Cross Civils on course for expansion
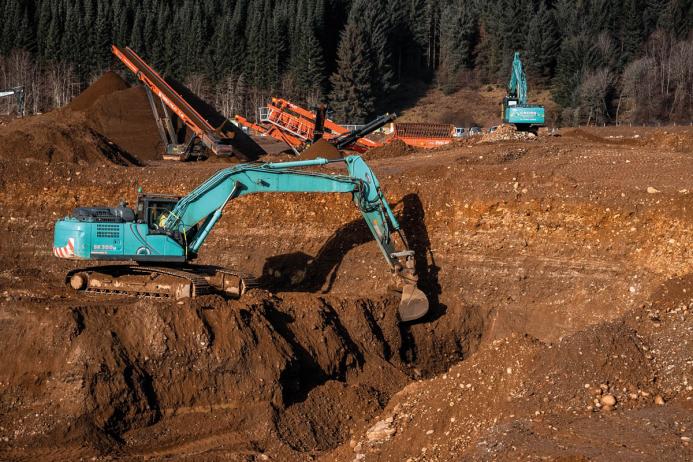
First published in the May 2025 issue of Quarry Management
Molson assistance with golf course quarry project helps lay foundations for further company expansion
Just a stone’s throw away from Loch Tay lies one of the most picturesque quarrying operations in Scotland. The quarry is owned and operated by Cross Civils & Construction Services Ltd based in nearby Aberfeldy. Kevin Cross is managing director of the company which, in just five years, has grown to become one of the biggest multi-discipline contractors in the region.
From a one-man band operation to now employing more than 30 people, the company has grown on the back of Mr Cross’s desire to deliver cost-effective, quality workmanship on time. ‘We started our operations undertaking small-scale construction and civils work, but this has quickly grown into what we are doing today,’ he commented. ‘We now undertake larger, more complex projects, either as the main contractor or as a sub-contractor, and this is how we have found ourselves working on a new golf course on the banks of the Tay.’
The new golf course development has seen the Cross Civils team undertake a large volume of civil engineering works away from the course itself. Due to the course’s relatively remote location, when the requirement for nearly 100,000 tonnes of sand came about, the company had to look at a multitude of alternatives.
‘Originally, the only feasible solution we could see was to import all the material by road. This would have meant 5,000 lorry journeys through Aberfeldy, which, at the best of times, isn’t great for traffic. There was also the high transport cost and, obviously, the huge carbon footprint associated with it,’ explained Mr Cross. ‘We needed to look at other alternatives and, thankfully, found one with a large sand and gravel deposit situated next to the river Tay.
‘This had its own issues with ecologists and council officials not keen at the outset. However, the sand and gravel deposits are around 15–20m above the Tay, which meant we would not be encroaching on the river itself or digging into the water table, something that pleased everyone. We still had the issue of transporting material to the other side of the river and considered a temporary bridge. Again, this was fraught with issues, and we eventually agreed on a short, country lane journey away from the populated areas to the satisfaction of all interested parties.’

With planning consent approved, Mr Cross and his team set about looking for contractors capable of undertaking the project but eventually decided that it would be best to undertake the work themselves and, therefore, began to draw up a shopping list of plant and equipment required to fulfil the works.
‘We have a small fleet of kit ranging from mini-diggers through to 21-tonners for our regular operations,’ said Mr Cross, ‘but we knew we needed to upscale for this project. We had the men capable of doing the work and through them and our own enquiries, we decided to take look at Finlay kit for the crushing and screening machines. We already had a relationship with the Molson Young team having previously taken a couple of mini-diggers into the fleet. We knew what they were like to deal with, we knew they were good on the service and backup, and we were confident in the quality of the kit they could supply.’
Molson’s local sales manager drew up a plan for what was required based on the type of products that were to be produced, after which the purchase agreement was completed, and Mr Cross commenced the initial site set-up ready for quarrying to start.
Planning permission allowed for the excavation of 5m of sand and gravel across the entire site. To achieve this, layers of topsoil and subsoil were removed and stockpiled for use in reinstatement works once the material has been extracted. To extract the sand and gravel, Mr Cross opted for a used Kobelco SK300-7 excavator. ‘It’s an ideal size to get in and out of our site and has the capacity we need to get the raw material from the ground at a steady enough rate,’ he commented. ‘Sitting on a bench part-way through the cut, the SK300 has had a relatively simple life servicing just one 30-tonne capacity dumptruck that takes the material to the crushing and screening operation.
