Red Dot Award for Keestrack R3e
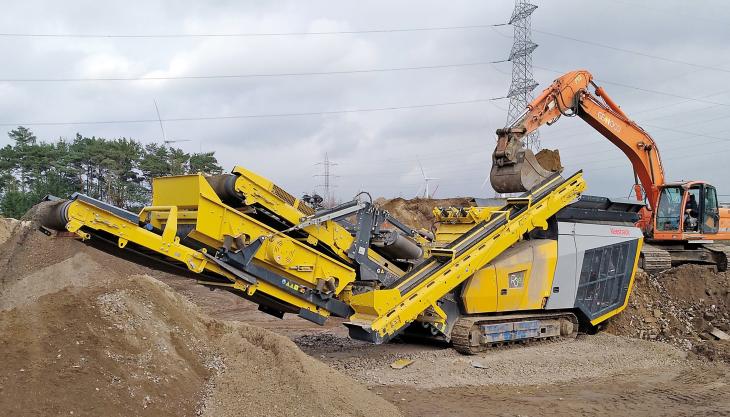
Fully hybrid tracked impact crusher receives prestigious award for outstanding design
FOLLOWING its world premiere at Intermat, in Paris, the new track-mounted Keestrack R3e impact crusher unit has now been officially awarded with an international Red Dot Award 2018 design prize in the ‘Industrial equipment, Machines and Automation’ category.
Besides the R3e’s striking design – which will characterize all future models in the new series from Keestrack – the designers have also implemented innovative ideas for operation and industrial safety, as well as integrating multi-stage production steps and a forward-looking, fully hybrid power unit in a compact and highly mobile machine concept.
The project was led by Keestrack’s chief executive officer, Kees Hoogendoorn, and lasted approximately two years from the initial designs and scale studies, using the 1:20 model presented at Bauma 2016, right up to comprehensive prototype testing from the summer of 2017.
Industrial designers of the famed Austrian design bureau RDD Design Network supported the design and production specialists of Keestrack Engineering GmbH, in Austria, and the company’s production facility at Šternberk, in the Czech Republic, in their work.
For more than 20 years, these specialists have supported international companies from a wide variety of industries, such as automotive, mechanical engineering and construction, in the design of sophisticated industrial products with both aesthetic and functional qualities. RDD Design Network has now received its ninth Red Dot award for the Keestrack R3e machine, and three of its previous awards were also for mineral-processing units.
Besides the characteristic double-sided boomerang, which has been part of Keestrack’s logo for the past two years, the key design features of the Keestrack R3e include extensive body panelling made of modern composite materials. Light yet ruggedly built, they meet the rigorous demands of day-to-day work on site, whilst simple and wide-opening flaps and door units afford easy access to the machine and drive components below, optimizing the operation and daily maintenance of the 250 tonnes/h crusher.
According to Keestrack, a major challenge was the integration of the fully hybrid electric drive without impairing the characteristic operating weight and transport dimensions of machines in the 30-tonne class. Despite the 300kVA surface-mounted generator and two electric motors for the all-electric drive of all machine components from the on-board diesel engine or mains power, the Keestrack R3e weighs just 32 tonnes, even when fully equipped.
In addition to an active pre-screening unit, the equipment also includes a magnetic separator and an efficient 4.4 square metre single-deck post-screening unit with an oversize material recycler, to ensure efficient production of high-grade final product sizes.