New Connected Worksite solution from Ammann
New digital solution integrates all phases of construction to create single cohesive roadbuilding process
THE Connected Worksite, a new digital solution from Ammann, integrates all phases of the road construction process and identifies efficiencies at every step – thereby enhancing profitability. In collaboration with Q Point, the digitalization experts, Ammann offer an integrated solution that is said to improve the efficiency, transparency, and sustainability of the entire asphalt-related process.
The accessible technology can be utilized for the entirety of a project or during specific phases, including construction planning and order management, planning and production at the asphalt plant, loading and delivery of materials, paving and compaction, and thorough documentation.
The Connected Worksite brings together all the pieces of the puzzle to create one co-ordinated workflow. According to Ammann, this advanced communication streamlines each phase of roadbuilding and ultimately brings operational efficiency and cost savings.
Customer orders are provided digitally and monitored in real time. Orders can be transmitted as binding or non-binding, which the plant can immediately accept, reject, or respond to in more detail. Changes can be made from an office computer or a mobile device from any location. Each instruction is recorded for further review, if needed.
The Connected Worksite uses the digital orders to create a production schedule which is automatically transferred to the plant’s control system. This optimizes material usage and ensures tight deadlines are met. Operating and production data and batch protocols can be analysed centrally, even if multiple control systems are utilized.
As new mix is weighed, the system captures and transmits the appropriate delivery data to the truck driver and the construction team. This allows those at the jobsite to time their work to match the delivery of the mix.
The communication works both ways: The mixing plant receives real-time information about the truck locations, which helps plan further production and loading.
Monitoring of mix temperatures is essential to ensuring high quality. With the Connected Worksite, crews know the temperature of the mix at each stage: during production, as it leaves the plant, when it is in transit, when it arrives, when it is in the hopper, when it is behind the screed, and during compaction.
Ammann Compaction Expert (ACE), Ammann’s proprietary intelligent compaction system, also provides control and guidance. ACE can be supplemented by a cloud-based solution that allows the exchange of information between machines. The data also can be viewed online.
Continuous documentation offers valuable insights into all phases. The data help uncover opportunities for improvement – and at an early stage while adjustments can still be made. At a later date, a detailed history can be shared with clients as needed.
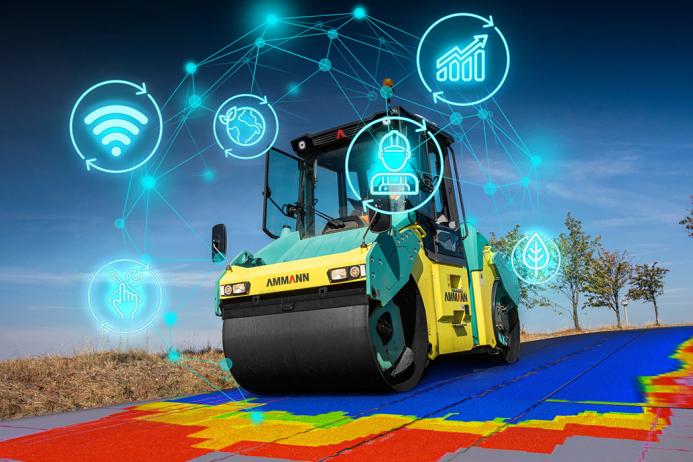