Powerscreen launch the Premiertrak 300
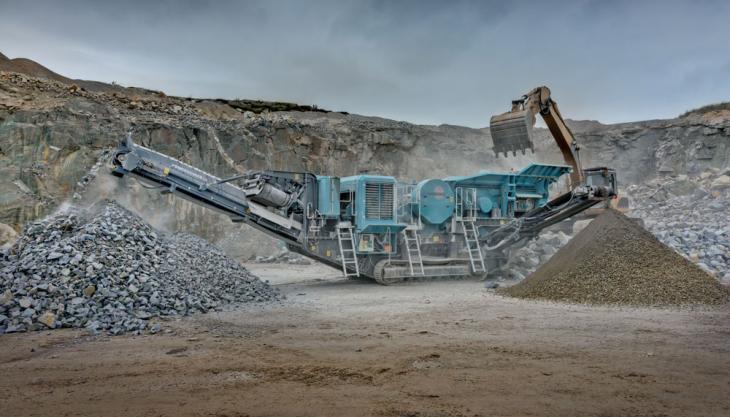
Latest mobile jaw crusher designed to increase productivity and improve fuel efficiency for customers
POWERSCREEN, one of the world’s leading providers of mobile crushing and screening equipment, have introduced the new Premiertrak 300 jaw crusher.
Damian Power, Powerscreen global product director, said: ‘With its exciting new features and feedback from the testing period, we’re confident that the Premiertrak 300 will set new standards worldwide. The machine was recently showcased at a preview demonstration for distributors and customers and there was a lot of enthusiasm among the attendees.’
In advance of its launch, the Premiertrak 300 crusher underwent extensive testing in sites around the UK. One of the test sites was J. Gourley and Sons’ operation in Northern Ireland.
Thomas Gourley, a representative from the quarry operator, commented: ‘The Premiertrak 300 gets a five-star rating from us. As a family-run company we are a relatively small team and any time and money savings can make a big difference.
‘When producing 63mm roadbase material, the crusher provides excellent tonnes per hour output to fuel efficiency ratio. In terms of fuel consumption, we found it outperformed crushers we have used from other brands by around 30%. This is in addition to the time saved by not having to stop production to refuel, and in this industry saving time is saving money, allowing us to do what we do best – producing quality material to meet our customers’ needs.’
The Premiertrak 300 crusher – which has a 1,000mm x 600mm (40in x 24in) jaw chamber – is capable of producing up to 280 tonnes/h of crushed material.
The machine has also been developed with the option of a vibrating grizzly feeder (VGF) or a large, fully independent hydraulically driven pre-screen, which improves fines removal and reduces chamber wear costs. Both options are proportionally controlled by engine load to maintain excellent throughput.
To coincide with the independent pre-screen feature, an optional hydraulically folding extended side conveyor with a stockpile height of 3.1m has been added to the machine to improve stockpile capacity.
A new bypass chute design on the crusher incorporates a ‘flap gate’ to allow the operator to switch between using the side conveyor or sending the material to the main belt without the need to fit a blanking mat on the bottom screen deck.
The Powerscreen jaw chamber has a hydraulically adjustable closed-side setting, which can be adjusted in a matter of minutes by a single operator without requiring tools.
A hydraulic release chamber option (Premiertrak R300 crusher) incorporates a proven hydraulic release mechanism to allow the chamber to ‘dump’ and pass un-crushable material, which is suitable for recycling applications. Another option designed for recycling duties is a hydraulically adjustable deflector plate.
According to Powerscreen, the Premiertrack R300 is highly versatile as it also incorporates a new lock-out function that allows it to work in hard rock quarry applications with the same chamber.
The machine’s new hopper design incorporates a complete hydraulic fold and lock system which removes the need for manual wedges and can be raised/lowered from ground level, removing the need to work at height and providing rapid set-up times. Full hopper extensions are available to further increase capacity.
Designed with transport in mind, the crusher boasts a highly compact transport envelope that provides savings on shipping costs and times. It weighs approximately 32,400kg and features two-speed tracking for optimum mobility. In addition, an intuitive control panel allows machine settings to be changed easily and provides excellent diagnostics for fault-finding if required.
Mr Gourley commented: ‘The size of the machine for transport was another massive benefit. With the same output tonnage and finished product quality as other crushers we’ve used, we saved up to 70% in transport costs when moving the Premiertrak 300 between sites.’
The Premiertrak 300 crusher is powered by a Tier 3/Stage IIIA-compliant Cat C9 ACERT 205kW (275hp) engine or a Tier 4 Final-compliant Scania DC9 80A 202kW (272hp) engine, which is designed to run at the most economical speeds to reduce fuel consumption and noise pollution. Drive to the crushing chamber can be either ‘direct’ clutch drive for increased fuel efficiency, or via a hydrostatic system (Tier 4 only) to allow the option of reverse running or unblocking.
V- Belt adjustment on both variants is via a single adjustment screw which can be completed in a matter of minutes. Fuel efficiency coupled with a large fuel tank capacity ensures longer shifts between refuelling.