Rapid deliver concrete success at Goathill Quarry
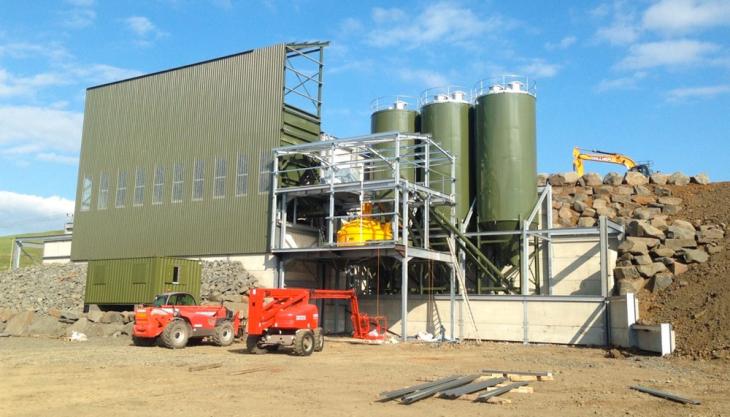
Bespoke mixing plant from Rapid International facilitates Collier Group’s entrance into concrete sector
WHEN Northern Ireland-based Rapid International Ltd supplied Collier Group with their first bespoke concrete batching plant, at Goathill Quarry, in Fife, the move signified the Scottish Group’s entrance into the ready-mixed and precast concrete industry.
Established in 2000, Collier Group are comprised of Collier Quarrying & Recycling and Collier Haulage, and occupy an enviable location in Fife with efficient motorway links to Edinburgh and Scotland’s central belt via the M90, M8 and M9.
The company’s business activities include: the processing of inert rubble, muck and soil; the transportation of ash from local power stations; and the production of Type 1 sub-base, rock armour, single-size aggregates (including high PSV) and manufactured concrete sand.
In 2015 the Group began to explore the option of adding value to their existing aggregates offering by entering the concrete market, and subsequently made the decision to begin production of ready-mixed concrete, concrete blocks and agricultural wall panels at Goathill.
To facilitate this transition, Collier Group looked to mixing technology experts Rapid International for a bespoke static concrete batching plant solution.
Outlining the Group’s rationale for selecting Rapid International, managing director Duncan Collier said: ‘Our key reasons for selecting Rapid were their willingness to be involved with our vision of a one-off bespoke plant and their ability to fabricate the bins, silos and mixer in house and to our specifications.’
Collier Group’s bespoke concrete batching plant features five 80-tonne capacity aggregate bins and three 160-tonne capacity silos (two of which are split into two), which are accessed from the upper ground level, along with four 2,500-litre admixture tanks and filler hoses, which are located in the mixer building.
The aggregates are fed on to a 23m long horizontal weigh-belt that feeds directly into a Rapid planetary mixer capable of producing 80m3 of concrete per hour. This is the only conveyor belt in the entire plant, as all the bins can be filled directly by loading shovel, dumptruck or tipper.
The batch control cabin, which features computer controls from Pneutrol Ltd, truckmixer loading point and wet hopper are all located on the lower yard level of the plant. This is where the blocks and precast products are made (inside or outside depending on weather conditions), making vehicle management and material supply easier to control.
Commenting on the success of the bespoke concrete batching plant, Duncan Collier said: ‘It has been two years since the first concrete was produced at Goathill, and the response, production, support and spare parts have all been – Rapid!’