Metso introduce new ‘in-the-pit solutions’ service
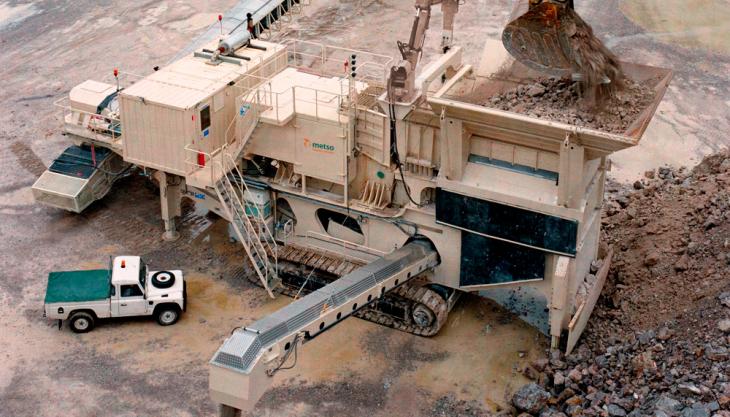
New service offering designed to help mining operators to be more sustainable and cost-effective
METSO say mining operators are continuously being challenged to rethink how to shape their operations to be more sustainable and profitable. The Finnish firm’s new comprehensive in-the-pit solutions (ITPS) programme aims to trim such operations by optimizing the entire process – from design and selection of machinery to production.
According to Metso, savings of water and energy are achieved with a cost reduction of up to 35%. ‘The mining industry is continuously exploring not only new ways to mine at lower cost, but also new sustainable methods, technologies, and systems,’ said Erik Isokangas, Director of Metso’s ITPS.
‘Transportation of ore and waste is one of those areas; it can account for up to 50-60% of the operating cost of mining. If truck haulage can be minimized, significant savings can be achieved.’
He added: ‘Metso's in-the-pit solutions are an advanced option for conventional production processes where truck haulage is used. With these solutions, it is possible to reduce overall costs by as much as 35%. The savings mainly come from improved energy efficiency, resulting from well-planned conveying and reduced maintenance and labour costs.’
Metso's sophisticated ITPS offering includes: concept and feasibility studies, design and engineering; equipment/systems, procurement; commissioning; as well as maintenance and operation. The ITPS can also be connected to Metso's tailored Life Cycle Services programmes.
The company can supply both fully mobile and semi-mobile in-the-pit crushing systems, as well as conveying and material handling solutions to cater for different types of demand and operations.
A fully mobile crushing system removes the reliance on truck haulage. Here, an excavator loads material directly into the hopper of a Lokotrack mobile crushing plant. Crushed rock is then transported to an in-pit belt conveyor via mobile Lokolink conveyors.
The conveyor carries crushed rock from the Lokotrack to a processing plant or waste dump. If/when blasting is performed, the Lokotrack and Lokolink conveyors can be moved to a safe distance. After the blast, a wheel loader cleans the quarry floor and the Lokotrack plant moves to the new muck pile.
A semi-mobile crushing unit reduces the distance of truck haulage. Metso's units are designed to be moved as a single device or disassembled into 4 to 6 smaller modules mounted on skids for easy transportation.
Typically, these crushing systems are moved every few years. This method leverages the flexibility of trucking operations while reducing the cost of long-distance haulage. The main applications relate to operations where the mining is selective, where the ore body is heterogeneous or for capacities over 3,000 metric tons per hour for hard rock.