RSMX with TwinDrive adds the finishing touch
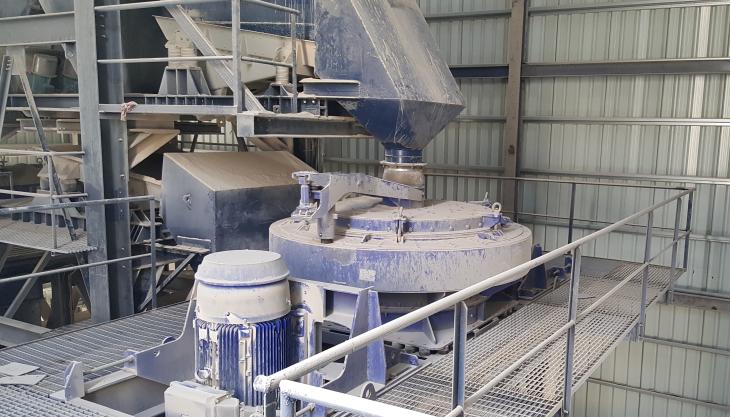
Stevin Rock rely on two rotor centrifugal crushers from BHS-Sonthofen to create high-quality concrete sands
THE sand component of the high-strength concrete used to construct Dubai’s prestigious skyscrapers must be pure and the particle shape needs to be cubical, but as the large quantities of natural sand in the region do not possess these properties, local producers Stevin Rock manufacture the much sought-after commodity from the local limestone.
Stevin Rock’s limestone quarry in the northern Al-Hajar mountains of the United Arab Emirates (UAE), some two hours’ drive from Dubai, is the third-largest site of its kind in the world. More than 60 million tonnes of high-quality limestone are extracted here every year, the majority of which is processed on site in a complex, multi-stage process.
The limestone from the quarry is gradually reduced to 5–10mm in size, whereupon two BHS-Sonthofen RSMX rotor centrifugal crushers with TwinDrive (double drive), which were installed in September 2018, are used for the crucial final step – breaking the limestone particles down to 0–5mm while also turning it into the ideal cubical shape.
‘In other words, our rotor centrifugal crushers perform the final finishing step,’ explained Hans Traut, BHS-Sonthofen’s area sales manager for the Middle East and North Africa. ‘They put the finishing touches on the sand and ultimately determine the quality of the product. The sand is then washed one final time and that’s it – done.’
Mr Traut has worked with Stevin Rock for eight years – but BHS-Sonthofen experts have been working in the region for several decades. Today, fifteen quarries and multiple dry-mortar plants in the region use BHS impact crushers.
Over the years, BHS-Sonthofen have examined hundreds of tonnes of samples from different sites across the Gulf region at their technical centre in Sonthofen, Germany, examining how each rock behaves, how it break up, and what flow speed generates the optimum result.
Mr Traut was able to draw upon this expertise with the rotor centrifugal crushers at Stevin Rock, defining important parameters before installation and adjusting the machines to suit the customer’s plant to ensure the two RSMX units achieved the desired result.
In their first fourth months of operation, the two BHS machines helped Stevin Rock to produce around 300,000 tonnes of high-quality sand – and the plant is still not at full capacity. At present, only one of the two rotor centrifugal crushers operates at a time, as only one washing system is connected. However, a second washing system is planned, which means production will soon increase even further.
The RSMXs have already proven themselves and are setting the standard in terms of both product quality and the use of wear parts. The latter, in particular, can be an important cost factor during continuous operation, but after his first two inspections Mr Traut was happy to report ‘zero wear’, thanks in part to the patented twin-chamber design of the rotor.
Whilst every single particle of the input material undergoes extreme acceleration due to the centrifugal force in the rotor and is hurled against an anvil ring that acts as the impact wall, the rock material also rubs and breaks against itself and not – as is the case with competing technologies – exclusively against the metallic wear parts.
BHS-Sonthofen also utilize especially high-quality and durable materials, with special spin profiles made from tungsten carbide protecting the RSMX in the area where the finished material leaves the rotor. ‘We have constantly improved the design of our rotor centrifugal crushers over the years,’ explained Mr Traut. ‘The RSMX is a unique solution that is characterized by both its precision and its flexibility.’
Mr Traut carries out an in-depth on-site inspection of Stevin Rock’s rotor centrifugal crushers at least once a year – even during the quarry’s midnight shift change if necessary. ‘This close contact and dialog with the customer is what’s important to us,’ he said.
‘Ultimately, a product is being manufactured here that is contributing, literally, to shaping the future of the region. The sand that our crushers manufacture is used in practically every major construction project in the Gulf.’