‘As we are quite limited on space, we can’t process material just to stockpile it,’ explained Mr Cross. ‘We must have material going out of the gate to allow us to produce more. With the inclement weather of late, it’s been a bit of a challenge balancing things out here as well as on the golf course construction works. This was another issue we thought we would run into, as when we approached local hauliers to transport the material, they all wanted too many clauses in their contracts that could have seriously affected our ability to make money here. To remedy this, we went out and purchased a pair of tippers ourselves. Not only does this allow us to take loads to the golf course as and when required, but also it now gives us the ability to undertake haulage on our own projects as and when we see fit.’
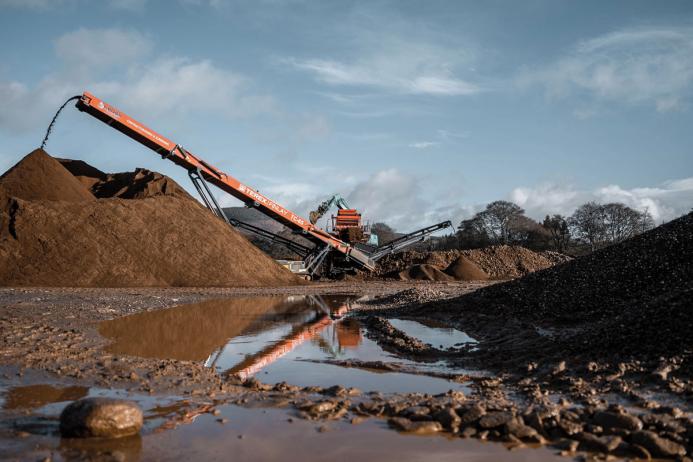
Most of the excavated material can be screened straight from the dig, with this work being undertaken by a new Kobelco SK210LC-11 excavator which loads into an equally new Finlay 674 inclined screen. The 674 screen is well suited to aggregate production thanks to its easily adjustable three-deck screenbox which provides more than 50m2 of screen deck surface. Moreover, the 674 can be set up or stripped down for transport in minutes, making it a very versatile tool for short-duration jobs. It is also very compact when made ready for transport, which is a necessity on the roads around the project.
The sand and gravel deposits were part of the former river bed many thousands of years ago and inevitably contain some larger material. This is easily screened out with the resulting fine sand being stockpiled via a Finlay TC-65 tracked conveyor, allowing a larger cone of material to build up and ensuring the screening operations can carry on uninterrupted for an entire shift.
The oversize material is moved across the site from the Finlay 674 to a Finlay J-1160 jaw crusher. Fed by a 23-tonne excavator, the J-1160 has proved its worth processing the river stones extracted from the cut. The jaw on the J-1160 can be quickly configured to crush alternative sizes of material should a project have a specific requirement, making it a very handy addition to the Cross Civils fleet. Aggregates produced from the river stone are transferred to the final screening point where a second Finlay 674 three-deck screen and TC-65 handle the material.
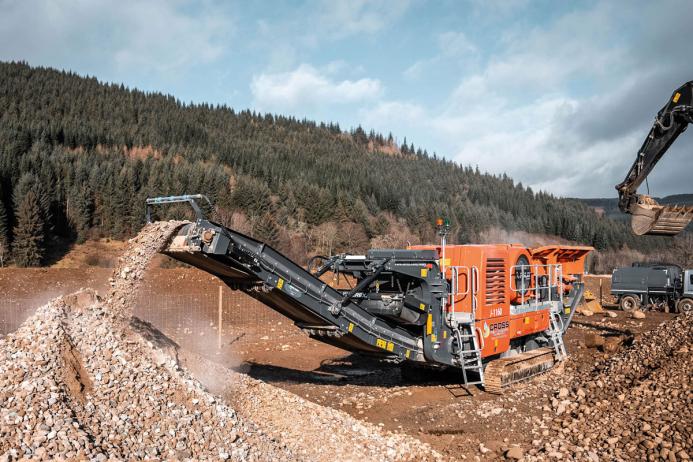
Loading and stockpiling of the materials are handled by a Hyundai HL970CVT. ‘We were unable to source a suitable low-hours wheel loader locally, but with Molson’s help we managed to source one from the South West,’ said Mr Cross. ‘It has been a great tool for us; economical, powerful, and reliable – just what we wanted.’
The Finlay machines provide Cross Civils with half a dozen different aggregates, allowing them to not only meet the golf course construction company’s requirements for sand, but also to produce drainage stone and fill materials for the project.
‘Although this project was primarily designed to bring materials to the golf course development, it has given us the taste for further expansion into small-scale contract crushing operations,’ concluded Mr Cross. ‘We are going to be on site for several more months removing the material and reinstating the ground. It has been a very successful project so far, made easier with the help and assistance we have received from the Molson team.’
Subscribe to Quarry Management, the monthly journal for the mineral products industry, to read articles before they appear on Agg-Net.com