavators will be deployed in an aggregate quarry, a sand and gravel pit and a recycling facility, the all-new Volvo EC250E excavators and L150H wheel loader will be engaged on long-term contracts processing of incinerator bottom ash (IBA) at locations across Hampshire and Oxfordshire.
Besides machine reliability and performance, Nick Moth says he expects significant fuel savings with these latest products. The EC220D’s for instance, benefit from the use of Volvo’s Stage IIIB D6 engine, delivering 175hp (129kW) of power and 849Nm of torque, coupled to an improved hydraulic system with larger pumps which in turn significantly improves hourly fuel consumption with shorter cycle times.
The larger EC250E excavators are equipped with Stage IV final Volvo eight-litre engines developing 215hp. Operators can select the best work mode for the task at hand, ensuring optimum performance and fuel efficiency.
Similarly, the new Volvo L150H wheel loader is exceptionally productive and fuel efficient. It features a Volvo Stage IV 13-litre engine, enhanced by a Volvo powertrain and intelligent hydraulics which supply power only on demand.
To further reduce fuel consumption and cycle times, the loader’s Automatic Power Shift (APS) and Fully Automatic Power Shift (FAPS) functions automatically adjust the machine’s gears in line with engine speed and travel speed.
Another intelligent feature, the Reverse-By-Braking (RBB) function, automatically reduces the engine rev/min and applies the service brakes when the operator changes the direction of the machine. This not only helps conserve fuel but also reduces stress on the drivetrain, thereby extending component life.
Moreover, Volvo’s Optishift technology combines the RBB function with a lock-up torque converter to create a direct drive between the engine and the transmission, eliminating power losses in the torque converter and reducing fuel consumption by up to 18%.