Second Volvo L350F for Singleton Birch
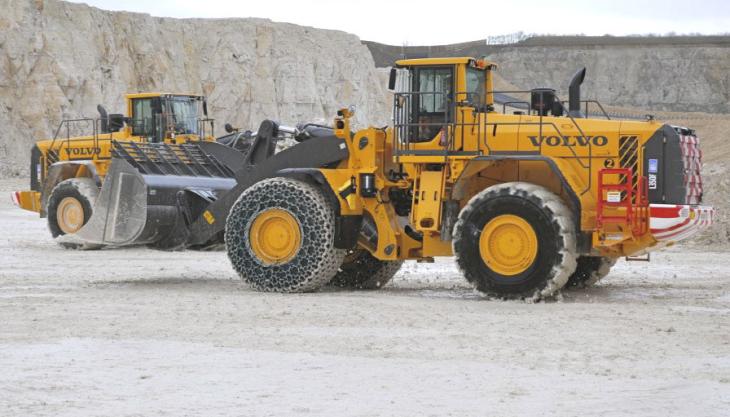
Delivering on a fuel-saving promise secures another order for Volvo’s flagship wheel loader
SINGLETON Birch Ltd have taken delivery of their second Volvo L350F wheel loader for quarrying activities at Melton Ross Quarries, Barnetby, North Lincolnshire, based upon the fuel savings achieved by their first machine delivered in February 2010.
Back then, the independent lime-producing company took a leap of faith in opting for an L350F as one of its prime movers – departing from its previous choice of supplier. The company’s decision was based on the expectation of significant fuel savings over the lifetime of the machine.
‘At the time, we were swayed by Volvo’s claim for their flagship loader of making a 10 litre per hour saving in fuel, and they were right because the machine has done just that,’ said quarry manager Mark Sacker.
‘At today’s cost for red diesel, the L350F saved us in excess of £20,000 in its first year of operation and, as a result, this became the main driving factor for us to opt for the model once again to replace our second face machine.’
Uniquely, Singleton Birch are now the only quarry operators in Great Britain running two Volvo L350F loaders side by side, with both machines deployed on loading blasted chalk from the face and delivering it to a mobile sizer on runs of up to 150m.
Both machines operate a 12h shift, seven days a week, delivering around 450 tonnes of material per hour to the primary unit. As with the existing L350F, the new 52-tonne wheel loader has been especially prepared to Singleton Birch’s specification and follows, where practicable, the MPA checklist for safety parameters applicable to mobile plant.
The most significant modification to the machine ensures safe entry and exit to/from the operator’s compartment thanks to the hydraulically retractable steps located at the nearside rear of the machine together with a widened platform and associated grab rails to facilitate full cab door opening.
Other additions to the standard specification include: a reversible fan; modified mirrors; strobe reverse lights; alternator cooling; bespoke rock guard for the front windscreen; dust buster for the air intake; rock deflectors for the 6.9 cubic metre spade-nosed rock bucket; Groeneveld central lubrication system; and a tyre pressure monitoring system supplied and monitored by Earthmover Tyres. An RDS 9000 weighing system has also been installed in order to monitor actual production.
In addition, Singleton Birch have purchased a pair of Pewag chains for the front wheel and tyre assemblies to evaluate the cost savings versus their annual expenditure on tyre repairs, and to monitor the effect of adding an additional 2 tonnes of dead weight to the machine.
‘It will be interesting to compare the two machines going forward,’ said Mr Sacker. ‘The initial investment in tyre chains is huge, but we are confident this will offer a good return versus the cost of repairing our tyres from damage which is unavoidable in this type of application.
‘We would also anticipate fuel consumption to go up slightly, but again are very confident this will be offset by the higher productivity achieved due to reduced slippage when loading at the face.’